Zur Demontage empfiehlt sich der Drehständer R-770, auf dem der Motor um die vertikale und horizontale Achse gedreht werden kann
Bevor Sie den Motor auf dem Ständer montieren, entfernen Sie den Ölfilter mit Wärmetauscher, Lüfter, Auspuffkrümmer, vordere Stützhalterungen und den Anlasser;
- - die Reibflächen der Teile, mit Ausnahme der ausdrücklich genannten, bei der Montage mit Motoröl schmieren;
- - Achten Sie beim Befestigen von Teilen mit Schraubverbindungen auf das entsprechende Anzugsdrehmoment;
- - nichtmetallische Dichtungen für eine einfache Montage. Bei Bedarf installieren Sie sie, indem Sie eines der Gegenstücke mit einem gleichmäßigen Schmierfett einfetten.
- - Achten Sie darauf, dass die Dichtungen gleichmäßig an den Passflächen anliegen, fest eingespannt sind und nicht über die Kontur der Passflächen hinausragen;
- - Schmieren Sie beim Einbau die Gummidichtringe und die Anlauffasen der Passteile mit einem gleichmäßigen Fett;
- - Achten Sie beim Aufstecken der Teile darauf, dass die Stifte nicht verbogen werden.
Empfehlungen zum Ausbau, Einbau und zur Prüfung von Motorteilen
So entfernen Sie die Antriebszahnradbaugruppe der Kraftstoffpumpe mit der Welle:
- - Lösen Sie die vier Befestigungsschrauben des Kompressors und entfernen Sie den Kompressor;
- - Lösen Sie die drei Schrauben, mit denen die Servopumpe befestigt ist, und entfernen Sie die Pumpe.
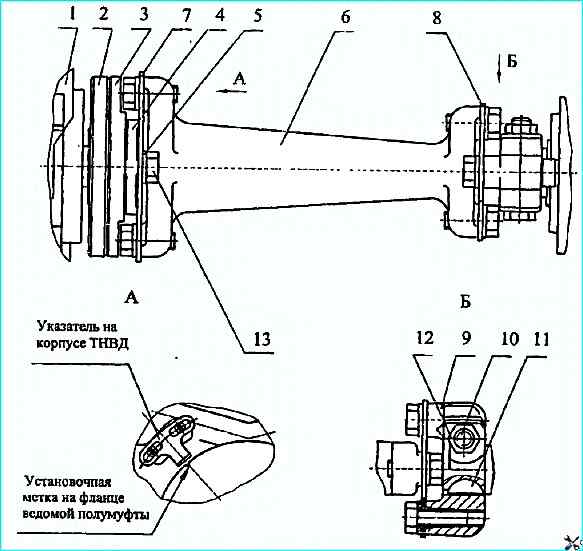
- - Lösen Sie die Spannschraube 10 (Abb. 1)
- - Entfernen Sie die hintere Lagergehäusebaugruppe mit der Manschette;
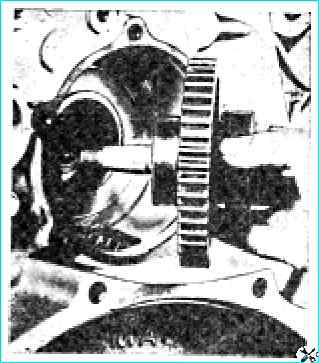
- Antriebszahnrad der Hochdruck-Kraftstoffpumpe mit Welle ausbauen (Abb. Antriebszahnrad der Hochdruck-Kraftstoffpumpe mit Welle ausbauen).
Achten Sie beim Zusammenbau darauf, dass die Markierungen an den Enden des Antriebszahnrads und des Nockenwellenzahnrads aufeinander ausgerichtet sind.
Zum Ausziehen der Zylinderlaufbuchse mit dem Abzieher 801.05.000 (Abb. Ausziehen der Zylinderlaufbuchse mit Abzieher) den Griff an der Schraube 1 entlang klappen und in dieser Stellung in die Laufbuchse einführen.
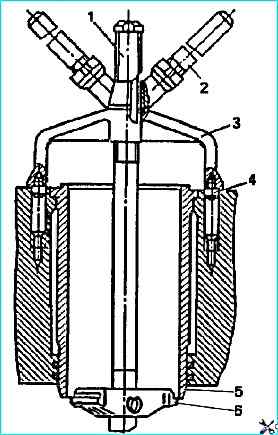
Haken Sie den Griff am unteren Ende der Hülse 5 ein, stellen Sie ihn senkrecht zur Schraube, montieren Sie dann die Stützen 4 im Loch auf der Gegenfläche des Blocks und drehen Sie den Griff 2, schrauben Sie die Schraube heraus, bis die Hülse ist komplett entfernt.
So entfernen Sie das Schwungradgehäuse:
- - den Kompressor entfernen;
- - die Servolenkungspumpe ausbauen;
- - Lösen Sie die drei Schrauben und entfernen Sie das hintere Auge;
- - Entfernen Sie die Klammern, mit denen das Kraftstoffablassrohr an den Einspritzdüsen befestigt ist.
- - Lösen Sie die Befestigungsschraube des Ölmessstabs. Lösen Sie die Schwungradbefestigungsschrauben und die Befestigungsschrauben mit M8-Gewinde
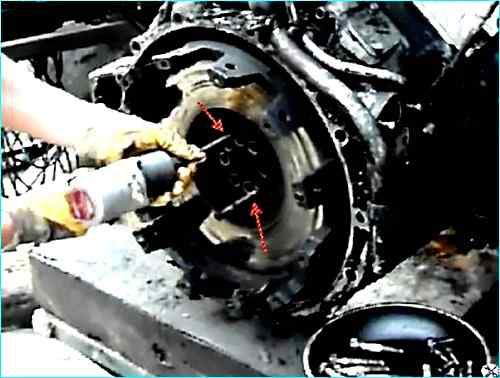
- - das Schwungrad entfernen;
- - Lösen Sie die Befestigungsschrauben des Schwungradgehäuses und entfernen Sie das Gehäuse.
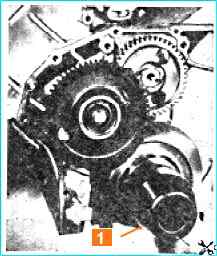
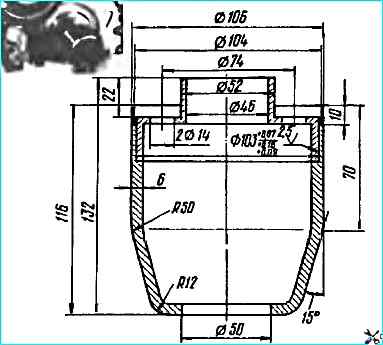
Verwenden Sie beim Einbau des Schwungradgehäuses einen Dorn, um die Manschette der Kurbelwellenenddichtung zu schützen (Abb. Dorn für den Manschetteneinbau des Schwungradgehäuses):
- Dabei die Manschette großzügig mit Motoröl einfetten.
Es gibt sieben Reparaturgrößen von Laufbuchsen zur Reparatur von Kurbelwelle, Block und Pleuel. Die Bezeichnung der Wendeplatte ist auf der Rückseite aufgedruckt.
Zur Demontage und Demontage der Pleuel-Kolben Gruppengeheul:
- - den Zylinderkopf ausbauen (siehe „Gasverteilungsmechanismus“);
- - Kohlenstoffablagerungen vom oberen Riemen der Hülse entfernen;
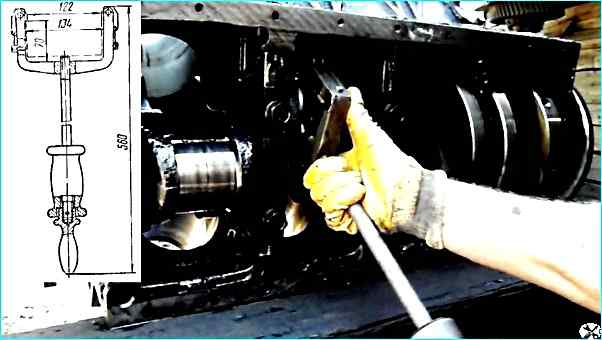
- - Entfernen Sie die untere Pleuelkopfabdeckung mit einem Abzieher (Abb. Entfernen der unteren Pleuelkopfabdeckung mit einem Abzieher):
- - Entfernen Sie die Kolbenbaugruppe mit der Pleuelstange aus dem Zylinder;
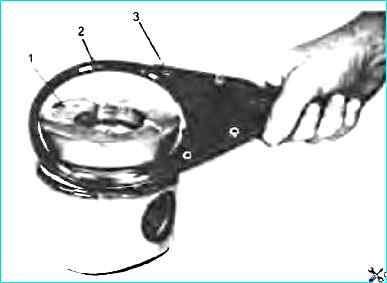
- - Entfernen Sie die Kolbenringe mit einer Vorrichtung (Abb. Entfernen der Kolbenringe mit einem Abzieher);
- - Entfernen Sie die Sicherungsringe mit der Zange И801.23.000 von den Kolbennaben;
- - den Kolben in einem Ölbad auf eine Temperatur von 80-100 ° C erhitzen;
- - Entfernen Sie den Kolbenbolzen.
Beim Zusammenbau und Einbau der Pleuel-Kolben-Gruppe:
- - Kompressionsringe mit der konischen Oberfläche (mit dem Stempel OBER) zum Kolbenboden hin einbauen; bei den Motoren 740.13-260 und 740.14-300 wird der obere Ring so eingebaut, dass sich die innere Nut auf der Unterseite befindet;
- - Die Ölabstreifringe werden wie folgt montiert: Zuerst den Federexpander in die Nut einsetzen, dann den Ölabstreifring so aufsetzen, dass die Stoßstelle des Expanders dem Ringschloss diametral gegenüberliegt;
- benachbarte Ringe mit Sperren in entgegengesetzte Richtungen lenken;
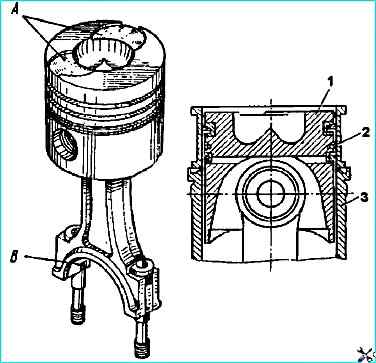
- - Beim Zusammenbau Kolben und Pleuelstange so montieren, dass die Nuten A für die Ventile im Kolbenboden und die Nut „B“ in der Pleuelstange für die Verriegelungsnase der Laufbuchse auf der gleichen Seite liegen (siehe Abb. . Einbau des Kolbens mit Pleuelstange und Ringen in die Laufbuchsen der Zylinder):
- - den Stift nicht in einen kalten Kolben einpressen;
- - Beim Einbau des Kolbens in den Zylinder muss dieser zunächst in den Käfig I801.00.01 eingesetzt werden (siehe Abb. Einbau des Kolbens mit Pleuelstange und Ringen in die Zylinderlaufbuchse):
- - der auf der Kolbenunterseite eingestanzte Index muss mit dem auf dem Hülsenende eingestanzten Index übereinstimmen, wenn der Kolben nicht ausgetauscht wurde. Die Aussparungen für die Ventile am Kolbenboden in Richtung Zylinderblockverkrümmung verschieben.
Die Paarungsmarkierungen der Nummern auf Pleuel und Pleueldeckel müssen übereinstimmen.
Um die Kurbelwelle auszubauen, entfernen Sie:
- - Pleuel- und Kolbengruppe;
- - Schwungradgehäuse;
- - vordere Abdeckung des Blocks mit der hydraulischen Kupplungsbaugruppe;
- - Ölpumpe mit Ölansaugeinheit;
- - Hauptlagerdeckel;
- - Entfernen Sie die Kurbelwelle mit einem oder mehreren Hebezeugen und haken Sie sie mit Messinghaken am ersten und vierten Kurbelzapfen ein.
Beim Einbau der Kurbelwelle in den Motor:
- - Richten Sie die Markierungen auf den Antriebszahnrädern der Einheiten aus;
- - Stellen Sie sicher, dass die Abmessungen der Laufbuchsen mit den Abmessungen der Wellenzapfen übereinstimmen.
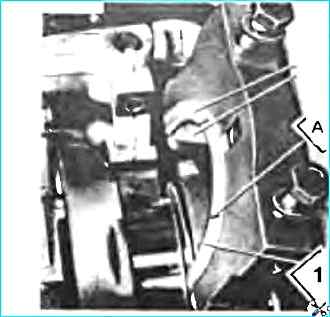
- - Installieren Sie die Axiallager-Halbringe so, dass die Seiten mit den Nuten an den Axialenden der Welle anliegen (siehe Abb. Installieren der Kurbelwellen-Axiallager-Halbringe):
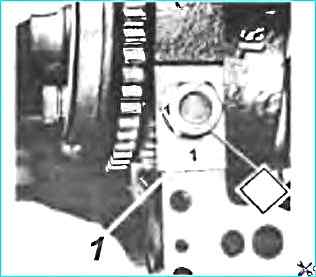
- - Stellen Sie sicher, dass die Nummern der Hauptlagerdeckel mit den Seriennummern der Lager am Zylinderblock übereinstimmen (siehe Abb. Einbau der Hauptlagerdeckel) – die Nummern beginnen am vorderen Ende;
- - Ziehen Sie die Hauptlagerdeckelschrauben und die Blockverbindungsschrauben in der folgenden Reihenfolge fest:
Gewinde in den Blocklöchern und an den Bolzen von Schmutz reinigen, Gewinde an den Bolzen mit Motoröl schmieren, überschüssiges Öl entfernen.
Setzen Sie die Hauptlagerdeckel fest und ohne Verformung auf die Montageflächen.
Die M16-Befestigungsschrauben der Abdeckung mit Unterlegscheiben 16x3 einschrauben und dabei ein vorläufiges Anzugsdrehmoment von 95–120 Nm (9,6–12 kgf.m) beachten.
Dichtung der Fenster Ziehen Sie die Befestigungsschrauben der Abdeckung vorsichtig fest und achten Sie dabei auf ein Anzugsdrehmoment von 275-295 Nm (28 - 30 kgf.m).
Installieren und ziehen Sie die Blockverbindungsschrauben fest. Achten Sie dabei auf ein Anzugsdrehmoment von 147–167 Nm (15–17 kgf.m).
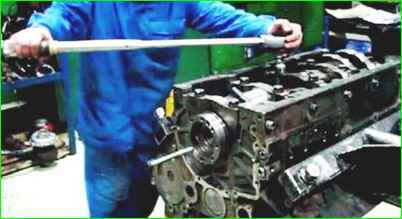
Beim Anziehen von Schrauben mit einem Drehmomentschlüssel sollte der Widerstand gleichmäßig und ohne Ruckanfälle ansteigen. Zählen Sie die Momente, in denen Sie den Schlüssel bewegen.
Nach dem Festziehen sollte sich die Kurbelwelle durch die auf die Schwungrad-Befestigungsstifte ausgeübte Handkraft frei drehen lassen; das Axialspiel im Axiallager sollte mindestens 0,05 mm betragen.
Hinweis: Während der Übergangsphase der Produktionsentwicklung kann der Motor einen Zylinderblock mit verschraubten Stößelstangenführungen, mit übergroßen Nockenwellenbuchsen, ohne übergroße Ölkanäle und mit den folgenden Anzugsdrehmomenten für die Hauptlagerdeckelschrauben verwenden:
- - vorläufiges Anziehen – 95–120 Nm (9,6–12 kgf.m);
- - endgültiges Anziehen – 206–230 Nm (21–23,5 kgf·m).
- - die Zugschrauben werden mit einem Drehmoment von 81–91 Nm (8,2–9,2 kgf m) angezogen.
Zur Demontage und Montage der Kurbelwelle:
- - Entfernen Sie die vorderen und hinteren Gegengewichte sowie das Kurbelwellen-Antriebszahnrad und das Ölpumpen-Antriebszahnrad mit dem Abzieher I801.01.000.
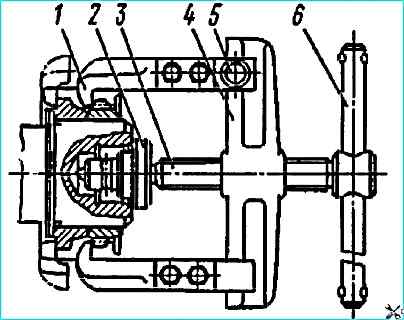
Zum Abnehmen des Kurbelwellenzahnrads und des hinteren Gegengewichts die Backen der Greifzange 1 (siehe Abb. Abnehmen des Zahnrads und des hinteren Gegengewichts der Kurbelwelle mit einem Abzieher) an der Kante des Gegengewichtszahnrads greifen und mit Stoppern 5 fixieren.
Schraube 3 durch Spitze 2 gegen das Ende der Kurbelwelle stecken und durch Drehen des Griffs 6 Schraube 3 in Querträger 4 schrauben, bis das Zahnrad vollständig entfernt ist.
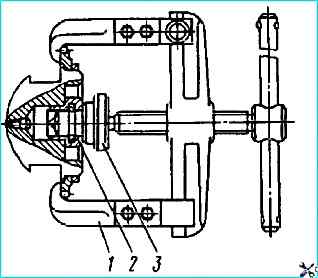
Um das Antriebszahnrad der Ölpumpe und das vordere Kurbelwellengegengewicht zu entfernen (Abb. Entfernen des Antriebszahnrads der Ölpumpe und des hinteren Kurbelwellengegengewichts), installieren Sie Spitze 2 auf Spitze 3 und entfernen Sie das Zahnrad auf die gleiche Weise wie das Entfernen des Kurbelwellenzahnrads ;
- - Drehen Sie den Einsatz um;
- - Reinigen Sie die Ölzufuhrlöcher vor der Montage von Ablagerungen;
- - die Welle waschen und die Kanäle mit Druckluft ausblasen;
Hinweis: Beim Einsatz einer neuen Kurbelwelle ist es notwendig, den Einsatz abzuschrauben, die Welle zu waschen und die Kanäle mit Druckluft auszublasen.
Die Montage der Kurbelwelle erfolgt in umgekehrter Reihenfolge; vor dem Aufpressen des vorderen Gegengewichts, des Ölpumpen-Antriebsrads, des hinteren Gegengewichts und des Kurbelwellen-Antriebsrads auf die Kurbelwelle sind diese auf eine Temperatur von 105 °C zu erwärmen.
Abmessungen der Teile, mm
Kolbenringe:
- Spalt im Kompressionskolbenringschloss * 0,4-0,6
- Spalt im Ölabstreifer Kolbenringschloss * 0,30-0,60
- Endspalt des oberen Kompressionsrings 0,12-0,17
- Unteres Endspiel des Kompressionsrings*. 0,09-0,14
- Endspiel des Ölabstreifrings* 0,077–0,112
Kolben:
- Durchmesser der Löcher für den Finger. 44.987 - 44.994
- Das Spiel in der Kolben-Laufbuchsen-Verbindung (bei einer Kolbenlänge von 104 mm vom Boden) beträgt 0,119-0,162
- * Messen Sie den Kolbenringspalt mit einer 0 (120+0,03) mm Lehre
Ärmel:
Innendurchmesser 120,0 0 - 120,021
Kolbenbolzen:
- Kolbenbolzendurchmesser 44.993-45.000
- Das Spiel in der Verbindung zwischen Kolbenbolzen und oberem Pleuelkopf beträgt 0,017-0,031
Einlagen:
- Dicke der Hauptlagerschale 2.440-2.452
- Dicke der Lagerschalen der Pleuelzapfen. 2.453-2.465
Kurbelwelle;
- Hauptzapfendurchmesser 94,989-95,011
- Lagerspiel in den Hauptzapfen 0,085-0,152
- Kurbelzapfendurchmesser 79,9905-80,0095
- Lagerspiel in Pleuelzapfen 0,06-0,104
- Axialspiel 0,100-0,195
- Durchmesser des Wellenzapfens für das vordere Gegengewicht und das Ölpumpen-Antriebsrad: 125.080-125.110
- Durchmesser des Zapfens der Welle für das hintere Gegengewicht und das hintere Zahnrad der Kurbelwelle: 105.070-105.096
- Durchmesser Wellenzapfenzähler für hintere Manschette: 104,86-105,00
- Durchmesser des Lagersitzes der Primärwelle des Getriebes: 51.977-52.008
- Bohrungsdurchmesser der Schwungrad-Befestigungsbuchse: 51,977–52,008
Halbringe des Axiallagers des fünften Hauptlagers der Kurbelwelle
Dicke 4.010-4.050
Nockenwelle
- Durchmesser der Zwischenlagerzapfen 59.895 - 59.915
- Durchmesser der Zwischenlagerzapfenbuchse 60,00 - 60,03
- Durchmesser des hinteren Stützzapfens. 41.930 - 41.950
- Durchmesser der hinteren Stützzapfenbuchse. 42.000 -42.015
- Spalt im Gegenlagerzapfen - Zwischenlagerzapfen der Nockenwelle: 0,135 -0,085
- Spalt zwischen Gegenhülse und hinterem Lagerzapfen der Nockenwelle: 0,085 - 0,050
- Spalt am Passungsende des hinteren Lagergehäuses - Zahnradnabe: 0,15-0,30
Zahnriementeile
Durchmesser der Schubstange. 21.993 -21.972
Durchmesser Bohrung der Drückerführung 22.000 - 22.023
Spalt zwischen Schubstangen und Führung: nominal 0,007 - 0,051
Abstand zwischen Schaft und Ventilführung, mm:
- - Aufnahme 0,03 - 0,072
- - Version 0.07-0.112
Winkel α der Sitzfase (Einlass, Auslass) 45° - 45°15
Winkel γ der Ventilfase (Einlass, Auslass) 44°45 - 45°
So demontieren Sie den Zylinderkopf zum Austausch und beheben Fehler am Ventilmechanismus und der Zylinder-Kolben-Gruppe:
- - das Kühlmittel aus dem Motorkühlsystem ablassen;
- - Die Befestigungsschrauben des Auspuffkrümmers lösen und den Krümmer abnehmen;
- - Lösen Sie die Schrauben, mit denen der Luftansaugkanal und das Wassersammelrohr am zu entfernenden Kopf befestigt sind, und lockern Sie die Befestigungen dieser Schrauben
Auf anderen Köpfen, um den notwendigen Freiraum zum Entfernen zu erhalten;
Um die rechten Zylinderköpfe zu entfernen, entfernen Sie zuerst den Kompressor vom Motor.
- - das Verbindungsrohr der Luftansaugkanäle entfernen;
- - alle Rohrleitungen vom Kopf trennen und ihre Hohlräume vor Staub und Schmutz schützen;
- - Entfernen Sie die Düse, um das Spritzgerät vor Stößen und Verstopfungen der Löcher zu schützen, den Zylinderkopfdeckel, die Streben zusammen mit den Kipphebeln und Stangen;
- - Lösen Sie die Befestigungsschrauben des Zylinderkopfs und beachten Sie dabei die gleiche Reihenfolge wie beim Anziehen (Abb. Anziehreihenfolge der Befestigungsschrauben des Zylinderkopfs), und schrauben Sie sie dann heraus;
- - Entfernen Sie den Zylinderkopf vom Motor.
Achten Sie beim Einbau des Zylinderkopfes auf den korrekten Einbau der Dichtungen.
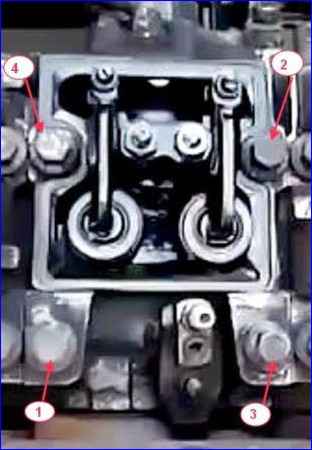
Ziehen Sie die Zylinderkopf-Befestigungsschrauben in drei Schritten in der in der Abb. gezeigten Reihenfolge fest. Reihenfolge des Anziehens der Zylinderkopfschrauben.
Nach dem Anziehen der Schrauben das thermische Spiel zwischen Ventilen und Kipphebeln prüfen und ggf. einstellen.
Zur Demontage und Montage des Ventilmechanismus mit dem Gerät I801.06.000 (siehe Abb. Demontage des Zylinderkopfs mit dem Gerät I801.06.000):
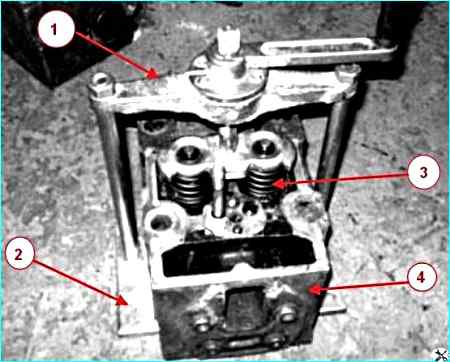
- - Montieren Sie den Zylinderkopf so auf der Basis, dass die Stifte in die Stiftlöcher des Kopfes passen;
- - Den Griff drehen, die Schraube einschrauben und mit einer Platte die Ventilfedern nach unten drücken;
- - Cracker und Buchsen entfernen;
- - Die Schraube vom Querträger lösen, die Platte und die Ventilfedern entfernen;
- - Entfernen Sie die Einlass- und Auslassventile.
Schmieren Sie die Ventilschäfte beim Zusammenbau des Ventilmechanismus mit Dieselöl.
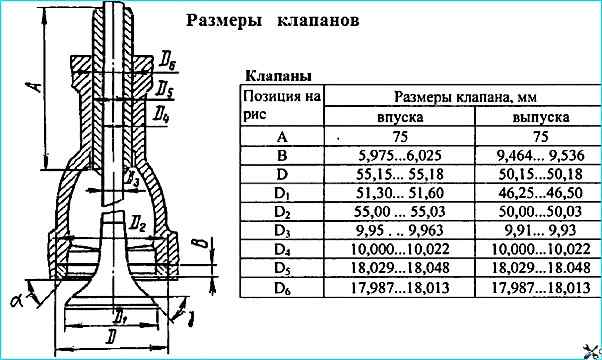
Die Abmessungen der Ventile sind in der Abbildung angegeben
Zum Läppen von Ventilen:
- - zerlegen Sie den Ventilmechanismus wie oben beschrieben;
- - Bereiten Sie eine Paste aus 1,5 Teilen (nach Volumen) grünem Siliziumkarbid-Mikropulver, einem Teil Dieselöl und 0,5 Teilen Dieselkraftstoff vor. Läpppaste vor Gebrauch aufrühren diese (Mikropulver kann sich absetzen);
- - Tragen Sie eine dünne, gleichmäßige Schicht Paste auf die Fase des Ventilsitzes auf und schmieren Sie den Ventilschaft mit Motoröl. Das Läppen wird durch Hin- und Herbewegen und Drehen des Ventils mithilfe eines Bohrers mit Saugnapf oder -vorrichtung durchgeführt.
Halten Sie das Ventil gedrückt und drehen Sie es eine Dritteldrehung und dann eine Vierteldrehung in die entgegengesetzte Richtung. Läppen Sie die Ventile nicht mit kreisenden Bewegungen.
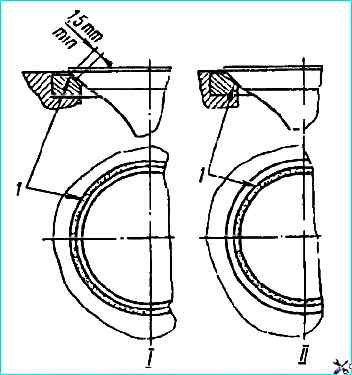
Fahren Sie mit dem Schleifen fort, bis auf den Fasen von Ventil und Ventilsitz ein gleichmäßiger matter Gürtel mit einer Breite von mindestens 1,5 mm erscheint (Abb. Position des matten Gürtels auf dem Ventilsitz);
- Nach dem Schleifen die Ventile und den Zylinderkopf mit Dieselkraftstoff waschen und mit Luft ausblasen.
Bauen Sie den Ventilmechanismus wie oben beschrieben zusammen und ermitteln Sie die Qualität des Ventilschliffs durch Prüfen auf Undichtigkeiten:
- Den Zylinderkopf abwechselnd mit den Einlass- und Auslassöffnungen nach oben montieren und mit Dieselkraftstoff befüllen. Bei gut eingeschliffenen Ventilen darf an den Dichtstellen 30 Sekunden lang keine Luft austreten.
Wenn Kraftstoff austritt, klopfen Sie mit einem Gummihammer auf das Ende des Ventils. Wenn das Leck nicht aufhört, schleifen Sie die Ventile erneut.
Kontrollieren Sie ggf. die Qualität des Läppens „mit dem Bleistift“, indem Sie mit einem weichen Graphitstift sechs bis acht Linien in gleichmäßigen Abständen über die Ventilfase ziehen.
Setzen Sie das Ventil vorsichtig in den Sitz ein und. Drücken Sie fest und drehen Sie eine Vierteldrehung. Alle Linien sollten gelöscht sein. Andernfalls wiederholen Sie den Schleifvorgang.
Beim korrekten Läppen sollte das matte Band auf dem Kopfsitz an der größeren Basis des Sitzkegels beginnen, wie in der Abbildung gezeigt.