Filtro de aceite centrífugo ZIL-5301
El diseño de un filtro de aceite centrífugo se muestra en la Fig. 1
No está permitido lavar las piezas de un filtro de aceite centrífugo fabricado en aleación de aluminio en un entorno agresivo
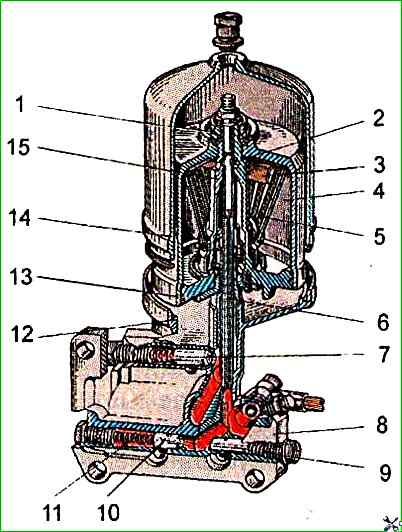
A la hora de montar la centrífuga se deben utilizar piezas que estén libres de contaminación.
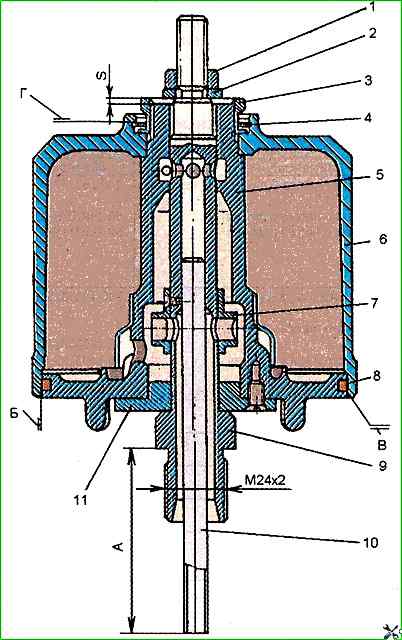
La falta de planitud de la superficie de contacto de la carcasa del filtro no debe exceder los 0,08 mm en toda su longitud.
En las superficies de los orificios de la carcasa del rotor 5 (Fig. 2) y la tapa 11, que se acoplan con los muñones del eje del rotor 9, no se permiten rastros de destrucción química.
No deben dañarse las roscas de la carcasa del rotor 5.
La superficie “G” de la ranura anular en la carcasa del rotor para el anillo de empuje 4 no debe dañarse.
La falta de planitud y falta de paralelismo de las superficies laterales del anillo de empuje no debe exceder los 0,1 mm.
En la superficie “5” de la carcasa del rotor, que se acopla con la carcasa del rotor 6, no se permiten muescas ni abolladuras.
No redondez y tolerancia del perfil de la sección longitudinal del orificio de la carcasa. rotor debajo del muñón superior del eje del rotor - 0,01 mm.
La carcasa del rotor debe estar estáticamente equilibrada.
Desequilibrio residual: no más de 150 g-mm.
La masa debe ajustarse perforando agujeros de 6 mm de diámetro en el extremo de la brida del rotor hasta una profundidad no superior a 2 mm.
La superficie cilíndrica de la copa, que se acopla con la superficie “B” del rotor, no debe tener curvas ni mellas. La falta de redondez de esta superficie es de 0,2 mm.
La superficie “B” del chaflán interior del extremo de la copa del rotor 6 no debe tener muescas con bordes afilados. Las mellas deben limpiarse.
La copa del rotor está equilibrada dinámicamente.
La masa debe ajustarse en dos planos: en el extremo superior y en el engrosamiento de la superficie inferior con una profundidad no mayor a 2 mm.
Desequilibrio residual no superior a 50 mm.
La no redondez y la tolerancia del perfil de la sección longitudinal del orificio de la tapa 11 de la carcasa del rotor para el muñón inferior es de 0,01 mm.
No se permiten grietas en la carcasa del filtro de aceite.
La profundidad del asiento de la válvula reductora de presión en la carcasa del filtro no debe exceder los 52 mm.
La profundidad del asiento de la válvula de drenaje y del asiento de la válvula del filtro centrífugo no debe exceder los 72 mm en la carcasa.
La curvatura de la generatriz del resorte de la válvula de drenaje y de la válvula del filtro centrífugo, que descansa libremente sobre la placa, no debe exceder 1 mm.
La curvatura de la generatriz del resorte de la válvula reductora de presión, que descansa libremente sobre la placa, no debe exceder 1 mm.
La tapa 11 de la carcasa del rotor, instalada en el eje del rotor, debe girar libremente con la mano.
Antes de instalar la tapa, se debe lubricar el muñón inferior del eje del rotor con aceite de motor.
No se permiten golpes, abolladuras, grietas ni deformaciones de la boquilla 7.
El tubo 10 debe tener un ajuste perfecto en el eje del rotor y sobresalir, proporcionando una dimensión “A” igual a 70±0,5 mm.
No se permite doblar el tubo 10.
El descentramiento de la superficie exterior del extremo del tubo prensado con respecto al diámetro medio de la rosca M24x2 del eje del rotor no debe exceder los 0,3 mm.
Antes de instalar la cubierta y la carcasa del rotor, los muñones del eje deben lubricarse con aceite de motor.
Primero se debe soplar el eje del rotor con aire comprimido.
Para la carcasa del rotor ensamblada, la tuerca especial 3 debe girar libremente con el esfuerzo de la mano.
Antes de instalar la copa del rotor 6 en el cuerpo del rotor, la junta tórica de goma debe lubricarse con grasa o aceite de motor M-10G2.
No está permitido cortar o rasgar el anillo.
Para un rotor ensamblado con un eje, el espacio entre el extremo de la carcasa del rotor 5 y la arandela de empuje 2 debe estar entre 8=0,3÷1,5 mm (ver Fig. 2).
El rotor debe girar sobre el eje libremente mediante el esfuerzo de la mano, sin sacudidas ni atascos.
La carcasa del filtro debe soplarse con aire comprimido antes del montaje.
Al instalar el conjunto del rotor con el eje en la carcasa del filtro, el eje del rotor debe apretarse a un par de 160÷200 Nm.
Las válvulas deben moverse en los asientos de la carcasa del filtro bajo la influencia de su propio peso , No se permiten válvulas colgantes.
Las pruebas de un filtro de aceite centrífugo en el stand KI-5278 deben realizarse con una mezcla de aceite de motor y combustible diesel con una viscosidad de 11,5 ÷ 16 mm 2/s (cSt) a la temperatura de prueba.
Se permite el uso de otros aceites minerales siempre que se mantenga la viscosidad especificada durante la prueba.
A una temperatura de prueba de 18÷22°C, se puede utilizar una mezcla compuesta por un 40% de aceite de motor M-10G o M-10V (en volumen) y un 60% de combustible diésel.
Después del ajuste, la apertura de la válvula centrífuga del filtro de aceite debe ocurrir a una presión de aceite de 0,7 ± 0,02 MPa.
La apertura de la válvula de drenaje debe ocurrir cuando la presión del fluido de trabajo sobre la válvula es de 0,25-0,35 MPa.
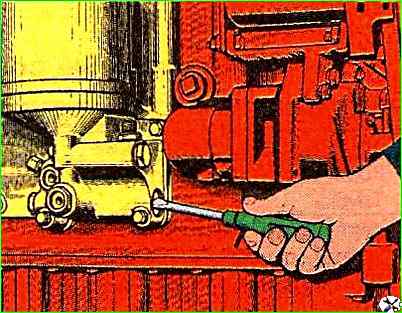
El ajuste final de la válvula (Fig. 3) debe realizarse con el motor diésel en marcha para establecer la presión del aceite en la línea dentro de 0,25÷0,35 MPa a una velocidad nominal del cigüeñal y una temperatura del aceite de 70÷80°C.
La válvula reductora de presión debe abrirse cuando la presión del aceite delante de ella sea de 0,05-006 MPa y con el bypass de aceite a la atmósfera.
El rotor bloqueado en el eje debe comprobarse para detectar fugas con una presión de aceite delante de él de al menos 0,8 MPa y una contrapresión en la salida del filtro de al menos 0,2 MPa.
En este caso, el flujo de fluido de trabajo a través de los cojinetes del rotor desde debajo de la tuerca del rotor (incluso a lo largo de la rosca) no debe fluir más de 0,067 dm 3/s; No se permiten fugas de aceite por debajo de la copa del rotor.
En el banco de pruebas KI-5278 con un caudal de aceite a través del rotor de 0,53 dm 3/s y una presión en la entrada al filtro de 0,7 ± 0,02 MPa, los parámetros deben ser los siguientes: presión detrás del filtro - al menos 0,25 MPa; flujo de aceite en la línea: al menos 0,53 3/s; velocidad del rotor no inferior a 5500 min -1.
El filtro ensamblado debe comprobarse para detectar fugas en 1 minuto a una presión en la entrada del filtro de 0,7÷0,8 MPa y una contrapresión en la salida de al menos 0,2 MPa.
En este caso no se permiten fugas o aparición de gotas de aceite en la superficie exterior del filtro y en las juntas.