The engine cooling system (Fig. 1) is liquid, closed type, with forced circulation of coolant
It consists of the following main elements; radiator, expansion tank, 7 water pump, fan, 2 thermostats and remote thermometer
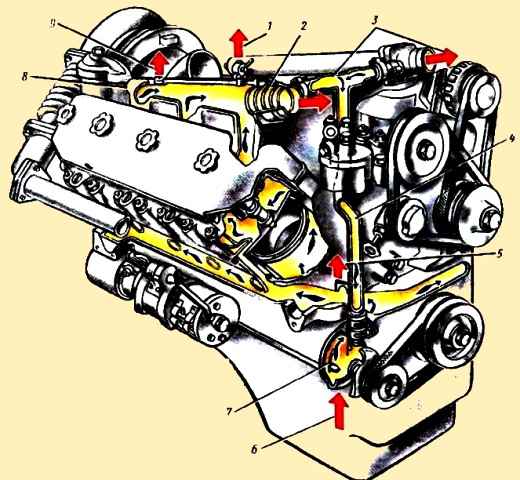
Cooling system diagram: 1 - air release when filling the cooling system during warming up with the starting heater: 2 - thermostat; 3 - coolant drain to the radiator; 4 - bypass tube; 5 - fluid supply to the air brake compressor; 6 - supply of coolant from the radiator; 7 - water pump; 8 - hole for installing a thermometer sensor; 9 - hot water outlet to the cabin heater
When the engine is running, the circulation of coolant in the cooling system is created by a centrifugal pump.
The pump takes fluid from the lower radiator reservoir and forces it through the channels in the timing gear cover into the right and left water jackets of the cylinder block.
Here the liquid washes the outer surface of the cylinder liners, absorbing heat, heats up, then from the cylinder block enters the water jackets of the cylinder heads and, first of all, to the hottest places - the exhaust valves and injector cups.
From the cooling jacket of the cylinder heads, the liquid enters the drainage pipelines, and from them through passages in the thermostats into the radiator, where it transfers heat to the air flow created by the fan.
The liquid cooled in the radiator again flows to the water pump.
Water pump (Fig. 2). Blade, centrifugal type - to prevent liquid from entering the cavity with lubricant, install a cuff 8 made of oil and petrol resistant rubber, which is pressed against the shaft with clips, and with a spring against the textolite thrust ring 6.
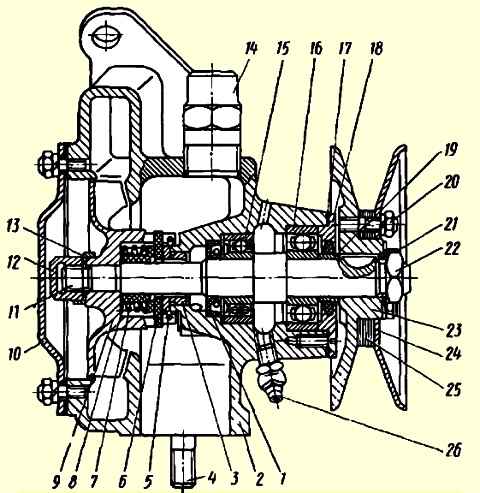
Water pump: 1 - oil seal; 2 - pump housing; 3 - bushing; 4 - stud for fastening the inlet pipe; 5 - oil seal retaining ring: 6 - oil seal thrust ring; 7 - oil seal spring; 8 - oil seal cuff; 9 - impeller; 10 - cover; 11 - roller; 12 - nut; 13 lock washer; 14 - bypass nipple of the water thermostat tube; 15,16 - ball bearings; 17 - gaskets; 18 - oil seal body; 19 - oil seal bushing; 20 - nut for fastening the pulley sidewall; 21 - lock washer; 22 - nut; 23 - pulley hub; 24 - sidewall of the pulley; 25 - adjusting shims; 26 - grease nipple
Radiator tubular-tape (snake) with oval-section tubes, three-row, mounted on the frame through rubber cushions.
A plug with a steam-air valve is installed on the expansion tank. The outlet valve of the plug opens at an excess pressure of 0.5 kgf/cm 2, which corresponds to water boiling at about 119˚ C.
The inlet valve of the plug opens when the pressure in the system drops to 0.13 kgf/cm 2.
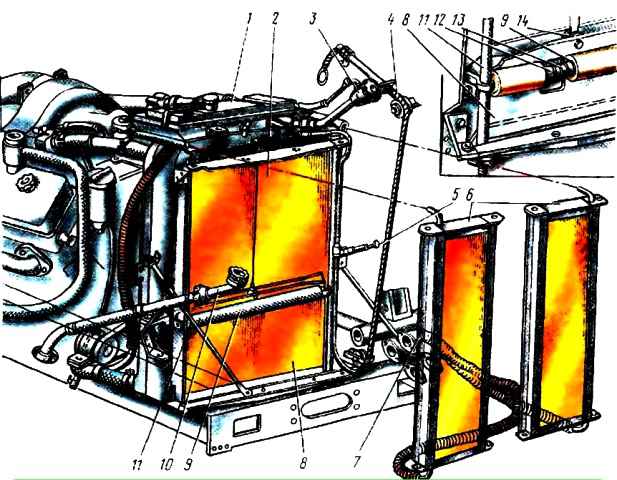
Radiator shutter drive: 1 - engine cooling expansion system tank; 2 - radiator of the engine cooling system; 3 - water filler neck; 4 - curtain drive cable; 5 - oil dipstick; 6 - oil radiators; 7 - tap for turning off oil radiators; 8 - curtain; 9 - drum; 10 - oil filler neck; 11 - drum bracket guide; 12 - axis; 13 - spring; 14 - drum bracket
Thermostats serve to speed up the warm-up of a cold engine and protect it from overcooling on the road.
When the temperature of the cooling system fluid drops to 70˚ C, thermostats automatically direct its entire flow directly to the water pump through the so-called small circulation circle, bypassing the radiator, and thereby create favorable conditions for its rapid warming up.
The radiator shutter can be fixed in any intermediate position and is controlled from the driver's cab.
Fan six-blade, gear-driven, rotates in the radiator casing.
Cooling system maintenance
To ensure normal operation of the cooling system, you must:
- - fill the cooling system with a special all-season liquid antifreeze-A 40 (composition by volume: antifreeze-A - 56%, clean water - 44%) or antifreeze A65 (antifreeze-A - 65%, clean water - 35%).
- - pour the liquid through a funnel with a mesh, using clean dishes;
- - monitor the temperature of the coolant, which should be within 75-98 ˚ C;
- - regularly check the coolant level through the neck of the cap on the expansion tank and top up if necessary. Measure with a cold engine. The minimum coolant level should be 10 mm from the bottom of the expansion tank;
- - in the summer, monitor the condition of the air channels of the radiator core and be sure to clean them if they are significantly clogged. Cleaning can be done with a jet of compressed air directed into the air channels of the radiator core from the casing side;
- - lubricate the water pump bearings in a timely manner.
Checking the system for tightness
A significant part of malfunctions in the cooling system occurs due to coolant leakage.
The most likely places for leakage are water pump seals, connections between hoses and pipes, radiator pipes and tanks, and drain valves.
The cooling system should be checked for leaks daily.
If the water pump impeller seal is faulty, liquid will flow out through the drain hole on the housing, which will protect the pump shaft bearings from destruction.
It is not allowed to eliminate fluid leakage from the pump by blocking the drainage hole. A pump with a faulty seal must be repaired.
Leaks at the hose interfaces can be eliminated by tightening the clamps, and if the hoses are damaged, by replacing them.
Adjusting the tension of the water pump drive belt.
A normally tensioned belt, when pressed with the thumb on the middle of the belt with a force of 3 kgf, should bend by 10 - 15 mm.
Belt tension is adjusted using spacers.
If the belt tension is weak, you need to unscrew the nuts securing the pulley sidewall and remove one or two adjusting shims, place them on the outer side of the sidewall and tighten the nuts, turning after tightening each nut, then check the belt tension.
The shims should not be removed from the pulley, since when replacing the old belt with a new one, all shims must be reinstalled between the hub and the removable pulley sidewall.
Belt slippage can occur due to oil getting on it. In this case, wipe the oily belt with a rag slightly moistened with gasoline.
Flushing the cooling system
In order to remove scale, rust and sediment, the cooling system must be flushed. When scale deposits are minor, a flush gun can be used for cleaning.
The engine and radiator are washed separately. To prevent rust, scale and sediment from the engine cooling jacket from clogging the radiator, the thermostats are removed from the engine before washing.
The direction of the jet should be opposite to the direction of water movement during normal circulation.
Before flushing the radiator, make sure that it is not clogged, otherwise a strong jet of water may damage the radiator.
When flushing, the radiator hoses are disconnected from the engine and, with the plug closed, water is first supplied to the upper radiator pipe to remove dirt accumulated in the lower tank, and then the direction of water flow is reversed and washed until it comes out of the upper tank the water will not be completely clean.
Scaling is removed from the cooling system with a solution of technical Trilon B (TU 6431-71) in water (20 grams of Trilon per 1 liter of water).
Trilon is a white powder, non-toxic, easily soluble in water, and does not cause foaming of water when it is heated and boiling. Excessive amounts of Trilon do not harm the cooling system parts.
Trilon solution is poured into the cooling system.
After 1 day of engine operation (at least 6-7 hours), the spent solution is drained and fresh solution is added. Washing continues for 4 - 5 days.
In the absence of Trilon B, scale can be removed from the cooling system with a solution consisting of soda ash (washing soda) in an amount of 0.5 kg per 10 liters of water and kerosene 1.0 kg per 10 liters of water.
Pour the solution into the cooling system for 24 hours, of which the engine must be in operating mode for at least 8 hours, then drain the solution while hot, and after cooling the engine, rinse the cooling system with clean water.