Checking the condition of brake drums, pads and friction linings of wheel brake mechanisms is carried out at each maintenance-2
The remaining thickness of the brake linings can be checked through inspection windows in the brake drums or brake guards.
If the lining thickness is less than 5 mm, the brake drum should be removed and wear assessed by the distance from the rivet to the surface of the lining.
Before removing the rear brake drums, you must disengage the parking brake.
If the brake drum cannot be removed from the pads due to a shoulder formed when the drum wears out, it is necessary to bring the pads together.
To bring the pads together, rotate the brake adjuster screw and turn the adjusting lever in the direction opposite to the stroke of the brake chamber rod when braking.
Clean the removed brake parts from dirt, remove rust and inspect the working surfaces. Brake drums must not have cracks or chips.
If deep scuffs, scratches or wear with a diameter of more than 0.5 mm are found on the brake drum, then such drums should be bored to one of the nearest repair sizes given in the table.
Table 1
Dimensions - Diameter of the outer surface of the pads - Diameter of the internal brake drum, mm:
- KAAZ nominal - 379.6 -0.60 mm - 380.5 +0.36 mm;
- RAA nominal - 420 -0.4 mm - 420 +0.38 mm
- KAAZ first repair - 380.6 -0.60 mm - 381.5 +0.36 mm;
- RAA first repair - 421 -0.4 mm - 421 +0.38 mm
- KAAZ second repair - 381.6 -0.60 mm - 382.5 +0.36 mm;
- RAA second repair - 422 -0.4 mm - 422 +0.38 mm
- KAAZ third repair - 382.6 -0.60 mm - 383.5 +0.36 mm;
- RAA third repair - 423 -0.4 mm - 423 +0.38 mm
- KAAZ fourth repair - 383.6 -0.60 mm - 383.5 +0.36 mm;
- RAA fourth repair - 424 -0.4 mm - 424 +0.38 mm
The brake drum must be bored together with the hub, centered on the outer rings of the bearings pressed into the hub.
The runout of the machined drum surface should not exceed 0.25 mm.
If, after machining the drum, its internal diameter exceeds 384.5 mm for KAAZ axles and 424 mm for RAA axles, then such a drum should be replaced.
The maximum diameter of the working surface of the brake drum, upon reaching which the operation of the bus is prohibited, is 386 mm for KAAZ axles, and 426 mm for RAA axles.
Brake pads must not have mechanical damage.
Chips and cracks passing through the holes for rivets or extending more than 15 mm are not allowed on the friction linings. If the surfaces of the linings become oily, the linings must be replaced.
The wear of the lining should be assessed by the distance from the rivet to the surface of the lining at the point of greatest wear.
If the lining is worn to a level of 0.5 mm above the rivet, the lining is rejected. This distance should be at least 2 mm for a serial block.
If you use linings made of other materials, you should be guided by the wear time of these linings in the current operating conditions of the bus, so that until the next maintenance-2 there is a guarantee that the linings will not wear down to the rivets.
It is not allowed to install pads with different lining materials on the brake mechanisms of the same axle.
New linings must not have distortions or other damage.
The size of the linings must be adjusted to the brake drum and ensure a gap between the drum and the lining of at least 0.9 mm.
Perform the fitting operation on a lathe using a special device.
Do not replace just one of the brake pads or linings on one side of the bus.
If it is necessary to replace one or both linings on one wheel, then it is better to make such a replacement on both sides of the bus axle to prevent it from pulling to the side when braking.
New linings must not have distortions or other damage.
The size of the linings must be adjusted to the brake drum and ensure a gap between the drum and the lining of at least 0.3 mm.
Perform the fitting operation on a lathe using a special device.
Do not replace just one of the brake pads or linings on one side of the bus.
If it is necessary to replace one or both linings on one wheel, then it is better to make such a replacement on both sides of the bus axle to prevent it from pulling to the side when braking.
Replacement of brake pads on a PAZ-32053-07 bus with KAAZ axles
- Place the bus on the inspection ditch. Loosen the wheel rim nuts.
Raise the wheel jack so that the tire does not touch the supporting surface.
Install wheel chocks and a strong, stable support under the bridge.
Turn off the parking brake (if the rear axle brake pads are being removed).
- Unscrew the wheel rim mounting nuts and remove the wheel.
- To facilitate the removal of the brake drum, inside of which a groove has formed due to the action of the brake lining, you should recess the brake adjuster clamp and turn it with a wrench to the left (counterclockwise) until the brake expansion knuckle returns to its original position, then loosen the nuts of the support pins 9 (Fig. 1) pads and turn the fingers with the marks inward.
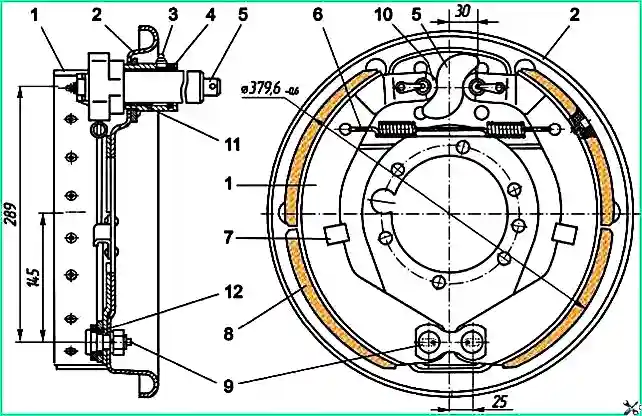
Brake mechanism of the PAZ-32053-07 bus (KAAZ): 1 - block; 2 - shield; 3 - expansion knuckle grease fitting; 4 - sealing ring; 5 - expansion fist; 6 - tension spring; 7 - guide bracket; 8 - overlay; 9 - pad support pin; 10 - roller; 11 - bushing of the fist support; 12 - pin bushing
After this, the gap between the brake lining and the drum will become maximum.
- Remove the drum, tension springs 6, unscrew the support pin nuts and remove the brake pads 1.
- Install the brake pads with new linings on the brake shield using support pins with bushings.
Pre-lubricate the surface of the 12th pin bushing with a thin layer of Litol-24 lubricant.
Remove excess lubricant. Grease should not come into contact with the surface of the brake linings. The marks on the heads of fingers 9 should be directed inward (Fig. 1).
- Center the shoes relative to the drum, turning the support pins to ensure that the shoes are in contact with the drum.
The gap between the brake lining and the drum should be (0.5-0.9) mm. The gap is checked with a feeler gauge through the windows in the brake shields.
When adjusting, the angle of rotation of the pad support pin should not exceed ±40° from the position with the marks inward.
- Tighten the support pin nuts.
- Rotate the brake adjuster lock to the right until it stops, that is, until the brake pads touch the drum.
Then turn the lock to the left by (120...180)°. In this case, a gap close to the required one will be established between the brake pads and the drum.
Then release the latch. If the latch remains recessed, turn it left and right within 30° until it returns to its original position under the action of the spring.
Replacement of brake pads on a PAZ-4234 bus with KAAZ axles
- Perform work 1-3 to replace the brake pads of the PAZ-32053-07 bus and remove the drum and spring.
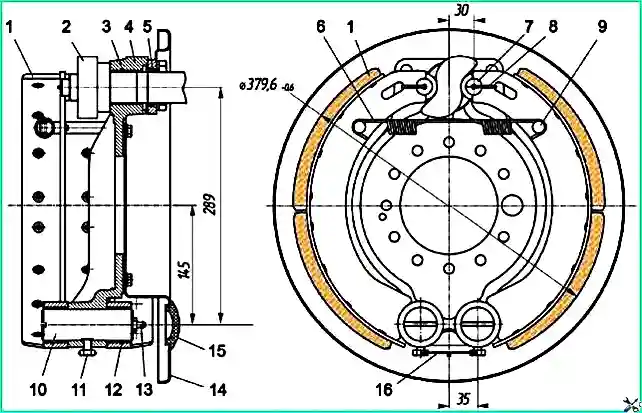
Brake mechanism of the PAZ-4234 (KAAZ) bus: 1 - block; 2 - expansion fist; 3 - bushing; 4 - brake caliper; 5 - sealing ring; 6 - tension spring; 7- pad roller; 8 - roller lock; 9 - spring axis; 10 - block axis; 11 - locking bolt; 12 - bushing; 13 - grease fitting; 14 - protective shield; 15 - plug; 16 - locking wire
- Remove the locking wire 16 (Fig. 2), unscrew the locking bolts 11 and knock out the axles 10 of the pads.
Before installation, the size of the linings must be adjusted to the brake drum and ensure a gap between the drum and the lining of at least 0.3 mm.
The adjustment can be done on a lathe using a fixture, the dimensions for which are shown in Fig. 2.
- Install the brake pads with fitted new linings onto the brake caliper using support axles 10 with bushings 12. Pre-lubricate the surface of the bushings with a thin layer of lubricant.
Remove excess lubricant.
Grease should not come into contact with the surface of the brake linings.
When installing the locking bolts 11, ensure that they fall into the flats of the axles 10. Secure the locking bolts with locking wire 16.
- Install the brake pad tension spring and brake drum, securing it to the hub with bolts. Before installing the drum on the hub, apply a thin layer of graphite grease to the hub seating surface.
After installing the pads, lubricate the brake pad axles through grease nipples 13 until fresh grease appears from the gaps.
To provide access to the oil nipples, you need to remove the plugs from the protective shields of the brake mechanisms or protective shields.
Grease should not come into contact with the working surfaces of the brake linings and drum.
If the brake pads were replaced by removing the wheel hub, then after installing the hub, you need to carefully extend the ABS wheel sensor until it comes into contact with the hub gear, and then turn the hub two or three turns to obtain the required clearance.
Replacement of brake pads of PAZ-32053-07 and PAZ-4234 buses with RAA axles
- Push in lock 2 (Fig. 3) of the brake adjuster and turn the key counterclockwise until the brake release knuckle returns to its original position.
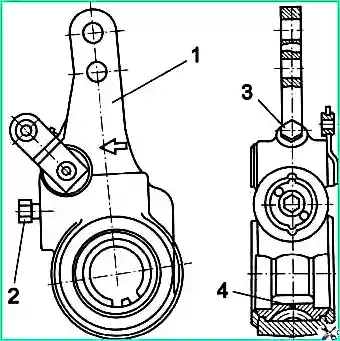
Brake regulator RT-40: 1 - regulator body; 2 – clamps; 3 - plug; 4 - hole for grease outlet
In this case, the gap between the brake lining and the drum will become maximum.
- Remove the hub together with the drum.
- Remove the tension springs and brake pads.
During assembly, lubricate the pad axles according to the “Lubrication Chart”.
- Remove the brake flaps to make adjustments easier.
- Loosen the nuts securing the eccentric axles (support pins) of the pads.
- Bring the eccentrics closer by turning the axes with the marks facing each other.
- Loosen the nuts and bolts securing the brackets (5-front, 6-rear) brake chambers.
- Loosen the expansion knuckle support bolts at the rear brake mechanisms.
- Apply compressed air to the brake chamber at a pressure of 0.1-0.15 MPa (1.0-1.5) kgf/cm 2, pressing the brake pedal when there is air in the system.
If there is no compressed air, remove the brake chamber rod pin and, pressing the adjustment lever in the direction of the brake chamber rod stroke when braking, press the pads to the brake drum.
- Center the pads relative to the drum, turning the eccentrics so as to ensure that the pads are in contact with the drum, which can be checked with a feeler gauge through the windows in the front brake flaps or with the rear brake flaps removed.
At a distance of (20-30) mm from the outer ends of the linings, a 0.1 mm thick probe should not pass along the entire width of the lining.
- Without stopping the supply of compressed air to the brake chamber, and in the absence of air, without releasing the adjustment lever and holding the axles of the pads from turning, securely tighten the axle nuts, bolts securing the brake chamber brackets and the expansion knuckle supports.
- Stop the compressed air supply or release the adjusting lever, attach the brake chamber rod to the lever and install the rear brake flaps.
Preliminary adjustment (installation) of the brake regulator is carried out to obtain the required strokes of the rods after replacing the pads:
- Release the energy accumulators.
- Install the regulator on the brake drive shaft and secure it to the shaft. The direction of action of the brake chamber force must coincide with the direction of the arrow marked on the regulator body.
- Push lock 2 (Fig. 3) inside the regulator until it stops, pressing its end with your finger.
Holding the lock in the recessed position, turn it to the right with a wrench until the holes in the regulator body and the brake chamber fork align.
- Connect the regulator body with the brake chamber fork and install the regulator drive rod.
- Rotate the lock to the right until it stops, i.e. until the brake pads touch the drum. Then turn the lock to the left by (120-180)°. In this case, a gap close to the required one will be established between the brake pads and the drum.
- Release the latch. If it remains recessed, turn it left or right within 30° until it returns to its original position under the action of the spring.
The stroke of the brake chamber rod is maintained automatically by the brake regulator.
If increased heating of the brake drums or low braking efficiency is detected, it is necessary to measure the stroke of the brake chamber rod when compressed air is supplied to it from the brake valve at an operating pressure of (0.7-0.8) MPa. The stroke of the brake chamber rod should be within (30-40) mm.
The difference between the strokes of the rods of the right and left chambers should not exceed 5 mm.
If the stroke of the rod does not correspond to the norm, then it is necessary to check the correct installation of the lever or find out the reason for the malfunction of the regulator and eliminate it.
The regulator has a non-separable design.
Maintenance of the brake regulator consists of adding ZhT-72 lubricant in an amount of (40-50) g every 60,000 km by pumping through the hole closed with plug 3 (Fig. 3).
Attention! The use of Litol-24 lubricant leads to malfunction of the regulator.
Attention! To prevent the brake pads of the rear wheels from freezing to the drums after a long stay during sudden temperature fluctuations, it is not recommended to leave the bus with parking brake without drying the brakes by smooth braking while driving.
Lubrication of the expansion cam shaft supports is carried out until fresh grease appears from the gaps between the shaft and the bracket.