Montagevorgang für den ZMZ-402-Motor
- - Reinigen Sie alle Passflächen des Blocks von festsitzenden und gerissenen Dichtungen bei der Demontage;
- - Befestigen Sie den Zylinderblock auf einem Ständer, schrauben Sie die Ölkanalstopfen vorne und hinten ab und blasen Sie alle Ölkanäle mit Druckluft aus
Schrauben Sie die Stopfen fest.
Wenn das Kupplungsgehäuse ausgetauscht oder nach der Reparatur am Block montiert werden muss, müssen zuerst zwei Befestigungsstifte vom Block entfernt und dann das Gehäuse mit Schrauben am Block befestigt werden.
Im Block ist auf den Außenlagern eine Kurbelwelle eingebaut, an deren Flansch der Blinkerständer befestigt ist.
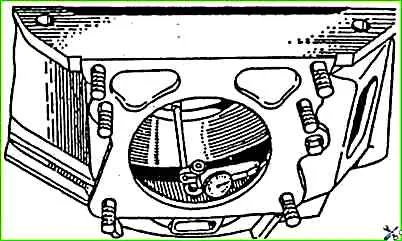
Überprüfen Sie beim Drehen der Kurbelwelle den Rundlauf des Lochs für den Zentrierring des Getriebes sowie die Rechtwinkligkeit des hinteren Endes des Kupplungsgehäuses relativ zur Achse der Kurbelwelle, wie in der Abbildung gezeigt.
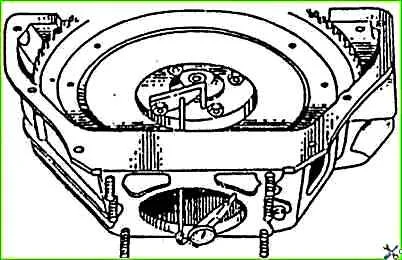
Der Rundlauf des Kurbelgehäuselochs und des Endes sollte 0,3 mm nicht überschreiten, das Ende - 015 mm.
Wenn der Lochschlag den angegebenen Wert überschreitet, lösen Sie die Schrauben und schlagen Sie leicht auf den Kurbelgehäuseflansch, um dessen korrekten Einbau sicherzustellen.
Nach dem Anziehen der Schrauben werden die Löcher für die Passstifte im Kurbelgehäuse und im Block auf Reparaturmaß aufgebohrt.
Schwärze in Löchern ist nicht erlaubt. Anschließend werden Stifte in die Löcher gedrückt, deren Durchmesser 0015–0051 mm größer ist als die Größe der Löcher.
Unrundheit am Kurbelgehäuseende wird durch Schaben beseitigt.
Es ist zu beachten, dass bei der Überprüfung der oben genannten Punkte eine ungetragene Kurbelwelle und Lager verwendet werden müssen, die nach dem Austausch des Kurbelgehäuses entfernt werden müssen.
- Ersetzen Sie defekte Zylinderlaufbuchsen wie folgt durch neue:
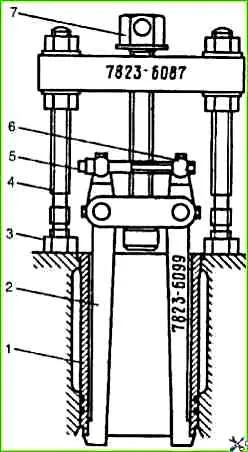
- a) Drücken Sie mit einem Kombi-Abzieher die alte Hülse heraus.
Nachdem Sie die Abzieherbeine in den Motorzylinder eingesetzt haben, sollten Sie die Stifte 4 am Block anlegen und die Beine mit einer Spreizschraube 5 auseinanderdrücken. Anschließend durch Drehen der Schraube 7 die Laufbuchse aus dem Zylinder drücken;
- - b) Reinigen Sie die Sitzflächen und Dichtflächen an der Hülse und dem Block gründlich von Zunder und Korrosion;
- - c) Setzen Sie die reparierte Laufbuchse mit einer weichen Kupferdichtung in den Zylinder ein, aus dem sie entfernt wurde.
Die Hülse sollte frei und ohne Kraftaufwand in den Zylinder eindringen und 002–010 mm über die Blockebene hinausragen.
Es ist bequemer, zunächst die Tiefe der Aussparung der Laufbuchse im Zylinder ohne Dichtung zu prüfen. Die Einsenkung sollte innerhalb von 020-025 mm liegen;
- - d) Sichern Sie die Hülse mit einer Halterung, damit sie nicht herausfällt;
- - Schneiden Sie zwei Dichtungen der hinteren Kurbelwellendichtung aus dem Kabel (jeweils 120 mm lang) und platzieren Sie sie im Block und Halter;
- - Führen Sie die Untermontage der Kurbelwelle durch. Schrauben Sie dazu alle Stopfen der Schmutzfänger der Pleuelzapfen ab und entfernen Sie Ablagerungen von ihnen.
Spülen und blasen Sie die Ölkanäle und Hohlräume der Schmutzfänger mit Druckluft aus, ziehen Sie die Stopfen mit einem Drehmoment von 38–42 Nm (38–4,2 kgcm) fest;
- Überprüfen Sie den Zustand der Arbeitsflächen der Kurbelwelle.
Nacks, Grate und andere äußere Mängel sind nicht erlaubt;
- - Kugellager 80203 AC9 mit zwei Schutzscheiben in das hintere Ende der Kurbelwelle einpressen. Es ist erlaubt, ein 60203A-Lager mit einer Schutzscheibe zu verwenden, und 20 g Litol-24-Schmiermittel müssen in den Lagerhohlraum gegeben werden
- - Schrauben Sie das Schwungrad an die Kurbelwelle. Ziehen Sie die Muttern mit einem Drehmoment von 76–83 Nm (7,6–8,3 kgcm) an.
Sichern Sie die Muttern, indem Sie einen der Schnurrhaare der Sicherungsplatte auf die Kante der Mutter biegen.
- Schrauben Sie die Kupplungsdruckplattenbaugruppe mit dem Gehäuse an das Schwungrad, nachdem Sie zuvor die angetriebene Scheibe mit einem Dorn (Sie können die Eingangswelle des Getriebes verwenden) entlang des Lochs im Lager am hinteren Ende der Kurbelwelle zentriert haben .
Die auf dem Druckplattengehäuse und auf dem Schwungrad in der Nähe eines der Löcher für die Gehäusebefestigungsschrauben eingestanzten Markierungen müssen ausgerichtet sein.
Ziehen Sie die Schrauben mit einem Drehmoment von 20–25 Nm (2,0–2,5 kgcm) an.
- Kurbelwelle, Maho Das Opfer und die Kupplung werden als Baugruppe ausgewuchtet. Daher sollte beim Austausch eines dieser Teile ein dynamisches Auswuchten durch Herausbohren von Metall aus dem Schwungrad durchgeführt werden.
Mit dem Auswuchten der Kurbelwelle, des Schwungrads und der Kupplungsbaugruppe sollte nicht begonnen werden, wenn die anfängliche Unwucht 200 g/m² übersteigt.
In diesem Fall ist es notwendig, das Gerät zu zerlegen und die Auswuchtung jedes Teils einzeln zu überprüfen
- Platzieren Sie die hintere Drucklagerscheibe auf dem ersten Hauptzapfen der Kurbelwelle mit einer Gleitschicht zur Kurbelwellenwange;
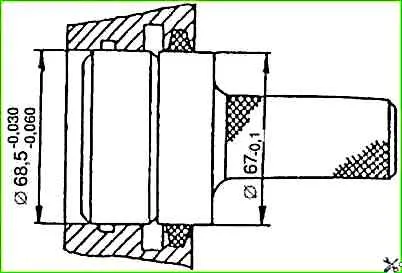
- - Drücken Sie die Dichtungspackung der hinteren Kurbelwelle mit einem Dorn in den Block und Halter.
- - Wischen Sie die Hauptlagerschalen und ihre Lager mit einem sauberen Tuch ab. Installieren Sie Einlagen im Bett;
- - Schmieren Sie die Hauptlagerschalen und den Kurbelwellenzapfen mit sauberem Motoröl und setzen Sie die Kurbelwelle in den Zylinderblock ein;
- - Setzen Sie die Hauptlagerdeckel so auf die Blockbolzen, dass sich die Verriegelungsnasen an der oberen und unteren Laufbuchse jedes Deckels auf einer Seite befinden und die auf den Deckeln eingeprägten Nummern den Bettnummern entsprechen.
Beim Einbau des vorderen Hauptlagerdeckels muss das Ende der hinteren Unterlegscheibe in die Nut des Deckels passen.
Das Ende des vorderen Lagerdeckels muss in derselben Ebene wie das Ende des Zylinderblocks liegen;
- - Bringen Sie die Hauptlagerdeckel an, indem Sie leicht mit einem Gummihammer darauf klopfen. Die Deckel sollten in die Nuten der Zylinderblockbetten passen;
- - Setzen Sie Unterlegscheiben auf die Stehbolzen, ziehen Sie die Muttern fest, tragen Sie 2-3 Tropfen (006 g) Unigerm-9-Dichtmittel auf den Gewindeteil der Muttern auf und ziehen Sie die Muttern gleichmäßig fest.
Das endgültige Anziehen muss mit einem Drehmomentschlüssel mit einem Drehmoment von 100–110 Nm (10–11 kg/cm) erfolgen.
Wenn kein Dichtmittel vorhanden ist, können die Muttern mit der Sicherungsplatte 24-1005301-01 gesichert werden;
- Setzen Sie die Gummidichtungen in die Nuten des Packungshalters ein und bestreichen Sie die aus der Nut herausragenden Seitenflächen mit Seifenwasser.
Platzieren Sie den Halter und ziehen Sie die Muttern fest;
- Drehen Sie die Kurbelwelle, die sich mit geringem Kraftaufwand frei drehen sollte.
Sie können die Kurbelwelle mit dem Schwungrad oder mit einer Vorrichtung drehen, die aus der Eingangswelle des Getriebes mit einem daran angeschweißten Tetraederschlüssel oder einem Griff mit quadratischem Loch besteht.
Das Gerät kann auch zum Zentrieren beim Einbau der Kupplungsscheibe verwendet werden;
- - Platzieren Sie die vordere Unterlegscheibe des Axiallagers mit der Gleitschicht nach außen, sodass die in den Block und die Abdeckung gedrückten Stifte in die Nuten der Unterlegscheibe passen;
- - Setzen Sie die Stahldruckscheibe der Kurbelwelle mit einer Fase im Innenloch in Richtung der vorderen Scheibe des Drucklagers auf;
- - Drücken Sie das Kurbelwellenrad ganz durch und prüfen Sie das Axialspiel.
Die Prüfung wird wie folgt durchgeführt: Platzieren Sie einen Schraubenzieher (Schraubenschlüssel, Hammerstiel usw.) zwischen der ersten Kurbel der Welle und der Vorderwand des Blocks und drücken Sie ihn als Hebel in Richtung der Welle Rückseite des Motors.
Bestimmen Sie mit einer Fühlerlehre den Spalt zwischen dem Ende der hinteren Unterlegscheibe des Drucklagers und der Ebene der Schulter des ersten Hauptlagerzapfens. Der Spalt sollte zwischen 0,125 und 0,325 mm liegen;
- Führen Sie die Untermontage der Pleuel- und Kolbengruppe durch
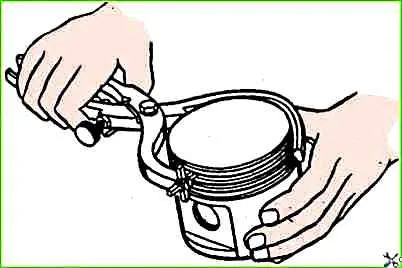
Reinigen Sie die Kolbenköpfe und Kolbenringnuten von Kohlenstoffablagerungen.
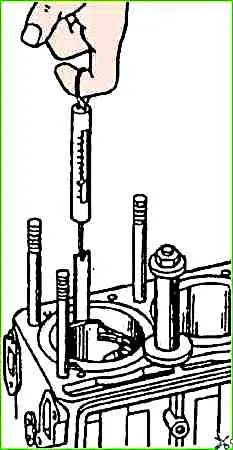
Im Falle des Austauschs von Kolben, Laufbuchsen, Kolbenbolzen oder Pleueln sollte die Untermontage der passenden Paare bei einer Temperatur der Teile (20 ± 3) °C erfolgen.
Bei gebohrten oder neuen Laufbuchsen müssen Kolben der gleichen Größengruppe wie die Laufbuchse eingebaut werden. Die Auswahl aus benachbarten Gruppen ist zulässig, und wie bei der Auswahl von Kolben in Arbeitsauskleidungen erfolgt die Auswahl auf der Grundlage der Zugkraft eines Sondenbandes mit einer Dicke von 0,05 mm und einer Breite von 10 mm.
Das Fühlerband wird in einer Ebene senkrecht zur Kolbenbolzenachse entlang des größten Durchmessers des Kolbens angebracht. Die Kraft auf das Dynamometer, das mit dem Sondenband verbunden ist, sollte 35–55 N (3,5–5,5 kgf) betragen.
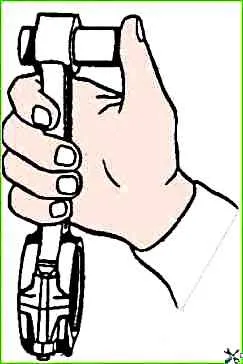
- Wählen Sie den Kolbenbolzen so an der Pleuelstange aus, dass er unter der Kraft des Daumens fest in das Pleuelloch passt, sich frei bewegt, ohne zu verklemmen und nicht unter dem Einfluss seines Eigengewichts herausfällt, wenn die Achse von Das Pleuelloch befindet sich in einem Winkel von ca. 45°.
Der Kolbenbolzen und die Pleuelstange müssen derselben oder einer benachbarten Größengruppe angehören.
Bei der Auswahl sollte der Kolbenbolzen leicht mit Motoröl geschmiert werden. Die Größengruppen von Kolben und Kolbenbolzen müssen übereinstimmen.
Der Kolben mit Kolbenbolzen, Kolbenringen und Pleuelstange muss gewichtsgesteuert sein. Der Gewichtsunterschied pro Motor sollte 12 g nicht überschreiten;
- Drücken Sie den Kolbenbolzen mit einem Werkzeug in den Kolben und die Pleuelstange.
Erwärmen Sie den Kolben auf eine Temperatur von 60–88 °C und schmieren Sie den Kolbenbolzen leicht mit Motoröl.
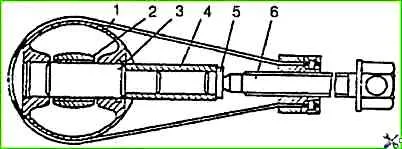
Verbinden Sie den Kolben mit einem Führungsdorn 3 mit der Pleuelstange, stecken Sie den Kolbenbolzen wie abgebildet auf das dünne Ende des Dorns, setzen Sie das Lager 5 auf den Bolzen und drücken Sie den Bolzen mit der Schraube 6 an seinen Platz.
Das Eindrücken eines Stifts in einen kalten Kolben kann zu einer Beschädigung der Oberfläche der Löcher in den Kolbennaben sowie zu einer Verformung des Kolbens selbst führen.
Beim Einsetzen des Kolbens in den Zylinder (an der Markierung „FRONT“ am Kolben) sollte das Loch zur Schmierung des Zylinderspiegels vom unteren Kopf der Pleuelstange in die entgegengesetzte Richtung zur Nockenwelle zeigen;
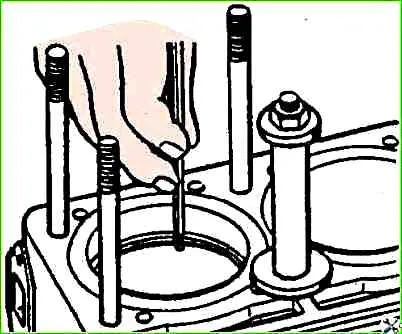
- Wählen Sie die Kolbenringe für den Zylinder aus, wie in der Abbildung gezeigt.
Der an den Verbindungsstellen der Ringe gemessene Spalt sollte bei Kompressionsringen 03–0,7 mm und bei Ölabstreifringscheiben aus Stahl 0,3–1,0 mm betragen.
Bei verschlissenen Zylindern beträgt der kleinste Spalt 0,3 mm;
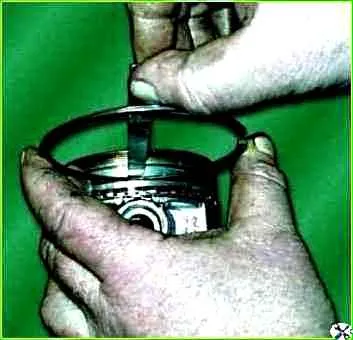
- Prüfen Sie mit einer Fühlerlehre den Spalt zwischen den Ringen und der Wand der Kolbennut, wie in der Abbildung gezeigt.
Überprüfen Sie den Umfang des Kolbens an mehreren Stellen.
Die Spaltgröße sollte im Bereich von 0,050–0,870 mm für den oberen und unteren Kompressionsring und 0,135–0,335 mm für den montierten Ölabstreifring liegen;
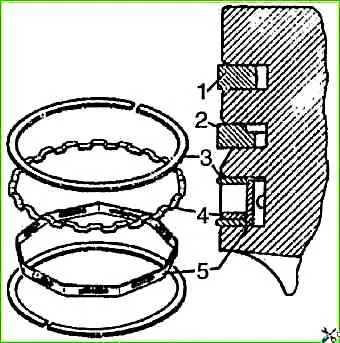
- Setzen Sie Sicherheitsmessingspitzen auf die Pleuelbolzen, drücken Sie die Ringe mit einer Crimpzange zusammen oder setzen Sie den Kolben mit einem konischen Ring in den Zylinder ein, wie in der Abbildung gezeigt.
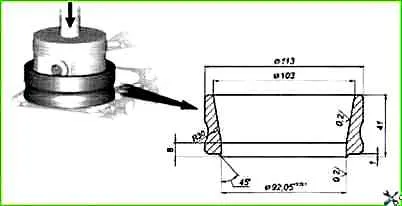
Vor dem Einbau des Kolbens sollten Sie noch einmal sicherstellen, dass die auf der Pleuelstange und deren Abdeckung eingestanzten Nummern mit der Seriennummer des Zylinders übereinstimmen, die korrekte Position des Kolbens und der Pleuelstange im Zylinder überprüfen;
- Ziehen Sie die Pleuelstange am unteren Kopf zum Pleuelzapfen, entfernen Sie die Messingspitzen von den Bolzen und setzen Sie die Pleuelstangenabdeckung auf.
Der Pleueldeckel sollte so montiert werden, dass die auf dem Deckel und dem Pleuel eingestanzten Zahlen in die gleiche Richtung zeigen.
Tragen Sie nach der Montage der Muttern 2-3 Tropfen (0,06 g) Unigerm-9-Dichtmittel auf den Gewindeteil der Muttern auf und ziehen Sie die Muttern gleichmäßig an.
Das endgültige Anziehen der Muttern muss mit einem Drehmomentschlüssel auf ein Drehmoment von 68–75 Nm (6,8–7,5 kg/cm) erfolgen.
Wenn gebrauchte Teile verwendet werden, ist es notwendig, die Reste des zuvor aufgetragenen Dichtmittels von den Muttern und Schrauben zu entfernen, sie mit Benzin zu entfetten und zu trocknen;
- - Setzen Sie den Kolben des vierten Zylinders in der gleichen Reihenfolge ein;
- - Drehen Sie die Kurbelwelle um 180° und setzen Sie die Kolben des zweiten und dritten Zylinders ein;
- - Drehen Sie die Kurbelwelle mehrmals, sie sollte sich leicht drehen lassen mit wenig Aufwand;
- - Bauen Sie die Nockenwelle in der folgenden Reihenfolge zusammen:
- - Platzieren Sie den Distanzring und den Druckflansch am vorderen Ende der Nockenwelle;
- - Drücken Sie das Nockenwellenrad mit dem Werkzeug auf und befestigen Sie es mit einer Schraube und einer Unterlegscheibe. Anzugsdrehmoment – 55–60 Nm (5,5–6,0 kg/cm);
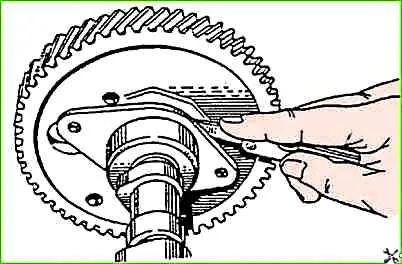
- - Stellen Sie das Axialspiel mit einer Fühlerlehre ein, die zwischen dem Nockenwellen-Druckflansch und der Zahnradnabe eingesetzt wird.
- - Reinigen Sie das Schmierrohr für die Steuerräder und schrauben Sie es mit einer Schraube und einer Klemme am Block fest. Nockenwelle. Der Spalt sollte innerhalb von 0,1–0,2 mm liegen;
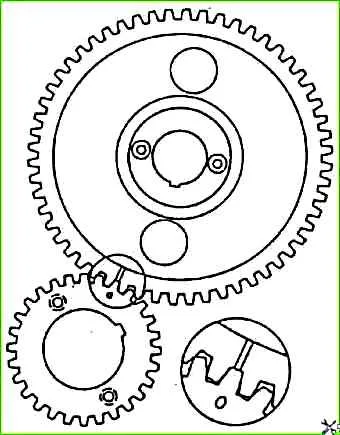
- Setzen Sie die zusammengebaute Nockenwelle in das Loch des Blocks ein, nachdem Sie zuvor ihre Lagerzapfen mit Motoröl geschmiert haben.
Wenn die Gänge eingelegt sind, muss der Zahn des Kurbelwellenzahnrads mit der Markierung „0“ in der Nut der Zähne des Nockenwellenzahnrads liegen.
Das seitliche Spiel im Eingriff sollte im Bereich von 0,025–0,1 mm liegen.
Wenn es einen größeren oder kleineren Spalt gibt, wählen Sie ein anderes Zahnradpaar;
- - Befestigen Sie den Druckflansch durch die Löcher im Nockenwellenrad mit zwei Schrauben und Federscheiben am Block;
- - Bringen Sie den Ölabweiser am Zapfen am vorderen Ende der Kurbelwelle an, wobei die konvexe Seite zum Zahnrad zeigt;
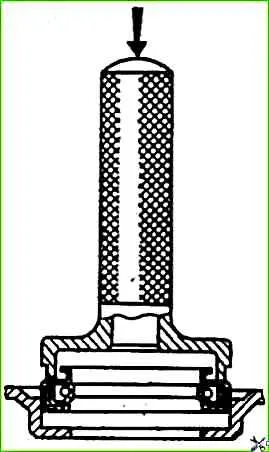
- Prüfen Sie die Eignung der in den Steuerraddeckel eingepressten Manschette für weitere Arbeiten.
Wenn die Manschette abgenutzte Arbeitskanten aufweist oder die in die Manschette eingesetzte Kurbelwellen-Riemenscheibennabe lose abdeckt, ersetzen Sie sie durch eine neue.
Es empfiehlt sich, die Manschette mit einem Dorn in den Bezug zu drücken, wie in der Abbildung dargestellt.
- Setzen Sie die Steuerradabdeckung auf die Bolzen der Dichtung;
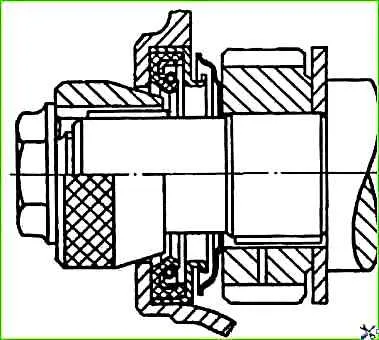
- Zentrieren Sie die Abdeckung mit einem Dorn am vorderen Ende der Kurbelwelle und ziehen Sie alle Muttern und Schrauben fest, mit denen die Abdeckung befestigt ist.
Wenn kein Zentrierdorn vorhanden ist, kann die Abdeckung entlang der Kurbelwellenriemenscheibennabe installiert werden.
Die Nabe muss so auf die Kurbelwelle gedrückt werden, dass ihr Ende 5 mm in das Loch im Deckel passt.
Befestigen Sie anschließend die Abdeckung mit Muttern und achten Sie dabei auf den gleichen Abstand um den Umfang zwischen der Nabe und dem Abdeckungsloch.
Der Spalt sollte durch leichte Schläge mit einem Holz- oder Gummihammer auf die Abdeckung ausgeglichen werden. Befestigen Sie anschließend die Abdeckung endgültig;
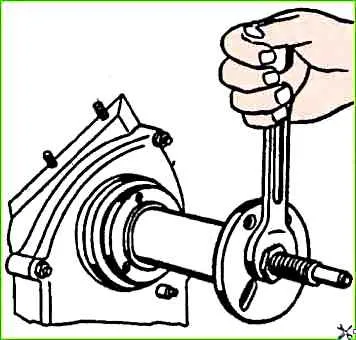
- - Entfernen Sie den Zentrierdorn und drücken Sie die Riemenscheibennabe mit der Kurbelwellen-Dämpferriemenscheibe
- - Setzen Sie einen Gummistopfen in die Keilnut ein und drücken Sie den Schlüssel hinein;
- - Schrauben Sie die Klemmschraube in die Spitze der Kurbelwelle, nachdem Sie eine Zahnscheibe darauf gelegt haben.
Prüfen Sie beim Drehen der Kurbelwelle mit der Kupplungsschraube, ob die Dämpferscheibe den Nockenwellendeckel berührt; - Installieren Sie die Ölpumpenbaugruppe mit dem Ölbehälter;
- - Installieren Sie den Ölpumpenantrieb und den Zündverteilersensor in der folgenden Reihenfolge:
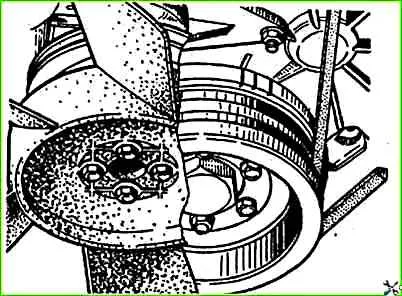
- Drehen Sie die Kurbelwelle und richten Sie die dritte Markierung auf der Dämpferscheibe mit der Markierungsrippe am Nockenwellendeckel aus.
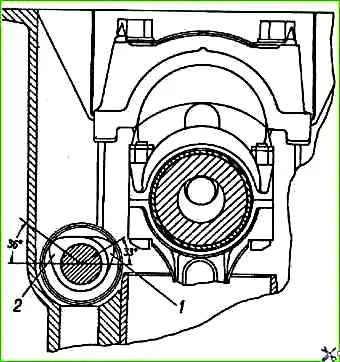
Die Nockenwellen, die die Ventile des ersten Zylinders betätigen, müssen mit ihren Scheitelpunkten in die entgegengesetzte Richtung zu den Stößeln (in Richtung Ölwanne) gerichtet und symmetrisch angeordnet sein
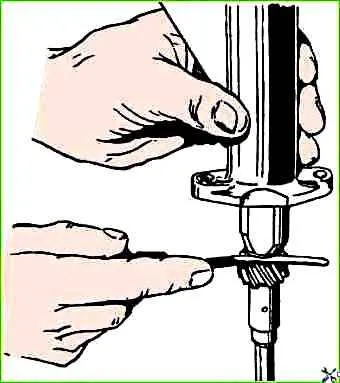
- - Prüfen Sie das Axialspiel zwischen Antriebsgehäuse und Zahnrad mit einer Fühlerlehre
- - Bringen Sie eine Dichtung an den Befestigungsbolzen des Antriebs an. Der Spalt sollte zwischen 0,15 und 0,40 mm liegen;
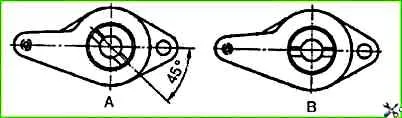
- Drehen Sie die Antriebswelle in die in „A“ gezeigte Position und setzen Sie den Antrieb in den Blocksockel ein.
Beim Einsetzen des Antriebs in die Buchse ist es notwendig, die Ölpumpenwelle leicht zu drehen, damit das Ende der Antriebswelle in das Loch in der Pumpenwelle eindringt.
Das Einsetzen des Laufwerks sollte ohne nennenswerten Kraftaufwand erfolgen.
Bei einem korrekt installierten Antrieb sollte der Schlitz in der Wellenbuchse parallel zur Achse des Motors und vom Motor versetzt sein, wie in „B“ gezeigt;
- Sichern Sie das Laufwerk;
- - auf Spiel in der Nockenwelle und den Antriebsrädern prüfen;
- - Schmieren Sie die Verbindungen des unteren Flansches des Zylinderblocks mit der Steuerradabdeckung und dem Packungshalter mit Klebstoff-Dichtmittel „Elastosil 1Z7-8Z“ oder UN-25-Paste;
- - Installieren Sie die Ölwannendichtung am unteren Flansch des Zylinderblocks;
- - Montieren Sie die Ölwanne auf den Stehbolzen, befestigen Sie sie mit Muttern und Unterlegscheiben und ziehen Sie die Muttern gleichmäßig an;
- - Installieren und verschrauben Sie den unteren Teil des Kupplungsgehäuses;
- - Reinigen Sie die Brennräume und Zylinderkopfkanäle von Ruß und Ablagerungen, wischen Sie sie ab und blasen Sie sie mit Druckluft aus;
- - Läppen Sie die Ventile mit einer Läpppaste, die aus einem Teil M-20-Mikropulver und zwei Teilen I-20A-Öl besteht.
Bevor Sie mit dem Schleifen beginnen, sollten Sie prüfen, ob sich die Ventilplatte verzieht und ob Ventil und Sitz durchgebrannt sind.
Wenn diese Mängel vorhanden sind, ist es nicht möglich, die Dichtheit des Ventils allein durch Schleifen wiederherzustellen und es muss zuerst der Sitz geschliffen und das beschädigte Ventil durch ein neues ersetzt werden.
Wenn der Spalt zwischen Ventil und Buchse 0,25 mm überschreitet, kann die Dichtheit ebenfalls nicht wiederhergestellt werden. In diesem Fall sollten Ventil und Buchse durch neue ersetzt werden.
Ventile (für Ersatzteile) werden in Standardgröße und Führungsbuchsen mit einem um 0,38 mm reduzierten Innendurchmesser hergestellt (um sie nach dem Einpressen in den Zylinderkopf auf die endgültige Größe zu reiben).
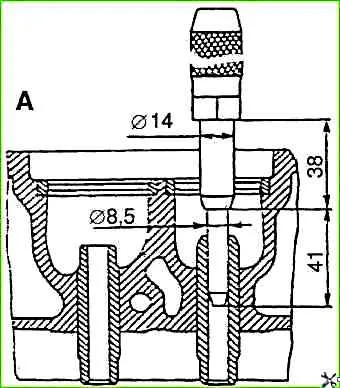
Die verschlissene Führungsbuchse wird mit einem Dorn herausgedrückt.
Ventilsitze werden durch Fräsen mit einem Hartmetall-Senker entfernt.
Reparatursitze haben einen um 0,25 mm größeren Außendurchmesser als Standardsitze, daher sind die Sitzbuchsen auf folgende Maße aufgebohrt: für den Einlassventilsitz – 49,25+0,025 mm, für das Auslassventil – 42,25+0,025 mm.
Vor dem Zusammenbau müssen die Führungsbuchsensitze in Kohlendioxid (Trockeneis) abgekühlt und der Zylinderkopf auf eine Temperatur von 160–175 °C erwärmt werden.
Beim Zusammenbau sollten Sitze und Buchsen frei oder mit leichtem Kraftaufwand in die Zylinderkopfaufnahmen eingeführt werden.
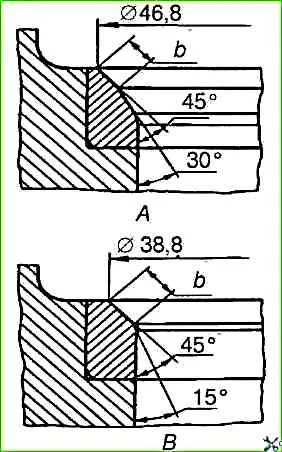
Das Einpressen neuer Buchsen für die Einlass- und Auslassventile erfolgt so lange, bis diese 20 mm über den Kopf hinausragen. Nach dem Einpressen werden die Löcher der Buchsen auf einen Durchmesser von 9+0,022 mm erweitert und die Sitzfasen geschliffen, zentriert sie entlang des Lochs in der Buchse.
Stellen Sie beim Schleifen sicher, dass die Fase am Ventilsitz innerhalb von 0,05 mm konzentrisch zum Loch in der Buchse ist. Die Fasen sind im 45°-Winkel geschliffen.
Außendurchmesser abschrägen Der Sitz für das Einlassventil sollte 46,8 mm und für das Auslassventil 38,8 mm betragen.
Die Breite der Fase sollte am Einlassventilsitz 1,8–2,3 mm und am Auslassventilsitz 2,3–2,5 mm betragen.
Die Breite der Fase wird durch Schleifen der Einlassventilsitzbohrung in einem Winkel von 30°, wie in „A“ gezeigt, und des Auslassventils in einem Winkel von 15°, wie in „B“ gezeigt, erreicht. Die Fase sollte über den gesamten Umfang gleich sein.
Nach dem Schleifen der Sitze und Schleifen der Ventile alle Gaskanäle gründlich reinigen und mit Druckluft ausblasen, damit kein Schleifstaub zurückbleibt;
- - Beschichten Sie die Ventilschäfte mit einer dünnen Schicht kolloidalem Graphit, verdünnt in Motoröl, oder schmieren Sie sie mit Öl
- - Drücken Sie die Öldichtungen auf die Ventilführungsbuchsen, setzen Sie die Ventile gemäß den Markierungen in die Buchsen ein und montieren Sie sie mit den Federn. Stellen Sie sicher, dass die Cracker in die Ringnut der Ventile passen;
- Reiben Sie Graphitpulver auf beide Seiten der Zylinderkopfdichtung und geben Sie es auf die Stehbolzen.
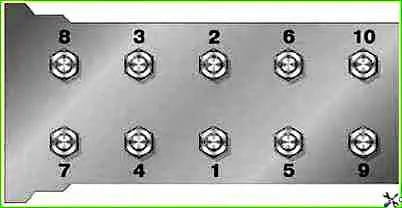
Setzen Sie den Kopf ein und sichern Sie ihn mit Muttern und Unterlegscheiben. Ziehen Sie die Muttern mit einem Drehmomentschlüssel mit einem Drehmoment von 83–90 Nm (8,3–9,0 kg/cm) an, um die Ordnung aufrechtzuerhalten
- Reinigen Sie die Löcher in den Kipphebeln, in der Kipphebelachse und den Einstellschrauben, im vierten Hauptpfosten der Kipphebelachse und in den Ölkanälen im Zylinderkopf mit Draht und blasen Sie sie mit Druckluft aus.
Überprüfen Sie den festen Sitz der Kipphebelbuchsen.
Wenn der Sitz während des Betriebs locker ist, kann sich die Buchse bewegen und das Schmierloch der Ventilstößelstange blockieren. Solche Buchsen müssen ersetzt werden;
- Montieren Sie die Kipphebelachse.
Bevor Sie jeden Kipphebel einbauen, schmieren Sie dessen Buchse mit Motoröl;
- - Führen Sie die Drücker entsprechend der Markierungen in die Buchsen ein. Schmieren Sie die Drücker und Löcher im Block vorab mit Motoröl;
- - Setzen Sie die Stangenbaugruppe mit den Spitzen in die Löcher im Zylinderkopf ein;
- - Montieren Sie die zusammengebaute Kipphebelachse auf den Stehbolzen und befestigen Sie sie mit Muttern und Unterlegscheiben. Die Einstellbolzen sollten mit ihrem kugelförmigen Teil auf der Kugel der oberen Stangenspitze aufliegen;
- - Stellen Sie die Abstände zwischen den Enden der Ventilschäfte und den Spitzen der Kipphebel ein. Der Spalt zwischen den Kipphebeln und dem ersten und achten Ventil beträgt 0,35–0,40 mm, der Spalt zwischen den übrigen Kipphebeln und Ventilen beträgt 0,40–0,45 mm.
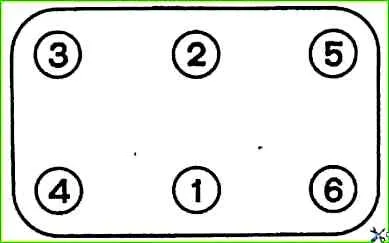
- - Installieren Sie die Dichtung und den Ventildeckel und befestigen Sie sie mit Schrauben und Unterlegscheiben. Achten Sie dabei auf den korrekten Anzug, wie in der Abbildung dargestellt.
- - Schmieren Sie die Ausrückkupplung und setzen Sie sie auf die vordere Abdeckung des Getriebes.
- - Getriebe einbauen und sichern;
- - Kupplungsausrückgabel einbauen;
- - Motorteile und Baugruppen einbauen