El desmontaje del cilindro de freno principal del vehículo GAZ-53A debe realizarse en la siguiente secuencia
Detenga el motor y libere el vacío del servomotor presionando el pedal del freno varias veces.
Desconecte la tubería del acoplamiento del cilindro maestro.
Desplace el líquido de frenos desde el cilindro maestro al recipiente presionando el pedal varias veces.
Retire la tapa de goma con el anillo de sujeción del extremo del cilindro maestro.
Retire el resorte de retorno del pedal del freno. Retire el pasador, la varilla de empuje con la varilla y retire la tapa protectora con el anillo tensor.
Retire el cilindro maestro del soporte del pedal. Para desatornillar los tornillos se recomienda utilizar la llave que se muestra en la Fig. 1.
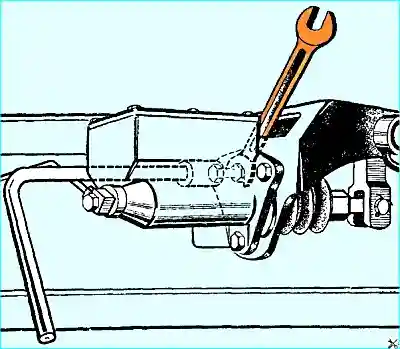
El desmontaje del cilindro maestro de freno y embrague del vehículo GAZ-66 debe realizarse en la siguiente secuencia.
Libera el amplificador del vacío.
Desconecte las tuberías de los acoplamientos del cilindro maestro.
Desplazar el líquido desde el cilindro principal hacia el recipiente.
Retire el soporte del cilindro maestro con el conjunto de pedales.
Retire las tapas de goma con los anillos de sujeción de la tapa de empuje del pistón.
Desenrosque las tuercas de los ejes excéntricos, retire los ejes excéntricos, retire los empujadores de pistón con casquillos (debajo de los ejes excéntricos) y las tapas protectoras de goma de los cilindros.
Retire el cilindro del soporte del pedal.
El desmontaje del cilindro maestro del freno debe realizarse en la siguiente secuencia.
Limpie la superficie exterior del cilindro. Desenrosque el tapón de llenado con la junta. Vierta el líquido de frenos restante del cilindro y del depósito.
Retire los acoplamientos con juntas de cobre.
Retire el anillo de retención, la arandela de empuje (o retire la tapa de empuje con junta para GAZ-66), el pistón, el manguito, el resorte con soporte y la válvula del cilindro.
Para retirar piezas, se puede pasar aire comprimido al cilindro a través de la salida ubicada en el extremo del mismo.
Retire la tapa del cilindro maestro con la junta.
Reparación de piezas del cilindro maestro
Lave todas las piezas del cilindro maestro con alcohol puro y límpielas con un paño limpio.
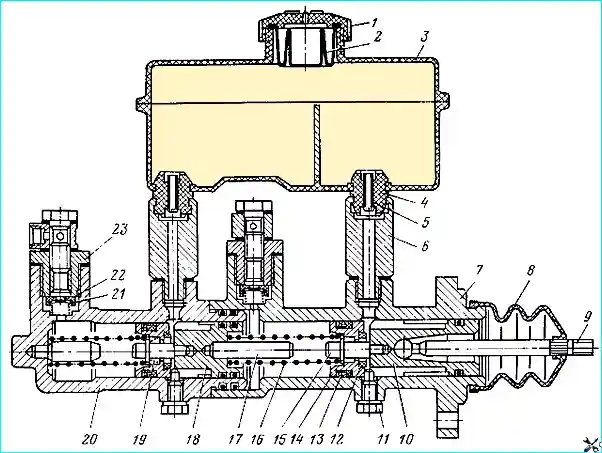
Cilindro maestro de freno: 1 - tapa del depósito; 2 – cubierta de goma; 3 – tanque; 4 – casquillo de goma; 5 – tubo; 6 – pezón; 7 – carcasa del cilindro primario; 8 – cubierta; 9 – empujador; 10, 18 – pistones; 11 – limitador de carrera; 12 – sello; 15 – varilla de empuje; 16, 19 – manantiales; 20 – cárter del cilindro secundario; 21 – placa de válvulas; 22 - válvula
Verifique el desgaste de las piezas y su estado.
Las dimensiones máximas permitidas de las piezas del cilindro principal se indican en la tabla. 1.
Tabla 1
Dimensiones nominales y de reparación de las piezas del cilindro principal, mm:
Tamaño nominal:
- - diámetro del cilindro 32,00+0,027 (32,08);
- - diámetro del pistón 32,00-0,025 (31,85);
- - diámetro de los bordes de los puños de trabajo 33 ± 0,2 (32,75)
Primera reparación:
- - diámetro del cilindro 32,25+0,027 ;
- - diámetro del pistón 32,25-0,025 ;
- - diámetro de los bordes de los puños de trabajo 33,50 ± 0,2
Segunda reparación:
- - diámetro del cilindro 32,50+0,027 ;
- - diámetro del pistón 32,50—0,025 ;
- - diámetro de los bordes de los puños de trabajo
Tercera reparación:
- - diámetro del cilindro 32,75+0,027 ;
- - diámetro del pistón 32,75-0,025 ;
- - diámetro de los bordes de los puños de trabajo 34,00 ± 0,2
Cuarta reparación:
- - diámetro del cilindro 33,00+0,027 ;
- - diámetro del pistón 33,00-0,025 ;
- - diámetro de los bordes de los puños de trabajo -
Las dimensiones entre paréntesis son las que son aceptables sin reparación
Carcasa del cilindro maestro. Compruebe si hay rayas o corrosión en la superficie de trabajo del cilindro. Claro
Los orificios de derivación y salida del cárter con un palo de madera, y el orificio de compensación con un alambre blando y romo de Ø 0,6 mm.
Si la superficie del cilindro presenta signos de rayaduras, corrosión y desgaste, se afila hasta un diámetro no superior a 32,152 mm. En este caso se instalan puños nuevos.
Si después de la reparación aparece una fuga, se debe perforar el cilindro y luego afilarlo según uno de los tamaños de reparación. En este caso se establecen los tamaños correspondientes de pistones y puños.
Pistón del cilindro maestro. Compruebe si hay rayaduras, corrosión, desgaste y obstrucciones en los cojinetes agujeros de retorno.
Si la válvula de resorte remachada al extremo delantero del pistón no está asentada de forma segura o se ha desplazado de modo que los orificios del pistón quedan expuestos, vuelva a instalar la válvula y utilice un punzón adicional para asegurarla.
Válvula. Limpie la válvula antes de lavarla con una herramienta contundente y sumérjala en alcohol para enjuagarla. Cualquier daño o hinchazón requiere reemplazo.
Limpie cuidadosamente la suciedad del tapón de llenado del cilindro y limpie el orificio de ventilación.
Los puños del pistón del cilindro maestro deben ser elásticos y los bordes de trabajo deben estar afilados y sin defectos.
Montaje, instalación en el vehículo y prueba del cilindro maestro
Antes del montaje, lave todas las piezas del cilindro maestro con alcohol puro y sóplelas con aire comprimido. Lubrique los puños y el espejo del cilindro con líquido de frenos.
Monte el cilindro maestro en el orden inverso al de desmontaje.
Después de instalar el resorte con el conjunto de válvula y soporte, el manguito interior y el pistón en el cilindro, verifique si el pistón retorna bien bajo la acción del resorte.
Después de instalar la arandela y el anillo de retención en el cilindro, verifique con un alambre blando de Ø 0,6 mm con un extremo romo para ver si el orificio de compensación del manguito está bloqueado.
Después de montar el cilindro maestro del freno, el orificio “A” con un diámetro de 0,7 mm no debe estar cubierto por un manguito de goma (Fig. 3). Esto se comprueba con un alambre de 0,6 mm de diámetro.
La distancia desde la brida de montaje del cárter hasta el extremo del empujador debe ser de 92,5 mm. La carrera del pistón no debe ser superior a 37 mm (ver Fig. 3).
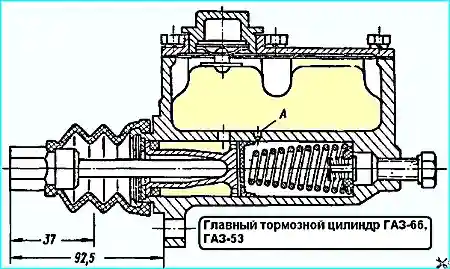
Después de instalar el cilindro en el soporte del pedal, instale el empujador con el conjunto de tapa en el pistón del cilindro sin colocar la tapa en el cuerpo.
Pruebe el cilindro maestro, para ello es necesario:
- - instalar un manómetro hidráulico en la salida; - Llene el depósito del cilindro con líquido de frenos hasta el nivel normal. Durante y después de la prueba, agregue líquido si es necesario;
- - enroscar el tapón de llenado con la junta;
- - purgar el cilindro presionando el pedal del freno 2-3 veces, limpiar el cilindro; - Compruebe que el cilindro no presente fugas bajo una presión de aproximadamente 90 kg/cm². Crea presión presionando el pedal con fuerza constante.
No debe haber fugas de líquido, caída de presión ni movimiento del pedal en 1,5 minutos;
- - Verifique que la válvula del cilindro no tenga fugas, para ello presione el pedal y bájelo.
Tenga en cuenta las lecturas del manómetro; La válvula debe mantener una sobrepresión de 0,8 kg/cm² en el sistema durante una hora;
- - desconectar el manómetro del cilindro y fijar en su lugar el acoplamiento con dos juntas de cobre nuevas mediante un perno;
- - conectar la tubería al acoplamiento;
- - desenrosque el tapón de llenado y llene el líquido de frenos hasta el nivel normal;
- - enroscar el tapón con la junta;
- - coloque la tapa de goma en la carcasa del cilindro y fíjela con un anillo de sujeción;
- - purgar el sistema de frenos.
Al montar el cilindro maestro GAZ-66, tenga en cuenta que la válvula de sobrepresión no esté instalada en la cavidad del cilindro maestro de accionamiento del embrague, y que los pistones descansen contra la tapa.
Sustitución de piezas de accionamiento hidráulico
Limpie y enjuague antes de reemplazar la pieza.
Al reemplazar mangueras o conexiones en T, ajuste bien sus conexiones.
El tubo de freno se sustituye en caso de daños, abolladuras o estrechamiento de la sección transversal.
Al doblar la tubería para adaptarla a su ubicación de instalación, tenga cuidado de no provocar grietas.
Para ello, coloque una carcasa de resorte del diámetro adecuado en la tubería o doble la tubería utilizando un rodillo.
Los extremos de las tuberías deben tener doble abocardado para garantizar conexiones herméticas.
Al hacer tuberías nuevas, corte sus extremos estrictamente perpendicularmente, preferiblemente con un cortatubos, para no aplastarlos. Limpie cuidadosamente las rebabas en los extremos a lo largo de los diámetros exterior e interior.
Lave las paredes internas de las líneas de freno nuevas con alcohol puro.
La manguera flexible del freno se reemplaza si se encuentran rayones u otros daños.
Al reemplazar la manguera del freno, desenrosque la tuerca de conexión de la tubería que va a ella, luego desenrosque la tuerca que fija la manguera al marco y luego desenrosquela del cilindro de la rueda o la T en el eje trasero.
Instale la manguera en orden inverso.
Al apretar la tuerca de fijación de la manguera o la tuerca de conexión de la tubería, sujete la manguera con una llave para evitar que gire.
La manguera no debe tocar las piezas chasis.