Motorschmiersystem – kombiniert: unter Druck und Spritzwasser
Öl unter Druck schmiert die Haupt- und Pleuellager der Kurbelwelle, die Nockenwellenlager, die Drucklager der Kurbelwelle und der Nockenwelle, die Kipphebelbuchsen und die oberen Spitzen der Stößelstangen
Die restlichen Teile werden mit aufgesprühtem Öl geschmiert.
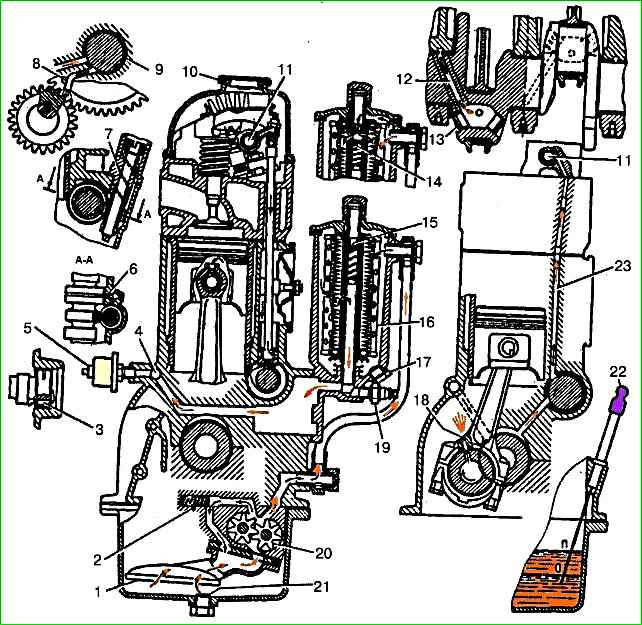
Das Schmiersystem umfasst eine Ölpumpe 20 mit einem Einlassrohr und einem Druckminderventil (in der Ölwanne installiert), Ölkanäle, einen Ölfilter mit Bypassventil, eine Ölwanne, eine Ölstandsanzeige und ein Öl Einfülldeckel, ein Öldruckanzeigesensor, ein Alarmsensor für den Notöldruck.
Das von der Pumpe aus der Ölwanne angesaugte Öl gelangt durch den Ölbehälter über Kanäle im Pumpenkörper und im Außenrohr in das Ölfiltergehäuse.
Nachdem das Öl das Filterelement 16 passiert hat, gelangt es in den Hohlraum der zweiten Trennwand des Zylinderblocks, von wo aus es durch einen gebohrten Kanal in die Ölleitung – den Öllängskanal 4 – gelangt.
Vom Längskanal wird das Öl über geneigte Kanäle in den Blocktrennwänden den Hauptlagern der Kurbelwelle und den Nockenwellenlagern zugeführt.
Das Öl, das vom fünften Nockenwellenträger in den Hohlraum des Blocks zwischen Welle und Stopfen fließt, wird durch eine Querbohrung im Wellenzapfen in das Kurbelgehäuse abgeleitet.
Das Öl fließt durch die Kanäle 12 von den Hauptzapfen der Kurbelwelle zu den Pleuelzapfen.
Öl wird der Kipphebelachse vom hinteren Nockenwellenträger zugeführt, der in der Mitte eine Ringnut aufweist, die über Kanäle 23 im Block, Zylinderkopf und im vierten Hauptpfosten der Kipphebelachse mit dem Hohlraum 11 in Verbindung steht die Wippachse.
Durch die Löcher in der Kipphebelachse fließt Öl zu den Kipphebelbuchsen und dann durch die Kanäle in den Kipphebeln und Einstellschrauben zu den oberen Spitzen der Stößelstangen.
Öl wird den Nockenwellenantriebsrädern über ein Rohr 8 zugeführt, das in ein Loch im vorderen Ende des Blocks eingepresst ist und mit der Ringnut 9 am ersten Lagerzapfen der Nockenwelle verbunden ist.
Aus dem Auslass des Rohrs, das einen kleinen Durchmesser hat, wird ein Ölstrahl ausgestoßen, der auf die Zahnradzähne gerichtet ist.
Durch einen Querkanal im ersten Zapfen der Nockenwelle fließt Öl aus derselben Nut im Zapfen zum Druckflansch der Nockenwelle.
Die Antriebsräder der Ölpumpe werden durch einen Ölstrom geschmiert, der aus Kanal 6 im Block ausgestoßen wird, der mit dem vierten Nockenwellenzapfen verbunden ist, der ebenfalls eine Ringnut aufweist.
Die Zylinderwände werden durch Ölspritzer aus dem Strahl geschmiert, der aus Loch 18 im unteren Kopf der Pleuelstange ausgestoßen wird, wenn dieses Loch mit dem Kanal im Kurbelwellenzapfen zusammenfällt, sowie durch Öl, das unter den Kurbelwellenlagern hervorfließt.
Alle anderen Teile (Ventil – Schaft und Ende, Antriebswelle der Ölpumpe und Zündverteiler, Nockenwellennocken) werden mit Öl geschmiert, das aus den Lagerspalten fließt und von sich bewegenden Motorteilen verspritzt wird.
Kapazität des Schmiersystems - 6 l.
Das Öl wird durch den Öleinfüllstutzen am Ventildeckel in den Motor eingefüllt und mit einem Deckel mit Gummidichtung verschlossen.
Der Ölstand wird durch die Markierungen „P“ und „O“ auf der Ölstandsanzeigestange kontrolliert. Der Ölstand sollte zwischen den Markierungen „P“ und „O“ gehalten werden.
Der Druck im Schmiersystem sollte bei durchschnittlichen Fahrzeuggeschwindigkeiten (ca. 50 km/h) 200–400 kPa (2–4 kgf/cm 2) betragen.
Sie kann bei kaltem Motor auf 450 kPa (4,5 kgf/cm 2) ansteigen und bei heißem Wetter auf 150 kPa (1,5 kgf/cm 2) sinken.
Reduzierung des Öldrucks bei einer durchschnittlichen Drehzahl unter 100 kPa (1 kgf/cm 2) und bei niedriger Leerlaufdrehzahl – unter 50 kPa (0,5 kgf/cm 2). ) weist auf eine Fehlfunktion des Schmiersystems oder übermäßigen Verschleiß hin Kurbelwellen- und Nockenwellenlager.
Der weitere Betrieb des Motors unter diesen Bedingungen muss gestoppt werden.
Der Öldruck wird durch ein Messgerät auf der Instrumententafel ermittelt, dessen Sensor in das Ölfiltergehäuse eingeschraubt ist.
Zusätzlich ist das System mit einer Öldruckwarnlampe ausgestattet, deren Sensor in das Loch im Boden des Filters eingeschraubt wird.
Die Warnleuchte befindet sich auf der Instrumententafel und leuchtet rot, wenn der Druck im System unter 40–80 kPa (04–0,8 kgf/cm 2) fällt.
Sie können ein Fahrzeug nicht fahren, wenn die Notöldrucklampe leuchtet.
Bei niedriger Leerlaufdrehzahl und beim Bremsen ist nur ein kurzzeitiges Aufleuchten der Lampe zulässig.
Wenn das System ordnungsgemäß funktioniert, erlischt die Lampe bei einer leichten Erhöhung der Drehzahl.
Wenn der Öldruck zu niedrig oder zu hoch gegenüber den oben genannten Werten ist, sollten Sie zunächst die Funktionstüchtigkeit der Sensoren und Anzeigen prüfen.
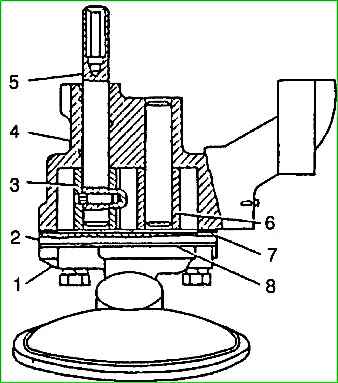
Die Zahnradölpumpe ist im Ölsumpf installiert.
Die Pumpe ist mit zwei Bolzen an geneigten Plattformen an der dritten und vierten Trennwand des Zylinderblocks befestigt.
Die präzise Montage der Pumpe wird durch zwei in den Zylinderblock eingepresste Buchsenstifte gewährleistet.
Pumpenkörper 4 ist aus einer Aluminiumlegierung gegossen, die Zahnräder 3 und 6 haben gerade Zähne und bestehen aus Cermet (Sintermetallpulver).
Antriebsrad 3 ist mit einem Stift an Rolle 5 befestigt.
Am oberen Ende der Walze befindet sich ein sechseckiges Loch, in das die Antriebswelle der Ölpumpe passt.
Das angetriebene Zahnrad 6 dreht sich frei auf einer in das Pumpengehäuse eingepressten Achse.
Pumpendeckel 2 besteht aus Grauguss und wird mit vier Schrauben an der Pumpe befestigt.
Unter der Abdeckung befindet sich eine 0,3 mm dicke Pappdichtung.
Der Ölbehälter und das Einlassrohr 1 der Ölpumpe sind in einem einzigen Gehäuse aus einer Aluminiumlegierung untergebracht. Der aufnehmende Teil des Rohres hat ein gerolltes Netz.
Das Rohr ist mit vier Schrauben an der Ölpumpe befestigt, zusammen mit dem Ölpumpendeckel durch eine Paronitdichtung 8.
Die Leistung der Ölpumpe ist deutlich höher als die des Motors.
Die Kapazitätsreserve ist notwendig, um in jedem Motorbetriebsmodus einen ausreichenden Öldruck im System sicherzustellen.
Überschüssiges Öl fließt aus dem Druckhohlraum der Pumpe durch das Druckminderventil zurück in den Saughohlraum.
Wenn der Ölfluss durch die Lagerspalte zunimmt (bei Motorverschleiß), bleibt auch der erforderliche Druck im System erhalten, allerdings gelangt in diesem Fall eine geringere Ölmenge durch das Druckminderventil zurück in das System Aufnahmeraum der Pumpe.
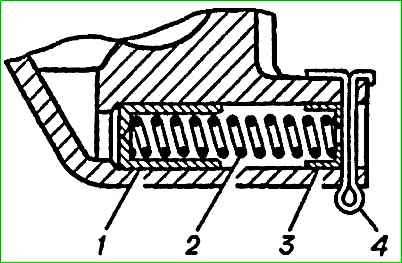
Im Ölpumpengehäuse befindet sich ein Kolbendruckminderventil. Das Ende des Kolbens 1 steht unter Öldruck, unter dessen Einfluss sich der Kolben bewegt und dabei die Kraft der Feder 2 überwindet.
Wenn ein bestimmter Druck erreicht ist, öffnet der Kolben das Loch im Abflusskanal, sodass überschüssiges Öl in den Aufnahmehohlraum der Pumpe fließen kann.
Die Feder des Druckminderventils ruht auf einer flachen Unterlegscheibe 3 und ist mit einem Splint 4 gesichert, der durch die Löcher in der Nabe am Pumpenkörper geführt wird.
Das Druckminderventil ist nicht einstellbar; Die erforderliche Druckcharakteristik ergibt sich aus den geometrischen Abmessungen des Pumpengehäuses und den Eigenschaften der Feder: Um die Feder auf eine Länge von 40 mm zusammenzudrücken, ist eine Kraft im Bereich von 435–48,5 N (435–485 kgf) erforderlich .
Im Betrieb darf die Federkraft des Druckminderventils in keiner Weise verändert werden.
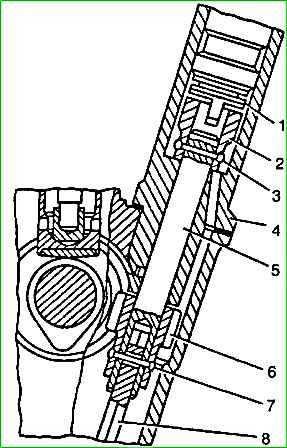
Die Ölpumpe und der Zündverteiler werden von der Nockenwelle über ein Paar Schrägverzahnungen angetrieben.
Das Antriebsrad besteht aus Stahl und ist in den Körper der gusseisernen Nockenwelle eingegossen.
Das Antriebsrad 8 besteht aus wärmefestem Stahl und ist mit einer Rolle 5 verbunden, die sich in einem Gusseisengehäuse dreht.
Das obere Ende der Walze ist mit einer Hülse 2 mit einem ausgestattet Schlitz (um 1,15 mm von der Achse der Walze versetzt) zum Antrieb des Zündverteilersensors.
Die Buchse auf der Welle wird mit einem Stift 3 gesichert. Mit dem unteren Ende der Welle ist eine Sechskantwelle 10 schwenkbar verbunden, deren unteres Ende in das Sechskantloch der Ölpumpenwelle passt.
Beim Drehen wird das Zahnrad 8 durch die Druckscheiben 6 und 7 gegen das Ende des gusseisernen Antriebsgehäuses gedrückt.
Die Schmierung dieser Einheit sowie der Rolle im Antriebsgehäuse erfolgt durch Öl, das von den Antriebsrädern versprüht wird und an der Blockwand herunterfließt.
Das an den Wänden herunterfließende Öl gelangt in den Schlitz (Falle) am unteren Ende des Antriebsgehäuses und dann durch das Loch auf die Oberfläche der Walze.
In das Loch für die Rolle im Antriebsgehäuse ist eine spiralförmige Nut eingeschnitten, entlang der das Öl beim Drehen der Rolle nach oben steigt und sich gleichmäßig über die gesamte Länge verteilt.
Überschüssiges Öl aus dem oberen Hohlraum des Antriebsgehäuses wird durch die Ablassöffnung im Gehäuse zurück in das Kurbelgehäuse abgeleitet.
Die korrekte Position des Zündverteilersensors am Motor wird dadurch gewährleistet, dass der Antrieb so im Block eingebaut wird, dass, wenn sich der Kolben des ersten Zylinders im OT (Kompressionshub) befindet, der Schlitz an der Antriebshülse ist parallel zur Motorachse im maximalen Abstand davon.
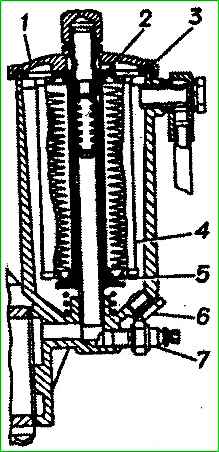
Der Ölreinigungsfilter ist ein Vollstromfilter mit austauschbaren Filterelementen aus Papier oder Baumwolle. Das gesamte in das System gepumpte Öl passiert den Filter.
Für diese Motoren werden folgende Filterelemente verwendet: NAMI-VG-10, REGOTMAS-412-1-05 und REGOTMAS-412-1-06.
Der Filter besteht aus einem Gehäuse, einem Deckel 1, einer zentralen Stange mit einem Bypassventil und einem Filterelement 4.
Das Filtergehäuse besteht aus einer Aluminiumlegierung und ist über eine Paronitdichtung mit vier Bolzen am Zylinderblock befestigt.
Die zentrale Stange ist fest in den Körper eingeschraubt. Am oberen Ende der Stange befindet sich ein Gewinde für die Mutter zur Befestigung der Filterabdeckung.
Ein Stopfen 6 wird von unten in das Gehäuse eingeschraubt, um abgesetzte Verunreinigungen abzuleiten.
Der Notöldrucksensor 7 ist in die Nabe im unteren Teil des Gehäuses eingeschraubt.
Filterabdeckung 1 besteht aus einer Aluminiumlegierung. Die Befestigung erfolgt mit einer Hutmutter, die auf das Gewindeende der aus dem Deckel herausragenden Mittelstange aufgeschraubt wird.
In der Nut der Abdeckung befindet sich eine Gummidichtung. Die Deckelmutter ist mit einer Kupferdichtung abgedichtet.
Der zentrale Filterstab ist hohl.
In seinem oberen Teil befindet sich ein Bypassventil, bestehend aus einer Textolithplatte des Ventilsitzes, einer Feder und einem Federanschlag.
Die Stange verfügt über vier Lochreihen für den Öldurchgang; Die oberste Reihe befindet sich über dem Ventil und über dem Filterelement.
Im Normalzustand des Elements ist sein Widerstand gering, etwa 10–20 kPa (0,1–0,2 kgf/cm 2), und das gesamte Öl strömt durch das Element hindurch, wie in der Abbildung gezeigt Diagramm mit Pfeilen .
Vom Filterelement gelangt das gereinigte Öl durch die Löcher in die Stange und weiter in das Schmiersystem.
Wenn das Element verstopft ist, erhöht sich sein Widerstand, und wenn der Druck 70–90 kPa (0,7–0,9 kgf/cm 2) erreicht, öffnet sich das Bypassventil und beginnt, Öl durchzulassen.
Beim Einbau in das Gehäuse werden die Enden des Filterelements von unten und oben mit den Ringen 2 und 5 aus ölbeständigem Gummi abgedichtet, die den Mittelstab dicht abdecken.
Die Abdichtung an den Enden wird durch eine Feder und eine Stützscheibe gewährleistet, die das Element an das Ende des Deckelvorsprungs drücken.