Пневматична система гальм автобуса складається з компресора, пневмоапаратів та трубопроводів
З метою запобігання відмовам пневмоапаратів гальмівної системи від засмічення, на вході в гальмівний кран, осушувач, чотириконтурний захисний клапан і в модулятори (по 2) встановлюється сітчастий фільтр очищення стисненого повітря.
Першу перевірку стану фільтрів слід проводити після обкатки автобуса.
У разі засміченості сітки, необхідно вивернути плоскогубцями фільтр зі штуцера корпусу пневмоапарата та очистити стисненим повітрям.
Наступні перевірки стану фільтрів рекомендується виконувати при сезонному технічному обслуговуванні.
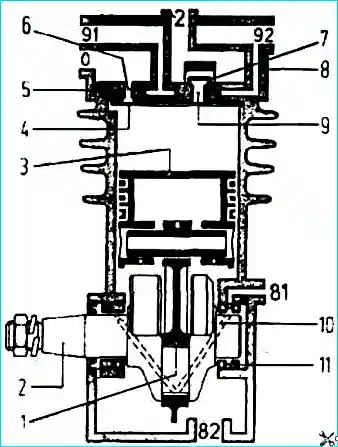
Компресор- (рис. 1) одноциліндровий поршневий тип, з повітряним охолодженням блоку циліндрів і з водяним охолодженням головки циліндрів.
Привід компресора ремінний від шківа колінчастого валу. Регулювання натягу ременів здійснюється переміщенням кронштейна компресора.
Масло до шатунної шийки подається в свердління колінчастого валу компресора через задню кришку по шлангу із системи змащення двигуна.
Шарикопідшипники, поршневі пальці та стінки циліндра змащуються розбризкуванням. З компресора масло зливається в олійний картер двигуна.
При обслуговуванні компресора перевіряється кріплення компресора до кронштейна, кріплення кронштейна до двигуна, кріплення шківа, натяг приводного ременя, кріплення головки циліндрів компресора, а також стан і кріплення нагнітального шланга компресора та шлангів підвода охлажда.
Протяжку гайок головки циліндрів слід виконувати рівномірно по діагоналі в кілька прийомів, кожен прийом не більше ніж на 1-2 грані.
Остаточна затяжка проводиться моментом 18-25 Нм (1,8-2,5 кгс м).
При установці нового компресора після 15 хвилинної обкатки слід перевірити натяг приводних ременів.
Для компресора виробництва ВАТ «АК АДВІС» рекомендується один раз на рік при сезонному обслуговуванні, але не більше ніж через 100000 км пробігу здійснити очищення від нагару поршнів та клапанів.
Ознаками несправності компресора є: поява шуму і стукоту в ньому, надмірне нагрівання (понад 190˚С), збільшений вміст масла в конденсаті, що зливається з повітряних балонів.
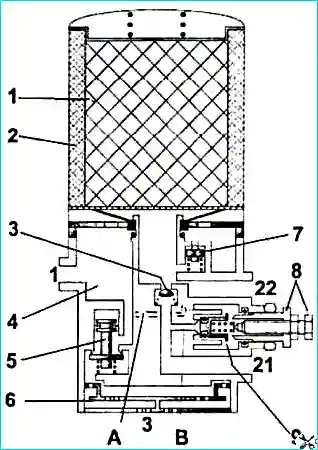
Підводи: 1 - підведення від компресора; 21 - відведення до чотириконтурного захисного клапана; 22 - відведення до повітряного ресивера регенерації; 3 - атмосферний висновок
Осушувач повітря з вбудованим регулятором тиску (мал. 2) призначений для очищення стисненого повітря від вологи та забруднень, а також для автоматичної підтримки робочого тиску в системі пневматичного приводу гальм.
Подається повітряним компресором повітря проходить через кільцевий фільтр 2, де відбувається його попереднє очищення від забруднень.
Там же повітря охолоджується, а частина вологи, що міститься в ньому, збирається в камері відокремлення води 4.
Потім повітря осушується, проходячи через гранулоподібний порошок 1, і надходить до зворотного клапана 3, відкриває його і проходить через відведення 21 до чотириконтурного захисного клапана і далі до повітряних ресиверів.
Одночасно через жиклер і відвід 22 наповнюється повітряний ресивер ємністю 5 літрів для регенерації осушуючого елемента.
Увага! Осушувач повітря має електропідігрів клапанного вузла, що вмикається кнопкою на щитку приладів.
Електропідігрів включається автоматично при температурі навколишнього повітря менше +10°С і відключається після нагрівання до +30°С.
Спеціального обслуговування осушувач не потребує.
Для контролю нормальної роботи осушувача слід щодня перевіряти відсутність конденсату в балоні, розташованому після осушувача, і стежити за герметичністю пневматичного приводу гальмівної системи.
При правильній експлуатації фільтруючий елемент осушувача забезпечує якісне очищення повітря протягом двох років.
При появі в ресиверах конденсату необхідно замінити фільтруючий елемент.
При наявності в конденсаті оліїа необхідно відремонтувати компресор, оскільки замаслювання гранул порошку осушувача різко знижує термін його роботи.
Заміна фільтруючого елемента осушувача повітря проводиться в наступному порядку:
- 1. Очистити поверхню осушувача від бруду.
- 2. Послабити різьбове з'єднання нагнітального трубопроводу від компресора та випустити з нього повітря.
- 3. Відвернути, обертаючи проти годинникової стрілки, патрон фільтруючого елемента.
- 4. Встановити новий патрон, трохи змастивши маслом ущільнювальну прокладку.
- 5. Затягнути рукою патрон не більше 15 Нм (1,5 кгс м).
- 6. Затягнути різьбове з'єднання нагнітального трубопроводу.
Чотириконтурний захисний клапан призначений для поділу живильної магістралі на два основних і два додаткові контури, автоматичного відключення одного з контурів у разі його пошкодження та збереження запасу стисненого повітря в неушкоджених контурах, а також для збереження повітря у всіх контурах у разі пошкодження живильної магістралі .
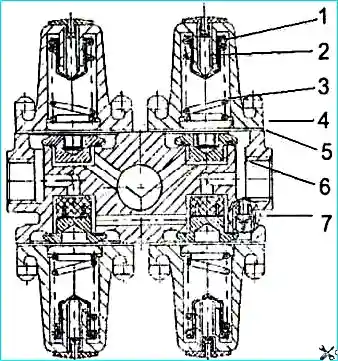
Регулювання секцій захисного клапана проведено таким чином, що спочатку відкриваються магістральні клапани робочої гальмівної системи та приводу дверей (на рис. 4 секцій 21, 22, 24) при величині тиску перепуску 6,2 +0,3 кгс/см 2, а потім відкривається клапан гальмівної системи стоянки (секції 23) при величині тиску перепуску 6,7 +0,3 кгс/см 2.
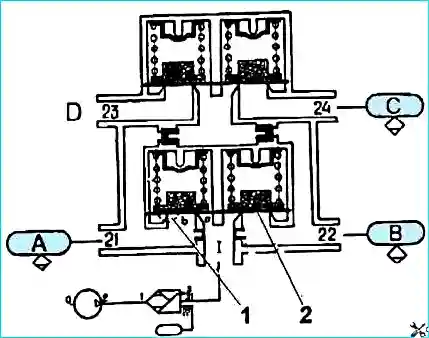
При розгерметизації секції 21 у неї з секції 23 через спеціально вбудований клапан забезпечується перепуск стиснутого повітря з темпом не менше 60 л/хв.
Після перепуску залишковий тиск повітря в енергоакумуляторах повинен бути не більше 1 кгс/см 2 .
Регулювання клапана виключає можливість торкання автобуса з місця при заповненні пневмосистеми стисненим повітрям до моменту, що забезпечує загальмовування автобуса з необхідною ефективністю, а також виключає можливість гальмування стоянкової гальмівної системи автобуса при зниженні рівня тиску в контурі 1 робочої гальмівної системи ,0 кгс/см 2.
Ручний кран гальма стоянки призначений для керування пружинними енергоакумуляторами стоянкової гальмівної системи.
Під час руху автобуса рукоятка крана знаходиться в крайньому передньому положенні. Пристрій крана забезпечує автоматичне повернення рукоятки в нижнє положення при відпусканні.
Тільки в крайньому задньому положенні ручка фіксується.
Для відгальмовування пружинних енергоакумуляторів ручку слід витягнути в радіальному напрямку, при цьому ручка вільно повертається в положення "відгальмовано".
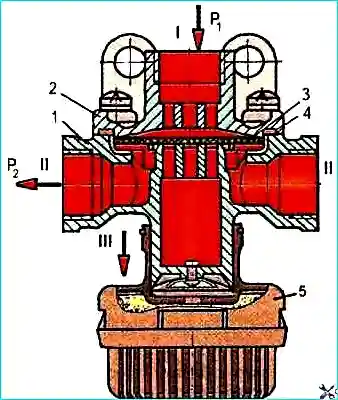
Клапан швидкого гальмування призначений для прискорення випуску повітря з виконавчих механізмів, за рахунок скорочення шляху прохідного стисненим повітрям під час випуску.
Клапан встановлений біля гальмівних камер заднього моста.
При положенні рукоятки крана гальма стоянки в положенні «відгальмовано» стиснене повітря надходить у виведення "I" клапана (рис. 5), діафрагма 3 притискається до випускного сідла в корпусі; при цьому краї діафрагми відгинаються і стиснене повітря проходить у висновки "II" і далі в енергоакумулятори.
При падінні тиску у виведенні I діафрагма 3 під дією стисненого повітря у висновках II відривається від випускного сідла в корпусі 1 і притискається до сідла у кришці 2, перекриваючи тим самим прохід повітря у виведення "I". Стиснене повітря при цьому через виведення "III" випускається в атмосферу.
До можливих несправностей клапана швидкого відгальмовування відносяться: витік стисненого повітря по роз'єму кришки 2 (рис. 5) і корпусу 1, яка відбувається через ослаблення кріплення кришки або дефекту кільця ущільнювача 4, і вихід стисненого повітря в о довкілля з виведення "III" через несправність мембрани 3.
Для розбирання клапана швидкого гальмування треба відвернути чотири гвинти кріплення кришки 2.
При заміні мембрани 3 одночасно треба замінити і гумове кільце ущільнювача 4.
Після складання клапана його треба встановити на стенд і провести випробування на працездатність та герметичність за схемою, показаною на малюнку (правий висновок "II" закрити заглушкою), за наступною методикою.
Три рази подати та випустити повітря під тиском 0,75 МПа у виведення "I".
- встановити тиск у виведенні "I" - 0,02 МПа. При цьому у висновку "II" має виникнути тиск.
- Підвищити тиск у виведенні "I" до 0,75 МПа. При цьому тиск у виведенні "II" має зростати.
Різниця між тисками у висновках "I" та "II" не повинна перевищувати 0,02 МПа.
Перевірку клапана на герметичність треба проводити під тиском 0,5 МПа у виведенні "I". При обмиленні поява бульбашок повітря не допускається протягом 1 хв.
Далі треба встановити тиск 0,75 МПа у висновках "I" та "II" і послідовно знижувати тиск у виводі "I".
При цьому у виведенні "II" має спостерігатися відповідне зниження тиску, а з атмосферного виведення "III" має виходити повітря.
При зниженні тиску у виведенні "I" до нуля тиск у виведенні "II" має стати рівним нулю.
Кран гальмівний (мал. 6.) призначений для керування колісними гальмівними механізмами при двоконтурному гальмівному приводі.
Висновки "I" та "II" (див. рис. 6) крана з'єднані з повітряними ресиверами двох роздільних контурів приводу робочого гальма.
Від висновків "III" та "IV" стиснене повітря надходить до гальмівних камер. У корпусі крана встановлено вимикачі сигналів гальмування.
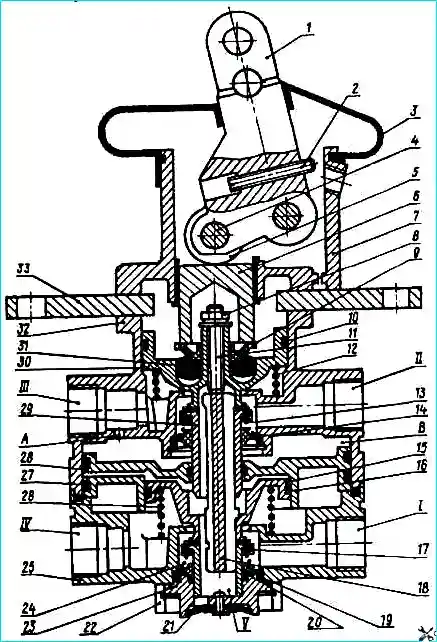
При обслуговуванні гальмівного крана перевіряється кріплення крана до кронштейна основи кузова, перевіряється цілісність захисного гумового чохла та щільність його встановлення, проводиться діагностична перевірка правильності роботи крана.
У зимовий час у разі замерзання крана для попередження пошкоджень гумових та пластмасових деталей не рекомендується відігрівати кран відкритим вогнем.
Слід застосовувати для опалення тепле повітря або гарячу воду.

У зв'язку з поступовим порушенням рухливості поршнів гальмівного крана в процесі експлуатації автобуса, особливо при попаданні води та олії всередину крана на поверхні тертя, рекомендується при ТО-2 проводити діагностичну перевірку роботи крана. Для цього потрібно, не знімаючи кран з автобуса, приєднати до його верхнього і нижнього секційних висновків по одному манометру і, натискаючи на гальмо педаль, відзначати різницю тисків. Різниця тиску не повинна перевищувати 0,25 кгс/см 2.
При невиконанні цієї умови необхідно провести ремонт крана.
Рекомендується періодичністю один раз на 2 роки проводити профілактичне розбирання гальмівного крана для очищення, мастила та заміни гумових ущільнювальних кілець та зношених деталей.
Складання та перевірка працездатності гальмівного крана
1. Складання проводити з урахуванням таких вимог:
- а) збірка повинна проводитися в умовах, що виключають можливість потрапляння на деталі абразивного пилу, що збираються, тощо.
- б) складання гумових деталей повинно проводитися обережно, щоб унеможливити їх пошкодження. Наявність на гумових деталях порізів, рисок та інших дефектів не допускається.
- в) всі деталі, що труться, змастити тонким шаром мастила ЦИАТИМ 221. Допускається застосування мастил ЖТ-72 ТУ 38.101.345-77 або ЖТ 79Л ТУ 32ЦТ 1176-86.
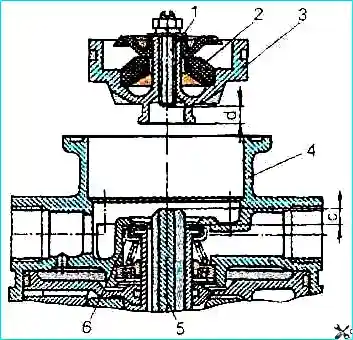
- 2. Перед встановленням верхнього поршня виміряти відстань "с" (рис. 8) виступу хвостовика поршня над клапаном.
- 3. За допомогою регулювального гвинта у верхньому поршні встановити відстань а = (з + 0,8) мм та законтрити регулювальний гвинт.
- 4. Встановити верхній поршень і за потреби притиснути його транспортним затискачем.
- 5. Зібрати апарат з опорною плитою та важелем.
- 6. Встановити регулювальний болт до упору в важіль так, щоб не було зазору між роликом 4 і штовхачем 5 (рис. 7), зафіксувати регулювальний болт 2.
- 7. Підключити кран до системи стисненого повітря відповідно до схеми випробувань (мал. 7).
- 8. Тричі перемістити важіль до упору (хід не менше 31,2 мм). При переміщенні важеля не повинно бути заїдань і він має швидко повертатися у вихідне положення.
- 9. Подати повітря під тиском Р11 = Р12 = 0,75 мПа (7,5 кгс/см 2) висновки 11 і 12. Тричі перемістити важіль до упору та назад. Тиск у висновках 21 та 22 має змінюватися від 0 до тиску у висновках 11 та 12 та назад.
- 10. При переміщенні важеля на 4,7-7,4 мм (хід штовхача 1,9-3,0 мм) у виводі 21 має з'явитись тиск. При досягненні у виведенні 21 тиску Р21 = 0,05 мПа (0,5 кгс/см 2) тиск у виводі 22 має бути не менше 0,025 мПа (0,25 кгс/см 2).
При цьому хід важеля повинен перевищувати 4,7 мм (хід штовхача має перевищувати 1,9 мм).
Випередження зростання тиску у виводі 21 по відношенню до зростання тиску у виводі 22 може зберігатися по всьому діапазону тисків, але не перевищувати 0,025 мПа (0,25 кгс/см 2 ).
Початковий стрибок тиску у висновках 21 і 22 не повинен перевищувати 0,02 мПа (0,2 кгс/см 2).
- 11. При досягненні у виведенні 21 тиску P21 = 0,3 мПа (3,0 кгс/см 2) хід важеля має бути 14,5-19,9 мм (хід штовхача 5,8-8,0 мм).
- 12. При досягненні у виведенні 21 тиску Р21 = 0,75 мПа (7,5 кгс/см 2) хід важеля повинен бути 21-27мм (хід штовхача 8,4- 10,8 мм).
- 13. Загальний хід важеля до упору має становити 31,1-39,1 мм (хід штовхача 12,5-15,7 мм).
- 14. При плавному переміщенні важеля тиск у висновках 21 і 22 після початкового стрибка повинен плавно підвищуватися, а при відпусканні важеля плавно знижуватися.
- 15. Подати повітря під тиском Р12 = 0,75 мПа (7,5 кгс/см 2) у висновок 12. Перемістити важіль до упору. При цьому у виводі 22 тиск має змінитися від 0 до 0,75 мПа (7,5 кгс/см 2).
- 16. Подати повітря під тиском Р11 = 0,75 мПа (7,5 кгс/см 2) у висновок 11. Перемістити важіль до упору. При цьому у виведенні 21 тиск має змінитися від 0 до 0,75 мПа (7,5 кгс/см 2).
- 17. Перевірити апарат на герметичність. Кран повинен бути герметичний за будь-якого положення важеля.
Перевірку проводити при відпущеному важелі та тиску P11 = P12 = 0,75 МПа (7,5 кгс/см 2) у висновках 11 і 12 і при натисненому до упору важелі і тиску Р = 0,75 мПа (7,5 кгс/см 2) у виводі 11.
Витік повітря в кожному випадку не повинен перевищувати 8 см 3 /хв.
Привід гальмівного крана відрегульований правильно, якщо повний хід педалі гальма, який визначається по переміщенню центру майданчика педалі, становить 105-117 мм.
При цьому майданчик педалі не повинен торкатися підлоги в крайньому натиснутому положенні, а гальмівний кран повністю відкритий.
Вільний хід педалі 18-25 мм.
Вільний хід педалі гальма обумовлений конструкцією гальмівного крана.
У разі потреби (при знятті-установці крана) можна відрегулювати, сумісивши обертанням вилки по різьбленню тяги отвір у вилці з отвором важеля крана, що знаходиться у вільному стані, та вивернувши з тяги вилку на один оборот.
У цьому положенні слід встановити палець вилки, зашплінтувати палець і затягнути контргайку вилки.
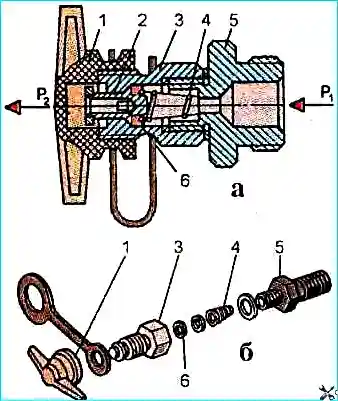
Клапан контрольного виведення (рис. 9) призначений для приєднання до приводу контрольно-вимірювальних приладів з метою перевірки тиску.
На автобусі встановлено три клапани: один на правій передній та два на правій задній гальмівних камерах.
Для приєднання до клапана слід застосовувати шланги та вимірювання прилади з накидною гайкою M16x1,5.
Для розбирання клапана контрольного виведення затиснути його в лещата за штуцер 5 і вивернути захисний ковпачок 1.
Відвернути корпус 3, вийняти пружину 4 і зняти клапан 6.
Складання клапана здійснюється у зворотній послідовності.
Для перевірки працездатності клапана встановити його на випробувальний стенд та підключити за схемою, показаною на рис. 9а.
Подати повітря під тиском 0,75 МПа у висновок 1(Р1) і тричі втопити та відпустити штовхач клапана.
Перевірити клапан на герметичність.
Потім підключити до виводу 1(Р2) ємність 0,5 л.
Втопити штовхач клапана. При цьому тиск у висновках 1 і 11 має зрівнятися протягом не більше 5 с.
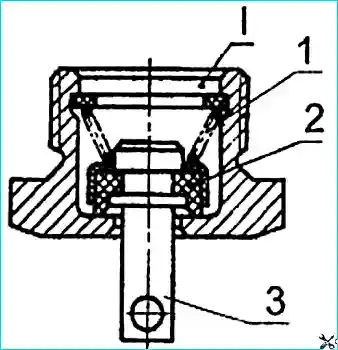
Кран зливу конденсату (рис. 10) призначений для примусового зливу конденсату з повітряного ресивера гальмівного приводу, а також, при необхідності, для випуску стисненого повітря з ресивера.
Кран зливу конденсату відкривається при натисканні на штовхач 3 вгору або відведенні його в будь-який бік.
Під час обслуговування пневматичного приводу гальмівної системи автобуса перевіряється герметичність системи в цілому та її окремих частин.
Місця сильного витоку повітря визначають на слух, а місця слабкого витоку - за допомогою мильної емульсії.
Витік повітря в робочій гальмівній системі визначається при заповненій системі до робочого тиску при натиснутій гальмівній педалі.
При цьому падіння тиску не повинно перевищувати 0,05 мПа (0,5 кгс/см 2) протягом 15 хвилин і 0,05 мПа (0,5 кгс/см 2) протягом 30 хвилин при вільному положенні органів управління.
Витік повітря в стоянковій гальмівній системі визначається при положенні рукоятки ручного гальма в положенні «Розторможено».
Витік повітря зі з'єднань трубопроводів усувається підтяжкою або заміною окремих деталей з'єднань.
Щоб уникнути поломки приєднувальних бобишок на гальмівних пневмоапаратах, момент затягування штуцерів, пробок, гайок не повинен перевищувати 30-50 Нм (3-5 кг/см 2).
Дня підвищення безвідмовності та надійності роботи гальмівної системи рекомендується один раз на два роки проводити профілактичне розбирання гальмівного крана; гальмівних камер задніх та передніх гальм, захисного клапана; ручного гальмівного крана; клапана швидкого гальмування; заміну змінного патрона осушувача незалежно від їх технічного стану.
Виявлені під час контрольної перевірки несправні апарати повинні бути відремонтовані за допомогою ремонтних комплектів, перевірені на працездатність та відповідність характеристикам.
Порядок збирання та перевірки апаратів викладено у спеціальних інструкціях. Їх ремонт здійснюється особами, які пройшли необхідну підготовку.