Das Kontrollsystem ermöglicht es Ihnen, sowohl bei geparktem als auch bei fahrendem Fahrzeug vom Fahrersitz aus den Luftdruck in den Reifen zu verändern, den Druck in den Reifen zu kontrollieren und das Fahrzeug mit geringen Reifenschäden weiter zu bewegen.
Aufbau des Reifendruckregelsystems (Abb. 1):
- - Kompressor 1.
- - Luftzylinder 4.
- - Steuerventil 7.
- - Druckregler 3.
- - Sicherheitsventil 5.
- - Radluft-Absperrventile.
- - In den Achszapfen eingebaute Dichtblöcke (Abb. 2).
- - Manometer.
- - Rohrleitungen und Schläuche.
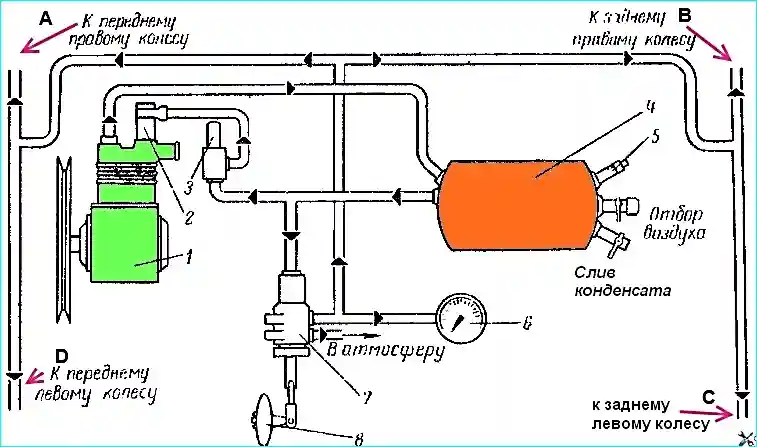
Diagramm des Reifendruckregelsystems:
- Kompressor.
- Zylinder wird entladen.
- Druckregler.
- Heißluftballon.
- Sicherheitsventil.
- Manometer.
- Steuerventil.
- Steuerventilgriff.
- - (A) Zum rechten Vorderrad.
- - (B) Zum rechten Hinterrad.
- - (C) Zum linken Vorderrad.
- - (D) Zum linken Hinterrad.
Kompressorfunktionen:
Der Kompressor von Fahrzeugen mit Reifendruckregelsystem verfügt im Gegensatz zu dem Kompressor von Fahrzeugen ohne dieses System über einen Entlastungszylinder, der in eine Gewindebohrung im Kompressorkopf oberhalb des Einlassventils eingeschraubt ist.
So funktioniert das System:
- - Wenn der Druck im System auf 5–5,5 kg/cm² ansteigt, verbindet der Druckregler den Entlastungszylinder mit dem Lufttank. Dadurch gelangt Druckluft in den Entlastungszylinder und bewegt den Kolben 6 (siehe Abb. 3) nach unten.
- - Die nach unten bewegte Kolbenstange öffnet Ventil 12 und verbindet den Zylinderraum mit dem Motorluftfilter. Wenn sich der Kompressorkolben nach oben bewegt (Kompressionshub), wird die Luft zurück in den Luftfilter und nicht in das System gedrückt, d. h. der Kompressor läuft ohne Last.
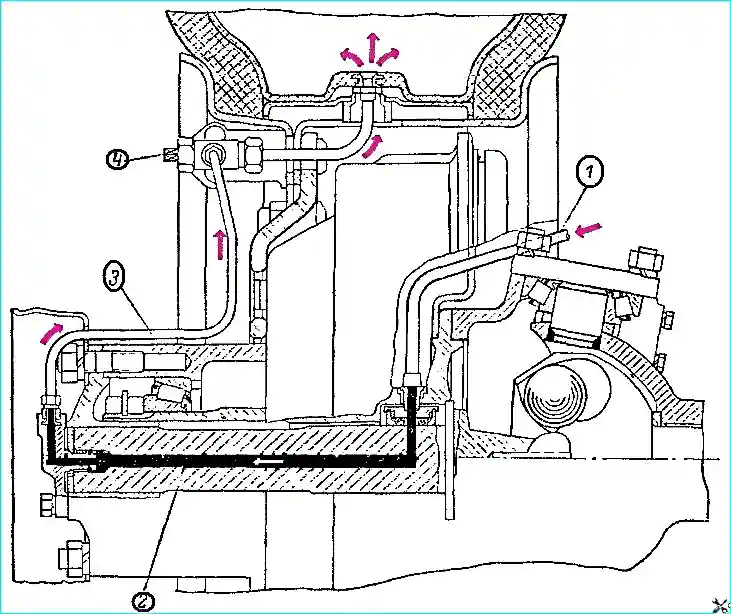
Schema der Luftversorgung des Radreifens:
- Luftzufuhrschlauch zum Dichtungsblock.
- Luftkanal.
- Luftzufuhrleitung zum Radkran.
- Luftkran.
Druckregler:
- - Wenn der Druck im System auf 4–4,5 kg/cm² abfällt, verbindet der Druckregler den Entlastungszylinder mit der Atmosphäre. Kolben 6 mit Stange steigt unter der Wirkung von Feder 7 nach oben, das Einlassventil wird geöffnet und der Kompressor beginnt erneut, Luft in das System zu pumpen.
- - Der Druckregler (Abb. 4) hält zusammen mit dem Entlastungszylinder den Druck im System automatisch im Bereich von 4–4,5 bis 5–5,5 kg/cm².
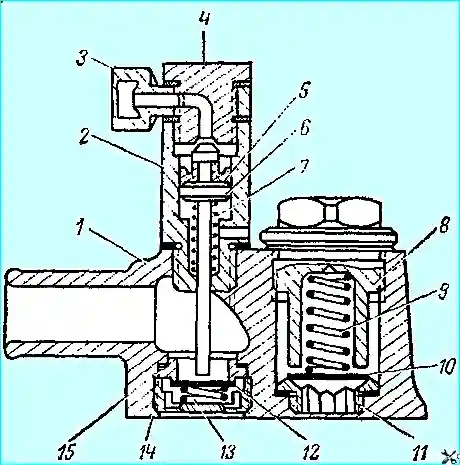
Kompressorkopf:
- Kopfgehäuse.
- Zylinderkörper entladen.
- Kupplung.
- Brustwarze.
- Manschette.
- Kolben.
7, 9, 13. Federn.
- Stau.
- Ablassventil.
11, 16. Sättel.
- Einlassventil.
- Einlassventilkörper.
Sicherheitsventil (Abb. 5):
Wird für den Fall eines Ausfalls des Druckreglers installiert. Eingestellt auf 6 kg/cm² Druck, der höher ist als der Druckregler.
Steuerventil (Abb. 6):
Ermöglicht das Anschließen der Radschläuche an einen Kompressor (beim Aufpumpen der Reifen mit Luft), an die Atmosphäre (bei nachlassendem Reifendruck) oder das Verschließen (zum Aufrechterhalten des vorhandenen Reifendrucks).
Luftbehälter:
Entwickelt, um Kondensat aus Wasserdampf und Öl zu beseitigen, das zusammen mit der Druckluft vom Kompressor in das System gelangt.
Störungen des Reifendruckregelsystems und wie man sie behebt:
- Luftleckage bei Steuerventil in Neutralstellung und geöffneten Radabsperrventilen:
- Lose Verbindungen in Rohrleitungen und Schläuchen.
Lösung: Ziehen Sie die Verbindungen fest oder ersetzen Sie die Luftkanalelemente.
- Die Dichtmanschetten des Öldichtungsblocks sind beschädigt.
Abhilfe: Dichtblock oder beschädigte Manschetten austauschen.
- Beim Aufpumpen von Reifen mit Luft steigt der Druck in ihnen nicht auf 2,8 kg/cm²:
- Großes Luftleck im System.
Lösung: Leckstellen identifizieren und beseitigen.
- Blockieren des Entladezylinderkolbens durch Verschmutzung oder Verbiegen der Stange.
Lösung: Ersetzen Sie die gebogene Stange durch einen Kolben. Zylinderteile zerlegen, waschen und schmieren.
- Der Druckregler verbindet den Entlastungszylinder nicht mit der Atmosphäre, wenn der Druck im System abfällt:
- Lösung: Regler zerlegen, Teile in Benzin waschen, trocknen und zusammenbauen. Bei Bedarf anpassen.
- Verschlissene Kolbenringe oder Kompressorzylinder:
- Lösung: Reparieren oder ersetzen Sie den Kompressor.
- Häufiges Betätigen des Sicherheitsventils:
- Fehlfunktion des Druckreglers oder des Sicherheitsventils.
Lösung: Zerlegen, waschen und zusammenbauen. Bei Bedarf anpassen.
- Im Winter lässt sich ein oder alle Reifen nicht aufpumpen oder die Luft verlieren:
- Gefrorenes Kondensat verstopft den Luftkanal.
Lösung: Finden Sie die Verstopfung, erwärmen Sie sie und blasen Sie sie mit Luft aus.
Reparatur der Reifendruckregelanlage:
- Demontage, Prüfung und Montage von Systemeinheiten:
- - Lassen Sie vor dem Entfernen von Systemkomponenten die Druckluft aus der Luftflasche ab.
- - Demontieren Sie den Druckregler in der folgenden Reihenfolge:
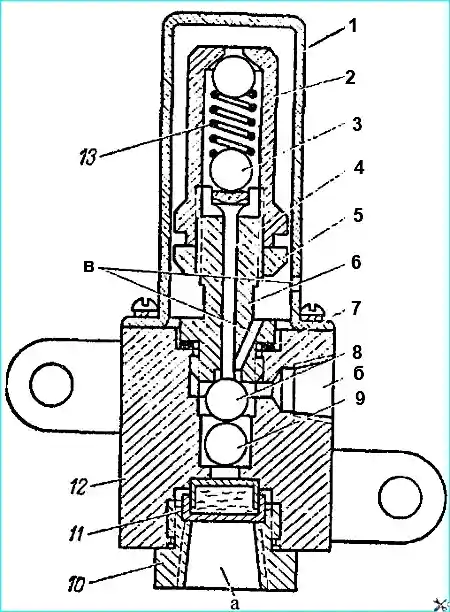
- - Entfernen Sie die Abdeckung von 1 Regler.
- - Kontermutter 5 lösen, Einstellkappe 2 abschrauben und Ventilschaft 4, Feder 13 und Stützkugeln 3 entnehmen.
- - Sitz 6 des Reglers abschrauben, Einstellbuchsen 7 und Kugelhähne 8 und 9 herausnehmen.
- - Schrauben Sie die Filterabdeckung 10 ab und entnehmen Sie den Filter 11.
- - Wenn ein Schaden festgestellt wird, müssen die Teile oder der Regler ausgetauscht werden.
- - Waschen Sie alle Teile vor dem Zusammenbau mit Benzin.
- - Bauen Sie den Regler in umgekehrter Reihenfolge zusammen.
- - Überprüfen Sie die Funktion des Reglers: Er sollte den Kompressor bei einem Druck von 5–5,5 kg/cm² abschalten und bei einem Druck von 4–4,5 kg/cm² einschalten.
- Druckregler einstellen:
- - Durch Drehen der Kappe 2 sicherstellen, dass der Kompressor bei einem Druck von 4–4,5 kg/cm² einschaltet.
- - Durch Veränderung der Anzahl der Einstellscheiben 7 einen Druck von 5–5,5 kg/cm² erreichen, bei dem der Kompressor abschaltet.
- Sicherheitsventil:
- - Zur Demontage Sitz 1 abschrauben, Ventilkugel 3 und Führungsstange 5 mit Feder 6 entnehmen.
- - Wenn das Kugelventil oder sein Sitz beschädigt ist, ersetzen Sie die Teile.
- - Waschen Sie die Teile vor dem Zusammenbau in Benzin.
- - Stellen Sie das Ventil nach der Montage auf einen Druck von 6 kg/cm² ein.
- Steuerventil:
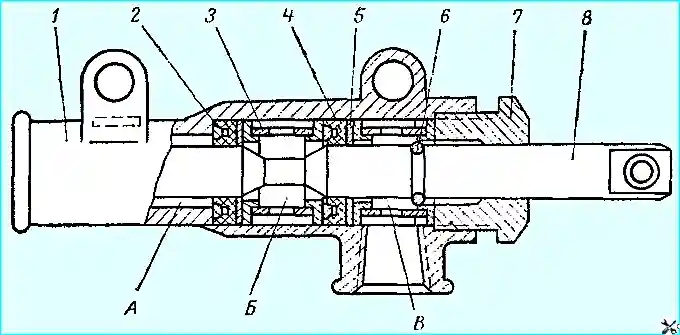
- - Zur Demontage die Feststellschraube der Mutter 7 lösen, Ventil 8, Dichtungen 4, Distanzringe 2, Buchsen 3 und Stützscheiben 5 entnehmen.
- - Ersetzen Sie beschädigte Dichtungen.
- - Teile vor der Montage waschen und schmieren.
- - Die Spannung der Dichtungen mit Mutter 7 einstellen.
- Blöcke versiegeln:
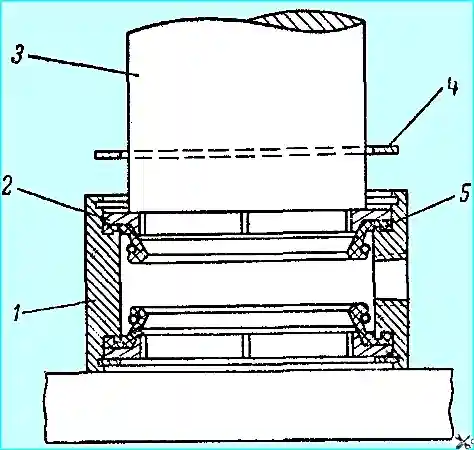
- - Identifizieren Sie den fehlerhaften Block, entfernen Sie den Drehstift und nehmen Sie ihn heraus.
- - Wenn die Dichtungen abgenutzt sind, zerlegen Sie den Block und ersetzen Sie die Dichtungen.
- - Überprüfen Sie die Dichtheit des Blocks bei einem Druck von 3 kg/cm².
- - Tragen Sie beim Einbau des Blocks in den Drehzapfen Fett in den Hohlraum zwischen den Manschetten auf.
Prüfung der Dichtheit des Systems:
- - Bei geöffneten Radkränen und dem Griff des Steuerventils in Neutralstellung, der Fall Der Luftdruck im Reifen sollte innerhalb von 12 Stunden 1 kg/cm² nicht überschreiten.
- - Führen Sie die Prüfung durch, nachdem die Reifen auf Umgebungstemperatur abgekühlt sind.