Requisitos para la bomba de gasóleo D-245
No se permite el desmontaje de un par de engranajes de inyección, así como de la carcasa y tapa de la bomba de aceite
No debe haber grietas, daños o roscas rotas en el cuerpo de la bomba ni en la cubierta
La falta de planitud de la superficie “G” (Fig. 1) de la carcasa de la bomba no debe exceder los 0,03 mm en toda su longitud.
La cantidad de desgaste local en la superficie "B" de la carcasa de la bomba de aceite en los lugares que coinciden con los engranajes de inyección se permite hasta 0,03 mm.
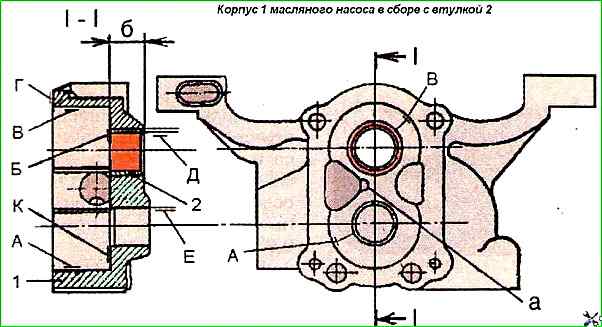
Si el desgaste es mayor se permite rechinar el cuerpo; en este caso, la rugosidad de la superficie tratada debe ser Ra≤1,25 micras.
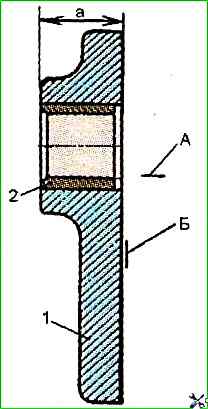
Se permite que el espesor de la cubierta (dimensión “a” en la Fig. 2) sea de al menos 16 mm.
La falta de planitud de la superficie “B” de la tapa de la bomba no debe exceder los 0,03 mm.
La no perpendicularidad de la superficie “B” a la superficie “A” no debe exceder los 0,03 mm en toda su longitud.
La altura de los engranajes de descarga debe ser la misma e igual a 28-0,040 mm; la diferencia de altura no está permitida más de 0,03 mm.
La profundidad de los casquillos de la carcasa de la bomba para los engranajes de descarga debe ser la misma con una desviación permitida de 0,06 mm.
Si la diferencia en las profundidades de los casquillos es superior a 0,06 mm o si hay rayones profundos y rebabas en las superficies de los extremos de los casquillos, se permite el procesamiento hasta que se eliminen los signos de desgaste.
El descentramiento de la superficie mecanizada “B” (ver Fig. 1) en relación con la superficie “D”, la superficie “K” en relación con la superficie “D”, la superficie “K”, en relación con la superficie “E” en un radio de 18 mm no debe exceder los 0, 05 mm.
Se permite profundizar los encajes en una cantidad en la que la dimensión "b" sea de al menos 15 mm.
Rugosidad de las superficies procesadas - Ra≤0,25 micras.
Control de escurrimiento según RTM 70.0001.234-83.
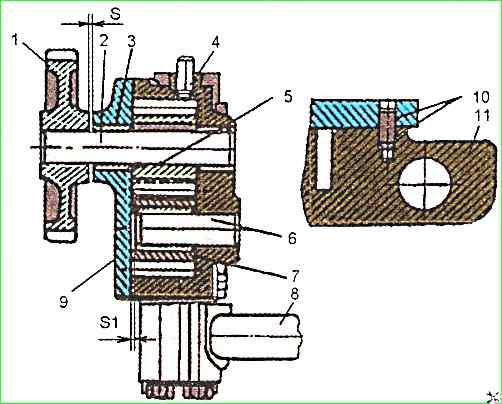
La profundidad de la ranura (dimensión “a”) en el cuerpo de la bomba debe ser de al menos 3 mm.
El hundimiento del extremo del pasador del engranaje impulsado en relación con el plano del conector de la carcasa de la bomba (S1) debe estar entre 0,7 y 1,3 mm (Fig. 3).
No se permite que el casquillo sobresalga por encima de los extremos de la rueda dentada impulsada de la bomba y las superficies de la tapa de la bomba.
La falta de redondez y la tolerancia del perfil de la sección longitudinal del orificio del casquillo del engranaje impulsado después del procesamiento no deben exceder los 0,025 mm.
El rebaje de los engranajes de presión de la bomba de aceite con respecto a la superficie (D) (ver Fig. 1) debe estar entre 0,04 y 0,13 mm.
Con un valor de hundimiento mayor, se permite la remoción de metal de la superficie “G”.
La desviación de la superficie mecanizada "P" con respecto a la superficie "D" en un radio de 29 mm no debe exceder los 0,07 mm.
La rugosidad de la superficie mecanizada debe ser Ra≤ 1,25 µm.
El diámetro de los orificios de los casquillos de la carcasa y de la tapa de la bomba, así como del casquillo del engranaje conducido, debe corresponder a 1 8 + 0,059 mm.
Si el diámetro es mayor, reemplace los casquillos por otros nuevos y luego mecanícelos hasta obtener el diámetro requerido.
El casquillo debe presionarse en la carcasa de la bomba de aceite al ras con la superficie "B".
El mecanizado de los orificios de los casquillos debe realizarse en el cuerpo de la bomba ensamblado con una tapa y una herramienta instalada.
Rugosidad de las superficies procesadas Ra≤ 2,25 µm.
La falta de redondez y la tolerancia del perfil de la sección longitudinal de los agujeros mecanizados es de 0,025 mm.
El diámetro de los casquillos de la carcasa de la bomba en los lugares de mayor desgaste debe ser de 42,25 mm.
Si las superficies “A” y “B” están desgastadas hasta un diámetro superior a 42,41 mm, se pueden restaurar con posterior taladrado hasta el diámetro de un cuerpo nuevo.
También se permite el taladrado excéntrico de casquillos para engranajes de tamaño nominal con desplazamiento de los ejes de los casquillos hacia el canal de aspiración de la bomba.
Se permite un desplazamiento de hasta 2,1 mm. La rugosidad de las superficies procesadas es Ra≤ 0,20 micras.
La holgura radial entre la carcasa de la bomba y la parte superior de los dientes de los engranajes de descarga debe estar en el rango de 0,125-0,245 mm.
Huecos entre los orificios del buje de la carcasa, las cubiertas de la bomba y el eje de la bomba, así como entre el orificio del buje y el eje el engranaje impulsado debe estar entre 0,032 y 0,07 mm.
La protuberancia de los pasadores cilíndricos 4 (ver Fig. 3) por encima del plano de acoplamiento debe ser de 7 ± 0,2 mm.
El espacio "S" entre el extremo del cubo del engranaje impulsor y la cubierta de la bomba ensamblada no debe ser superior a 0,2
Los pernos que sujetan la tapa de la bomba a la carcasa deben apretarse a un par de 18-25 Nm.
Los engranajes de la bomba ensamblada deben girar libremente con la mano, sin atascarse ni sacudidas.
El rodaje y la prueba de la bomba de aceite en el soporte Ki-5278 deben realizarse con una mezcla de aceite de motor y combustible diesel con una viscosidad de 11,5÷16 mm 2/s (cSt) a la temperatura de prueba.
Se permite el uso de otros aceites minerales siempre que se mantenga la viscosidad especificada durante la prueba.
A una temperatura de prueba de 18÷22° C, se puede utilizar una mezcla compuesta por un 40 % de aceite de motor M-10G y un 60 % de combustible diésel.
La bomba de aceite debe funcionar a una velocidad del rodillo de la bomba de 2320 ± 50 min -1 cada vez durante 2 minutos a una presión de salida de la bomba de 0,30 ± 02 MPa y una contrapresión de 0,7 ± 0,3 MPa.
Durante el proceso de rodaje, no se permiten el sobrecalentamiento de las piezas, ruidos extraños y fugas de aceite en las interfaces. Se permiten ligeras fugas de aceite a través de los espacios entre el eje de la bomba, los casquillos de la carcasa y la tapa de la bomba.
La bomba ensamblada debe probarse en un banco.
A una velocidad de rotación del rodillo de la bomba de 3170±25 min -1 y la contrapresión en la salida de la bomba es de 0,7÷0,75 MPa, el caudal volumétrico de la bomba reparada debe ser al menos 0,8 dm3/s y la potencia consumida por el variador no supera los 1,3 kW.
Al probar tuberías en busca de fugas con combustible diesel o aire bajo una presión de 0,1 ± 0,02 MPa, no se permiten fugas, gotas o fugas de aire.
La falta de planitud de los planos de contacto de las bridas de conexión del tubo de salida no debe exceder los 0,05 mm.
Al probar la estanqueidad del tubo de salida con agua a una presión de 1,0 MPa, no se permiten fugas ni la aparición de gotas de agua.