Compresor: tipo pistón, de flujo no directo, de dos cilindros, compresión de una sola etapa
Pistones de aluminio con pasadores flotantes; Los pasadores en los casquillos del pistón están asegurados contra el movimiento axial mediante anillos de retención
El aire del filtro de aire del motor ingresa a los cilindros del compresor a través de las válvulas de entrada de placa autoactuantes 21.
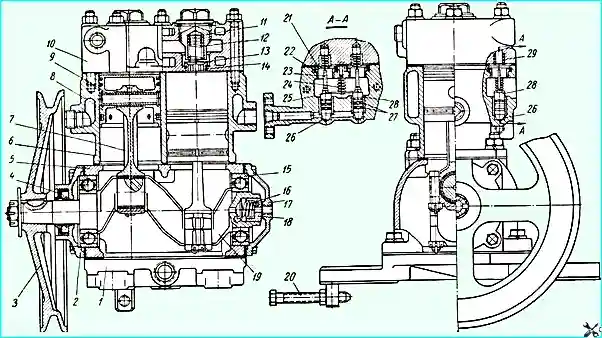
Compresor de aire: 1 - Tapa del cárter inferior; 2 - tapa del cárter delantero; 3 - polea; 4 - sello de aceite del cigüeñal; 5 - cárter del compresor; Bloque de 6 cilindros; 7 - biela; 8 - pistón con anillos; 9 - pasador de pistón con anillos de retención; 10 - culata; 11 - tapón de la válvula de descarga; 12 - resorte de válvula de descarga; 13 - válvula de descarga; 14 - asiento de la válvula de descarga; 15 - cojinete del cigüeñal trasero; 16 - resorte del sello; 17 - tapa del cárter trasero; 18 - sello; 19 - cigüeñal; 20 - perno de ajuste; 21 - válvula de entrada; 22 - guía de válvula de entrada; 23 - vástago de la válvula de admisión; 24 - resorte guía del balancín; 25 - balancín; 26 - émbolo; 27- anillos de estanqueidad; 28 - zócalo del vástago de la válvula de entrada; 29 - resorte de válvula de admisión
El aire comprimido por los pistones es forzado a entrar en el sistema neumático a través de las válvulas de descarga de placa autoactuantes 13 ubicadas en la culata del cilindro.
El bloque y la culata se enfrían mediante líquido suministrado desde el sistema de refrigeración del motor.
El líquido se suministra al sistema de enfriamiento del compresor desde la camisa de agua del tubo de admisión del motor y se drena desde el cabezal hacia la cavidad de succión de la bomba de agua.
Es necesario tener en cuenta que el llenado del sistema de refrigeración del compresor se produce únicamente cuando el motor está en marcha.
Por lo tanto, después de verter el líquido en el radiador, es necesario arrancar el motor, dejarlo funcionar durante 3 a 5 minutos y luego verificar el nivel en el radiador.
El suministro de aire del compresor al sistema neumático se corta de la siguiente manera.
Cuando la presión de aire en el sistema neumático alcanza 7,0-7,4 kg/cm 2, el regulador de presión suministra aire comprimido a través del canal “A” en el bloque de cilindros debajo de los émbolos 26 del dispositivo de descarga, que, al elevarse, abren las válvulas de entrada 21 de los dos cilindros, deteniendo así el suministro de aire al sistema neumático, ya que el aire puede moverse libremente de un cilindro a otro.
Cuando la presión de aire en el sistema neumático cae a 5,6-6,0 kg/cm 2, el regulador deja de suministrar aire comprimido a los émbolos del dispositivo de descarga.
El aire que se encuentra debajo del émbolo se libera a la atmósfera; Los émbolos, bajo la acción del resorte basculante, descienden, liberando las válvulas de entrada, y el compresor comienza nuevamente a bombear aire al sistema neumático.
El aceite se suministra a las superficies de fricción del compresor a través de un tubo desde la línea de aceite del motor hasta la cubierta trasera del cárter del compresor, y a través del sello a través de los canales del cigüeñal hasta los cojinetes de la biela.
Los cojinetes de bolas principales, los pasadores del pistón y las paredes del cilindro están lubricados por salpicadura.
Polea de hierro fundido.
Mantenimiento del compresor
Es necesario comprobar periódicamente la tensión de las tuercas, la fijación del compresor a la cabeza del motor, la fijación de la polea, la tensión de la correa de transmisión, el apriete de las tuercas y espárragos que fijan la cabeza.
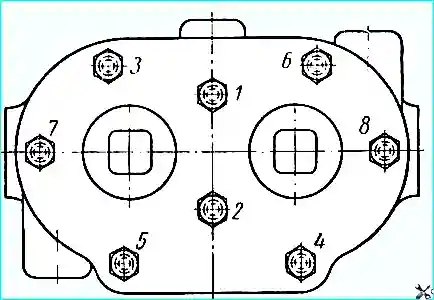
Orden de apriete de las tuercas de la culata del compresor
Las tuercas de los pernos que sujetan la cabeza deben apretarse uniformemente, en dos etapas, en el orden que se muestra en la Fig. 2.
El par de tensión final debe estar dentro de 1,2-1,7 kg/m después de 80.000-100.000 km de kilometraje, combinado con el mantenimiento estacional (en primavera), es necesario desmontar el cabezal del compresor para limpiar los pistones, válvulas, asientos, muelles, aire conductos, así como comprobar el funcionamiento y estanqueidad de las válvulas y émbolos del dispositivo de descarga.
Las válvulas que no proporcionen un sellado hermético deben ser rectificadas en sus asientos, y aquellas que estén muy desgastadas o dañadas deben reemplazarse por otras nuevas.
Las válvulas nuevas también deben ser pulidas sobre los asientos hasta que se logre un contacto continuo con los anillos cuando se prueba la pintura.
Es necesario comprobar el estado de los anillos de estanqueidad de los émbolos 26 (Fig. 1) del dispositivo de descarga y, si es necesario, sustituir los anillos.
En este caso se deberá observar el siguiente orden:
1. Arranque el motor y lleve la presión en el sistema neumático a 7,0-7,4 kg/cm2.
2. Detenga el motor.
3. Retire la manguera de goma que conecta el filtro de aire del motor al compresor.
Si el dispositivo de descarga no es hermético, se oirá un ruido característico del aire que pasa a través de la tubería de suministro de aire al compresor y se notará una ligera caída de presión en el manómetro del sistema neumático.
4. Reducir la presión de aire en el sistema neumático a 5,6-6,0 kg/cm2, mientras se bajan los émbolos.
5. Retire el tubo de suministro de aire, saque el resorte y el balancín,
A continuación, levante el casquillo del vástago del pistón y retírelo junto con el vástago del pistón, después de lo cual retire el émbolo de su casquillo con un gancho de alambre, insertándolo en un orificio de 2,5 mm de diámetro en el extremo del émbolo o suministrando aire comprimido al canal horizontal. del dispositivo de descarga del bloque de cilindros.
6. Reemplace los anillos de sellado de goma desgastados en los émbolos. Antes de la instalación, los émbolos con anillos de sellado deben lubricarse con aceite de motor.
Los signos de mal funcionamiento del compresor incluyen ruidos y golpes en el mismo y una mayor cantidad de aceite en el condensado drenado de los cilindros de aire.
Un mayor contenido de aceite en el condensado suele ser el resultado del desgaste de los anillos del pistón, del sello de aceite en el extremo trasero del cigüeñal, de los cojinetes de las cabezas de las bielas inferiores o de la resinificación del tubo de drenaje de aceite del compresor.
Ajuste de la tensión de la correa de transmisión del compresor
La correa de transmisión del compresor debe tensarse de manera que, cuando se aplique una fuerza de 4 kg, la desviación de la rama de la correa situada entre las poleas del compresor y del ventilador sea igual a 5-8 mm.
La tensión de la correa debe comprobarse diariamente.
La tensión de la correa de transmisión del compresor se ajusta moviendo el compresor.
Para ello, afloje las tuercas que sujetan la cubierta inferior al soporte y utilice el perno de ajuste 20 para asegurar la tensión requerida.
A continuación, debe apretar el soporte del compresor y bloquear el perno de ajuste con una contratuerca.