Depending on the vehicle configuration, different schemes and options for auxiliary unit drives may be used
Belts may vary in size, since auxiliary units such as the power steering pump, generator, and air conditioning compressor may be from different manufacturers.
Therefore, before checking and replacing belts, you need to decide which option is right for you.
The size of the belts is indicated on the outside.
You need to buy belts according to their size. When replacing belts, be sure to check the condition of the tension and auxiliary rollers.
Be sure to carry spare belts with you, especially on long trips.
Let's consider some variants and technology for replacing belts.
You will need: 13 mm wrenches (two), a punch or a mounting blade.
Check the belt tension by deflecting the branch between the pulleys of the power steering pump and the crankshaft.
The belt should fit tightly to the pulley, but do not allow excessive belt tension to increase the load on the pump bearings.
Loosen the tightening of the pump mounting nut to the tension bar.
Using a punch or mounting blade, move the pump to the desired side and achieve the desired tension.
If it is necessary to replace the belt, move the pump towards the engine so that the pump pulley can be released and the belt replaced.
Pay attention to the crankshaft position sensor wire.
Do not damage it when moving the pump.
Tighten the pump mounting nut to the tension bar.
Two-belt option with a coolant pump drive belt, alternator, power steering and compressor drive belt
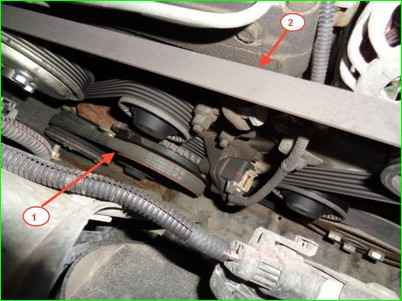
The work must be performed in an inspection pit or on a lift.
Prepare the car. Open the hood.
Remove the plastic engine protection (screen)
When the belts are loose or the auxiliary rollers are worn out, a characteristic "whistle" or noise appears when the engine is running in this area.
To check the tension of the auxiliary belt, press your finger on the belt in the middle between the generator pulley and the coolant pump.
When pressing with a force of about eight kilograms, the belt deflection should be 12 ± 1 mm.
To adjust the belt tension, remove the rubber air supply pipe to the throttle assembly.
Using a 13 mm socket, loosen the three nuts securing the tension roller bracket.
Photo 6 shows the location of the belts and nuts of the tension roller bracket.
Using a 13 mm wrench or head, turn the adjusting bolt clockwise, tightening the belt.
Tighten the tension roller mounting nuts. Start the engine, stop it after five minutes and check the belt tension.
Belts must not be overtightened, as the bearings of the units they rotate may fail due to excessive load.
Replace the auxiliary unit belts if cracks, tears or peeling rubber are detected.
First, remove the air conditioning compressor drive belt (see below).
After removing the air conditioning compressor drive belt, loosen the tension roller bracket mounting and rotate the adjusting bolt counterclockwise, loosening the belt tension.
Remove the belt from the tension roller and other pulleys. Install the new belt in the reverse order.
First, put the belt on the crankshaft pulley, and lastly on the tension roller.
After installation, adjust the belt tension.
Checking and removing the air conditioning compressor drive belt
To do this, remove the lower protection of the engine compartment and the mudguards of the engine compartment.
To simply check the tension of the air conditioning drive belt, press your finger on belt (Fig. 1) in the middle between the compressor and crankshaft pulleys.
When pressing force is about 10 kilograms, the belt deflection should be about 8 mm.
To adjust the belt tension, use a 13 head to loosen the two bolts securing the tension roller bracket.
Using a 13 mm head, turn the adjusting bolt clockwise, tightening the belt.
After tensioning the belt, tighten the tension roller bracket mounting bolts.
To remove the belt, loosen the tension roller bracket mounting bolts and loosen the belt tension by turning the adjusting bolt counterclockwise.
Remove the belt from the tension roller and the crankshaft and compressor pulleys.
Install the new belt in the reverse order.
Install the new belt in the reverse order.
Put the belt on the compressor pulley so that it located closer to the inner edge of the pulley.
And adjust the belt tension, as stated above.
After a short mileage of the car, it is necessary to check the belt tension.
New belts stretch a little, so it is better to check and tighten.
PS. And finally, after removing the belts, it is necessary to determine why the belt broke or was defective.
Increased belt wear occurs due to oil getting from under the seals or other mating surfaces of the engine.
Premature wear also occurs due to loosening of the belt tension.
In this case, the slippage of pulleys and excessive heating, and wear of both the belt itself and the unit pulley.
You should also pay attention to the pulleys themselves and the units that are driven by these belts.
The units that rotate with these belts should not jam due to bearing failure.
The pulleys should not have nicks or sharp edges.
Check the play of the generator rotors, coolant pump, air conditioning compressor and power steering pump by turning and shaking them by hand.
When buying belts, you should buy only from proven and reliable manufacturers. Inspect the belt, bend it and look at the quality of the product, the year of its manufacture.