Requirements for the oil pump of the D-245 diesel engine
Disassembly of a pair of injection gears, as well as the housing and cover of the oil pump is not allowed
There should be no cracks, damage or stripped threads on the housing and cover of the pump
The non-flatness of the surface "G" (Fig. 1) of the pump housing should not exceed 0.03 mm along the entire length.
The amount of local wear of the surface "B" of the oil pump housing in places mating with the injection gears is allowed up to 0.03 mm.
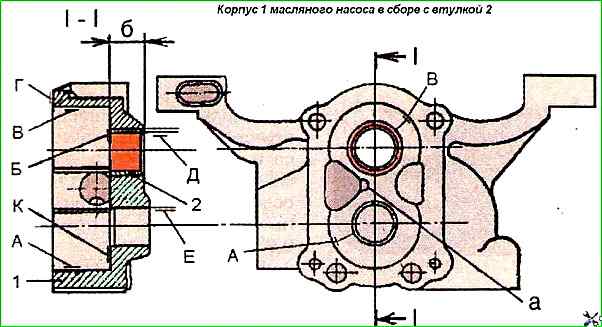
If the wear is greater, grinding of the housing is allowed; in this case, the roughness of the treated surface should be Ra≤1.25 μm.
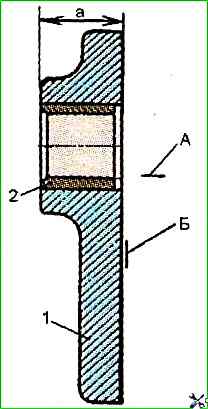
The thickness of the cover (dimension "a" in Fig. 2) is allowed to be not less than 16 mm.
The non-flatness of surface "B" of the pump cover should not exceed 0.03 mm.
The non-perpendicularity of surface "B" to surface "A" should not exceed 0.03 mm along the entire length.
The height of the pumping gears should be the same and equal to 28-0.040 mm; the difference in heights is allowed to be no more than 0.03 mm.
The depth of the pump housing seats for the delivery gears must be the same with an acceptable deviation of 0.06 mm.
If the difference in the depths of the seats is more than 0.06 mm or if there are deep scratches and burrs on the end surfaces of the seats, processing is allowed until traces of wear are removed.
The runout of the machined surface "B" (see Fig. 1) relative to surface "D", surface "K" relative to surface "D", surface "K", relative to surface "E" at a radius of 18 mm should not exceed 0.05 mm.
It is allowed to deepen the seats by an amount at which the size "b" will be at least 15 mm.
Roughness of the machined surfaces - Ra≤0.25 μm.
Runout control according to RTM 70.0001.234-83.
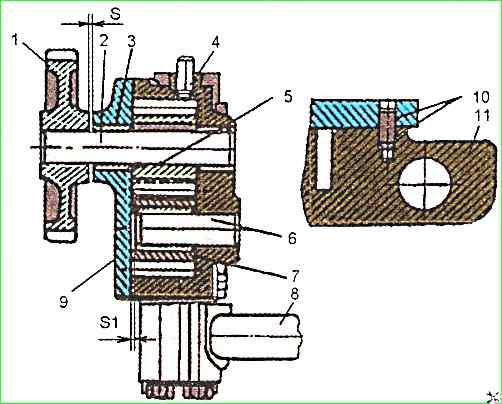
The groove depth (dimension "a") on the pump body must be at least 3 mm.
The recession of the end face of the driven gear pin relative to the plane of the pump body joint (S1) must be within 0.7-1.3 mm (Fig. 3).
The protrusion of the bushing above the ends of the driven gear of the pump and the surfaces of the pump cover is not allowed.
The non-roundness and tolerance of the longitudinal section profile of the driven gear bushing hole after processing must not exceed 0.025 mm.
The recession of the pressure gears of the oil pump relative to the surface (G) (see Fig. 1) must be within 0.04-0.13 mm.
With a greater recession value, metal removal from the surface is allowed «Г».
The runout of the machined surface «П» relative to the surface «Д» at a radius of 29 mm should not exceed 0.07 mm.
The roughness of the machined surface should be Ra≤ 1.25 μm.
The diameter of the holes of the bushings of the housing and cover of the pump, as well as the bushing of the driven gear should correspond to 1 8+0.059 mm.
If the diameter of the bushing is larger, replace it with new ones with subsequent processing to the required diameter.
The bushing should be pressed into the housing of the oil pump flush with the surface «В».
Machining of the holes of the bushings should be carried out on the assembled pump housing with the cover with one installation of the tool.
Roughness of the machined surfaces Ra≤ 2.25 μm.
Non-roundness and tolerance of the profile of the longitudinal cross-section of machined holes — 0.025 mm.
The diameter of the pump housing seats in places of greatest wear should be 42.25 mm.
If surfaces “A” and “B” wear to a diameter greater than 42.41 mm, they can be restored with subsequent boring to the diameter of the new housing.
Eccentric boring of seats for gears of nominal size with an offset of the seat axes towards the suction channel of the pump is also allowed.
Offset is allowed up to 2.1 mm. Roughness of machined surfaces — Ra≤ 0.20 µm.
The radial clearance between the pump body and the tops of the teeth of the pump gears should be within 0.125-0.245 mm.
The clearances between the holes of the body bushings, the pump covers and the pump shaft, as well as between the hole of the bushing and the axis driven gear should be within 0.032-0.07 mm.
The protrusion of the cylindrical pins 4 (see Fig. 3) above the mating plane should be 7±0.2 mm.
The gap "S" between the end of the drive gear hub and the cover on the assembled pump should be no more than 0.2
The bolts securing the pump cover to the housing should be tightened to a torque of 18-25 Nm.
The gears of the assembled pump should rotate freely by hand, without jamming or jerking.
Running-in and testing of the oil pump on the KI-5278 stand should be carried out on a mixture of motor oil and diesel fuel with a viscosity of 11.5÷16 mm2/s (cSt) at the test temperature.
It is allowed to use other mineral oils, provided that the specified viscosity is maintained during the test.
At a test temperature of 18÷22° C, a mixture of 40% M-10G motor oil and 60% diesel fuel can be used.
The oil pump must be run in at a pump shaft speed of 2320±50 min -1 each time for 2 minutes at a pump outlet pressure of 0.30±02 MPa and a back pressure of 0.7±0.3 MPa.
During the run in process, overheating of parts, extraneous noise, and oil leaks at mating points are not allowed. Minor oil leakage through gaps between the pump shaft, housing bushings and pump cover is allowed.
The assembled pump must be tested on a bench.
At a pump shaft speed of 3170±25 min -1 and a backpressure at the pump outlet of 0.7÷0.75 MPa, the volumetric flow of the repaired pump must be at least 0.8 dm3/s, and the power spent on the drive must not exceed 1.3 kW.
When testing the pipes for leaks with diesel fuel or air under a pressure of 0.1±0.02 MPa, leaks, drops or air seepage are not allowed.
The non-flatness of the mating surfaces of the connecting flanges of the outlet pipe must not exceed 0.05 mm.
When testing the outlet pipe for tightness with water under pressure of 1.0 MPa, no leaks or water droplets are allowed.