Je nach Zündart kann Gasdiesel als Motor mit Zwangszündung klassifiziert werden
Sein Arbeitsablauf unterscheidet sich vom Arbeitsablauf von Ottomotoren dadurch, dass der elektrische Funke als Zündquelle des Arbeitsgemisches durch eine Dosis Dieselkraftstoff ersetzt wird
Am Ende des Kompressionshubs wird eine kleine (Pilot-)Dosis Dieselkraftstoff in die erhitzte Luft-Gas-Ladung eingespritzt.
Die Zünddosis an Kraftstoff wird dem Zylinder so zugeführt, dass er früher als das Gas zündet und die gesamte Masse des Gas-Luft-Gemisches entzündet.
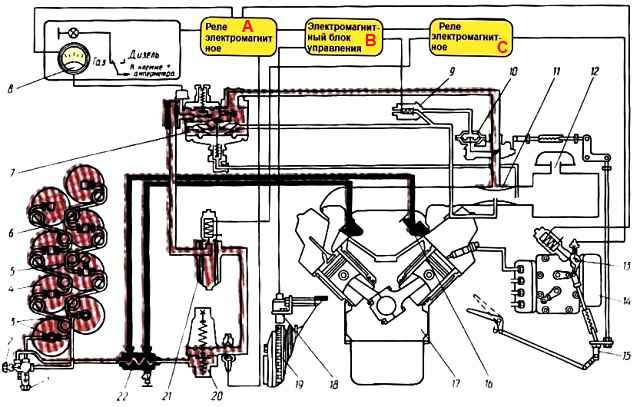
Schema einer Gasflascheninstallation: 1 - Füllventil; 2 - Durchflussventil; 3 - Absperrventil; 4 - Ballon; 5 - Hochdruckmanometer; 6 - Hochdruckleitung; 7 - Niederdruckminderer; 8 - Manometer; 9 - Dreiwege-Magnetventil; 10 - Spender; 11 - Mischer; 12 - Luftreiniger; 13 - Mechanismus zur Begrenzung der Pilotdosis Kraftstoff; 14 - Hochdruckpumpe; 15 - Steuerantrieb für Regler und Gasspender; 16 – tippen; 17 - Motor; 18 - Geschwindigkeitswandler; 19 - Zahnkranz; 20 - Hochdruckminderer; 21 - Magnetventil mit Filter; 22 - Gasheizung; A - elektromagnetisches Relais; B - Steuereinheit; C – elektromagnetisches Relais
Bei der Umrüstung eines Dieselmotors auf den Betrieb im Gas-Diesel-Modus wird ein Gas-Luft-Mischer mit einem System zur Regelung der Gaszufuhr bei Lastwechsel und ein modernisierter Kurbelwellendrehzahlregler mit Kraftstoffzufuhrbegrenzer bei laufendem Motor eingesetzt Gas-Diesel-Betrieb werden dem Design des Antriebssystems hinzugefügt.
Diese Umstellungsmethode ermöglicht einen schnellen Übergang vom Diesel- in den Benzin-Diesel-Modus und zurück.
Informationen zu Gasdieselkraftstoff
Komprimiertes Erdgas wird als Hauptkraftstoff in Gas-Diesel-Motoren verwendet.
Die Eigenschaften komprimierter Erdgase, die als Kraftstoff verwendet werden, müssen den Anforderungen der TU 51-166-83 entsprechen, die zwei Gasklassen festlegt: „A“ und „B“.
Diese Gase bleiben bei normalen Umgebungstemperaturen und hohem Druck (bis zu 20 MPa) gasförmig.
Der Hauptbestandteil von Erdgas ist Methan, ein wertvoller Brennstoff mit guten Klopfeigenschaften und einer relativ hohen spezifischen Verbrennungswärme.
Erdgase enthalten auch schädliche Verunreinigungen, deren Anteil durch technische Bedingungen begrenzt ist.
Dazu gehören giftige Gase (Schwefelwasserstoff und Kohlenmonoxid), nicht brennbare Gase (Stickstoff, Kohlendioxid) und Feuchtigkeit.
Kohlenmonoxid (CO) und Schwefelwasserstoff (H2S) haben eine starke toxische Wirkung auf den menschlichen Körper; außerdem bildet Schwefelwasserstoff bei der Verbrennung Schwefelverbindungen, die Motorteile und Gasgeräte zerstören.
Der CO-Gehalt im Gas sollte 1 % nicht überschreiten und die Masse an Schwefelwasserstoff in 100 m 3 sollte 2 g nicht überschreiten.
Das Vorhandensein von Feuchtigkeit führt bei Minustemperaturen zur Bildung von Verstopfungen in Rohrleitungen und zur Gasreduzierung.
Mit Schwefelverbindungen bildet Feuchtigkeit Säuren, die Korrosion an den Wänden von Zylindern und Rohrleitungen verursachen.
Odorierung von komprimiertem Erdgas ermöglicht es Ihnen, das Vorhandensein von Gas am Arbeitsplatz und im Arbeitsbereich anhand des Geruchs festzustellen.
Beim Odorieren werden 0,016 g Mercaptanschwefel pro 1 m³ Gas zugesetzt.
Aus toxikologischen Gründen sollte die maximal zulässige Gaskonzentration an Arbeitsplätzen und in Arbeitsbereichen 300 mg/m 3 nicht überschreiten. Die Bestimmung erfolgt mit Gasanalysatoren.
Aufgrund der Tatsache, dass Methan viel leichter als Luft ist, sollten für die Wartung und Reparatur von Gas-Diesel-Fahrzeugen im oberen Teil der Räumlichkeiten Lüftungssaug- und Gasalarmsensoren installiert werden.
Zusätzlich zu den aufgeführten Verunreinigungen enthält Erdgas weitere brennbare Gase: Propan, Ethan, Butane und Pentane, deren Anteil unbedeutend ist, daher werden die Eigenschaften komprimierter Erdgase durch ihren Hauptbestandteil Methan (CHc) bestimmt.
Entflammbarkeitsgrenzen charakterisieren die Konzentration von Gasen in einem Gemisch mit Luft, bei der ein Motorbetrieb möglich ist.
Erdgas hat bei einer Temperatur von +20 °C und Normaldruck eine Brennbarkeitsgrenze: untere – 4 %, obere – 15 % des Gasgehalts im Luftvolumen. Bei dieser Konzentration ist das Gas-Luft-Gemisch explosionsfähig.
Der Gaskompressibilitätskoeffizient berücksichtigt die Unverhältnismäßigkeit der Volumenänderung mit zunehmendem Druck.
Für Methan liegt der Kompressibilitätskoeffizient bei 0 °C und einer Druckänderung von 0,1 bis 20 zwischen 1 und 0,82.
Unter Berücksichtigung des Kompressibilitätskoeffizienten an Gastankstellen, Tabellen zum Hubraum von Fahrzeugen.
Gasflascheninstallation
In einer Gasflaschenanlage speichern Sie Erdgas in einem komprimierten Zustand von bis zu 20 MPa in Flaschen.
Die Erdgasreserve in einer Flasche bei einem Druck von 20 MPa beträgt etwa 10 m 3.
Um eine Reichweite von 250...300 km zu gewährleisten, können je nach Fahrzeugmodell sechs, acht oder zehn Zylinder zum Einsatz kommen.
Die Abbildung zeigt ein Diagramm der Gasflascheninstallation der Sattelzugmaschine KamAZ-54118 mit acht Zylindern 4.
Das Zylinderpaket besteht aus zwei Abschnitten mit jeweils vier Zylindern. Dieses Schema ermöglicht es dem Motor, mit den Gasreserven eines Abschnitts zu arbeiten, wenn die Dichtung in einem anderen Abschnitt gebrochen ist.
Zylinderabschnitte, die jeweils über ein Absperrventil 3 verfügen, sind über ein Kreuz mit 1 Füllventil und 2 Versorgungsventilen verbunden.
Während des Motorbetriebs im Gas-Diesel-Betrieb sind die Ventile 2 und 3 geöffnet.
Unter hohem Druck stehendes Druckgas strömt durch die Heizung 22, in der das Kühlmittel die Flüssigkeit des Motorkühlsystems ist, und gelangt in den einstufigen Hochdruck-Gasreduzierer 20, wo der Gasdruck auf 0,9–1,1 reduziert wird MPa.
Auf dem Weg zum Reduzierer wird das Gas erhitzt, um Eispfropfen in der Rohrleitung zu vermeiden, die sich durch starke Abkühlung des Gases bilden können, wenn der Druck im Reduzierer stark abnimmt.
Dann wird das Gas dem Filter 21 mit einem Filzelement und einem elektromagnetischen Ventil zugeführt und von dort zu einem zweistufigen Gasreduzierer 7, wo sein Druck nahezu auf Atmosphärendruck reduziert wird.
Der Betrieb des Getriebes wird durch Vakuum gesteuert, das über ein Rohr vom Mischdiffusor 11 auf das Getriebe übertragen wird.
Vom Reduzierer gelangt Gas über den Spender 10 in den Mischer, wo ein Gas-Luft-Gemisch entsteht und dann zusammen mit Luft in die Motorzylinder gesaugt wird.
Der Gasdruck in den Zylindern und damit die Kraftstoffzufuhr in ihnen wird mit einem Hochdruckmanometer 5 kontrolliert. Mit dem Niederdruckmanometer 8 wird die Funktion der ersten Getriebestufe überprüft.
Auf der Abdeckung des Kurbelwellendrehzahlreglers ist ein elektromagnetischer Mechanismus 13 installiert, der den Weg des Reglersteuerhebels von der Position der minimalen Leerlaufdrehzahl auf die Position begrenzt, die der Zufuhr der Pilotdosis Kraftstoff entspricht.
Der Motor wird in den Gas-Diesel-Modus umgeschaltet, nachdem der Dieselmotor gestartet und auf eine Kühlmitteltemperatur von mindestens 50°C aufgewärmt wurde, indem der Schlüssel am Cockpit-Instrumentenbrett auf die Position „Gas“ gestellt wird.
Elektrisches Motorsteuerungssystem. Zu diesem Zweck ist das Fahrzeug mit zusätzlichen Gas-Diesel-Elektrogeräten ausgestattet.
Es umfasst außerdem ein System zur Begrenzung der Gaszufuhr: wenn die Kurbelwelle die maximale Drehzahl erreicht, wenn der mechanische Geschwindigkeitsregler die Zufuhr der Pilotdosis flüssigen Kraftstoffs abschaltet, und eine elektrische Sperre, die die gleichzeitige Zufuhr von Gas und Kraftstoff verhindert Vollversorgung mit flüssigem Dieselkraftstoff (Doppelschub).
Zylinder für Druckgas. Flaschen dienen der Lagerung und dem Transport von Gaskraftstoff und sind die wichtigsten Komponenten der Gasausrüstung eines Autos. Die Sicherheit des Fahrzeugbetriebs hängt von ihrer Zuverlässigkeit und Dichtheit ab.
Die Zylinder sind für einen Arbeitsdruck von 20 MPa ausgelegt. Sie werden aus nahtlosen Rohren durch Aufrollen der Böden und Hälse hergestellt.
Um die Festigkeit zu erhöhen und die Bruchsicherheit im Falle einer Zerstörung zu gewährleisten, werden sie einer Wärmebehandlung, einem Härten und einem Anlassen unterzogen.
Derzeit werden zwei Arten von Zylindern aus Kohlenstoffstahl oder legiertem Stahl verwendet.
Normale Karbonstahlflasche mit einem Fassungsvermögen von 50 Litern. hat eine Masse von 93 kg.
Der Zylinder aus legiertem Stahl hat das gleiche Fassungsvermögen, wiegt jedoch nicht mehr als 65 kg.
Fertige Zylinder werden auf Festigkeit und Dichtheit der Verbindungen mit Armaturen geprüft.
Verwendbare Flaschen sind rot lackiert und auf der Vorderseite unten sind folgende Passdaten eingeprägt: Markenzeichen des Herstellers, Flaschennummer, Gewicht, Herstellungsdatum und Jahr der nächsten Prüfung, Betriebsdruck und Prüfdruck, Füllmenge, Stempel der Qualitätskontrolle Prüfer der Anlage, Hersteller und Normnummer.
Betrachten wir ein Beispiel für die Angabe des Herstellungsdatums und des nächsten Tests 10-89-94 – der Zylinder wurde im Oktober 1989 hergestellt und getestet, wiederholte hydraulische Tests sollten 1994 stattfinden
Der Bereich auf dem Zylinder mit den Passdaten ist mit farblosem Lack überzogen und von einem farbigen Rahmen umgeben.
Der Zylinderhals hat ein Loch mit konischem Gewinde, in das ein Adapter zum Anschluss von Rohren eingeschraubt wird
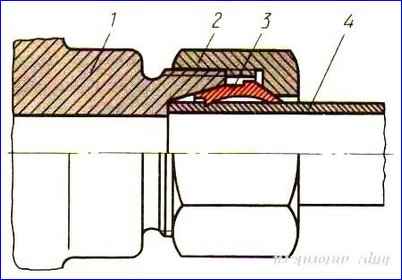
Eine notwendige Voraussetzung für den richtigen Mund Neuer Adapter im Zylinder – das Vorhandensein von 3-4 Ersatzgewinden am Adapter.
Die Flaschen sind durch Hochdruck-Gasleitungen miteinander verbunden. Sie bestehen aus nahtlosen Stahlrohren mit einem Außendurchmesser von 10 mm und einer Wandstärke von 2 mm.
Gasleitungen werden ohne Dichtungen angeschlossen. Die Dichtheit der Verbindungen wird dadurch erreicht, dass der Nippel 3 in das Rohr 4 eingeschnitten wird und das Rohrende mit der Überwurfmutter 2 fest an den Anschlussstutzen 1 gedrückt wird.
Der Nippelanschluss ermöglicht eine wiederholte Demontage. Beim Einbau eines neuen Nippels ist darauf zu achten, dass dieser einen Abstand von ca. 1,5-2 mm vom Rohrende hat.
Beim Anziehen der Überwurfmutter 2 verformt sich der Nippel 3 und nimmt die Form eines inneren konischen Lochs im Fitting an, wodurch die Dichtheit der Verbindung gewährleistet wird.
Gleichzeitig schneidet der Nippel eine scharfe Kante in die Rohrwände und verhindert so, dass dieser unter dem Einfluss von hohem Druck aus der Verbindung gezogen wird.
Die Anzugskraft der Überwurfmutter beim vorläufigen Einsetzen des Rings sollte 40-56 N betragen.
Der Nippel muss fest auf dem Schlauch sitzen. Wenn der Nippel nach dem Anziehen der Mutter keine dichte Verbindung gewährleistet, sollte er zusammen mit der Gasleitung ausgetauscht werden.
Vorläufiges Anlöten des Nippels mit Lot und Aufweiten der Rohrenden ist nicht zulässig.
Wenn die Nippelverbindung nach dem Anziehen der Mutter 2 keine vollständige Dichtheit gewährleistet, sollte sie ersetzt werden.
Dazu wird der Nippel 3 zusammen mit einem Rohrstück abgeschnitten, das Rohrende auf einer Länge von 13-15 mm von Farbe und Korrosionsschutzbeschichtung gereinigt und ein neuer Nippel darauf montiert.
Um die Verdrehkräfte auszugleichen, die bei möglichen Verformungen des Fahrzeugrahmens über die Zylinder auf die Gasleitung übertragen werden, werden die Hochdruckrohre so gebogen, dass sie Ausgleichsringe bilden.
Diese Ringe gleichen auch die Reduzierung der Schlauchlänge beim Austausch des Nippels aus.
Die Zylinder am Auto werden mit Halterungen und Klammern befestigt.
Eine Verschiebung von Zylindern aufgrund einer Lockerung ihrer Befestigungen kann zum Bruch von Hochdruckgasleitungen in der Nippelverbindung führen.
Rohrbrüche gehen in der Regel mit schwerwiegenden Folgen bis hin zum Brand einher. Daher muss die Befestigung der Zylinder die Möglichkeit ihrer Bewegung vollständig ausschließen.
Besonderes Augenmerk sollte auf die Verstärkung der Zylinder durch Klammern gelegt werden. Es ist nicht zulässig, die Klemmen festzuziehen, bis sich ihre Enden berühren.
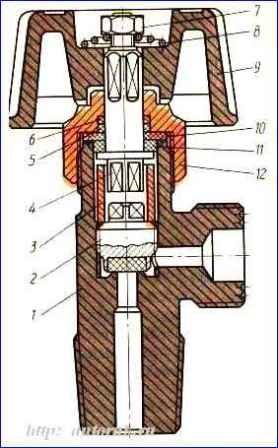
Ventile
Die Gasflascheninstallation verfügt über vier Ventile: zwei Flaschenventile, ein Füllventil und ein Versorgungsventil (Hauptventil).
Zylinderventile werden verwendet, um Zylinderabschnitte an eine gemeinsame Leitung anzuschließen.
Das Füllventil ist zum Befüllen von Druckgasflaschen konzipiert.
Der Füllventilanschluss verfügt über ein spezielles Linksgewinde und ist mit einem Stopfen verschlossen, der ihn vor Schmutz und Feuchtigkeit schützt.
Bei anderen Ventilen haben Anschlüsse Rechtsgewinde.
Zum Anschluss von Gasleitungen wird an dieser Armatur ein Adapter montiert, der mit einer Dichtung abgedichtet ist. Ansonsten sind alle Ventile gleich aufgebaut, ihr Aufbau ist in der Abbildung dargestellt.