Die Nockenwelle besteht aus Stahl, mit gehärteten Nocken und einem Zahnrad zum Antrieb des Zündverteilers, und wird über zwei Zahnräder angetrieben
Die Nockenwelle ruht auf fünf mit Bimetall-Bandbuchsen ausgestatteten Stützen; das diametrale Spiel der Nockenwellenlager beträgt beim neuen Motor 0,03–0,09 mm für die vier vorderen Lager und 0,025–0,077 mm für das fünfte hintere Lager.
Die axiale Bewegung der Nockenwelle wird durch einen Flansch zwischen dem Zahnrad und dem vorderen Ende des ersten Zapfens begrenzt, der mit zwei Schrauben am vorderen Ende des Blocks befestigt ist.
Der Unterschied zwischen der Höhe des auf dem vorderen Zapfen der Nockenwelle aufgesetzten Distanzrings und der Dicke des Flansches beträgt 0,08–0,208 mm.
Diese Werte entsprechen dem Axialspiel der Nockenwelle eines neuen Motors.
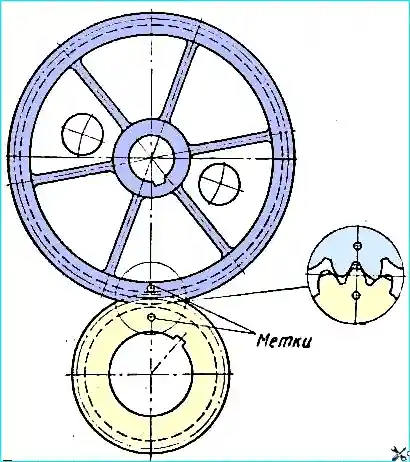
Für die korrekte gegenseitige Montage der Zahnräder ist es notwendig, das Kurbelwellenzahnrad und das Nockenwellenzahnrad so anzuordnen, dass die Markierungen auf derselben Linie liegen, die die Mittelpunkte dieser Zahnräder verbindet (Abb. 1).
Ventile - obenliegend, im Zylinderkopf in einer Reihe angeordnet, zur Zylinderachse geneigt; werden über Stangen, Stößel und Kipphebel von der Nockenwelle angetrieben.
Die Ventile bestehen aus hitzebeständigem Stahl; - der Winkel der Arbeitsfase des Einlassventilsitzes beträgt 30°, der des Auslassventilsitzes 45°; Der Auslassventilschaft verfügt über eine mit Natrium gefüllte Bohrung und die Ventilplatte hat am Sitz eine hitzebeständige Schweißfase.
Um die Lebensdauer der Auslassventile zu erhöhen, werden diese während des Motorbetriebs durch einen speziellen Mechanismus zwangsweise verdreht.
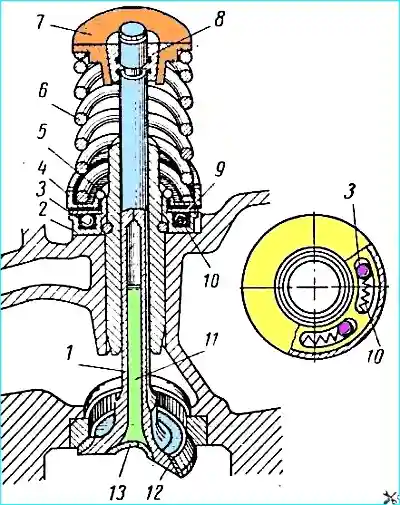
Der Mechanismus zum Drehen des Auslassventils (Abb. 2) besteht aus einem festen Gehäuse 2, fünf Kugeln 3 und ihren Rückholfedern 10 (in schrägen, bogenförmigen Aussparungen des Gehäuses angeordnet), einer Tellerfeder 9, einer Anlaufscheibe 4, auf die die Ventilfeder über einen Sicherungsring 5 drückt.
Die Anlaufscheibe 4 und die Tellerfeder mit Spalt werden auf den Gehäusevorsprung aufgesetzt, der sich in einer speziellen Aufnahme im Zylinderkopf befindet (Abb. 3).
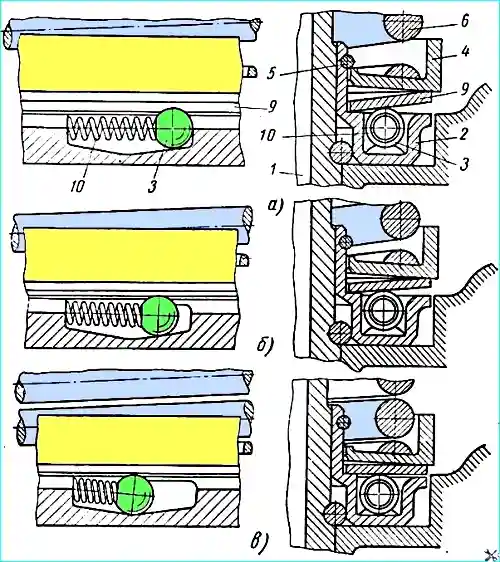
Bei geschlossenem Ventil (Abb. 3, a) wird die Kraft der Feder 6 über die Anlaufscheibe 4 auf die Außenkante der Tellerfeder 9 übertragen, die mit ihrer Innenkante auf der Schulter des Gehäuses 2 aufliegt.
Beim Öffnen des Ventils (Abb. 3, b) erhöht sich die Kraft der Ventilfeder; unter dem Einfluss erhöhter Kraft richtet sich die auf den Kugeln ruhende Tellerfeder auf;
- Zwischen der Innenkante der Feder und der Schulter des Gehäuses entsteht ein Spalt, und die Kraft der Federn 10 beginnt, auf die Kugeln 3 übertragen zu werden, die entlang der geneigten Oberflächen der Aussparungen rollen und die Tellerfeder 9 und die Anlaufscheibe 4 in einem bestimmten Winkel drehen und mit ihnen die Ventilfeder 6 und das Ventil 1.
Beim Schließen des Ventils (Abb. 3, c) nimmt die Kraft der Ventilfeder ab, die Auslenkung der Tellerfeder vergrößert sich; sie liegt an der Schulter des Gehäuses an und gibt die Kugeln frei, die unter der Einwirkung der Federn in ihre Ausgangsposition zurückkehren und sich zwischen der Unterlegscheibe und der geneigten Oberfläche des Gehäuses verkeilen.
Beim Zerlegen eines Motors, der mehr als 70.000 km gelaufen ist, ist es notwendig, den Zustand der Federn 10 (siehe Abb. 2 und 3) und der Kugeln des Auslassventil-Drehmechanismus zu überprüfen.
Sollten an den Federwindungen Verschleißspuren erkennbar sein, muss die Feder mit der verschlissenen Stelle nach unten gedreht werden.
Beim Zusammenbau des Ventildrehmechanismus muss auf die korrekte Montage der Kugeln und Federn geachtet werden.
Bei korrekter Montage sollten die Federn einen Abstand haben Je nach gewählter Drehrichtung wird die Kugel hinter der Kugel platziert.
Ventilkipphebel bestehen aus geschmiedetem Stahl und haben eine Bronzebuchse.
Ventilstößel bestehen aus Stahl und sind hohl. Um die Zuverlässigkeit des Nocken-Drückerpaares zu erhöhen, wird am Ende des Drückers ein spezielles Gusseisen angeschweißt.
Im unteren Teil des Stopfers befinden sich Löcher, um das in den Stopfer gelangte Öl abzulassen.
Stahlstangen mit gehärteten Kugelenden.
Der für beide Zylinderbänke gemeinsame Ansaugkrümmer aus einer Aluminiumlegierung befindet sich zwischen den Zylinderköpfen und ist mit einem Wassermantel zur Erwärmung des Gemischs ausgestattet.
Die Muttern, mit denen der Ansaugkrümmer am Zylinderkopf befestigt ist, müssen gleichmäßig und überkreuz von der Mitte zu den Rändern des Krümmers angezogen werden, damit die Gummidichtung nicht aus der Verbindung zwischen Ansaugkrümmer und Kopf herausgedrückt wird.
Das Anzugsdrehmoment der Muttern sollte zwischen 2 und 2,5 kgm liegen.
Die Abgasleitungen bestehen aus Verbundwerkstoff und Temperguss, eine auf jeder Seite des Blocks.
Die Montage der Verbundgasleitung am Motor muss in folgender Reihenfolge erfolgen:
- - die Dichtungsfuge muss sich unter der Klemmverschraubung befinden; die Achse der Schraube, mit der die Klemme am kurzen Arm der Gasleitung festgezogen wird, muss senkrecht zu den Flanschen der Gasleitungsbefestigung am Zylinderkopf stehen;
- - Die Achse der Schraube, mit der die Klemme am langen Arm der Gasleitung festgezogen wird, muss parallel zu den Flanschen der Gasleitungsbefestigung am Zylinderkopf verlaufen.
Die Schraube wird mit dem Kopf nach oben eingebaut; Schraubenanzugsdrehmoment 1,4-1,7 kgm.
Ziehen Sie die Muttern, mit denen die Abgasverbundleitung am Zylinderkopf befestigt ist, in der folgenden Reihenfolge fest: Mittelflansch – zuerst die untere Mutter festziehen, dann die obere, Anzugsdrehmoment 4–4,5 kgm; Extremflansche - Muttern sollten mit einem Anzugsdrehmoment von 3-3,5 kgm festgezogen werden.