El sistema de freno neumático de un autobús consta de un compresor, dispositivos neumáticos y tuberías
Para evitar que se obstruyan fallas de los dispositivos neumáticos del sistema de frenos, se instala un filtro para purificar el aire comprimido en la entrada de la válvula de freno, secador, válvula de seguridad de cuatro circuitos y en los moduladores (2 cada uno).
La primera comprobación del estado de los filtros se debe realizar tras el rodaje del autobús.
Si la malla está obstruida es necesario desenroscar el filtro del racor del cuerpo del dispositivo neumático mediante unas pinzas y limpiarlo con aire comprimido.
Se recomiendan más controles del estado del filtro durante el mantenimiento estacional.
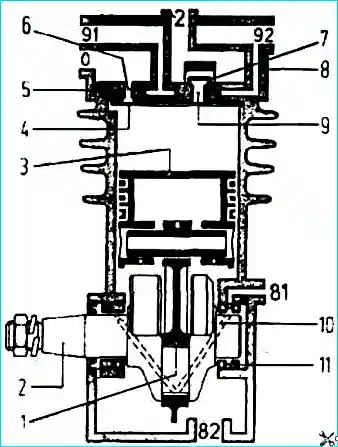
Compresor - (Fig. 1) tipo pistón monocilíndrico, con bloque de cilindros refrigerado por aire y culata refrigerada por agua.
El compresor es accionado por una correa de la polea del cigüeñal. La tensión de la correa se ajusta moviendo el soporte del compresor.
El aceite del muñón de la biela se suministra al orificio del cigüeñal del compresor a través de la cubierta trasera a través de una manguera desde el sistema de lubricación del motor.
Los rodamientos de bolas, los pasadores del pistón y las paredes del cilindro están lubricados por salpicadura. El aceite se drena del compresor al cárter de aceite del motor.
Al dar servicio al compresor, verifique la fijación del compresor al soporte, la fijación del soporte al motor, la fijación de la polea, la tensión de la correa de transmisión, la fijación de la culata del compresor, así como así como el estado y sujeción de la manguera de descarga del compresor y de las mangueras de suministro de refrigerante a la culata.
El ajuste de las tuercas de la culata debe realizarse uniformemente en diagonal en varios pasos, cada paso no más de 1 o 2 bordes.
El apriete final se realiza con un par de 18-25 Nm (1,8-2,5 kgf m).
Al instalar un compresor nuevo, después de un rodaje de 15 minutos, debe comprobar la tensión de las correas de transmisión.
Para un compresor fabricado por AK ADVIS OJSC, se recomienda limpiar los pistones y válvulas de los depósitos de carbón una vez al año durante el mantenimiento estacional, pero no más de después de 100.000 km.
Los signos de un mal funcionamiento del compresor son: aparición de ruidos y golpes, calentamiento excesivo (más de 190˚C), aumento del contenido de aceite en el condensado drenado de los cilindros de aire.
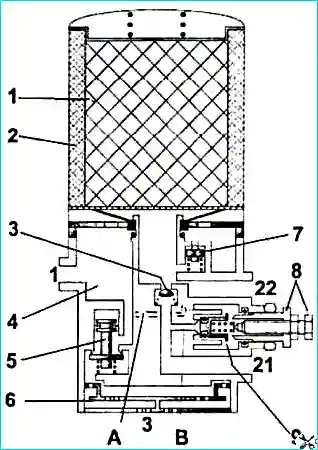
Entradas: 1 - entrada del compresor; 21 - salida a la válvula de seguridad de cuatro circuitos; 22 - salida al receptor de aire de regeneración; 3 - salida atmosférica
Un secador de aire con un regulador de presión incorporado (Fig. 2) está diseñado para limpiar el aire comprimido de la humedad y los contaminantes, así como para mantener automáticamente la presión de funcionamiento en el sistema de accionamiento del freno neumático.
El aire suministrado por el compresor de aire pasa a través del filtro de anillo 2, donde se limpia previamente de contaminantes.
Allí se enfría el aire y parte de la humedad que contiene se recoge en la cámara de separación de humedad 4.
Luego se seca el aire, pasa por el polvo granulado 1, entra en la válvula de retención 3, la abre y pasa por la salida 21 a la válvula de seguridad de cuatro circuitos y luego a los receptores de aire.
Al mismo tiempo, se llena un depósito de aire con una capacidad de 5 litros a través de la boquilla y la salida 22 para regenerar el elemento de secado.
¡Atención! El secador de aire tiene un conjunto de válvula calentada eléctricamente, que se activa mediante un botón en el panel de instrumentos.
La calefacción eléctrica se enciende automáticamente a una temperatura ambiente inferior a +10°C y se apaga después de calentar a +30°C.
La secadora no requiere mantenimiento especial.
Para controlar el funcionamiento normal de la secadora, se debe comprobar diariamente la ausencia de condensación en el cilindro situado después de la secadora y controlar la estanqueidad del accionamiento neumático del sistema de frenos.
Si se utiliza correctamente, el elemento filtrante del secador proporciona una purificación del aire de alta calidad durante dos años.
Si aparece condensación en los receptores, es necesario sustituir el elemento filtrante.
Si hay aceite en el condensado, es necesario eliminarlo instale el compresor, ya que lubricar los gránulos de polvo desecante reduce drásticamente su vida útil.
La sustitución del elemento filtrante del secador de aire se realiza en el siguiente orden:
- 1. Limpia la superficie de la secadora de suciedad.
- 2. Afloje la conexión roscada del tubo de descarga del compresor y purgue el aire.
- 3. Desenrosque el cartucho del elemento filtrante girándolo en sentido antihorario.
- 4. Instale un cartucho nuevo, lubricando ligeramente la junta de sellado con aceite.
- 5. Apriete el cartucho manualmente a un par de no más de 15 Nm (1,5 kgf m).
- 6. Apriete la conexión roscada del tubo de descarga.
La válvula de seguridad de cuatro circuitos está diseñada para dividir la línea de suministro en dos circuitos principales y dos adicionales, apagar automáticamente uno de los circuitos en caso de daño y mantener un suministro de aire comprimido en circuitos no dañados, así como para preservar el aire en todos los circuitos en caso de daños en la línea de suministro.
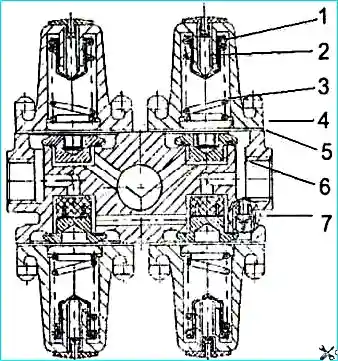
Las secciones de la válvula de seguridad se ajustan de tal manera que primero se abren las válvulas principales del sistema de freno de servicio y el accionamiento de la puerta (en la Fig. 4, secciones 21, 22, 24) a una presión de derivación de 6,2 +0,3 kgf/cm 2, y luego la válvula del sistema de freno de estacionamiento (sección 23) se abre a una presión de derivación de 6,7 +0,3 kgf/cm 2.
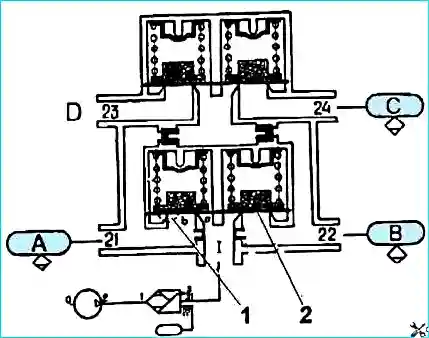
Cuando la sección 21 se despresuriza desde la sección 23 a través de una válvula especialmente incorporada, el aire comprimido se desvía a una velocidad de al menos 60 l/min.
Después del bypass, la presión del aire residual en los acumuladores de energía no debe ser superior a 1 kgf/cm 2.
El ajuste de la válvula elimina la posibilidad de arrancar el autobús al llenar el sistema neumático con aire comprimido hasta el punto que asegura el frenado del autobús con la eficiencia requerida, y también elimina la posibilidad de soltar el sistema de freno de estacionamiento del autobús cuando el nivel de presión en el circuito 1 del sistema de freno de servicio cae por debajo de un nivel mínimo de menos de 4,0 kgf/cm 2.
La válvula manual del freno de estacionamiento está diseñada para controlar los acumuladores de energía de resorte del sistema de freno de estacionamiento.
Cuando el autobús está en movimiento, la manija de la grúa está en la posición extrema hacia adelante. El dispositivo de grúa garantiza que el mango vuelva automáticamente a la posición inferior cuando se suelta.
El mango se fija sólo en la posición más trasera.
Para liberar los acumuladores de energía de resorte, se debe tirar del mango hacia afuera en dirección radial, mientras el mango regresa libremente a la posición "liberada".
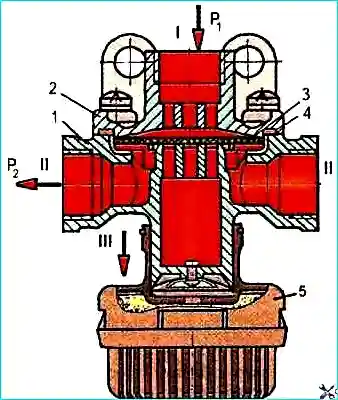
La válvula de liberación rápida está diseñada para acelerar la liberación de aire de los actuadores, reduciendo el camino recorrido por el aire comprimido durante la liberación.
La válvula está instalada cerca de las cámaras de freno del eje trasero.
Cuando la manija de la válvula del freno de estacionamiento está en la posición "liberada", el aire comprimido ingresa a la salida "I" de la válvula (Fig. 5), el diafragma 3 se presiona contra el asiento de salida en la carcasa; en este caso, los bordes del diafragma se doblan y el aire comprimido pasa a los terminales "II" y luego a los acumuladores de energía.
Cuando la presión en el terminal I cae, el diafragma 3, bajo la acción del aire comprimido en los terminales II, se arranca del asiento de salida en la carcasa 1 y se presiona contra el asiento en la tapa 2, bloqueando así el paso de aire hacia terminal “I”. El aire comprimido se libera a la atmósfera a través del terminal "III".
Las posibles averías de la válvula de liberación rápida incluyen: fuga de aire comprimido a través del conector de la tapa 2 (Fig. 5) y la carcasa 1, que se produce debido al aflojamiento de la tapa o a un defecto en el anillo de sellado 4, y liberación del aire comprimido al medio ambiente y del terminal "III" debido a una membrana defectuosa 3.
Para desmontar la válvula de liberación rápida, es necesario desatornillar los cuatro tornillos que sujetan la tapa 2.
Al reemplazar la membrana 3, también se debe reemplazar la junta tórica de goma 4 al mismo tiempo.
Después de ensamblar la válvula, se debe instalar sobre un soporte y probar su operatividad y estanqueidad de acuerdo con el diagrama que se muestra en la figura (cerrar el terminal derecho “II” con un tapón), de acuerdo con el siguiente método.
Aplicar y liberar aire a una presión de 0,75 MPa tres veces al terminal “I”.
- fije la presión en el terminal “I” a 0,02 MPa. En este caso, la presión debería aparecer en el pin “II”.
- Aumente la presión en el terminal “I” a 0,75 MPa. En este caso, la presión en el terminal “II” debería aumentar.
La diferencia entre las presiones en los terminales “I” y “II” no debe exceder los 0,02 MPa.
La válvula debe ser revisada para detectar fugas bajo una presión de 0,5 MPa en el puerto “I”. Al lavar, no se permite la aparición de burbujas de aire durante 1 minuto.
A continuación, es necesario ajustar la presión a 0,75 MPa en los terminales “I” y “II” y reducir sucesivamente la presión en el terminal “I”.
En este caso, se debe observar una disminución correspondiente de presión en el terminal “II” y el aire debe escapar del terminal atmosférico “III”.
Cuando la presión en el terminal “I” disminuye a cero, la presión en el terminal “II” debería volverse cero.
La válvula de freno (Fig. 6) está diseñada para controlar los mecanismos de freno de las ruedas con un accionamiento de freno de doble circuito.
Los terminales “I” y “II” (ver Fig. 6) de la válvula están conectados a los receptores de aire de dos circuitos de accionamiento del freno de servicio separados.
Desde los terminales “III” y “IV”, el aire comprimido fluye hacia las cámaras de freno. Los interruptores de señal de freno están instalados en el cuerpo de la grúa.
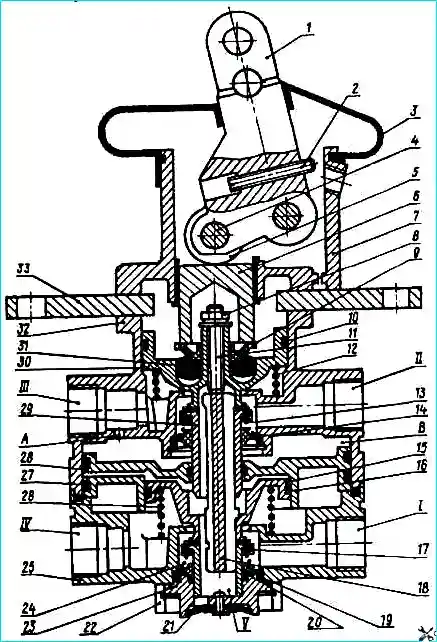
Al dar servicio a una válvula de freno, se verifica la conexión de la válvula al soporte de la base del cuerpo, se verifica la integridad de la funda protectora de goma y la estanqueidad de su instalación, y se realiza una verificación de diagnóstico para el funcionamiento correcto de la válvula. válvula.
En invierno, si el grifo se congela, para evitar daños en las piezas de goma y plástico, no se recomienda calentar el grifo al fuego.
Debes utilizar aire tibio o agua caliente para calentar.

Debido a la interrupción gradual de la movilidad de los pistones de la válvula de freno durante la operación del autobús, especialmente cuando el agua y el aceite ingresan a la válvula en la superficie de fricción, se recomienda realizar una verificación de diagnóstico del funcionamiento de la válvula durante A 2. Para hacer esto, sin quitar la válvula del autobús, debe conectar un manómetro a sus terminales seccionales superior e inferior y, presionando el pedal del freno, observar la diferencia de presión. La diferencia de presión no debe exceder los 0,25 kgf/cm 2.
Si no se cumple esta condición, se deberá reparar la grúa.
Se recomienda realizar el desmontaje preventivo de la válvula de freno una vez cada 2 años para limpiar, lubricar y sustituir juntas tóricas de goma y piezas desgastadas.
Montaje y comprobación del funcionamiento de la válvula de freno
1. El montaje debe realizarse teniendo en cuenta los siguientes requisitos:
- a) el montaje debe realizarse en condiciones que excluyan la posibilidad de que polvo abrasivo, etc., entre en contacto con las piezas ensambladas.
- b) El montaje de las piezas de goma debe realizarse con cuidado para evitar la posibilidad de daños. No se permite la presencia de cortes, rayones y otros defectos en las piezas de goma.
- c) lubrique todas las superficies de fricción de las piezas con una fina capa de lubricante CIATIM 221. Se permite utilizar lubricantes ZhT-72 TU 38.101.345-77 o ZhT 79L TU 32CT 1176-86.
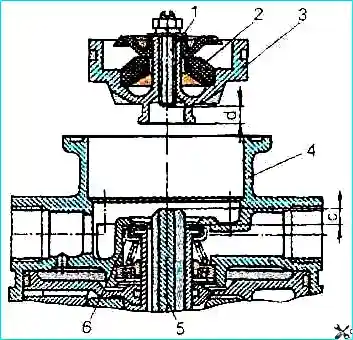
- 2. Antes de instalar el pistón superior, mida la distancia “c” (Fig. 8) del saliente del vástago del pistón por encima de la válvula.
- 3. Usando el tornillo de ajuste en el pistón superior, ajuste la distancia a = (c + 0,8) mm y bloquee el tornillo de ajuste.
- 4. Instale el pistón superior y, si es necesario, presiónelo con una abrazadera de transporte.
- 5. Ensamble el aparato con la placa base y la palanca.
- 6. Instale el perno de ajuste completamente en la palanca para que no quede espacio entre el rodillo 4 y el empujador 5 (Fig. 7), fije el perno de ajuste 2.
- 7. Conecte el grifo al sistema de aire comprimido de acuerdo con el diagrama de prueba (Fig. 7).
- 8. Mueva la palanca tres veces hasta que se detenga (recorrido de al menos 31,2 mm). Al mover la palanca no debe producirse atasco y debe volver rápidamente a su posición original.
- 9. Suministre aire bajo presión P11 = P12 = 0,75 mPa (7,5 kgf/cm 2) a los terminales 11 y 12. Mueva la palanca completamente ida y vuelta tres veces. La presión en los terminales 21 y 22 debe cambiar de 0 a la presión en los terminales 11 y 12 y viceversa.
- 10. Cuando la palanca se mueve entre 4,7 y 7,4 mm (carrera del empujador entre 1,9 y 3,0 mm), debería aparecer presión en el terminal 21. Cuando la presión en la salida 21 alcanza P21 = 0,05 mPa (0,5 kgf/cm 2), la presión en la salida 22 debe ser de al menos 0,025 mPa (0,25 kgf/cm 2).
En este caso, la carrera de la palanca debe superar los 4,7 mm (la carrera del empujador debe superar los 1,9 mm).
El aumento de presión en el terminal 21 antes del aumento de presión en el terminal 22 se puede mantener en todo el rango de presión, pero no exceder 0,025 mPa (0,25 kgf/cm 2).
El aumento de presión inicial en los terminales 21 y 22 no debe exceder los 0,02 mPa (0,2 kgf/cm 2).
- 11. Cuando se alcanza la presión P21 = 0,3 mPa (3,0 kgf/cm 2) en el terminal 21, la carrera de la palanca debe ser de 14,5-19,9 mm (carrera del empujador 5,8-8,0 mm).
- 12. Cuando se alcanza la presión P21 = 0,75 mPa (7,5 kgf/cm 2) en el terminal 21, la carrera de la palanca debe ser de 21 a 27 mm (la carrera del empujador es de 8,4 a 10,8 mm). ).
- 13. La carrera total de la palanca hasta el tope debe ser de 31,1 a 39,1 mm (la carrera del empujador es de 12,5 a 15,7 mm).
- 14. Cuando la palanca se mueve suavemente, la presión en los terminales 21 y 22 después del salto inicial debería aumentar gradualmente, y cuando se suelta la palanca, debería disminuir gradualmente.
- 15. Suministre aire bajo presión P12 = 0,75 mPa (7,5 kgf/cm 2) al terminal 12. Mueva la palanca por completo. En este caso, la presión en el terminal 22 debe cambiar de 0 a 0,75 MPa (7,5 kgf/cm 2).
- 16. Suministre aire bajo presión P11 = 0,75 mPa (7,5 kgf/cm 2) al terminal 11. Mueva la palanca por completo. En este caso, la presión en el terminal 21 debe cambiar de 0 a 0,75 MPa (7,5 kgf/cm 2).
- 17. Compruebe el dispositivo en busca de fugas. El grifo debe quedar sellado en cualquier posición de la palanca.
Verifique con la palanca suelta y presión P11 = P12 = 0,75 MPa (7,5 kgf/cm 2) en los terminales 11 y 12 y con la palanca presionada hasta el fondo y presión P = 0,75 mPa (7,5 kgf/cm 2) en el terminal 11.
La fuga de aire en cada caso no debe exceder los 8 cm 3 /min.
La transmisión de la válvula de freno se ajusta correctamente si el recorrido total del pedal del freno, determinado por el movimiento del centro de la pastilla del pedal, es de 105-117 mm.
En este caso, la plataforma del pedal no debe tocar el suelo en la posición extrema presionada y la válvula del freno debe estar completamente abierta.
Juego libre del pedal 18-25 mm.
El juego libre del pedal del freno está determinado por el diseño de la válvula del freno.
Si es necesario (al retirar e instalar un grifo), puede ajustarlo girando la horquilla a lo largo de la rosca de la varilla, alineando el orificio de la horquilla con el orificio de la palanca del grifo, que está en estado libre, y desenroscando la horquilla de la varilla una vuelta.
En esta posición, instale el pasador de la horquilla, fije el pasador y apriete la contratuerca de la horquilla.
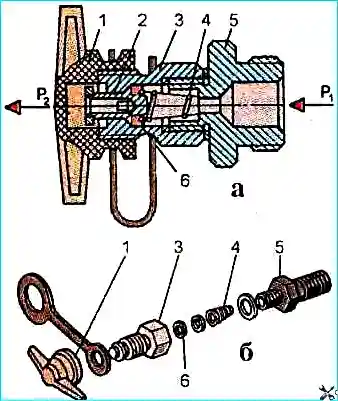
La válvula de salida de control (Fig. 9) está diseñada para conectar instrumentos de control y medición al variador con el fin de verificar la presión.
El autobús tiene tres válvulas: una en la cámara de freno delantera derecha y dos en la cámara de freno trasera derecha.
Para conectar a la válvula, utilice mangueras e instrumentos de medición con tuerca de unión º M16x1.5.
Para desmontar la válvula de salida de control, sujétela con un tornillo de banco en el racor 5 y desenrosque la tapa protectora 1.
Desatornille la carcasa 3, retire el resorte 4 y retire la válvula 6.
La válvula se monta en orden inverso.
Para comprobar el funcionamiento de la válvula, instálela en un banco de pruebas y conéctela según el diagrama que se muestra en la Fig. 9a.
Aplique aire a una presión de 0,75 MPa al terminal 1 (P1) y presione y suelte el empujador de la válvula tres veces.
Revise la válvula en busca de fugas.
Luego conecte una capacidad de 0,5 litros al pin 1(P2).
Empotrar el empujador de válvula. En este caso, la presión en los terminales 1 y 11 debería igualarse en no más de 5 s.
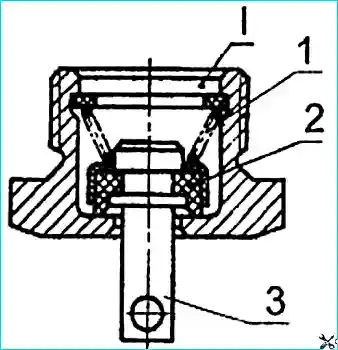
La válvula de drenaje de condensado (Fig. 10) está diseñada para drenar forzadamente el condensado del depósito de aire del accionamiento del freno y también, si es necesario, para liberar aire comprimido del depósito.
La válvula de drenaje de condensado se abre cuando presiona el empujador 3 hacia arriba o lo mueve en cualquier dirección.
Al realizar el mantenimiento del accionamiento neumático del sistema de frenos del autobús, se comprueba la estanqueidad del sistema en su conjunto y de sus piezas individuales.
Los lugares con fuertes fugas de aire se determinan de oído y los lugares con fugas débiles se determinan con emulsión de jabón.
Una fuga de aire en el sistema de frenos de servicio se determina cuando el sistema se llena hasta la presión de funcionamiento y se presiona el pedal del freno.
En este caso, la caída de presión no debe exceder 0,05 MPa (0,5 kgf/cm 2) durante 15 minutos y 0,05 MPa (0,5 kgf/cm 2) durante 30 minutos con los mandos en posición libre.
Se detecta una fuga de aire en el sistema de freno de mano cuando la manija del freno de mano está en la posición "Sin freno".
Las fugas de aire de las conexiones de las tuberías se eliminan apretando o reemplazando las piezas de conexión individuales.
Para evitar la rotura de los resaltes de conexión de los dispositivos neumáticos de freno, el par de apriete de los racores, tapones y tuercas no debe exceder los 30-50 Nm (3-5 kg/cm 2).
Para aumentar la confiabilidad y confiabilidad del sistema de frenos, se recomienda realizar el desmontaje preventivo de la válvula de freno una vez cada dos años; cámaras de freno de frenos traseros y delanteros, válvula de seguridad; válvula de freno manual; válvula de liberación rápida; sustitución de un cartucho secador de recambio, independientemente de su estado técnico.
Los dispositivos defectuosos descubiertos durante una verificación de control deben repararse utilizando kits de reparación y verificar su operatividad y cumplimiento de las especificaciones.
El procedimiento para ensamblar y probar los dispositivos se establece en instrucciones especiales. Sus reparaciones son realizadas por personas que han recibido la formación necesaria.