The fuel system includes elements of the following subsystems:
- – fuel supply system, including fuel tank 16 (Fig. 1), fuel pump 5 with built-in fuel pressure regulator, fuel pipes 1 and 17, hose 18, fuel rail 2 (Fig. 2) with injectors 1, and fuel filter 2 (see Fig. 1);

Fuel supply system: 1 - pipes fuel (plastic); 2 - fuel filter; 3 - fuel filter mounting bracket; 4 - fuel pump sealing ring; 5 - fuel pump; 6 - spacer ring; 7 - fuel pump mounting pressure ring; 8 - filler pipe hose; 9 - fuel tank filler pipe plug; 10 - filler pipe neck lining; 11 - clamp; 12 - fuel tank filler pipe; 13 - air bleed hose; 14 - fuel tank mounting clamp; 15 - connector (quick-release connector); 16 - fuel tank; 17 - fuel tubes (metal); 18 - fuel supply hose; 19 - bracket; 20 - injectors; 21 - fuel rail
- – air supply system consisting of air filter 3 (Fig. 3), air supply hose 11, throttle assembly 4;
- – fuel vapor recovery system including adsorber 15 (Fig. 4), adsorber purge valve 5, fuel vapor separator 11, gravity valve 10, connecting vapor lines 1, 2, 12, 13, 14 and hoses 4.
The engine is equipped with an electronic control system with distributed fuel injection.
In the distributed fuel injection system, the functions of mixture formation and metering of the fuel-air mixture supply to the engine cylinders are separated: the injectors perform metered fuel injection into the intake pipe, and the amount required at each moment of operation The amount of air supplied to the engine is supplied by a system consisting of a throttle assembly and an idle speed controller.
This control method makes it possible to ensure the optimal composition of the combustible mixture at each specific moment of engine operation, which allows for maximum power with the lowest possible fuel consumption and low toxicity of exhaust gases.
The fuel injection system and ignition system are controlled by the engine electronic control unit (ECU), which continuously monitors the engine load, vehicle speed, engine thermal state, and the optimality of the combustion process in the engine cylinders using appropriate sensors.
A feature of the VAZ-2170 Lada Priora injection system is the synchronous operation of the injectors in accordance with the valve timing (the engine control unit receives information from the phase sensor).
The controller turns on the injectors sequentially, and not in pairs or simultaneously, as in asynchronous injection systems.
Each injector is turned on after 720° crankshaft rotation. In starting modes and in dynamic engine operating modes, an asynchronous fuel supply method is used without synchronization with the crankshaft rotation.
The main sensor for the fuel injection system is the exhaust gas oxygen concentration sensor (lambda probe).
It is installed in the engine exhaust manifold and, together with the engine control unit and injectors, forms a control circuit for the composition of the air-fuel mixture supplied to the engine.
Based on the sensor signals, the engine control unit determines the amount of unburned oxygen in the exhaust gases and, accordingly, evaluates the optimality of the air-fuel mixture entering the engine cylinders at each moment in time.
Having recorded a deviation in the composition from the optimal 1:14 (fuel / air), which ensures the most efficient operation of the exhaust gas catalytic converter, the control unit changes the composition of the mixture using the injectors.
Since the oxygen concentration sensor is included in the feedback circuit of the engine control unit, the fuel-air mixture control circuit is closed.
A special feature of the VAZ-2170 Lada Priora engine control system is the presence, in addition to the control sensor, of a second, diagnostic oxygen concentration sensor installed at the outlet of the neutralizer.
Based on the composition of the gases that have passed through the neutralizer, it determines its operating efficiency.
Fuel tank 16 (see Fig. 1) welded, stamped, installed under the body floor in its rear part and secured with two steel clamps 14.
To prevent fuel vapors from entering the atmosphere, the tank is connected through a fuel vapor separator 11 (see Fig. 4) and a gravity valve 10 by steam lines 12, 13, 14 and 1 to an adsorber 15.
An electric module of an electric fuel pump (fuel pump) 5 (see Fig. 1), which combines the pump itself, the fuel level indicator sensor and the fuel pressure regulator.
A branch pipe for connecting the filler pipe 12 is made at the rear of the tank.
From the pump, fuel is supplied to the fuel filter 2, installed below on the base of the body, and from there it enters the fuel rail 21, fixed to the cylinder head of the engine. From the fuel rail, fuel is injected by injectors 20 into the intake channels of the cylinder head, with the fuel torch directed at the intake valve.
Excess fuel is drained into the fuel tank through the fuel pressure regulator installed in the electric fuel pump module.
This fuel pressure regulator installation scheme, in addition to eliminating a long return drain line, prevents an increase in the fuel temperature in the tank, which causes excessive vaporization.
The fuel pump (electric fuel pump module) 5 (see Fig. 1) is submersible, vortex type, with a coarse fuel filter. The pump supplies fuel and is installed in the fuel tank, which reduces the possibility of vapor locks, since the fuel is supplied under pressure, not under vacuum.
The fuel pump supplies fuel from the fuel tank through the main fuel filter to the injector rail under pressure of more than 380 kPa.
Fine fuel filter 2 (see Fig. 1) is full-flow, secured in bracket 3 on the body base next to the fuel tank. The filter is non-separable, equipped with a steel housing with a paper filter element.
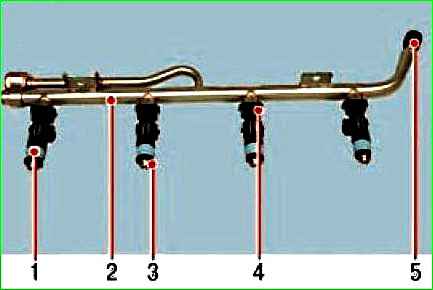
Fuel rail and injectors: 1 - injector; 2 - fuel rail; 3 - sealing ring; 4 - injector retainer; 5 - fuel pressure control nipple cap
Fuel rail 21 (see Fig. 1), which is a hollow tubular part, serves to supply fuel to the injectors and is fixed to the cylinder head.
The engine uses a drainless fuel system, the pressure in the rail is maintained by a fuel pressure regulator installed in the electric fuel pump module.
Injectors 20 are attached to the rail with clamps 4 (see Fig. 2) through rubber sealing rings.
To equalize the pressure in the injectors, fuel is supplied to the middle part of the rail.
The injectors with their sprayers enter the holes located above the intake channels of the cylinder head. The injector holes are sealed with rubber sealing rings.
The injector is designed for metered injection of fuel into the engine cylinders and is a high-precision electromechanical valve in which the shut-off valve needle is pressed against the seat by a spring.
When an electrical impulse is supplied from the control unit to the electromagnet winding, the needle rises and opens the nozzle hole through which fuel is supplied to the engine intake pipe.
The amount of fuel injected by the injector depends on the duration of the electrical impulse.
The fuel pressure regulator is installed in the fuel pump module and is designed to maintain constant fuel pressure in the fuel rail.
The regulator is connected to the beginning of the supply line immediately after the fuel filter and is a bypass valve with a spring having a strictly calibrated force.
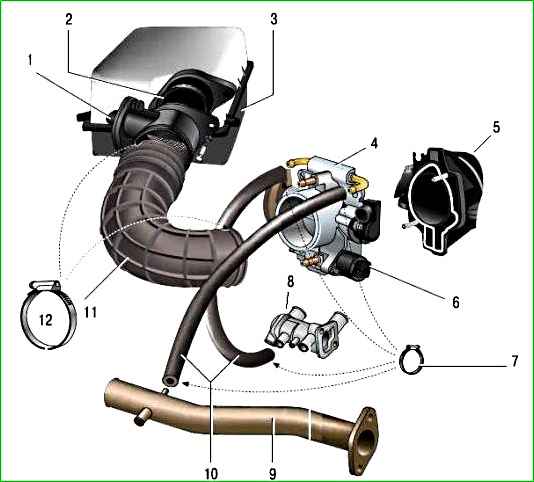
Air supply system: 1 - mass air flow sensor: 2 - sealing sleeve: 3 - air filter: 4 - throttle assembly; 5 - intake manifold: 6 - idle speed control valve or additional air regulator; 7 - hose clamps; 8 - thermostat; 9 - coolant pump inlet pipe; 10 - throttle assembly heating hoses; 11 - air supply sleeve; 12 - air supply hose mounting clamps
Air filter 3 (see Fig. 3) is installed in the front part of the engine compartment on three rubber supports.
The filter element is paper, flat, with a large filtering surface area.
The filter is connected by a rubber corrugated air supply hose 11 to the throttle assembly 4. A mass air flow sensor 1 is installed between the hose and the filter.
The throttle assembly 4 (see Fig. 3) is attached to the intake manifold 5.
It measures the amount of air entering the intake pipe.
The air flow into the engine is controlled by a throttle valve connected to the pedal drive accelerator.
The throttle assembly includes 4 throttle position sensors and 5 idle speed controller.
In the flow part of the throttle assembly (before the throttle valve and a) there are vacuum extraction holes necessary for the operation of the crankcase ventilation and fuel vapor recovery systems.
Idle speed regulator 5 regulates the crankshaft speed in idle mode by controlling the amount of air supplied bypassing the closed throttle valve.
It consists of a two-pole stepper motor and a cone valve connected to it.
The valve extends or retracts according to signals from the engine control unit.
When the regulator needle is fully extended (which corresponds to 0 steps), the valve completely blocks the air passage.
When the needle is retracted, an air flow is provided proportional to the number of steps the needle moves away from the seat.
By changing the opening and closing value of the regulator valve, the control unit compensates for a significant increase or decrease in the amount of air supplied, caused by its suction through a leaky intake system or, conversely, a clogged air filter.
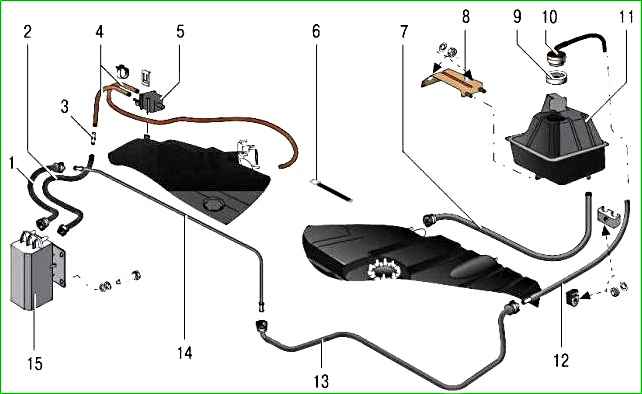
Fuel vapor recovery system: 1 - front vapor line tube; 2 - adsorber and purge valve tube; 3 - adapter; 4 - hoses; 5 - adsorber purge valve; 6 - clamp; 7 - fuel drain tube; 8 - separator bracket; 9 - valve gasket; 10 - gravity valve; 11 - fuel vapor separator; 12 - rear vapor line tube; 13 - middle steam pipe; 14 - steam pipe; 15 - adsorber
The fuel vapor recovery system prevents fuel vapors from escaping from the fuel system into the atmosphere, which have an adverse effect on the environment.
The system uses a method of absorbing vapors with a carbon adsorber 15 (see Fig. 4).
It is installed in the engine compartment on the radiator trim panel and is connected by steam pipes to the separator 11 of fuel vapors installed in the niche of the left rear wheel, and to the valve 5 of the adsorber purge, located in the engine compartment on the decorative casing of the engine.
The electromagnetic valve of the adsorber purge switches the operating modes of the system according to signals from the engine control unit.
Fuel vapors from the tank are partially condensed in the separator 11, the condensate is drained back into the tank through pipe 7.
The remaining vapors through gravity valve 10 installed in the separator pass through steam pipes 12, 13, 14, 1 and enter the adsorber 15.
The second nipple of the adsorber is connected by a hose to the valve 5 of the adsorber purge, and the third one is connected to the atmosphere.
When the engine is turned off, the third nipple is blocked by a built-in check valve, in this case the adsorber does not communicate with the atmosphere.
When the engine is started, the ECU begins to send control pulses to the electromagnetic valve.
The electromagnetic valve opens, under the action of the vacuum, the check valve in the adsorber also opens, due to which air from the atmosphere and fuel vapors from the separator enter the adsorber.
At this time, the sorbent is purged: gasoline vapors are removed through hoses 4 and throttle assembly 4 (see Fig. 3) into the intake manifold 5.
Failures in the fuel vapor recovery system result in unstable idle speed, engine stalling, increased toxicity of exhaust gases and deterioration of the vehicle's driving performance.