The VAZ-21126 engine is based on the VAZ-2112 engine
Increasing engine displacement mod. 21126 up to 1.6 l compared to displacement mod. 2112 is achieved by increasing the piston stroke while keeping the cylinder diameter unchanged.
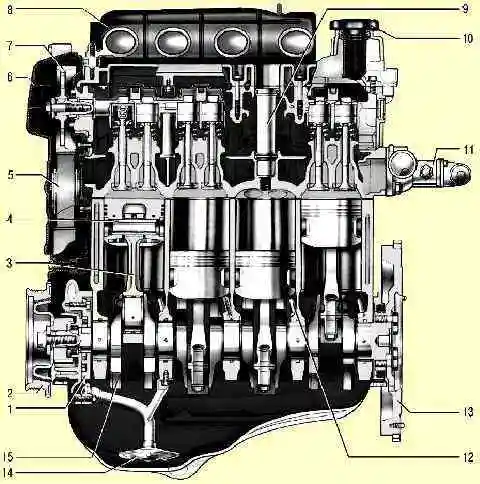
The cylinder block is cast from special high-strength cast iron, which gives the engine structure rigidity and strength.
The coolant ducts that form the cooling jacket are made along the entire height of the block, this improves the cooling of the pistons and reduces the deformation of the block from uneven overheating.
The cooling jacket is open at the top towards the block head.
At the bottom of the cylinder block there are five supports for the crankshaft main bearings, the covers of which are bolted.
The supports are equipped with thin-walled steel-aluminum liners that act as crankshaft bearings.
The middle support has grooves into which thrust half-rings are inserted to hold the crankshaft from axial movements.
Compared to engine cylinder block mod. 2112 cylinder block mod. 21126 is 2.3 mm higher, the height from the axis of the main bearing beds to the top surface of the block is 197.1 mm.
The crankshaft is cast from special high-strength cast iron.
The main and connecting rod journals of the shaft are ground.
To lubricate the connecting rod bearings, oil channels are drilled in the crankshaft and closed with plugs.
Eight counterweights located on the crankshaft are used to reduce vibration.
Crank radius of engine crankshaft mod. 21126 is 2.3 mm larger than the engine mod. 2112, due to which the piston stroke increased from 71 to 75.6 mm.
To distinguish the shafts, the marking “11183” is cast on one of the counterweights of the crankshaft of the VAZ-21126 engine.
At the front end of the crankshaft there is an oil pump, a timing belt pulley and a generator drive pulley with a built-in torsional vibration damper.
At the rear end of the crankshaft there is a flywheel cast from cast iron. A steel toothed rim is pressed onto the flywheel.
Connecting rods are forged steel, with covers on the lower heads.
The connecting rod caps are made by tearing them off from a solid connecting rod. This achieves higher accuracy of installation of the cover on the connecting rod.
Thin-walled liners are installed in the lower head of the connecting rod, and a steel-bronze bushing is pressed into the upper head.
Pistons are cast from aluminum alloy.
Each of them has three rings installed: two upper compression rings and a lower oil scraper ring.
The piston bottom is flat, with four recesses for the valves, and on the pistons of the engine mod. 21126 recesses are enlarged compared to engine recesses 2112.
The pistons are cooled with oil, for which special nozzles are installed in the main bearing supports.
They are tubes containing spring-loaded balls.
While the engine is running, the balls open holes in the tubes, and a stream of oil hits the piston from below.
In the engine mod. 21126, a “piston-piston rings-piston pin-connecting rod” set of reduced weight was used (the weight of the piston was reduced from 350 to 235 g, the piston pin - from 113 to 65 g, the connecting rod - from 707 to 485 g, the whole set - by 32%) .
The oil sump is steel, stamped, bolted to the cylinder block from below.
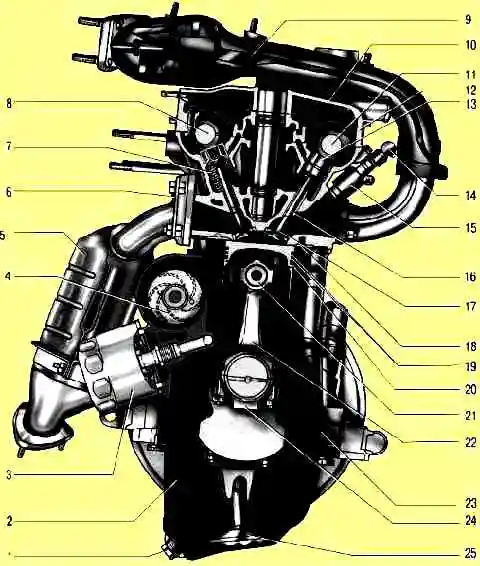
The cylinder head, installed on top of the cylinder block, is cast from aluminum alloy.
At the bottom of the head there are channels cast through which the liquid that cools the combustion chambers circulates.
Two camshafts are installed at the top of the head: one for the intake valves, the other for the exhaust valves.
Engine cylinder head mod. 21126 is different from the mod head. 2112 with an increased area of flanges for the inlet pipeline and spark plug wells made integral with the block head.
Camshafts are installed in supports made in the upper part of the cylinder head, and in one common bearing housing bolted to the cylinder head.
Camshafts are cast iron.
The camshaft pulleys of the 21126 engine differ from the pulleys of the 2112 engine by having the valve timing marks shifted by 2°.
To reduce wear, the working surfaces of the cams and the surfaces under the oil seal are heat-treated - bleached.
The camshaft cams operate the valves through tappets.
Engine 21126 is equipped with hydraulic valve pushers, which automatically compensate for clearances in the valve drive. This engine does not need to adjust the valve clearances during operation.
The engine has four valves per cylinder: two intake and two exhaust.
Guide bushings and valve seats are pressed into the block head. The guide bushings are also equipped with locking rings that keep them from falling out.
Valve scraper caps are installed on the guide bushings to reduce oil penetration into the cylinders.
Each valve has one spring.
The camshafts are driven by a rubber toothed belt from the crankshaft.
The cylinder head cover is made of aluminum.
The joint between the cover and the cylinder head is sealed with a gasket.
The cylinder head cover of the 21126 engine differs from the 2112 cover in the absence of a platform for mounting the ignition module and the presence of holes for mounting individual ignition coils next to the spark plug wells.
Engine lubrication system combined: splash and pressure.
Main and connecting rod bearings and camshaft supports are lubricated under pressure.
The system consists of an oil sump, a gear oil pump with an oil receiver, a full-flow oil filter, an oil pressure sensor and oil passages.
The engine cooling system consists of a cooling jacket, a radiator with an electric fan, a centrifugal water pump, a thermostat, an expansion tank and hoses.
The power supply system includes an electric fuel pump installed in the fuel tank, a throttle assembly, a fine fuel filter, a fuel pressure regulator, injectors, and fuel hoses.
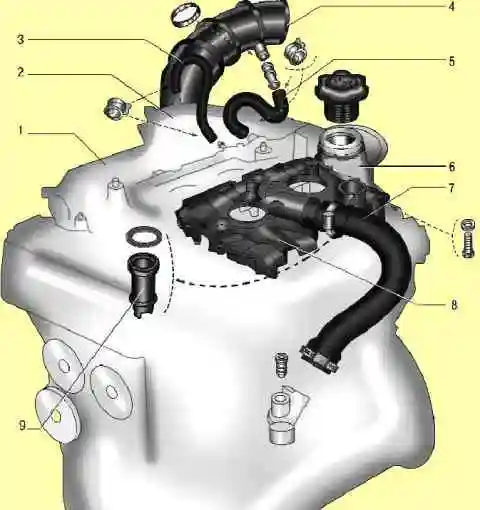
Differences between elements of the engine power supply system mod. 21126 from engine mod. 2112:
- – tubular fuel rail without fuel return is made of stainless steel instead of aluminum alloy;
- – fuel injectors of reduced size are not interchangeable with the previous ones;
- – a redesigned fuel pressure regulator is installed in the fuel pump module rather than on the fuel rail;
- – there is no hole in the throttle assembly connecting the air supply hose to the intake module, bypassing the throttle valve.
Changed throttle body flange configuration.
The power system functionally includes a fuel vapor recovery system with a carbon adsorber, which prevents the release of fuel vapor into the atmosphere.
The ignition system consists of individual ignition coils mounted on the cylinder head cover and spark plugs.
The ignition coils are controlled by the engine electronic control unit (ECU).
Installation of individual ignition coils instead of the engine ignition module mod. 2112 made it possible to eliminate high-voltage ignition wires and improve the technical characteristics and reliability of the system.
The crankcase ventilation system is closed, with crankcase gases removed through separator 8 (Fig. 3) of the oil separator installed in cover 6 of the cylinder head into the intake pipe.
Next, the crankcase gases are sent to the engine cylinders, where they are burned yut.
When the engine is idling, crankcase gases flow through hose 3 of the small circuit through a calibrated hole (nozzle) in the throttle body.
In this mode, a high vacuum is created in the intake pipe, and crankcase gases are effectively sucked into the throttle space.
The jet limits the volume of sucked gases so that engine idle operation is not disrupted.
When the engine is running under load, when the throttle valve is partially or fully open, the main volume of gases passes through the large circuit hose 5 into the air supply hose 4 in front of the throttle assembly and further into the intake manifold and combustion chambers.