Setting the fuel injection advance angle for diesel D-245.7E3 / D-245.9E3 bus PAZ 32053-07
The need to install (reinstall) the pulse wheels of the crankshaft and the fuel injection pump drive gearbox shaft to synchronize them may be caused by rearranging the fuel injection pump drive gearbox during routine diesel repairs
The installation of pulse wheels according to the proposed scheme is carried out to synchronize the signals from the crankshaft speed sensors and the input shaft of the injection pump drive and is ensured by binding the sensor signals to the common reference point of the shaft position at the moment the piston of the first cylinder passes the top dead center (TDC).
To ensure correct installation of the impulse wheels, it is necessary to make a device for fixing the locating pin in accordance with the sketch (Fig. 1).
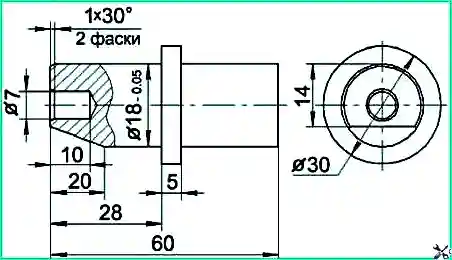
Remove the cylinder head cover.
Install the piston of the first cylinder to the TDC position, turning the crankshaft clockwise using bolt 4 (Fig. 2), until the axis of the 16th tooth of the “crown” of the impulse wheel coincides (when counting counterclockwise from the gap segment at “ crown" of the impulse wheel) with sensor axis 1.
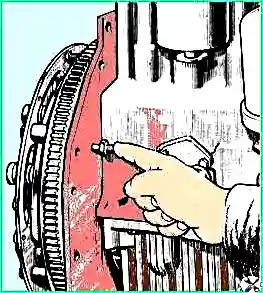
Make sure that the intake and exhaust valves of cylinder 1 are closed.
If the exhaust valve is open, turn the crankshaft a full turn and recheck the condition of the valves.
Install the piston of the first cylinder on the compression stroke (beyond ~ 60° of the crankshaft rotation angle before TDC), for which:
- turn the crankshaft clockwise using bolt 4 (Fig. 3) approximately two turns
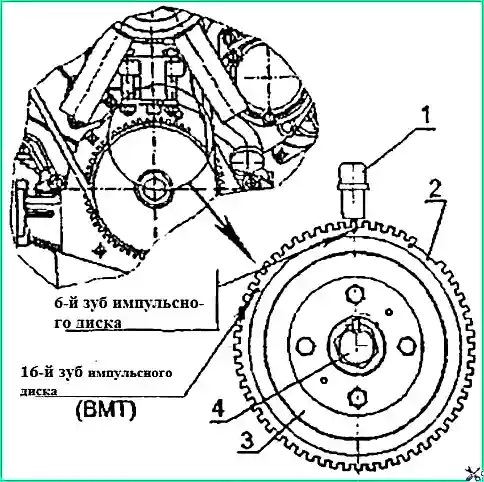
- at the same time, on the second turn, turn it out in accordance with Fig. 2 clamp from the threaded hole of the rear sheet, insert it with the reverse side into the same hole until it stops into the flywheel (for ZIL diesel engines, press the spring-loaded clamp until it stops into the flywheel) and turn the crankshaft until the clamp coincides with the hole in the flywheel;
In this case, pulse wheel 2 (Fig. 3), mounted on the crankshaft pulley 3, will be positioned in such a way that the axis of sensor 1 will pass along the axis of the sixth tooth of the “crown” of the pulse wheel (when counting counterclockwise from the gap segment at “ crown of the impulse wheel).
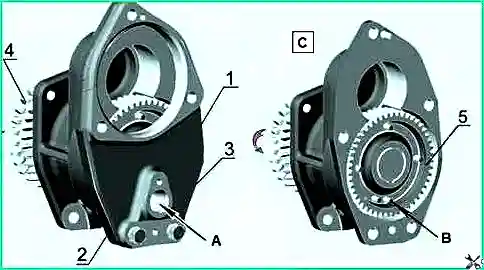
If there is misalignment between the sensor and the sixth tooth, it is necessary to loosen the fastening of the sensor and ensure that the axes of the sensor and the tooth coincide, and secure the sensor.
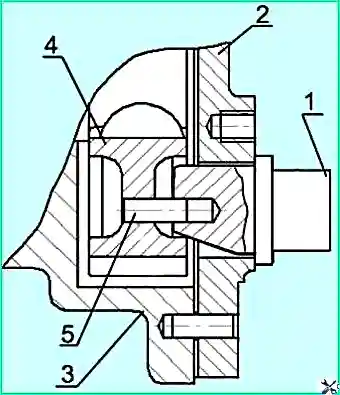
With the gearbox removed, turn clockwise the drive coupling half 5 (Fig. 5) (in Fig. 4 the gearbox is shown with the gear drive gear installed on the drive coupling half) to achieve the position in the window for installing the sensor of two sequentially located pulse pins.
By slightly turning the drive in the opposite direction, position the alignment pin (the first one in the direction of shaft rotation) in the center of the window.
Install a device into the window to fix the position of the mounting pin 1 (Fig. 5) and secure the device with the mounting flange 2 and bolts 3.
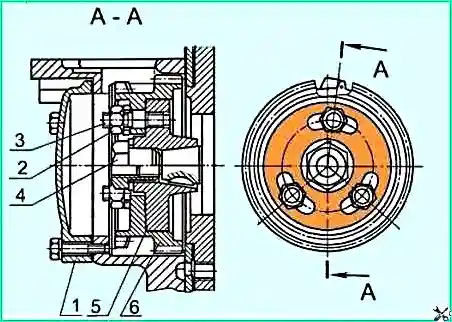
Remove the hatch cover 1 (Fig. 6) and, supporting the drive gear 6 through the hatch window, insert the half-coupling drive 5 into the grooves of the drive gear pin 3, thus installing the gearbox.
Attach the gearbox to the distribution panel.
Install and tighten nuts 2 to a torque of 35-50 Nm.
Remove the mounting flange and remove the mounting fixture.
Replace the mounting flange and secure it.
Install the hatch cover, speed sensor and secure them.
Remove the flywheel retainer and screw its threaded part into the rear sheet. Install the cylinder head cover