Clutch (Fig. 1) single-plate diaphragm type with a damper device on the driven disk
The clutch pressure is generated by the disc pressure spring.
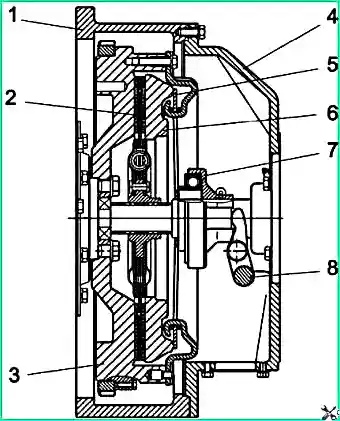
There is no gap between the pressure spring and the release bearing, so the inner race of the bearing rotates at the engine speed.
During operation, the clutch does not require adjustment.
The clutch pedal rotates in the body bracket on a plastic bushing. The bushing is not lubricated.
In the uppermost position, the pedal is held by spring 3. In this case, the pedal rests against rubber buffer 2.
The ends of the clutch fork, moving in the hole in the clutch housing and in the bushing, are lubricated through two grease nipples.
The release bearing does not require lubrication.
Lubricant is added (replaced) into the cavity of the release bearing coupling when performing related repairs, or during seasonal maintenance - in the fall, as well as in case of deterioration in the mobility of the coupling.
The clutch release drive of the PAZ-32053-07 bus (Fig. 2) is hydraulic.
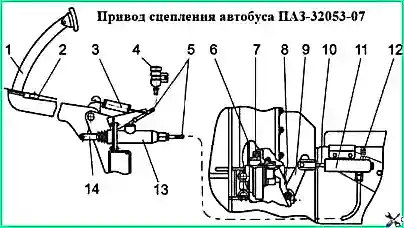
Main cylinder 13, mounted on a bracket under the driver's floor, is activated by pedal 1.
To remove air from the system, working cylinder 11 has a valve that is closed with a rubber cap.
When pedal 1 is not pressed, the cavity under the piston of the main cylinder 13 communicates with reservoir 4 through a compensation hole, which eliminates an increase in pressure in the hydraulic system and clutch slipping.
A spring located inside the working cylinder constantly presses the clutch release bearing against the clutch disc pressure spring.
When the clutch linings wear under the action of the pressure spring of the clutch drive disk, the parts associated with them take a new position, compressing the spring of the working cylinder.
In this case, excess fluid from the working cylinder enters the tank through the compensation hole.
The available length reserve of the working cylinder for piston movement ensures the calculated wear of the clutch linings without adjustment.
Adjustment of the clutch release drive should ensure free play of the clutch pedal (7-8) mm, which corresponds to a gap of (1±0.5) mm between the pusher and the piston of the clutch master cylinder.
The length of the clutch master cylinder piston pusher is adjusted by turning the pusher fork.
After adjusting the length of the pusher, you need to tighten the locknut and install the master cylinder protective cap in place.
When repairing the clutch slave cylinder and replacing parts, you need to check and, if necessary, adjust the length of the slave cylinder piston pusher.
The length from the center line (center) of the hole on the fork to the end of the pusher ball joint should be (150±1) mm.
Filling (bleeding) the hydraulic clutch drive
- Unscrew the cap of the filler tank, remove the plug reflector and fill the reservoir with brake fluid to two-thirds of its height.
- On the clutch slave cylinder, remove the cap from the bleeder valve and place a rubber hose (sleeve 6x14-10) about 500 mm long onto the valve. Place the free end of the hose into a transparent container with a capacity of at least 0.5 liters containing brake fluid. Pour brake fluid up to half the height of the container.
- Create pressure in the system by sharply pressing the clutch pedal (3-4) times at intervals of (3-5) seconds.
- Keeping the pedal pressed, unscrew the working cylinder bleed valve (1/2 -3/4) turns, making sure that the end of the hose remains immersed in the liquid. Liquid with air bubbles will escape into the vessel.
- After the liquid stops flowing into the vessel, turn the valve all the way, and then release the pedal. During pumping, it is necessary to add working fluid to the master brake cylinder reservoir, avoiding a “dry bottom” in the reservoir.
- Repeat the above pumping operations until liquid comes out of the hose without air bubbles.
- Keeping the pedal pressed, turn the bleeder valve all the way and smoothly release the pedal.
- Remove from bleeder valve hose and put on the rubber cap.
- Add fluid to the reservoir to two-thirds of its height, install the reflector and reservoir cap.
The clutch release drive of the PAZ-4234 bus (Fig. 3) can be hydropneumatic.
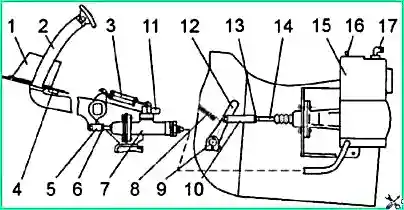
The pneumatic hydraulic booster (abbr. PGU) is installed in a complete set with a ZF SACHS clutch (Germany).
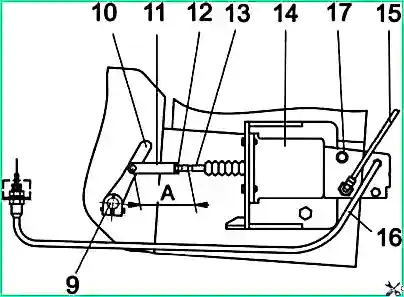
CCGT units manufactured by KAMAZ or Knorr-Bremse (Germany) are used.
PGU is designed to reduce the force on the clutch pedal when it is pressed. The CCGT operates effectively when there is air pressure in the bus pneumatic system - (0.6-0.8) MPa.
The full travel of the clutch pedal is limited by setting the pedal travel limiter 1.
Attention! Operating a bus without a clutch pedal travel limiter will result in clutch failure.
Adjustment of the clutch release drive with the PSU should ensure free play of the pedal - 3-10 mm.
The free play of the pedal in the clutch with the PGU-Knorr-Bremse is regulated by changing the length of the master cylinder piston pusher (see PAZ-32053-07); in the clutch with the PGU-KAMAZ, the free play of the clutch fork lever is additionally regulated.
For clutches with PGU-Knorr-Bremse, the free play of the clutch fork lever is adjusted automatically.
Adjusting the free play of the clutch fork lever (PGU-KAMAZ only):
- Check the free play of the fork lever by rocking the lever in both directions until it reaches its extreme positions.
The free play of the lever should be ─ (1+0.5) mm.
- Remove the pressure spring 8 of the clutch fork lever.
- Loosen locknut 13 of the PSU rod.
- Change the length of the pusher rod by rotating the fork along the thread of the rod.
- Tighten the locknut and install the pressure spring.
After complete adjustment of the clutch drive (in this case, the clutch pedal travel limiter must be installed), the working stroke of the PSU pusher should be (16.5-19.0) mm.
Checking the free play of the fork lever at the clutch with PGU-KAMAZ should be done at every maintenance-1.
At each TO-2 for the clutch with PGU-KAMAZ, you need to check the characteristics of the pressure spring of the fork lever.
The permissible force from the spring when stretched to a length of 130 mm must be at least (75-90) N. If the force is less, the pressure spring should be replaced.
During repairs during installation of the clutch fork lever, you should check the alignment of the marks on the end of the clutch fork shaft and on the lever body, which ensures the position of the lever necessary for proper operation.
During repairs, during the installation of the Knorr-Bremse PSU, the rotation of the fork on the PSU pusher rod should ensure that the distance from the axis of the fork hole to the annular groove on the PSU piston pusher is equal to (186-189) mm.
After making this adjustment, tighten the PSU pusher locknut.
The working stroke of the PSU pusher should be (16.5-19.0) mm.
If it is difficult to move the release bearing clutch along the cover of the input shaft of the gearbox, as well as once a year during seasonal maintenance and repairs associated with removing the gearbox, it is necessary to clean the surface of the cover from wear products of the driven clutch disk and replace or supplement release bearing clutch cavity with Optimal Olista LongTime 3 EP lubricant.
Filling the clutch hydraulic drive with working fluid (removing air from the fluid) is carried out in the same way as on the PAZ-32053-07 bus, taking into account that the bypass valve is located on the PGU body (Fig. 3) and the PGU must be connected to the compressed air pneumatic system with pressure (0.6-0.8) MPa.
Possible clutch malfunctions and methods of elimination
Probable cause
Elimination method
Incomplete engagement of the clutch (the clutch “slips”).
A specific smell, a decrease in acceleration intensity and soon movement style
a) oil getting on the friction linings from the engine or gearbox
Fix oil leak. Replace the driven disc or friction linings. If the oiling is slight, wash the linings with gasoline and clean
working surfaces with fine sandpaper.
b) excessive wear of the driven disk linings
Replace the driven disk or friction linings
Incomplete disengagement of the clutch (clutch “drives”)
Accompanied by difficult gear shifting and grinding noise when changing gears
a) presence of air in the clutch hydraulic drive
Bleed the hydraulic system
b) wear of the inner cuff of the master cylinder
Replace the cuff
c) deformation of the driven disk
Replace the driven disk or edit it
(face runout of the disk relative to the hub spline is no more than 0.7 mm)
d) jamming of the driven disk hub on the splines of the input shaft
Remove jam
e) jamming of the front bearing of the gearbox input shaft (in the flywheel)
Replace the bearing
Fluid leakage from the clutch master or slave cylinder
- Wear of the outer cuff of the master cylinder or the cuff of the working cylinder
Replace worn cuffs or replace cylinder