Kompressor - Kolbentyp, nicht direkt durchströmt, zwei Zylinder, einstufige Kompression
Aluminiumkolben mit schwimmend gelagerten Bolzen; Die Bolzen in den Kolbennaben sind durch Sicherungsringe gegen axiale Verschiebung gesichert
Luft aus dem Motorluftfilter gelangt durch selbsttätige Platteneinlassventile 21 in die Kompressorzylinder.
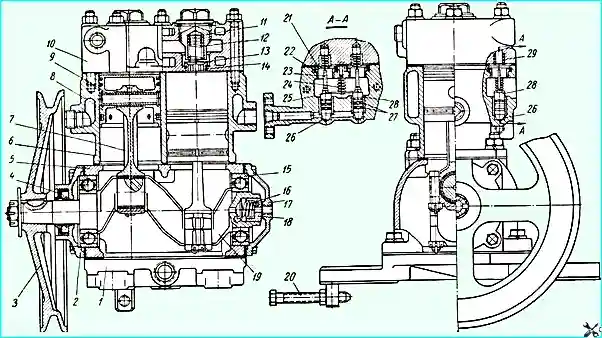
Luftkompressor: 1 – untere Kurbelgehäuseabdeckung; 2 - vordere Kurbelgehäuseabdeckung; 3 - Riemenscheibe; 4 - Kurbelwellen-Öldichtung; 5 - Kurbelgehäuse des Kompressors; 6 - Zylinderblock; 7 - Pleuelstange; 8 - Kolben mit Ringen; 9 - Kolbenbolzen mit Sicherungsringen; 10 - Zylinderkopf; 11 - Ablassventilstopfen; 12 - Auslassventilfeder; 13 - Auslassventil; 14 - Auslassventilsitz; 15 - hinteres Kurbelwellenlager; 16 - Dichtungsfeder; 17 - hintere Kurbelgehäuseabdeckung; 18 - Siegel; 19 - Kurbelwelle; 20 - Einstellschraube; 21 - Einlassventil; 22 - Einlassventilführung; 23 - Einlassventilschaft; 24 - Kipphebelführungsfeder; 25 - Kipphebel; 26 - Kolben; 27- Dichtringe; 28 - Einlassventilschaftbuchse; 29 - Einlassventilfeder
Die von den Kolben komprimierte Luft wird durch die selbsttätigen Plattenauslassventile 13 im Zylinderkopf in das pneumatische System gedrückt.
Block und Kopf werden durch Flüssigkeit gekühlt, die vom Motorkühlsystem zugeführt wird.
Flüssigkeit wird dem Kompressorkühlsystem aus dem Wassermantel des Motoransaugrohrs zugeführt und vom Kopf in den Saugraum der Wasserpumpe abgelassen.
Es ist zu beachten, dass das Befüllen des Kompressorkühlsystems nur bei laufendem Motor erfolgt.
Daher müssen Sie nach dem Einfüllen von Flüssigkeit in den Kühler den Motor starten, ihn 3–5 Minuten laufen lassen und dann den Füllstand im Kühler prüfen.
Die Luftzufuhr des Kompressors zum pneumatischen System wird wie folgt abgeschaltet.
Wenn der Luftdruck im pneumatischen System 7,0-7,4 kg/cm 2 erreicht, liefert der Druckregler Druckluft durch Kanal „A“ im Zylinderblock unter den Kolben 26 der Entladevorrichtung. die beim Aufsteigen die Einlassventile 21 der beiden Zylinder öffnen und dadurch die Luftzufuhr zum pneumatischen System unterbrechen, da sich die Luft frei von Zylinder zu Zylinder bewegen kann.
Wenn der Luftdruck im pneumatischen System auf 5,6–6,0 kg/cm 2 abfällt, unterbricht der Regler die Druckluftzufuhr zu den Kolben der Entladevorrichtung.
Luft unter dem Kolben wird in die Atmosphäre freigesetzt; Unter der Einwirkung der Kipphebelfeder senken sich die Kolben ab, geben die Einlassventile frei und der Kompressor beginnt erneut, Luft in das pneumatische System zu pumpen.
Die Ölzufuhr zu den Reibflächen des Kompressors erfolgt über einen Schlauch von der Motorölleitung zur hinteren Abdeckung des Kompressorkurbelgehäuses und durch die Dichtung durch die Kurbelwellenkanäle zu den Pleuellagern.
Die Hauptkugellager, Kolbenbolzen und Zylinderwände werden spritzgeschmiert.
Gusseiserne Riemenscheibe.
Kompressorwartung
Es ist notwendig, regelmäßig die Spannung der Muttern, die Befestigung des Kompressors am Motorkopf, die Befestigung der Riemenscheibe, die Spannung des Antriebsriemens und das Anziehen der Muttern und Bolzen, die den Kopf sichern, zu überprüfen.
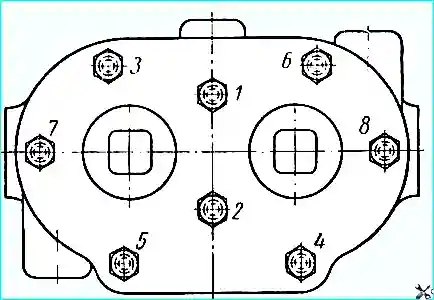
Die Reihenfolge des Anziehens der Muttern des Kompressorzylinderkopfes
Die Muttern der Bolzen, die den Kopf befestigen, sollten in der in der Abbildung gezeigten Reihenfolge gleichmäßig in zwei Schritten angezogen werden. 2.
Das endgültige Spanndrehmoment sollte nach 80.000-100.000 km Laufleistung im Bereich von 1,2-1,7 kg/m liegen. In Verbindung mit der saisonalen Wartung (im Frühjahr) ist es notwendig, den Kompressorkopf zu entfernen, um die Kolben, Ventile, Sitze, Federn, Luftkanäle sowie die Funktion und Dichtheit der Ventile und Kolben der Entladevorrichtung zu überprüfen.
Undicht abschließende Ventile müssen bis zum Sitz abgeschliffen bzw. stark verschlissene oder beschädigte Ventile durch neue ersetzt werden.
Auch neue Ventile sollten so lange auf den Ventilsitzen geläppt werden, bis beim Lacktest durchgehender Ringkontakt erreicht ist.
Es ist notwendig, den Zustand der Dichtungsringe der Kolben 26 (Abb. 1) der Entladevorrichtung zu überprüfen und die Ringe gegebenenfalls auszutauschen.
Dabei ist folgende Reihenfolge einzuhalten:
- 1. Starten Sie den Motor und bringen Sie den Druck im pneumatischen System auf 7,0–7,4 kg/cm 2.
- 2. Stellen Sie den Motor ab.
- 3. Entfernen Sie den Gummischlauch, der den Motorluftfilter mit dem Kompressor verbindet.
Wenn die Entlastungsvorrichtung nicht dicht ist, ist ein charakteristisches Geräusch von Luft zu hören, die durch die Luftzufuhrleitung des Kompressors strömt, und das Druckmessgerät des pneumatischen Systems zeigt einen leichten Druckabfall an.
- 4. Reduzieren Sie den Luftdruck im pneumatischen System auf 5,6–6,0 kg/cm 2, während die Kolben abgesenkt werden.
- 5. Luftzufuhrrohr entfernen, Feder und Kipphebel herausnehmen,
Heben Sie dann die Kolbenstangenfassung an und entfernen Sie sie zusammen mit der Kolbenstange. Entfernen Sie anschließend den Kolben mit einem Drahthaken aus seiner Fassung, indem Sie ihn in ein Loch mit 2,5 mm Durchmesser am Ende des Kolbens einführen oder Druckluft zuführen. zum horizontalen Kanal der Zylinderblock-Entladevorrichtung.
- 6. Ersetzen Sie abgenutzte Gummidichtringe an den Kolben. Kolben mit Dichtringen sollten vor dem Einbau mit Motoröl geschmiert werden.
Anzeichen für eine Fehlfunktion des Kompressors sind unter anderem Geräusche und Klopfgeräusche sowie eine erhöhte Ölmenge im Kondensat, das aus den Luftzylindern abgelassen wird.
Ein hoher Ölgehalt im Kondensat ist üblicherweise eine Folge des Verschleißes an Kolbenringen, der Öldichtung am hinteren Ende der Kurbelwelle, der unteren Pleuellager oder einer Verstopfung des Ölablassrohrs des Kompressors.
Einstellen der Spannung des Kompressor-Antriebsriemens
Der Antriebsriemen des Kompressors muss so gespannt sein, dass bei einer Krafteinwirkung von 4 kg die Durchbiegung des zwischen den Riemenscheiben des Kompressors und des Lüfters liegenden Riemenzweigs 5-8 mm beträgt.
Die Riemenspannung sollte täglich überprüft werden.
Die Spannung des Kompressorantriebsriemens wird durch Bewegen des Kompressors eingestellt.
Lösen Sie hierzu die Muttern, mit denen die untere Abdeckung an der Halterung befestigt ist und stellen Sie mit der Einstellschraube 20 die erforderliche Spannung sicher.
Anschließend müssen Sie die Kompressorhalterung festziehen und die Einstellschraube mit einer Kontermutter kontern.