Sludge is drained from the fuel coarse filter daily. To drain the sludge you need:
Stop the engine.
Turn the lid tap and drain the water from the filter until clean fuel appears.
Attention! Do not overtighten the valve to avoid damaging the threads.
If more than 50 grams of fuel goes down the drain, you need to fill the filter with fuel by bleeding the fuel system to avoid difficulties when starting the engine.
Replacing the fuel coarse filter
Clean the fuel filter interface area from dirt.
Unscrew the filter using a special wrench or other available means.
Wipe the filter mating surface.
Remove the O-ring.
Fill the new filter with clean fuel and install it complete with a gasket, which you first lubricate with clean engine oil.
After the gasket touches the filter housing cup, tighten the filter another 3/4 turn.
Installation of the filter should be done only by hand.
Attention! Do not over-tighten the filter to avoid stripping the thread, damaging the sealing gasket and filter housing.
Replacing the fine fuel filter
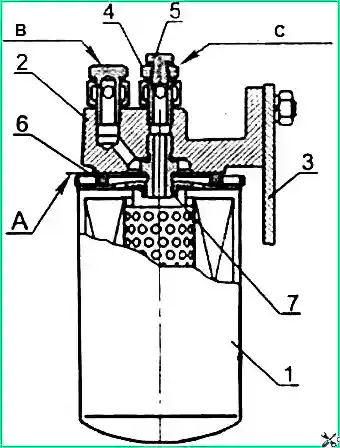
Fuel fine filter: 1 - Mann filter & Hummel WDK962; 2 - filter housing; 3 - bracket; 4 - fitting; 5 - plug (for air release); 6 - gasket; 7 - fitting
The service life of the fine fuel filter depends on the purity of the fuel used.
Replace the filter every 25 thousand km or according to the results of diagnostics of the Common Rail system, for which:
- - unscrew filter 1 from fitting 7 in housing 2 and install a new Mann & Hummel WDK962, supplied assembled with gasket 6, which is pre-lubricated with engine oil;
- - after gasket 6 touches installation pad “A” on body 2, tighten the filter another % turn. At the same time, tighten the filter only with your hands;
- - fill the system with fuel.
Filling the fuel system
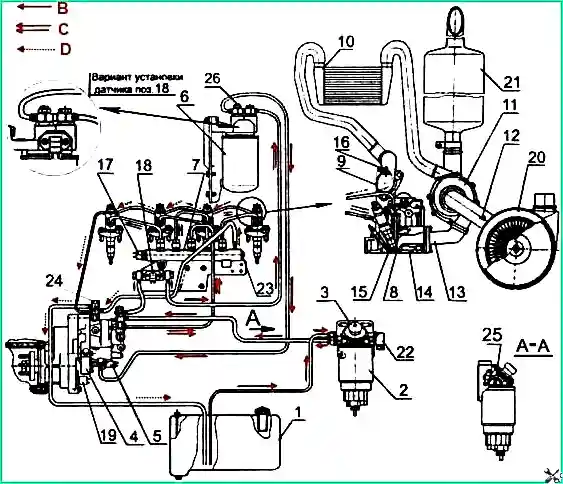
Power system diagram: 1 - fuel tank; 2 - fuel coarse filter; 3 - manual fuel priming pump; 4 - high pressure fuel pump; 5 - electromagnetic pressure regulator, 6 - fine fuel filter; 7 - high pressure fuel accumulator; 8 - nozzle; 9 - intake manifold; 10 - charge air cooler 11 - turbocharger; 12 - air filter clogging sensor; 13 - exhaust manifold; 14 - cylinder head; 15 - glow plug; 16 - charge air temperature and pressure sensor; 17 - high fuel pressure sensor; 18 - temperature and fuel pressure sensor; 19 - camshaft speed sensor; 20 - air cleaner; 21 - muffler; 22 - fuel heater; 23 - pressure limitation valve; 24 - angle rotating bolt; 25 - air release plug; 26 - plug; B - low pressure fuel lines; C - high pressure fuel lines; D - fuel lines for discharging excess fuel into the tank
Attention! Cranking the diesel engine with the starter when the power supply system is not filled with fuel is prohibited. The high pressure fuel pump will fail.
To fill the fuel system, it is necessary to remove air from it (bleed the system) for which:
Unscrew plug 26 (Fig. 2), located on the bolt securing the outlet fitting of the fine fuel filter, by 2-3 turns.
Bleed the system using booster pump 3 located on the coarse fuel filter housing 2, tighten plug 26 (tightening torque 7-8 Nm) when fuel appears without air bubbles.
Unscrew the bolt of the rotary angle 24 securing the drainage pipes on the high-pressure pump body by 2-3 turns and continue pumping using the booster pump until fuel appears without air bubbles.
Tighten bolt 24 (tightening torque 3-4 Nm).
Air purifier maintenance
Service the air purifier with paper filter elements made of special highly porous cardboard every 80 thousand kilometers (TO-2) or, if necessary, according to the indications of the clogging indicator.
Maintenance of the air purifier involves purging the main filter element, which traps dust entering the air purifier.
Contamination of the control filter element indicates damage to the main filter element (break of the paper curtains, peeling off bottoms).
In this case, it is necessary to blow out the control filter element, and replace the main one.
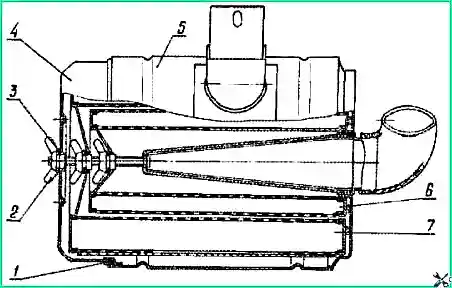
Air filter: 1 - sealing ring; 2 - wing nut; 3 - washer; 4 - cover; 5 - body; 6 - control filter element; 7 - main filter element
Servicing the air purifier in accordance with Fig. 2 perform in the following sequence:
Remove tray 4.
Remove main filter element 3.
Attention! It is not recommended to remove control filter element 6 from the housing.
Blow off the main filter element with compressed air, first from the inside and then from the outside until the dust is completely removed.
To avoid breaking through the paper curtain, the air pressure should be no more than 0.2-0.3 m
The air stream should be directed at an angle to the surface of the filter element.
During maintenance, it is necessary to protect the filter element from mechanical damage and oiling.
Do not blow the filter element with exhaust gases or wash it in diesel fuel
Clean the supply pipe, the internal surfaces of the housing and the air cleaner tray from dust and dirt.
Before assembling the air purifier, check the condition of the O-rings.
When assembling, make sure the filter elements are installed correctly in the housing and securely tighten the wing nut by hand.
Checking the tightness of the air cleaner and intake tract connections
Check the tightness of the connections of the air cleaner and the intake tract every 500 thousand km (4TO-1).
To check the tightness, use the KI-4870 GOSNITI device.
If the device is missing, check the tightness of the connections visually.
Check the condition and fastening of the hoses, if necessary, tighten their clamps, especially the hoses connecting the air filter to the engine intake manifold.
Hoses must be placed on nozzles of at least 30 mm. Cracks and ruptures of hoses are not allowed.
Maintenance of the Common Rail fuel system
Service of the Common Rail fuel system should be carried out at specialized service centers or with the involvement of specialists from specialized service centers for servicing the Common Rail system.
Replacement of injectors based on the results of testing the “Common Rail” power supply topic should be carried out taking into account the markings of the injector and sprayer, applied in the places indicated in Fig. 4.
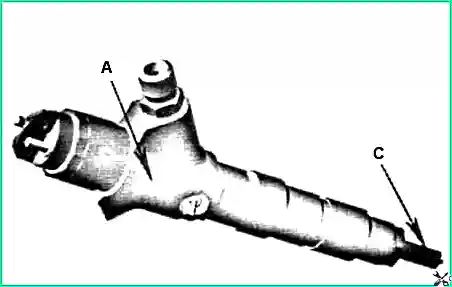
Replacing the nozzle in the nozzle without the use of special equipment and specially trained personnel, as well as during the warranty period, is prohibited.
During the warranty period, replacement of the nozzle in the nozzle can only be carried out by service or by workshops specially authorized by Bosch.
Turbocharger maintenance
The turbocharger does not require special maintenance during operation; its disassembly and repair are not allowed.
Partial or complete disassembly, as well as repairs, are possible after removing the diesel turbocharger and only in a specialized enterprise.
Reliable and durable operation of a turbocharger depends on compliance with the rules and frequency of maintenance of diesel lubrication and air cleaning systems, using the type of oil recommended by the manufacturer, monitoring the oil pressure in the lubrication system, replacing and cleaning oil and air filters.
Damaged oil supply and drain lines, as well as air lines connecting to the turbocharger, must be replaced immediately.
When replacing a turbocharger, fill the oil supply hole with clean engine oil up to the level of the flange, and when installing gaskets under the pipeline flanges, do not use sealants.
If a malfunction occurs, the compressor should be sent to a workshop, where qualified specialists will determine the cause of the malfunction and eliminate it.