Die hydraulischen Drücker der ZMZ-406- und ZMZ-405-Motoren, die in Form von zylindrischen Drückern hergestellt sind und sich zwischen der Nockenwelle und den Ventilen befinden, vereinen zwei Funktionen: Kraftübertragung von der Nockenwelle auf die Ventile und Beseitigung von Lücken in ihrem Laufwerk.
Der Betrieb des hydraulischen Stößels basiert auf dem Prinzip der Inkompressibilität des Motoröls, das während des Motorbetriebs ständig den inneren Hohlraum des hydraulischen Stößels füllt und seinen Stößel bewegt, wenn im Ventiltrieb ein Spalt entsteht.
Dadurch ist ein konstanter und spielfreier Kontakt des Stößels (Ventilantriebshebels) mit dem Nockenwellennocken gewährleistet.
Das bedeutet, dass die Ventile während der Wartung nicht angepasst werden müssen.
Das Funktionsprinzip des hydraulischen Schiebers ist in der Abbildung dargestellt.
Öl unter dem Druck, der für den Betrieb des hydraulischen Drückers erforderlich ist, wird seinen inneren Hohlräumen „A“ und „B“ vom Kanal „B“ des Motorschmiersystems durch ein seitliches Loch im Drücker 6 zugeführt ringförmige Nut seiner zylindrischen Oberfläche.
Wenn Ventil 1 geschlossen ist, werden Drücker 6 (durch Kolben 7) und Hülse 9 durch die Expansionskraft der Feder 8 gegen den Nockenwellennocken 5 bzw. das Ende des Ventilschafts gedrückt.
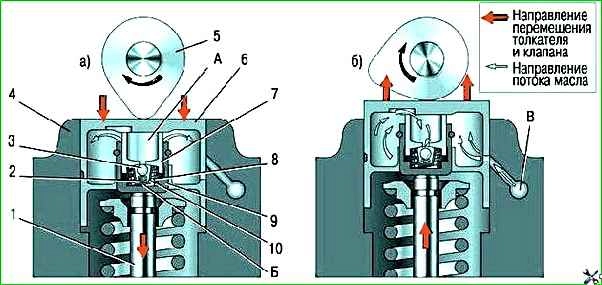
Der Druck in den Hohlräumen „A“ und „B“ ist gleich, das Rückschlagventil 3 des hydraulischen Kompensators wird durch die Feder 2 an den Sitz im Kolben 7 gedrückt – es gibt keine Lücken im Ventilmechanismus.
Wenn sich die Nockenwelle dreht, läuft der Nocken 5 in den Stößel 6 und bewegt ihn und den damit verbundenen Stößel 7.
Die Bewegung des Kolbens 7 in der Hülse 9 führt zu einem starken Druckanstieg im Hohlraum „B“.
Trotz kleiner Öllecks durch den Spalt zwischen Kolben und Hülse bewegen sich Stößel 6 und Hülse 9 als ein Stück und öffnen Ventil 1.
Bei weiterer Drehung der Nockenwelle reduziert Nocken 5 den Druck auf Stößel 6 und der Öldruck in Hohlraum „B“ wird niedriger als in Hohlraum „A“.
Rückschlagventil 3 öffnet sich und lässt Öl aus Hohlraum „A“, der mit der Motorölleitung verbunden ist, in Hohlraum „B“ fließen.
Der Druck im Hohlraum „B“ steigt, Hülse 9 und Kolben 7 bewegen sich relativ zueinander und bilden einen Spalt im Ventilmechanismus.
Der den Hydrostößeln zugeführte Öldruck wird durch ein spezielles Ventil reguliert, das im Zylinderkopf installiert ist.
Da nach dem Abstellen des Motors Öl aus den von der Ölpumpe kommenden Kanälen in den Ölsumpf fließt und die Ölversorgungskanäle zu den Hydrostößeln gefüllt bleiben, kann es nach dem Starten des Motors zur Bildung von Luftstopfen in den Hohlräumen des Motors kommen Letzteres.
Um sie zu beseitigen, sind in den Motorölversorgungskanälen kalibrierte Ausgleichslöcher vorgesehen, die eine automatische Spülung der Hohlräume der hydraulischen Stößel gewährleisten.
Darüber hinaus ermöglichen Ausgleichsbohrungen eine leichte Reduzierung des Öldrucks, der bei hohen Motordrehzahlen in die Hydrostößel gelangt, wenn der Druck im Hohlraum des Hydrostößels so hoch werden kann, dass sein Stößel auf der Rückseite des Stößels aufliegt Nockenwellennocken, öffnet das Ventil im Moment leicht, was nicht der Ventilsteuerung entspricht.
Fast alle Störungen hydraulischer Drücker werden anhand des charakteristischen Geräusches diagnostiziert, das der Gasverteilungsmechanismus bei verschiedenen Motorbetriebsarten aussendet.
Ventilgeräusche können manchmal durch leichtes Drehen der Feder oder des Ventils um die Längsachse beseitigt werden.
Gehen Sie dazu wie folgt vor.
- 1. Drehen Sie die Kurbelwelle in eine Position, in der sich das Ventil, das das Geräusch erzeugt, leicht zu öffnen beginnt.
- 2. Drehen Sie die Feder ein wenig und das Ventil dreht sich gleichzeitig.
- 3. Den Motor starten. Wenn das Geräusch weiterhin besteht, wiederholen Sie die Schritte 1 und 2.
- 4. Wenn das Drehen der Feder und des Ventils nicht zum gewünschten Ergebnis führt, überprüfen Sie den Zustand der Feder und messen Sie die Lücken zwischen den Ventilschäften und Führungsbuchsen (siehe Reparatur des Zylinderkopfs ZMZ-406 GAZ-3110). Beseitigen Sie größere Lücken (im Vergleich zum Nennwert).
Wenn Ventil und Feder in gutem Zustand sind und das Klopfen der Ventile bei laufendem Motor immer noch zu hören ist, ist der Hydrostößel defekt. Ersetzen Sie es wie folgt.
- - Trennen Sie das Kabel von nach Minuspolen der Batterie.
- - Entfernen Sie die Nockenwellen von den Zylinderkopfstützen (siehe Nockenwellen ZMZ-406 GAZ-3110).
Es ist bequemer, den hydraulischen Drücker mit einem starken Magneten oder Saugnapf zu entfernen.
Legen Sie den neuen Hydrostößel vor dem Einbau in einen Behälter mit Motoröl, drücken Sie mehrmals auf die Hydrostößelhülse, um Luft zu entfernen, und füllen Sie ihn mit Öl.
Entfernen Sie den Hydrostößel aus dem Zylinderkopfsockel.
Schmieren Sie die Buchse im Zylinderkopf mit Motoröl und installieren Sie den hydraulischen Drücker in der Buchse.
Die restlichen hydraulischen Stößel werden auf die gleiche Weise ausgetauscht.
Bauen Sie die Nockenwellen- und Steuerradantriebsteile in umgekehrter Reihenfolge wie beim Ausbau ein.
Nach dem Starten eines kalten Motors kann es zu einem Klopfgeräusch der Ventilstößel kommen, das verschwinden sollte, wenn der Motor auf eine Kühlmitteltemperatur von plus 80...90 °C erwärmt wird.
Wenn das Klopfgeräusch nicht mehr als 30 Minuten nach Erreichen der angegebenen Temperatur verschwindet, muss die Funktionsfähigkeit der hydraulischen Drücker wie folgt überprüft werden.
Ein Klopfen, das beim Starten eines kalten Motors, bei wiederholtem Starten des Motors (mit mehreren erfolglosen Starts), beim Starten des Motors nach längerem Stehen und anschließendem Verschwinden beim Warmlaufen des Motors auftritt, ist keine Fehlfunktion des hydraulischen Stößels.
Dieses Klopfgeräusch der hydraulischen Drücker wird durch das Ansaugen von Luft in die Kammer des hydraulischen Kompensators des hydraulischen Drückers verursacht, was zu einem Verlust seiner Steifigkeit und einem stoßartigen Betrieb des Ventilantriebs führt.
Um Luft zu entfernen, wird empfohlen, die folgenden Schritte durchzuführen:
– Starten Sie den Motor und erwärmen Sie ihn auf Betriebstemperatur.
Stellen Sie den Motorbetriebsmodus für 3–4 Minuten auf eine konstante Drehzahl von 2500 U/min oder auf einen variierenden Drehzahlbereich von 2000–3000 U/min ein und hören Sie dann zu, wie der Motor 15–30 Sekunden lang im Leerlauf läuft.
In 90 % der Fälle sollte das Klopfen aufhören
- - Wenn das Klopfen nicht aufhört, wiederholen Sie den Zyklus bis zu fünf Mal;
- - Wenn das Klopfen nach der oben genannten Arbeit nicht aufhört, arbeiten Sie weitere 15 Minuten bei einer Drehzahl von 2000...3000 U/min und hören Sie dann zu, wie der Motor 15...30 Sekunden lang im Leerlauf läuft.
Wenn das Klopfen nach 5 Zyklen plus 15 Minuten Motorbetrieb nicht verschwindet, müssen folgende Arbeiten durchgeführt werden:
- - Verwendung eines Stethoskops (oder eines anderen Geräts, das den Ton verstärkt), um die Klopfquelle zu lokalisieren;
- - Entfernen Sie die Ventilabdeckung;
- - Drehen Sie die Nockenwellen langsam, stellen Sie alle Hydrostößel nacheinander auf die Position „Ventil vollständig geschlossen“ und überprüfen Sie sie in dieser Position, indem Sie auf das Arbeitsende entlang der Bewegungsachse Kraft ausüben:
- a) elastische Elastizität bei kurzzeitiger Anwendung einer Kraft von etwa 10 N (1 kgf) weist auf das Vorhandensein von Luft in der Hochdruckkammer des Kompensators hin;
- b) das Auftreten eines Spalts zwischen dem Arbeitsende des hydraulischen Drückers und der Nocke, wenn eine Last von etwa 20...30 N (2-3 kgf) für 10...15 Sekunden ausgeübt wird und danach verschwindet Die Last wird entfernt, was auf ein Leck im Rückschlagventil des Kompensators oder auf Verschleiß des Kolbenpaars des hydraulischen Kompensators hinweist;
- c) Das Vorhandensein eines Spalts zwischen dem Arbeitsende und dem Nockenwellennocken weist auf eine Verkeilung des Kompensators hin
Ersetzen Sie die Hydraulikstößel bei den oben genannten Symptomen.
Falls die aufgeführten Kommentare fehlen, entfernen Sie alle Hydrostößel aus den Zylinderkopfbuchsen und überprüfen Sie das Aussehen der Hydrostößel und Nockenwellennocken auf grobe Kratzer, Risse, Verschleißerscheinungen, Fremdkörper und Verunreinigungen.
Überprüfen Sie die Ölversorgung der Hydrostößel, den Einlauf am Ende des Hydrostößels und die Drehung im Sitz. Teile, die schwerwiegende Mängel aufweisen, müssen ersetzt werden.
Überprüfen Sie den Zug der Ventilfedern unter Last (siehe Artikel „Reparatur des Zylinderkopfs des ZMZ-406 GAZ-3110“).
Ersetzen Sie die hydraulischen Drücker in den vom Stethoskop identifizierten Bereichen.
Mögliche Störungen
Erhöhtes Geräusch unmittelbar nach dem Starten des Motors
Ölleck aus einem Teil der Hydrostößel beim Parken – Geräusche, die einige Sekunden nach dem Starten des Motors verschwinden, sind kein Zeichen einer Fehlfunktion, da Öl aus einem Teil der Hydrostößel austrat, die unter der Last der Ventilfedern standen der offenen Ventile (die Ölversorgungskanäle blieben offen), deren Mangel zu Beginn des Motorbetriebs ausgeglichen wird
Intermittierende Geräusche im Leerlauf verschwinden mit zunehmender Kurbelwellendrehzahl
Beschädigung oder Verschleiß der Rückschlagventilkugel – Ersetzen Sie die hydraulischen Stößel
Verunreinigung des hydraulischen Schiebemechanismus durch Verschleißprodukte aufgrund nicht rechtzeitiger Wartung Ölmangel oder schlechte Qualität – Reinigen Sie die Teile des Mechanismus von Schmutz. Verwenden Sie das in der Bedienungsanleitung empfohlene Öl
Erhöhtes Geräusch im Leerlauf eines warmen Motors, verschwindet bei erhöhter Kurbelwellendrehzahl und fehlt bei kaltem Motor vollständig
Öl fließt durch den vergrößerten Spalt zwischen dem Kolben und der hydraulischen Drückerhülse – Ersetzen Sie den hydraulischen Kompensator
Erhöhtes Geräusch, das bei hohen Kurbelwellendrehzahlen auftritt und bei niedrigen Frequenzen verschwindet
Öl schäumt, wenn sich aufgrund der Bewegung der Kurbelwelle überschüssiges Öl (über der „P“-Markierung am Ölmessstab) im Ölsumpf befindet. Das Eindringen eines Luft-Schaum-Gemisches in den Hydrostößel stört dessen Funktion – Bringen Sie den Ölstand im Ölsumpf auf den Normalwert
Luftansaugung durch die Ölpumpe bei zu niedrigem Ölstand im Ölsumpf - Ölstand auf Normalniveau bringen
Beschädigung der Ölaufnahme durch Verformung der Ölwanne beim Auftreffen auf ein Straßenhindernis – Reparieren oder ersetzen Sie die defekten Teile
Dauergeräusch eines oder mehrerer Ventile, unabhängig von der Kurbelwellendrehzahl
Das Auftreten eines Spalts zwischen dem Stößel und dem Nockenwellennocken aufgrund einer Beschädigung des hydraulischen Kompensators. Nachdem Sie die Ventilmechanismusabdeckung entfernt haben, installieren Sie die Nockenwellennocken nacheinander mit den Vorsprüngen nach oben und prüfen Sie, ob dazwischen ein Spalt vorhanden ist die Drücker und die Nocken.
Vergleichen Sie die Geschwindigkeit seiner Bewegung mit der Geschwindigkeit der anderen, indem Sie (z. B. mit einem Holzkeil) auf den Drücker des zu testenden hydraulischen Kompensators drücken.
Wenn es eine Lücke oder eine erhöhte Bewegungsgeschwindigkeit gibt, ersetzen Sie den Kompensator.