Die Kompressorleistung bei 2000 U/min der Kurbelwelle beträgt 201 l/min. Der Kompressor muss zerlegt werden, wenn während des Betriebs Geräusche und Klopfgeräusche auftreten oder der Kompressor erheblich Öl in die Druckleitung abgibt.
Um den Kompressor vom Motor zu demontieren, entfernen Sie den Antriebsriemen, trennen Sie die Leitungen und lösen Sie die Befestigungsschrauben des Kompressors.
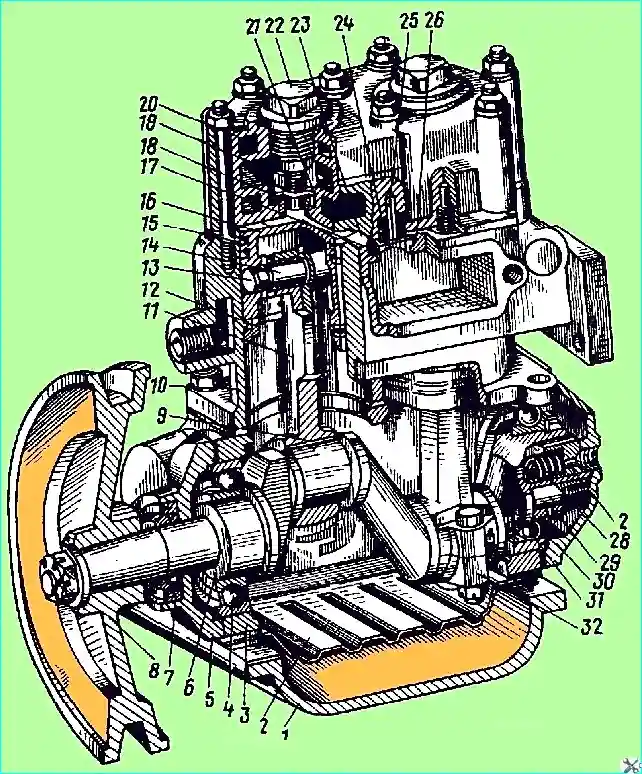
Zerlegen Sie den Kompressor in der folgenden Reihenfolge:
- – Schrauben Sie die Auslassventilstopfen ab und entfernen Sie die Federn und Ventile. Verwenden Sie einen Vierkantschlüssel mit einer Kopfgröße von 10 x 10 mm, um die Ventilsitze abzuschrauben.
- – Entfernen Sie die Kompressorriemenscheibe mit einem Abzieher. Den Segmentschlüssel herausschlagen.
- – Schrauben Sie die Befestigungsbolzenmuttern des Kompressorkopfes ab und entfernen Sie den Kompressorkopf vorsichtig, nachdem Sie zuvor die Kopfdichtung entfernt haben.
- – Entfernen Sie die Federn und Einlassventile aus der Aufnahme im Zylinderblock.
- – Lösen Sie die Schrauben und entfernen Sie die Luftzufuhrleitung.
- – Entfernen Sie die Pleueldeckel und bauen Sie die Kolben mit Pleuelstangen und Baugruppe aus dem Block aus.
- – Entfernen Sie die Kolbenringe, entnehmen Sie die Stopfen und den Kolbenbolzen und trennen Sie Pleuelstange und Kolben.
- – Lösen Sie die Schrauben und entfernen Sie den vorderen und hinteren Kurbelgehäusedeckel.
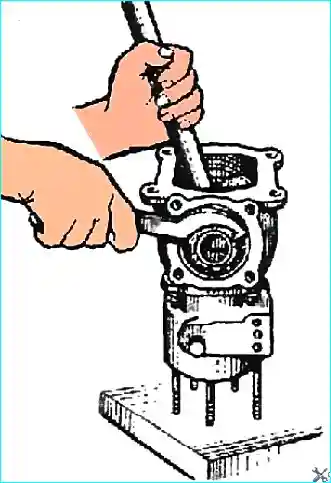
- — Entfernen Sie die hintere Deckeldichtung mit der Feder, schrauben Sie die Druckmutter des hinteren Kurbelwellenlagers ab (Abb. 2) und entfernen Sie die Sicherungsscheibe.
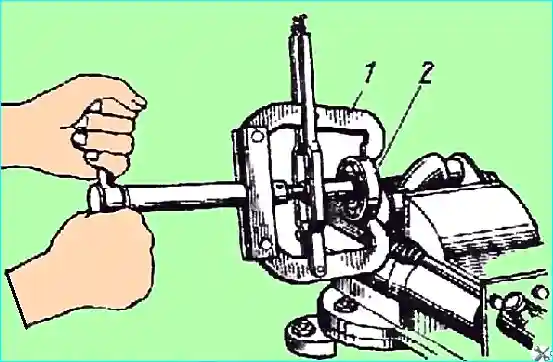
- — Kurbelwellenbaugruppe mit dem vorderen Lager durch den vorderen Lagersitz im Block herausschlagen. Das vordere Lager von der Kurbelwelle abpressen (Abb. 3);
- — Den Sicherungsring des hinteren Lagers entfernen und das hintere Lager aus dem Block drücken;
- — Den Wellendichtring vom vorderen Deckelsitz entfernen;
- — Block und Kurbelgehäuse trennen, die Stehbolzenmuttern lösen und die Dichtung vorsichtig abziehen.
Die Teile des zerlegten Kompressors waschen und sorgfältig prüfen. Alle Kanäle mit Druckluft ausblasen.
Prüfung des technischen Zustands von Kompressorteilen
Während des Betriebs können folgende Kompressordefekte auftreten:
- – im Zylinderkopf: Risse und Absplitterungen, ausgerissene Gewinde in den konischen Bohrungen für Fittings und Rohrleitungsbögen, Verformung der Passfläche zum Block;
- – im Zylinderblock: Risse, Brüche oder Riefenbildung und Verschleiß der Zylinderlauffläche;
- – im Kompressorkurbelgehäuse: Verschleiß der Lagersitze, ausgerissene Gewinde für Schrauben und Stehbolzen von Deckel und Block, Absplitterungen und Risse;
- – in der Kurbelwelle: Verschleiß der Pleuelzapfen, der hinteren und vorderen Deckeldichtung;
- – Verschleiß der Auslass- und Einlassventile und ihrer Sitze, Teile der Entlastungsvorrichtung, Schrumpfung oder Bruch der Ventilfedern;
- – in den Kompressorkolben: Riefenbildung, Verschleiß des Schaftes, Bohrungen bei Bolzen und Bruch von Kolbenringen;
- – im Kompressorpleuel – Verschleiß der oberen Zylinderkopfbuchse und Verschleiß der unteren Zylinderkopfbuchsen.
Ausgerissene oder verschlissene Gewinde im Blockkopf und anderen Kompressorteilen werden durch den Einbau von Einsätzen und anschließende Bearbeitung auf Nennmaß behoben.
Verschlissene Sitze und Ventile werden ausgetauscht. Nach dem Einbau eines neuen Sitzes oder Ventils müssen diese eingeschliffen werden.
Keilwellen Kolben und Muttern mit ausgerissenem Gewinde oder ohne Anschlussmöglichkeit müssen ausgetauscht werden.
Zylinderblock und andere Kompressorteile mit Absplitterungen und Rissen müssen durch neue ersetzt werden.
Zylinder werden durch Aufbohren und anschließendes Honen auf die in Tabelle 1 angegebenen Reparaturmaße repariert.
Beim Aufbohren von Zylindern dürfen Ovalität und Konizität 0,03 mm nicht überschreiten. Die Rechtwinkligkeit der Zylinderoberfläche zur Verbindungsebene mit dem Kurbelgehäuse darf auf einer Länge von 100 mm 0,03 mm nicht überschreiten.
Verschlissene Kolben und Kolbenringe müssen mit den in Tabelle 2 angegebenen Reparatursätzen ausgetauscht werden.
Der Unterschied im Kolbengewicht darf 15 g nicht überschreiten. Die Kurbelwellenhauptzapfen werden, sofern sie auf einen Durchmesser von weniger als 34,99 mm verschlissen sind, geschweißt und auf einen Durchmesser von 35 mm bearbeitet.
Verschlissene Pleuelzapfen werden auf das Reparaturmaß geschliffen und entsprechende Pleuellagersätze ausgewählt.
Beim Austausch der Kompressorkolbengruppe sollten Kolben, Pleuel und Bolzen gruppenweise ausgewählt werden (siehe Tabelle).
Die Teile der Gruppen sind farblich gekennzeichnet. Kolben und Kolbenbolzen sollten aus derselben Gruppe ausgewählt werden. Bei der Auswahl einer Pleuelstange ist der Einbau eines Bolzens aus einer benachbarten Gruppe zulässig.
Verbogene Pleuelstangen werden gerichtet. Die Abweichung der Pleuelkopfbohrungen darf auf einer Länge von 100 mm maximal 0,1 mm betragen.
Die Dichtung des vorderen Deckels, die keine Dichtheit gewährleistet, und die verschlissenen Teile der hinteren Dichtung werden nicht repariert und müssen ausgetauscht werden.
Montage des Kompressors
Der Kompressor muss gemäß den technischen Anforderungen in der folgenden Reihenfolge montiert werden:
- – Montage des Kolbens mit der Pleuelstange. Beim Einbau des Kolbenbolzens in die Pleuelstange sollte dieser mit Daumendruck fest in die Pleuelbohrung passen.
Kolben und Pleuelstange bei einer Umgebungstemperatur von 10–30 °C ohne Fett auswählen und bei der Endmontage die Kolbenbolzen-Pleuelbolzen-Verbindung mit Motoröl schmieren.
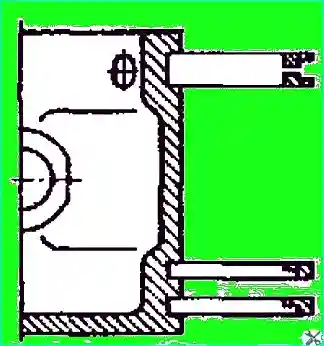
- – Kolbenringe am Kolben montieren (Abb. 4). Kompressionsringe mit der Nut am Innendurchmesser nach oben montieren.
Kompressionsringverbindungen vertikal zur Kolbenbolzenachse auf diametral gegenüberliegenden Kolbenseiten montieren.
- – Hinteres Kurbelwellenkugellager bis zum Anschlag in das Kompressorgehäuse einpressen. Vorderes Lager bis zum Anschlag auf die Kurbelwelle pressen.
Kurbelwelle in das Gehäuse einbauen, hintere Lagersicherungsscheibe auflegen, Mutter bis zum Anschlag des inneren Lagerrings an der Kurbelwelle festziehen und sichern.
- – Vorderen Kurbelgehäusedeckel montieren, Dichtung einpressen. Kurbelwellenzapfen vor dem Einbau mit Motoröl schmieren.
- – Feder und Dichtung in den Kurbelwellensitz einsetzen. Beim Einbau der Feder die Enden in die Kurbelwellen- und Dichtungsbohrung einführen.
Hinteren Kurbelgehäusedeckel montieren. Durch die Öffnung im Deckel prüfen, ob sich die Dichtung im Sitz frei bewegen kann. Kurbelwelle drehen. Die Drehkraft sollte 3 Nm nicht überschreiten.
- – Die Sitze 17 (siehe Abb. 1) und Führungen 26 der Einlassventile in den Block einpressen; die Einlassventile 25 einbauen.
- – Die Kolben mit Motoröl schmieren und zusammen mit den Gummiringen in die Sitze einsetzen. Die Kolben in den Buchsen müssen sich unter einer Kraft von 5 N frei bewegen lassen. Die Kolbenstangen mit den Buchsen in die Baugruppe, die Feder und den Kipphebel der Entlastungsvorrichtung einbauen.
- – Dichtung einbauen und Kurbelgehäuse mit Zylinderblock zusammenbauen.
- – Zylinderbohrung, Kurbelwellenzapfen, Kolbenringe und Hauptlager mit Motoröl schmieren.
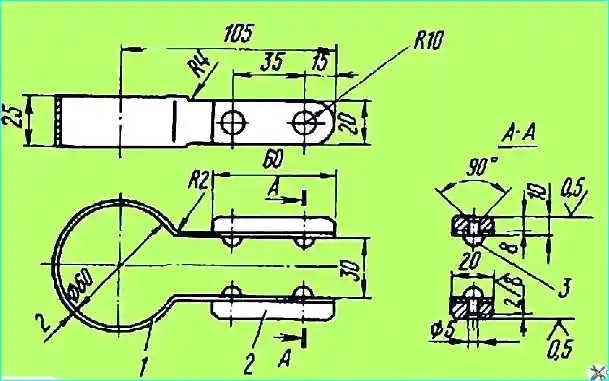
- – Kolben mit Pleuelstangen und Kompressionsringen mithilfe eines Presswerkzeugs in die Zylinder einbauen (Abb. 5);
Nach dem Einbau der Pleuellager die unteren Pleuelköpfe montieren. Das Anzugsdrehmoment der Pleuelschrauben beträgt 12,25–13,7 Nm.
Die Bohrung für den Splint in der Mutter und in der Pleuelschraube ausrichten und die Mutter festziehen. Die Mutter zum Einbau des Splints nicht lösen;
- – Leichtgängigkeit der Kurbelwelle prüfen; das Drehmoment zum Drehen der Kurbelwelle sollte 3 Nm nicht überschreiten;
- – Dichtung und Zylinderkopf montieren. Die Kopfbolzenmuttern gleichmäßig in zwei Schritten mit einem Anzugsdrehmoment von 12–17 Nm anziehen (Abb. 6).
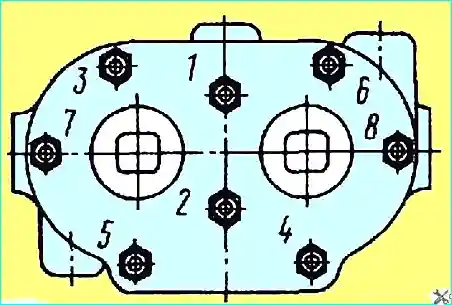
- – Schrauben Sie die 18 (siehe Abb. 1) Auslassventilsitze in die Zylinderkopfbuchsen ein, montieren Sie die 21 Auslassventile, 19 Auslassventilfedern und schrauben Sie die 22 Auslassventilstopfen in den Kopf.
- – Setzen Sie den Passfederstift ein und drücken Sie auf die Antriebsscheibe. Sichern Sie die Riemenscheibe mit einer Mutter und einem Splint.
- – Testen Sie den Kompressor.
Testen des Kompressors
Der Test wird auf einem speziellen Prüfstand bei einer Kurbelwellendrehzahl von 1200–1350 U/min und einem Öldruck im Schmiersystem von 118–245 kPa durchgeführt. Die Öltemperatur sollte mindestens 50 °C betragen.
Wenn der Kompressor 4–5 Minuten im Leerlauf läuft, prüfen Sie durch Berühren und Hören:
- – Erwärmung der Lager;
- – Geräusche der Lager;
- – Klopfen der Kolben (kein Klopfen);
- – Klopfen der Finger (kein Klopfen);
- – Ölleck (kein Leck).
Nach der Prüfung den Kompressor am Motor montieren und die relative Position der Lüfter- und Kompressorriemenscheibennuten einstellen. Mit Unterlegscheiben einstellen.
Spannung des Kompressorantriebsriemens einstellen.
Seit 1999 wird auch ein Kompressor mit einer Leistung von 270 l/min bei 2000 U/min Kurbelwellendrehzahl verbaut, der sich im Ventilsystem unterscheidet.
Besonderheiten des Kompressors
- – Fehlen von Auslassventilstopfen und Vorhandensein einer Abdeckung im Zylinderkopf.
Demontage, technische Zustandsprüfung, Montage und Prüfung sind ähnlich wie beim Kompressor mit einer Leistung von 201 l/min, mit Ausnahme einer geringfügig anderen Reihenfolge beim Aus- und Einbau des Ventilblockkopfes.