Der Ventilsteuerungsmechanismus ist dafür ausgelegt, die Zufuhr von Frischluft in die Zylinder und die Abgabe von Abgasen aus ihnen sicherzustellen
Die Einlass- und Auslassventile öffnen und schließen in bestimmten Positionen des Kolbens, was durch die Ausrichtung der Markierungen auf den Antriebszahnrädern der Einheiten während ihrer Installation sichergestellt wird.
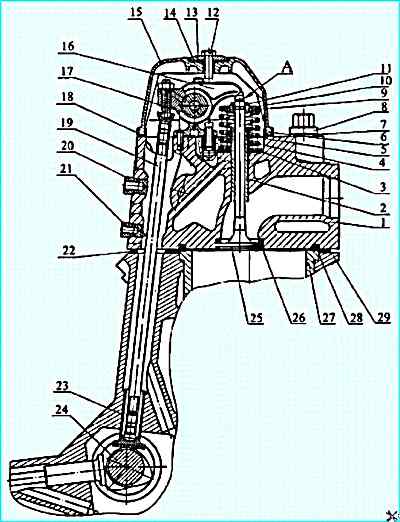
Gasverteilungsmechanismus: 1 - Zylinderkopf; 2 - Führungsbuchse; 3 - Ventilfederscheibe; 4, 5 - Ventilfedern; 6 - Ventilmanschette; 7 - Unterlegscheibe; 8 - Kopfbefestigungsschraube; 9 - Federplatte; 10 - Federplattenbuchse; 11 - Ventilknacker; 12 - Befestigungsschraube der Abdeckung; 13 - Unterlegscheibe; 14 - Schwingungsisolationsscheibe; 15 - Zylinderkopfhaube; 16 - Ventilkipphebel; 17 - Kipphebelständer; 18 - Deckeldichtung; 19 - Langhantel; 20 - Montageeinsatz für Ansaugkrümmer; 21 - Wasserrohr-Montageeinsatz; 22 - Dichtung; 23 - Drücker; 24 – Nockenwelle; 25 - Auslassventil; 26 - Auslasssitz; 27 - Zylinderlaufbuchse; 28 - Gasverbindungsring; 29 - Zylinderblock; (A) - Wärmelücke.
Gasverteilungsmechanismus - obenliegendes Ventil mit niedrigerer Nockenwellenposition.
Die Nockenwellennocken 24 betätigen entsprechend der Ventilsteuerung die Stößel 23.
Stangen 18 übertragen eine Kippbewegung auf die Kipphebel 16, und diese öffnen, den Widerstand der Federn 7 und 8 überwindend, die Ventile 25.
Die Ventile schließen unter der Einwirkung der Druckkraft der Federn.
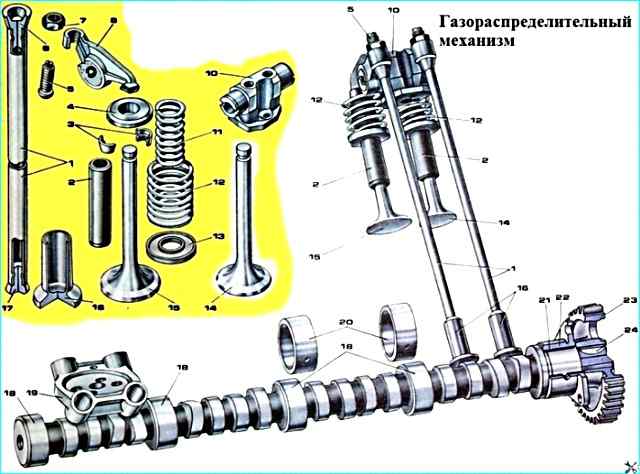
Gasverteilungsmechanismus: 1 - Ventilstößel; 2 - Ventilführungsbuchsen; 3 - Federplatte zur Befestigung der Cracker; 4 - Federplatte; 5 - Einstellschraube; 6 - oberes Ende der Stange; 7 - Nuss; 8 - Ventilkipphebel; 10 - Kipphebelständer; 11 - innere Ventilfeder; 12 - äußere Ventilfeder; 13 - Federscheibe; 14 - Auslassventil; 15 - Einlassventil; 16 - Ventilstößel; 17 - unteres Ende der Stange; 18 - Lagerzapfen der Nockenwelle; 19 - Drückerführung; 20 Nockenwellenzapfenbuchsen; 21 - hintere Nockenwellenbuchse; 22 - Lagergehäuse; 23 - Nockenwellenrad; 24 - Schlüssel
Die Nockenwelle besteht aus Stahl, die Nocken und Lagerzapfen werden einer Hochfrequenz-Wärmebehandlung unterzogen; Es ist im Zylinderblock auf fünf Gleitlagern installiert, bei denen es sich um mit einer Wälzlegierung gefüllte Stahlbuchsen handelt.
Der Durchmesser der Buchsen ist im Vergleich zu den Buchsen des Motormods 6 mm größer. 740.10.
Die Nockenwelle weist im Vergleich zur Nockenwelle des Motormod. vergrößerte Abmessungen sowie geänderte Ventilsteuerung und Ventilhub auf. 740.10.
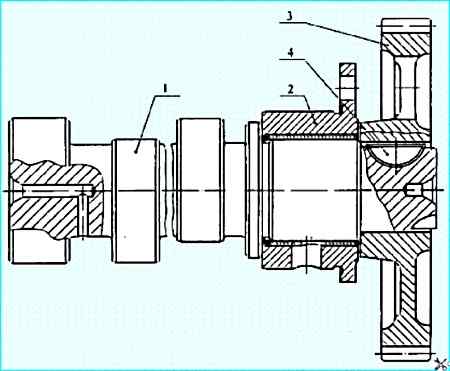
Nockenwelle: 1 - Nockenwelle; 2 - Lagergehäuse; 3 - Gang; 4 - Taste
Auf das hintere Ende der Nockenwelle ist ein geradverzahntes Zahnrad 3 aufgepresst.
Der Antrieb der Nockenwelle erfolgt vom Kurbelwellenrad über Zwischenräder.
Stahlzahnräder, gestanzt mit wärmebehandelten Zähnen.
Um die vorgeschriebene Ventilsteuerung zu gewährleisten, werden die Zahnräder bei der Montage entsprechend den an den Enden eingestanzten Markierungen eingebaut (siehe Artikel „Technische Eigenschaften des Motors KAMAZ 740.11-240“).
Die Welle wird gegen axiale Bewegung durch das Gehäuse 2 des hinteren Stützlagers gesichert, das mit drei Schrauben am Zylinderblock befestigt ist.
Der Aufsetzdurchmesser des hinteren Stützlagergehäuses ist im Vergleich zum Lagergehäuse der Motormod. größer. 740.10.
Einbau des Lagergehäuses der hinteren Nockenwellenhalterung des Motormod. 740.10 ist nicht zulässig, da dies zu einem Notfallabfall des Öldrucks im System und einem vorzeitigen Ausfall des Motors führt.
Hitzebeständige Stahlventile.
Der Winkel der Arbeitsfase der Ventile beträgt 90°. Der Durchmesser der Einlassventilplatte beträgt 51,6 mm, der der Auslassventilplatte 46,6 mm, die Hubhöhe des Einlassventils beträgt 14,2 mm und die der Auslassventilplatte 13,7 mm.
Die Geometrie der Einlass- und Auslassventilplatten gewährleistet die entsprechenden gasdynamischen Parameter des Einlasses und Auslasses von Gasen und daher ihren Ersatz durch Motorventile Mod. 740.10 wird nicht empfohlen.
Die Ventile bewegen sich in Führungsbuchsen aus Metallkeramik.
Um ein Eindringen von Öl in den Zylinder zu verhindern und den Ölverbrauch durch Verbrennung zu reduzieren, sind an den Ventilführungen Gummidichtmanschetten angebracht.
Das Scheibenrollen mit profiliertem Führungsteil, aus Stahl mit anschließender Beschichtung der Scheibenoberfläche mit Hartguss.
Der Drücker wurde einer chemischen und thermischen Behandlung unterzogen.
Die Ventilkipphebel bestehen aus gestanztem Stahl und sind Doppelarmhebel, bei denen das Verhältnis des größeren zum kleineren Arm 1,55 beträgt.
Die Kipphebel der Einlass- und Auslassventile sind auf einem gemeinsamen Ständer montiert und werden mit einem Federteller in axialer Richtung fixiert.
Kipphebel der Motorventile 740.11-240. anders als die Motorkipphebel-Modifikation. 740.10, haben keine Bronzebuchse.
Die Stößelstangenführungen sind aus einem Guss mit dem Zylinderblock gefertigt.
Die Stößelstangen sind aus Stahl, hohl und mit eingepressten Spitzen. Die Stangen sind 3 mm kürzer als die Stangen des Motormod. 740.10 und sind nicht mit diesen austauschbar.
Der Kipphebelständer besteht aus Gusseisen, seine Zapfen werden einer Hochfrequenz-Wärmebehandlung unterzogen.
Der Durchmesser der Zapfen ist im Vergleich zu den Zapfen des Kipphebelständers des Motormod. um 2 mm größer. 740.10.
Bei den Ventilfedern handelt es sich um Schraubenfedern, an jedem Ventil sind zwei davon installiert.
Die Federn haben unterschiedliche Wicklungsrichtungen. Der äußere Federdrahtdurchmesser beträgt 4,8 mm, der innere 3,5 mm.
Die voreingestellte Federkraft beträgt 355 N, die gesamte Arbeitskraft beträgt 821 N. Die Federn sind mit den Motorfedern Mod. austauschbar. 740.10.
Das Verfahren zum Einstellen des Spiels zwischen den Kipphebelspitzen und den Ventilen ist im Abschnitt „Wartung“ beschrieben.
Zylinderköpfe 1 (Abb. 1) sind für jeden Zylinder separat und aus einer Aluminiumlegierung gefertigt. Der Zylinderkopf verfügt über einen Kühlraum, der mit dem Kühlraum des Blocks kommuniziert.
Um die Unterseite des Kopfes zu verstärken, wurde seine Dicke im Bereich des Abgaskanals erhöht und im Vergleich zum Zylinderkopf des Motormods eine zusätzliche Rippe angebracht. 740.10.
Jeder Zylinderkopf ist auf zwei in den Zylinderblock eingepressten Passstiften montiert und mit vier Schrauben aus legiertem Stahl befestigt.
Einer der Befestigungsstifte dient gleichzeitig als Buchse für die Ölzufuhr zur Schmierung der Ventilkipphebel. Die Durchführung ist mit Gummiringen abgedichtet.
Im Kopf ist im Vergleich zum Kopf des 740.10-Motors die Öffnung zum Ablassen des Motoröls unter dem Ventildeckel in den Pleuelraum vergrößert.
Die Einlass- und Auslassöffnungen befinden sich auf gegenüberliegenden Seiten des Zylinderkopfes.
Der Ansaugkanal verfügt über ein tangentiales Profil, um eine optimale Rotationsbewegung der Luftladung zu gewährleisten, die die Parameter des Arbeitsprozesses und der Umweltleistung des Motors bestimmt und daher die Zylinderköpfe des Motormods ersetzt. 740.10 ist nicht zulässig.
Gusseisensitze und Metall-Keramik-Ventilführungen werden in den Kopf gepresst.
Die Ventilsitze weisen im Vergleich zu den Sitzen des Motormods eine erhöhte Interferenzpassung auf. 740.10, und sind mit einer scharfen Kante befestigt.
Der Auslasssitz und das Ventil sind so profiliert, dass sie dem Abgasausstoß weniger Widerstand entgegensetzen.
Anwendung des Auslassventil-Mod. 740.10 wird nicht empfohlen.
Die Verbindung „Zylinderkopf – Zylinderlaufbuchse“ (Gasverbindung) ist dichtungslos (Abb. Gasverbindung).
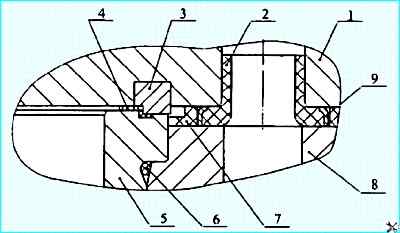
Gasanschluss: 1 - Zylinderkopf; 2 - Dichtring des Kühlmittelbypasses; 3 - Gasverbindungsring; 4 - Einfülldichtung; 5 - Zylinderlaufbuchse; 6 - Dichtring; 7 - Dichtung; 8 - Zylinderblock: 9 - Sieb
In die Bohrung an der unteren Ebene des Kopfes wird ein Stahldichtring 3 eingepresst. Mit diesem Ring wird der Zylinderkopf auf den Flansch der Laufbuchse montiert.
Die Dichtheit der Abdichtung wird durch hochpräzise Bearbeitung der Passflächen von Dichtring und Zylinderlaufbuchse 5 gewährleistet.
Der Dichtring verfügt zusätzlich über eine Bleibeschichtung zum Ausgleich von Mikrorauigkeiten der Dichtflächen.
Zur Reduzierung schädlicher Volumina ist in der Gasverbindung - Füllstück 4 eine Fluorkunststoffdichtung eingebaut.
Die Dichtung - der Füller wird mittels eines umgekehrten Konus unter Spannung auf dem überstehenden Band des Gasdichtrings fixiert.
Durch den Einsatz einer Einfülldichtung werden der spezifische Kraftstoffverbrauch und die Abgasqualmung verringert. Einweg-Fülldichtung.
Zur Abdichtung der Kühlmittel-Bypasskanäle sind in den Löchern an der Unterseite des Kopfes 2 Dichtringe aus Silikonkautschuk eingebaut.
Der Raum zwischen Kopf und Block, die Motorölablasslöcher und die Stangendurchgangslöcher sind mit einer Zylinderkopfdichtung 7 aus hitzebeständigem Gummi abgedichtet.
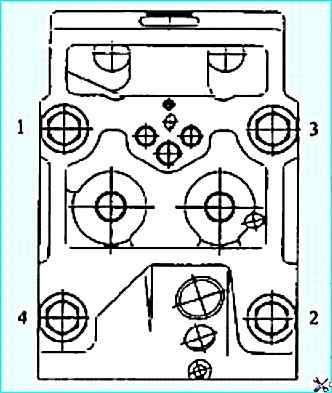
Anzugsreihenfolge für Zylinderkopfschrauben
Beim Zusammenbau des Motors sollten die Zylinderkopf-Befestigungsschrauben in drei Schritten in der in der Abbildung gezeigten aufsteigenden Nummernreihenfolge angezogen werden. 5
Die Anzugsdrehmomentwerte sollten sein:
- 1 Stufe – bis zu 39–49 Nm (4–5 kgf.m);
- 2. Empfang - bis zu 98–127 Nm (10–13 kgf.m);
- 3. Aufnahme - bis zu 186-206 Nm (19-21 kgf.m
Vor dem Einschrauben das Bolzengewinde mit einer Schicht Graphitfett schmieren.
Nach dem Anziehen der Schrauben muss das Spiel zwischen den Ventilen und den Kipphebeln eingestellt werden (das Einstellen des Ventilspiels wird im Artikel „Allgemeine Informationen zur Wartung des KAMAZ-Motors“ beschrieben).
Der Ventilmechanismus ist mit einer Aluminiumabdeckung 15 abgedeckt (siehe Abb. 1).
Zur Geräuschdämmung und Abdichtung der Verbindung zwischen Deckel und Zylinderkopf dienen eine schwingungsisolierende Unterlegscheibe 14 und eine Gummidichtscheibe 19.
Ziehen Sie die Befestigungsschrauben der Zylinderkopfhaube mit einem Drehmoment von 12,7–17,6 Nm (1,3–1,8 kgf.m) fest.
Hauptfehler des Ventilsteuerungsmechanismus
Abweichungen im Betrieb des Gasverteilungsmechanismus während des natürlichen Verschleißes von Teilen führen zu einer Verschlechterung der Dynamik des Mechanismus und tragen zu einem beschleunigten Verschleiß der Gegenteile bei. 25-27 % der Gesamtausfälle aller Motorsysteme sind auf den Zahnriemen zurückzuführen.
Die wichtigsten durch Zahnriemenfehler verursachten Motorstörungen können folgende sein:
- - Abnahme der Motorleistung, Anstieg des Kraftstoff- und Ölverbrauchs;
- - Zunahme der Rauchentwicklung durch Abgase;
- - Öldruckabfall im Motorsystem bei Temperaturen über 0° C;
- - instabiler Motorlauf im Leerlauf;
- - der Motor läuft unregelmäßig oder überhitzt;
- - Flüssigkeitslecks in den Anschlüssen des Kühlsystems.
Anzeichen für eine Fehlfunktion des Zahnriemens sind Klopfgeräusche im Zylinderkopf.
Ein lautes Klopfen im Zylinderkopf wird durch das Schlagen der Ventile gegen die Kipphebel verursacht, da zwischen dem Ventil und der Spitze des Kipphebels ein großer thermischer Spalt besteht.
Ein dumpfes metallisches Klopfen im Leerlauf und dessen Verstärkung bei Kraftstoffzufuhr sind Anzeichen für gebrochene Ventilfedern oder festsitzende Ventile.
Ein lockerer Ventilsitz liegt vor, wenn zwischen Kipphebelspitze und Ventil kein oder nur ein reduziertes thermisches Spiel vorhanden ist, sowie wenn die Belastbarkeit der festen Verbindung zwischen Zylinderkopf und Ventilsitz beeinträchtigt ist.
Wenn das Ventil nicht fest auf dem Sitz sitzt, bilden sich in bestimmten Bereichen Lücken zwischen Ventil und Sitz.
In die entstehenden Risse dringen heiße Gase unter Druck und mit hoher Geschwindigkeit ein, so dass die Fasenflächen an dieser Stelle stark korrodieren und die Passung der Fase zum Sitz sich verschlechtert.
Auf der Oberfläche der Fase sammeln sich Verbrennungsprodukte, wodurch die Dichtheit der Verbindung beeinträchtigt wird.
Eine Analyse typischer Schäden an Ventilen und Ventilsitzen zeigt, dass etwa 90 % aller Schäden dadurch entstehen, dass die Dichtheit der Verbindung zwischen Ventilsitz und Ventil beeinträchtigt ist.
Bei einer Vergrößerung des thermischen Spiels verringert sich der Ventilhub, was eine mangelhafte Füllung und Reinigung der Zylinder, erhöhte Stoßbelastungen und Verschleiß der Steuerteile zur Folge hat.
Bei sehr kleinen thermischen Spaltmaßen kommt es infolge von Verbrennungen oder Verschleiß der Arbeitsfasen von Ventil oder Ventilsitz zu einer Undichtigkeit des Brennraums, der Motor verliert an Kompression, überhitzt und entwickelt nicht die volle Leistung.
Die häufigsten Zahnriemenfehler sind die folgenden:
- – vorzeitiger Verschleiß der Sitz- und Ventilsitzflächen; Ventilführungsverschleiß;
- – Verletzung der Stabilität der Passung in der Verbindung Ventilsitz – Zylinderkopf;
- – Verformung des Zylinderkopfes;
- – Verformung des Ventilsitzes und des Ventilschafts;
- – Verformung der Ventilplatte; Ventilschaftbruch und Korrosion; Verschleiß der Stößellöcher;
- – Verschleiß der Nockenwellenbuchsen; Verschleiß der Nockenwellen; Verschleiß der Ventilkipphebel.
Vor der Durchführung einer Wartung ist eine individuelle Überwachung des Zustands des Zahnriemens erforderlich. Diese ermöglicht es, mithilfe spezieller Ausrüstung und ohne Demontage des Motors die oben genannten versteckten Fehler im Voraus zu erkennen und eine Liste mit Vorbeugungs- und Reparaturmaßnahmen festzulegen.
Der technische Zustand des Zahnriemens sollte anhand von Diagnoseparametern beurteilt und der Bedarf an Wartungs- und Reparaturarbeiten anhand der Grenzwerte dieser Parameter bestimmt werden.
Ein typischer Defekt der Ruten: Lockerer Sitz der Spitzen und Verbiegung des Rutenschaftes.
Typische Defekte an Ventilen sind Verschleiß der Arbeitsfasen, Verbiegung des Schaftes, Bruch der Ventilplatte, Verschleiß der Ventilstirnfläche
Typische Defekte an Drückern sind Verschleiß der Platte, ein Einsinken auf der Arbeitsfläche, Verschleiß der Stange
Verschlissene Platten und Stößelstangen werden durch Verchromen wiederhergestellt.
Nach der Restaurierung werden die Ventile in ihre Sitze eingeschliffen Zylinder-Geschicklichkeit.