El embrague del coche es seco, monodisco, con dispositivo amortiguador, instalado en una carcasa de fundición de aluminio (Fig. 1)
El embrague del automóvil GAZ-66 se diferencia del embrague del automóvil GAZ-53A solo en los diferentes pasadores de empuje de las horquillas de desembrague (lo cual se debe a diferentes accionamientos de desembrague), las tapas de las escotillas de instalación de encendido y el presencia de un pasador de instalación de encendido presionado en la carcasa del embrague del automóvil GA3-66 (no hay pasador en la carcasa del embrague GAZ-53A).
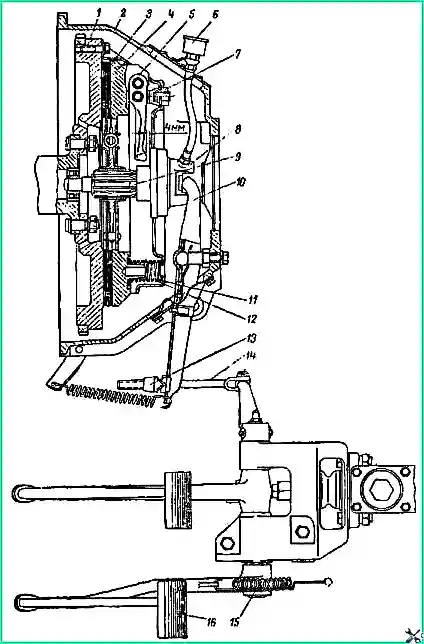
Los discos de presión y de accionamiento, así como los embragues de desembrague de los vehículos GAZ-53A y GAZ-66, no son diferentes.
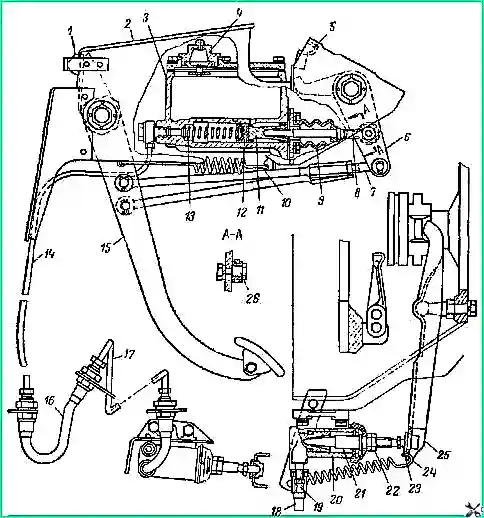
Accionamiento de desembrague del automóvil GAZ-66: 1 - tope de goma; 2 - soporte delantero; 3 - cilindro principal; 4 Conector; 5 - soporte trasero; 6 - palanca intermedia; 7 - tracción; 8 - empujador; 9 - funda protectora; 10 en 24 - resortes tensores; 11 - pistón del cilindro principal; 12- puño; 13 - resorte de retorno; 14 y 17 - tuberías; 15 - pedales; 16 y 18 - mangueras flexibles; 19 - válvula de derivación; 20 - cilindro de trabajo; 21 - empujador; 22 - contratuerca; 23 - punta del empujador; 25 - horquilla de desembrague; 26 - perno excéntrico
El accionamiento de desembrague del automóvil GAZ-53A es mecánico (ver Fig. 1), el accionamiento de desembrague del automóvil GAZ-66 (desconexión 2) es hidráulico.
Mantenimiento del embrague
Al lubricar el cojinete de empuje del embrague de desembrague, es necesario exprimir el lubricante en la cantidad de un llenado completo de la tapa de grasa.
Una lubricación más frecuente y generosa puede hacer que el exceso de lubricante llegue a los discos del embrague, lo que puede provocar fallas.
Una lubricación más infrecuente del rodamiento provoca un espesamiento del lubricante en los orificios que lo suministran desde la cavidad anular del acoplamiento al rodamiento, y el posterior fallo del rodamiento debido al cese del suministro de lubricante.
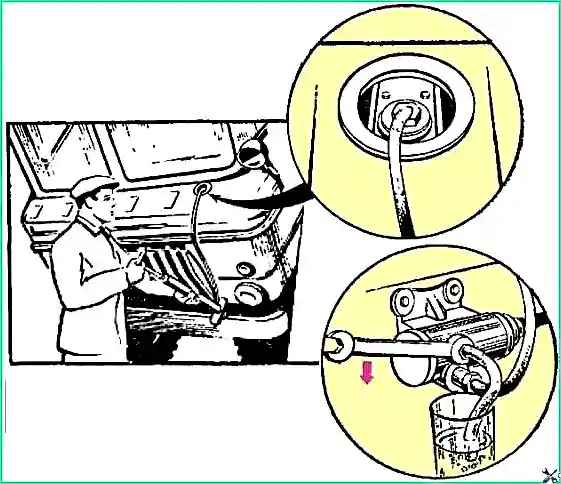
Se debe prestar especial atención al cuidado del mecanismo de desembrague del automóvil GAZ-66 en relación con el uso del líquido GTZh-22 como fluido de trabajo, ya que tiene fuertes propiedades oxidantes.
Para el funcionamiento normal del embrague de un vehículo GAZ-53A, es necesario garantizar un espacio de 4 mm entre las cabezas de las palancas de desembrague y el cojinete de empuje.
Para obtener esta holgura es necesario comprobar y ajustar periódicamente el juego libre del pedal del embrague, que debe ser de 35-45 mm.
El juego libre del pedal del embrague se ajusta cambiando la longitud de la varilla que conecta la horquilla de desembrague a la palanca en el eje del pedal.
Se consigue un aumento del juego libre desenroscando la tuerca de la varilla y una disminución apretándola.
Para el funcionamiento normal del embrague de un automóvil GAZ-66, es necesario asegurar un espacio entre las cabezas de las palancas de desembrague y el cojinete de empuje de 2 mm y un espacio entre el empujador y el pistón del cilindro maestro. de 0,5-1,5 mm.
Al ajustar la transmisión de liberación del embrague, primero ajuste el espacio entre el empujador y el pistón del cilindro maestro usando el perno excéntrico 26 (ver Fig. 2).
La holgura normal corresponde a un juego libre del pedal de 3,5 - 10 mm.
Después del ajuste, se aprieta la tuerca del perno 26.
Si no es posible garantizar el juego libre requerido del pedal utilizando un perno excéntrico, primero se debe ajustar cambiando la longitud de la varilla 7.
El espacio entre el cojinete de empuje de desembrague y las cabezas de palanca se ajusta cambiando la longitud del empujador del cilindro de trabajo, en este caso es necesario obtener un juego libre del extremo de la horquilla de desembrague de 3,5 mm.
Después del ajuste, el recorrido total del pedal debe ser de 30-37 mm.
Para el funcionamiento normal del embrague, también es necesario asegurarse de que la carrera del pistón del cilindro de trabajo sea de al menos 23 mm.
Con una carrera más pequeña, es posible que el embrague no se desacople por completo. La carrera del pistón del cilindro de trabajo no está regulada.
Un trazo reducido indica una Fugas de aire en el sistema de accionamiento hidráulico. En este caso, es necesario bombear el fluido al accionamiento hidráulico.
Para ello, retire la tapa protectora de goma de la cabeza de la válvula de derivación del cilindro de trabajo y coloque una manguera de purga en la cabeza.
Coloca el extremo de la manguera en un recipiente de vidrio en el que se vierte un poco de líquido y desenrosca las válvulas ¾ de vuelta.
Atornille la manguera de la bomba de neumáticos al extremo roscado del tapón del cilindro maestro y use la bomba para crear una ligera presión en el sistema (Fig. 3).
Al mismo tiempo, bajo la influencia de la presión, el líquido del depósito del cilindro maestro llena el sistema de accionamiento hidráulico, desplazando el aire a través de la válvula de derivación del cilindro de trabajo.
El aire de la manguera atravesará el líquido del recipiente de cristal en forma de burbujas.
Después de que se detenga la salida de aire del sistema de accionamiento hidráulico (las burbujas dejan de salir de la manguera de purga), cierre la válvula y retire la manguera de purga.
Coloque una tapa protectora en la cabeza de la válvula de derivación y, desenroscando el tapón del cilindro maestro, agregue líquido hasta un nivel de 15-20 mm por debajo del borde superior del orificio de llenado; atornille el enchufe.
Al bombear, no permita que la parte inferior del cilindro maestro quede expuesta.
Por lo tanto, si se ha fugado aproximadamente un vaso de líquido del sistema, deje de bombear y continúe solo después de agregar líquido al cilindro principal.
Fallos en el embrague y formas de solucionarlos
- Causas del mal funcionamiento
Remedio
El embrague no es fluido:
- Lubricación de los forros de fricción del disco conducido
Reemplace el disco impulsado o instale nuevos forros de fricción.
Si la lubricación es leve, se pueden lijar los revestimientos con papel de lija fino, después de lavarlos con gasolina
- Presión no simultánea del cojinete de empuje en las cabezas de las palancas de desembrague
Ajustar la posición relativa de los cabezales de las palancas mediante las tuercas 7 (ver Fig. 1) de las horquillas de soporte
- Desgaste excesivo de los forros de fricción (hasta los remaches)
Reemplazar el disco o cambiar los forros
Desacoplamiento incompleto del embrague - “el embrague se cerrará” (dificultad para cambiar de marcha y ruido de marcha en la caja de cambios al cambiar):
- Disponibilidad de aire en el sistema de accionamiento hidráulico
Purga de líquido en el sistema
- Gran juego libre del pedal del embrague
Ajustar el juego libre del pedal del embrague
- deformación del disco impulsado
Reemplace el disco o edítelo
- Presión no simultánea del rodamiento en las cabezas de las palancas de desembrague
Ajustar la posición relativa de las palancas
- Desgaste del manguito interior del cilindro maestro
Reemplace el brazalete
Enganche incompleto - “deslizamiento del embrague”:
- No hay espacio entre las cabezas de las palancas de desembrague y el extremo del cojinete de empuje
Ajustar el juego libre del pedal del embrague
- Aflojamiento de los muelles de presión del embrague
Reemplazar resortes
- Lubricación de discos
Reemplazar discos o forros de fricción
- Desgaste excesivo de los forros de fricción, superficie de fricción del volante o plato de presión
Reemplace los discos impulsados o los revestimientos de los discos y repare el volante y el plato de presión rectificando las superficies de fricción
Ruido, chirridos al pisar el pedal del embrague:
- Falta de lubricación en el cojinete de desembrague
Lubricar el rodamiento
- Desgaste del rodamiento del embrague
Reemplazar el rodamiento
Reparación del embrague
Las principales piezas del embrague que requieren reemplazo o reparación durante el funcionamiento son las placas impulsadas y de presión, así como el cojinete de desembrague.
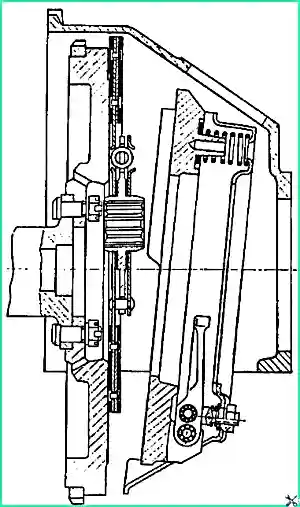
Sustitución del cojinete de desembrague
Para quitar el cojinete de desembrague, retire la caja de cambios junto con el embrague, desconecte el resorte de desembrague, retire el embrague y presione el cojinete para quitarlo.
Antes de presionar un nuevo rodamiento en el acoplamiento, compruebe que esté lleno de lubricante.
Al instalar una caja de cambios con embrague en un automóvil, es necesario asegurarse de que la manguera de suministro de lubricante al rodamiento no esté dañada; para ello, enrósquela dentro de la carcasa del embrague antes de instalar finalmente la caja de cambios en la carcasa del embrague. montantes.
Si por algún motivo se quitó o reemplazó la manguera de suministro de grasa al rodamiento, llénela con grasa durante la instalación.
Para hacer esto, exprima dos veces el contenido de una lata de aceite completamente llena; Eso Sólo la tercera vez el engrasador suministrará lubricante al cojinete de desembrague.
Extracción de los discos de embrague
Para quitar los discos de embrague del vehículo, retire la caja de cambios.
Habiendo retirado la parte inferior de la carcasa del embrague, desatornille los pernos que sujetan la carcasa del embrague al volante a través de la trampilla de la carcasa inferior.
En este caso, se deben desatornillar todos los tornillos gradualmente para no doblar las patas de soporte de la carcasa ni arrancar los tornillos que se desatornillan en último lugar.
Los discos de embrague separados del volante se retiran del cárter en una posición determinada.
Primero retire el disco de presión girándolo hacia abajo con una de las patas de la carcasa y levantando el disco conducido (Fig. 4), luego el conducido.
Desmontaje y montaje del plato de presión del embrague
La placa de presión se desmonta en el siguiente orden:
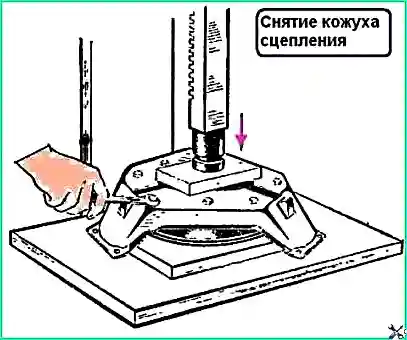
- - realizar marcas en la carcasa y en la placa de presión para mantener la posición original de estas piezas durante el montaje y, por tanto, mantener el equilibrio;
- - colocar el disco sobre la mesa de la prensa, colocando un soporte de madera debajo del disco para que las patas de la carcasa puedan bajar;
- - se coloca un taco de madera encima de la carcasa de manera que no cubra ninguna de las tuercas de ajuste de las horquillas de soporte de la palanca de desembrague (Fig. 5);
- - presionando el bloque con una prensa, comprimir los resortes del embrague para aliviar el esfuerzo de las palancas de desembrague, desenroscar las tuercas de las horquillas de soporte de la palanca, soltar lentamente la prensa, quitar la tapa del embrague, los resortes de la horquilla de soporte y los resortes de presión. ;
- - retirar con cuidado los dedos situados en los salientes de la placa de presión, separar las palancas con horquillas de apoyo de la placa de presión y montar los rodillos con cojinetes de agujas;
- - retirar con cuidado los dedos de las horquillas de soporte de la palanca, separar las horquillas de soporte y montar los rodillos con cojinetes de agujas.
Si se encuentran deformaciones, rayaduras, ranuras anulares o grietas causadas por el sobrecalentamiento en la superficie de fricción del disco de presión, el disco se reemplaza o repara mediante ranurado y rectificado; el espesor del disco reparado no debe ser más de 1,5 mm menor que el espesor del disco nuevo.
La diferencia de tamaño entre cada uno de los ejes de los tres orificios debajo de los ejes de las palancas de desembrague y la superficie mecanizada no debe ser superior a 0,15 mm, y la superficie en sí debe ser plana (al comprobar en una placa, la sonda de 0,05 mm no debe pasar).
Los resortes rotos o perdidos de presión deben ser reemplazados (es recomendable reemplazar todos los resortes).
La fuerza del resorte de presión debe ser de 62,5 a 68 kg cuando se comprime desde una longitud libre de 61 mm a una longitud de 40 mm.
También es necesario reemplazar los resortes de las horquillas de soporte de las palancas de desembrague que han perdido su elasticidad, ya que de lo contrario, a altas velocidades del motor, las cabezas de las palancas de desembrague pueden retroceder, lo que provocará un funcionamiento continuo del el cojinete de empuje y su desgaste prematuro.
Al comprimir el resorte de la horquilla de soporte desde una longitud libre de 12,5 mm hasta una longitud de 9,5 mm, la fuerza del resorte debe ser de 14 ± 1,5 kg.
La placa de presión con carcasa y palancas se montan en el siguiente orden:
- - montar las palancas de desembrague con las horquillas de soporte; Para hacer esto, se colocan bolas de goma con un diámetro de 8,5 mm en los orificios correspondientes de las palancas, después de lo cual los espacios entre las bolas y las paredes de los orificios se rellenan con rodillos de rodamientos de agujas (cada rodamiento debe tener 19 rodillos). . Se necesitan bolas de goma para garantizar que los rodillos no se deshagan durante el montaje.
- - Después de instalar los rodillos, se introducen una o dos gotas de aceite utilizado para lubricar la caja de cambios en los orificios de las palancas;
- - inserte las palancas de liberación del embrague con los rodillos en las ranuras de las horquillas de soporte, luego inserte con cuidado los dedos y sujételos. Una vez montadas, las bolas de goma se empujan hacia afuera con los dedos;
- - el plato de presión con las palancas de desembrague se monta del mismo modo;
- - utilizando, como durante el desmontaje, una prensa, un revestimiento de madera y un bloque, monte un disco de presión con carcasa, resortes y arandelas termoaislantes. En este caso, las marcas realizadas durante el desmontaje en el disco y la carcasa quedan alineadas.
Al montar una carcasa con un disco reparado, debajo de los resortes de presión se colocan arandelas metálicas, además de las arandelas termoaislantes, para compensar la reducción del espesor del disco y así mantener la fuerza de los resortes de presión. (en lugar de colocar arandelas debajo de los resortes, puede hacer una ranura anular para el volante debajo de las patas del disco de presión, la profundidad de la ranura debe ser igual a la cantidad en la que se redujo el grosor de la placa de presión después de la reparación) .
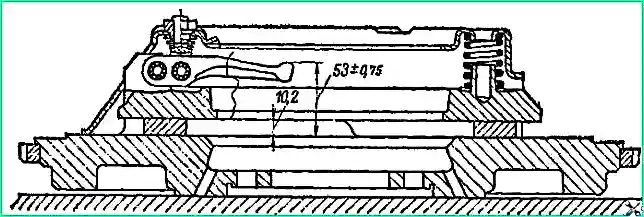
Después del montaje, ajuste la posición de los cabezales de la palanca de liberación del embrague.
Si no hay ningún dispositivo, esta operación se puede realizar mediante volante libre.
Para ello, se coloca el plato de presión ensamblado con la carcasa sobre la superficie de fricción del volante.
Entre la placa de presión y el volante, coloque arandelas de 10,2 mm de espesor en tres lugares y apriete los tornillos que sujetan la carcasa al volante.
Usando las tuercas de ajuste de las palancas extraíbles, asegúrese de que el tamaño desde la superficie del volante hasta los extremos de las palancas sea de 53 ± 0,75 mm (Fig. 6), y que la desviación de los extremos de las palancas desde un plano no es más de 0,3 mm;
- después de esto se desenroscan las tuercas de ajuste. En lugar de arandelas, puede utilizar un disco impulsado nuevo al realizar ajustes.
Reparación de disco accionado por embrague
Si hay un desgaste importante (casi hasta los remaches) o daños en los forros de fricción del disco impulsado, se reemplazan los forros.
Ambas pastillas deben sustituirse al mismo tiempo, ya que la diferencia de espesor de las pastillas alterará el funcionamiento normal del embrague.
Para quitar los revestimientos desgastados o dañados, debes perforar y sacar con cuidado los remaches que sujetan los revestimientos a las ballestas y al disco con un punzón.
Remachar forros nuevos de manera que la profundidad de los remaches sea de al menos 1,5 mm.
El descentramiento de un disco con revestimientos nuevos no debe ser superior a 0,7 mm cuando se mide en un radio de 125 mm desde el centro del disco.
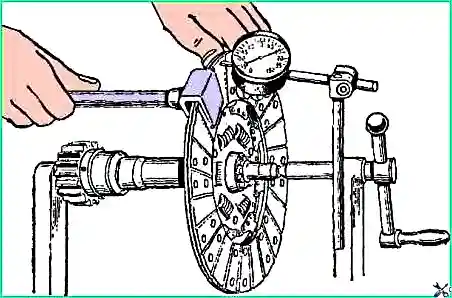
Si el descentramiento del disco es mayor que el valor permitido, cuando se desacopla el embrague se “impulsará” (desacoplamiento incompleto del embrague).
Si es necesario, el disco impulsado se ajusta utilizando el mandril que se muestra en la Fig. 7.
Instalación de discos de embrague. Los discos de embrague reparados se instalan en un automóvil en el siguiente orden:
- - se coloca lubricante refractario (constalin o grasa 1-13) en el orificio del rodamiento de bolas del eje de transmisión de la caja de cambios instalado en el volante;
- - limpie las superficies de fricción del volante y del plato de presión con un paño limpio ligeramente humedecido con gasolina;
- - introducir el disco conducido en el cárter, primero, asegurándose de que la parte corta de su cubo esté orientada hacia el volante, luego introducir la placa de presión, girando hacia abajo una de sus patas de soporte y presionándola contra el volante;</ li>
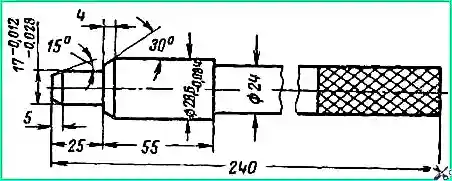
- - centre el disco impulsado con respecto al eje del cigüeñal del motor. Para hacer esto, inserte el mandril que se muestra en la Fig. en el orificio estriado del cubo del disco a través del orificio trasero de la carcasa del embrague. 8, de modo que su extremo encaje en el rodamiento de bolas del volante.
- Para centrar el disco impulsado, puede utilizar el eje libre de la caja de cambios;
- - antes de fijar la carcasa del embrague al volante, alinee las marcas en el volante y la carcasa, que se eliminan en fábrica después de equilibrar el cigüeñal, el volante y el embrague;
- - apretar progresivamente todos los tornillos que fijan la carcasa al volante;
- - instalar la caja de cambios y la parte inferior de la carcasa del embrague.
Reparación del accionamiento de desembrague del automóvil GAZ-66
Después de desmontar los cilindros principal y de trabajo, inspeccionar sus piezas, así como las piezas del soporte del pedal.
Las dimensiones nominales y las dimensiones máximas hasta las cuales se permite el desgaste de piezas sin reparación se indican en la tabla. 5.
Tabla 5. Dimensiones nominales y máximas permitidas de las piezas de accionamiento de desembrague sin reparación
Diámetro del orificio del cilindro maestro para el pistón:
- - tamaño nominal - 22 +0,023 mm;
- - tamaño permitido - 22.085 mm
Diámetro exterior del pistón del cilindro maestro:
- - tamaño nominal - 22 -0,040 mm;
- - tamaño permitido - 21.810 mm
Diámetro interior del cilindro de trabajo para pistón
- - tamaño nominal - 24 +0,023 mm;
- - tamaño permitido - 24,085 mm
Diámetro exterior del pistón del cilindro de trabajo
- - tamaño nominal - 24 -0,020 mm;
- - tamaño permitido - 23.840 mm
Diámetro interior del casquillo del pedal del embrague
- - tamaño nominal - 18 +0,105 mm;
- - tamaño permitido - 18.250 mm
Diámetro interior del casquillo del eje empujador
- - tamaño nominal - 14 +0,070 mm;
- - tamaño permitido - 14.210 mm
Si se detectan rayones o rayones en el espejo de los cilindros maestro o esclavo, Es posible reemplazar el cilindro o esmerilarlo y pulirlo hasta alcanzar uno de los tamaños de reparación recomendados en la tabla. 6 y 7.
Tabla 6. Dimensiones de reparación de piezas del cilindro maestro de desembrague
Tamaño nominal:
- - diámetro del cilindro - 22 +0,023 mm;
- - diámetro del pistón - 22 -0,040 mm;
- - diámetro del borde de trabajo del manguito interior - 23±0,2 mm
Tamaño de la primera reparación:
- - diámetro del cilindro - 22,25 +0,023 mm;
- - diámetro del pistón - 22,25 -0,040 mm;
- - diámetro del borde de trabajo del manguito interior - 23,5±0,2 mm
Segundo tamaño de reparación:
- - diámetro del cilindro - 22,50 +0,023 mm;
- - diámetro del pistón - 22,50 -0,040 mm;
- - diámetro del borde de trabajo del manguito interior - 23,5±0,2 mm
Durante el montaje, se permite instalar collares de sellado internos del tamaño nominal en el cilindro principal del primer tamaño de reparación.
Se pueden instalar collares de sellado externos de tamaño nominal para el primer y segundo tamaño de reparación.
Está permitido instalar un collar de sellado de tamaño nominal en el cilindro de trabajo del primer tamaño de reparación.
Tabla 7. Dimensiones de reparación de las piezas del cilindro de trabajo de desembrague
Edición anterior a junio de 1967:
- - nominal: diámetro del cilindro - 24 +0,023 mm, diámetro del pistón - 24 -0,02 mm, borde de trabajo del manguito - 25 +0,20 mm;
- - primera reparación: diámetro del cilindro - 24,25 +0,023 mm, diámetro del pistón - 24,25 -0,02 mm, borde de trabajo del manguito - 25,5 +0,20 mm;
- - segunda reparación: diámetro del cilindro - 24,5 +0,023 mm, diámetro del pistón - 24,5 -0,02 mm, borde de trabajo del manguito - 25,5 +0,20 mm
Edición desde junio de 1967:
- - nominal: diámetro del cilindro - 22 +0,023 mm, diámetro del pistón - 22 -0,02 mm, borde de trabajo del manguito - 22,7 +0,20 mm;
- - primera reparación: diámetro del cilindro - 22,25 +0,023 mm, diámetro del pistón - 22,25 -0,02 mm, borde de trabajo del manguito - 23,2 +0,20 mm;
- - segunda reparación: diámetro del cilindro - 22,5 +0,023 mm, diámetro del pistón - 22,5 -0,04 mm, borde de trabajo del manguito - 23,2 +0,20 mm
Las puntas esféricas de los empujadores de los cilindros principal y de trabajo, así como los huecos esféricos en los pistones de los cilindros y en el pasador de empuje de la horquilla del embrague deben ser lisos, sin marcas.
Las puntas de los empujadores deben coincidir con los huecos de los pistones a lo largo del punto en el centro de las esferas. Si se produce contacto a lo largo del anillo, entonces el acoplamiento es incorrecto y puede provocar que el empujador se pegue, desalineación y desgaste del pistón.
Al lijar la esfera en los empujadores, debes asegurarte de que el contacto no esté en el anillo, sino en el lugar.
Inspeccione los extremos de todos los casquillos y arandelas de plástico del soporte del pedal, limpie con cuidado las rebabas en sus extremos.
Comprueba que los muelles de tensión y retorno no están flojos.
Si los resortes están debilitados, reemplácelos.