Die Motoren verfügen über ein Mischschmiersystem (Druck- und Spritzschmierung)
Unter Druck wird Öl an die Haupt- und Pleuellager der Kurbelwelle sowie an die Nockenwellenlager geleitet
Die Ölzufuhr zu den Kipphebelbuchsen erfolgt mit pulsierendem Druck durch die hohlen Kipphebelachsen, in die das Öl durch Kanäle gelangt, die vom zweiten und vierten Nockenwellenlager ausgehen.
Die Ölzufuhr zu den übrigen Motorteilen erfolgt durch Schwerkraft und Spritzwasser.
Zur Kühlung des Öls sind die Motoren mit einem Ölkühler ausgestattet, der vor dem Kühler des Kühlsystems installiert ist.
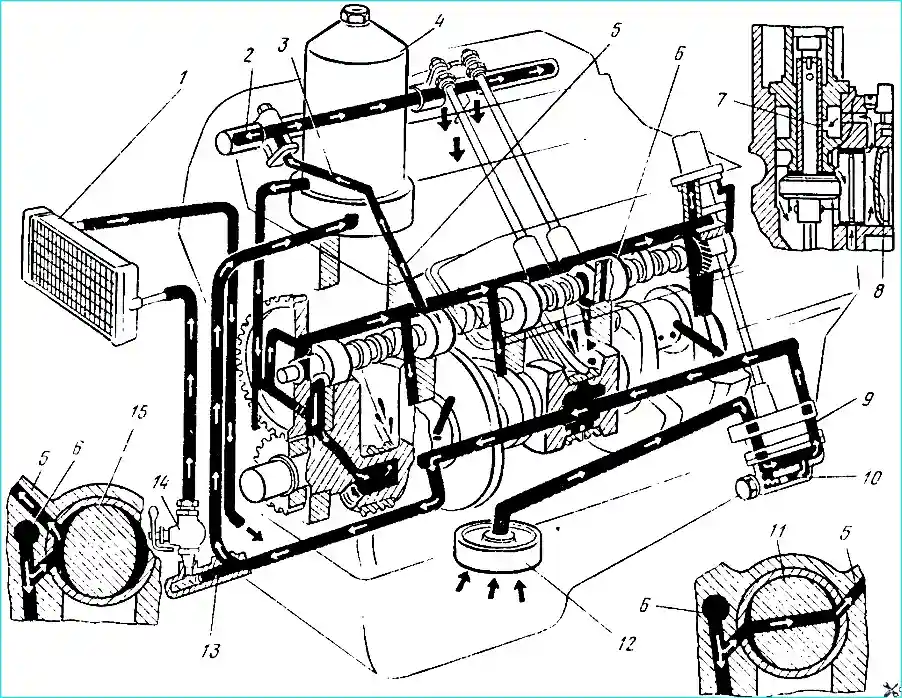
Der Druckabfall im Schmiersystem wird hauptsächlich durch den Verschleiß der Ölpumpenteile oder der Lager der Kurbelwelle und Nockenwelle verursacht.
Bei starkem Verschleiß beginnt die Ölpumpe, geräuschvoll zu arbeiten. Um Störungen an der Pumpe festzustellen, muss diese vom Motor abgebaut und zerlegt werden.
Sie sollten jedoch erst mit der Demontage der Pumpe beginnen, nachdem Sie den Zustand des Druckminderventils überprüft haben, da dieses die Ursache für einen anormalen Druck im Ölsystem sein kann (die Feder ist schwach, der Kolben steckt fest usw.).
Um sicherzustellen, dass das Druckminderventil ordnungsgemäß funktioniert, schrauben Sie den Stopfen ab, entfernen Sie die Feder und stellen Sie sicher, dass sich der Kolben frei und ohne zu klemmen in seinem Sitz bewegt und dass die Feder in einem normalen Zustand ist.
Die Länge der Feder im freien Zustand sollte 50 mm betragen. Die Kraft der Ventilfeder sollte bei einer Kompression um 10 mm 4,6 kg betragen.
Wenn die Kraft nachlässt, wird die Feder durch eine neue ersetzt, da das Unterlegen von Unterlegscheiben oder das Dehnen der Feder zur Kraftverstärkung strengstens verboten ist.
Ölpumpe demontieren
- 1. Entfernen Sie die Pumpe zusammen mit der Dichtung vom Zylinderblock.
- 2. Entfernen Sie das Gehäuseunterteil mit Abtriebsrad und Dichtung.
- 3. Entfernen Sie das untere Antriebszahnrad der Ölpumpe und den Zahnrad-Scheibenkeil von der Pumpenwelle.
- 4. Entfernen Sie die Ölpumpenleitplatte mit der Dichtung.
- 5. Das Abtriebszahnrad des Pumpenoberteils aus dem Gehäuse herausnehmen.
- 6. Die Welle mit dem Antriebszahnrad des Oberteils aus dem Pumpengehäuse herausnehmen.
- 7. Nach dem Zerlegen der Pumpe alle Teile gründlich waschen, trocknen und überprüfen.
- 8. Wird an der Trennwand der Ölpumpe ein Verschleiß eines Zahnrades festgestellt, ist dieses solange abzuschleifen, bis die Verschleißspuren beseitigt sind. Bei starkem Verschleiß der Teilgehäuse muss die Pumpe durch eine neue ersetzt werden.
Beachten Sie bei Reparaturen Folgendes.
Der Abstand vom Ende der Welle mit Sechskantloch bis zum oberen Ende des Antriebszahnrads des Pumpenoberteils sollte 40 ± 0,15 mm betragen.
Für den Stift zur Befestigung des Zahnrads auf der Pumpenwelle wird im Abstand von 15 mm vom Zahnradende ein Loch mit 4 mm Durchmesser bis zu einer Tiefe von 23 ± 0,5 mm gebohrt.
Der Stift darf nicht über die Ebene der Zahnhöhle hinausragen.
Beim Auspressen der Abtriebsradachsen aus den Pumpenteilgehäusen werden diese auf 100-120°C, beim Einpressen auf 160-170°C erhitzt und die Achsen in Trockeneis gekühlt.
Beim Einpressen der Abtriebsradachse ist ein Maß von 3 ± 0,25 mm in das Pumpengehäuse-Oberteil und 0,5 ± 0,25 mm in das Pumpengehäuse-Unterteil vom Gehäuseende bis zum Achsende einzuhalten.
Bauen Sie die Pumpe in umgekehrter Reihenfolge zusammen.
Beim Zusammenbau der Pumpe sollten die Paronit- oder Kartondichtungen der Gehäuse ausgetauscht werden (ihre Dicke beträgt 0,3–0,4 mm).
Die Verwendung von Schellack oder anderen Dichtmitteln sowie eine Erhöhung der Dichtungsstärke ist nicht zulässig, da hierdurch die Leistung der Ölpumpe reduziert wird.
Bevor Sie die Pumpe am Motor montieren, füllen Sie sie mit Öl, da eine trockene Pumpe gleich zu Beginn des Motorbetriebs die Reibflächen nicht mit Öl versorgt, was zu Riefenbildung und Ausfall führen kann.
Ölpumpenantrieb demontieren (Abb. 2). Den Stift 6 des Antriebsrades mit einem Durchschlag von 3 mm Durchmesser herausdrücken.
1. Sechskantwelle 7 des Ölpumpenantriebs demontieren.
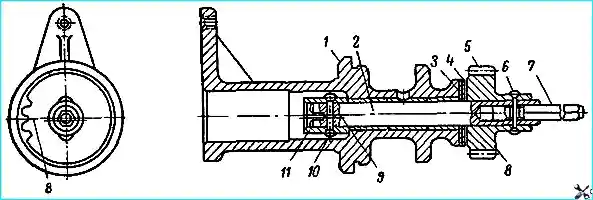
- 2. Drücken Sie 5 Antriebswelle mittels Dorn, wobei das Antriebsgehäuse mit seinem oberen Ende auf einer Platte mit einer Öffnung für den freien Austritt der mit der Druckhülse montierten Welle montiert wird.
- 3. Anlaufscheiben 3 und 4 entfernen und Welle 2 aus dem Antriebsgehäuse des Leistungsschalter-Verteilers nehmen.
- 4. Den Stift 10 der Druckhülse 11 der Antriebswelle herausdrücken und die Hülse herauspressen.
Nach der Demontage alle Antriebsteile waschen und gründlich überprüfen.
Montage des Brecher-Verteiler-Antriebs. Die Druckhülse 11 auf die Brecher-Verteiler-Antriebswelle aufpressen, dabei ein Maß von 19 ± 0,1 mm vom Wellenende bis zum unteren Hülsenende einhalten.
Bohren Sie in die Druckhülse im Abstand von 13 ± 0,15 mm vom Ende ein Loch mit einem Durchmesser von 4+0,03 mm.
Die Achse des Lochs in der Buchse muss mit der Achse des Lochs in der Antriebswelle des Leistungsschalterverteilers übereinstimmen.
Senken Sie Fasen 0,8 mm tief im 90˚-Winkel in eine Bohrung mit 4 mm Durchmesser auf beiden Seiten.
Stift 10 in die Bohrung eindrücken und beidseitig vernieten.
Schmieren Sie die montierte Walze mit sauberem Motoröl, setzen Sie sie in das Antriebsgehäuse des Brechers und Verteilers ein und testen Sie von Hand, ob sie sich leicht drehen lässt.
Montieren Sie Anlaufscheiben auf der Rolle, zuerst Stahl 3, dann Bronze 4.
Pressen Sie Zahnrad 5 auf Welle 2 und halten Sie dabei einen Abstand von 0,15–0,55 mm zwischen den Enden des Zahnrads und der bronzenen Anlaufscheibe ein.
Achse 9 der Nut auf der Welle muss parallel zur Achse verlaufen, die durch die Mitte der Vertiefung 8 am unteren Ende des Zahnrads verläuft, die zulässige Abweichung beträgt ± 2˚.
Bohren Sie ein Loch mit einem Durchmesser von 4+0,03 mm und halten Sie dabei einen Abstand von 9 ± 0,15 mm von der Lochachse bis zum Ende der Zahnradnabe ein.
Beim Bohren eines Lochs muss die Wellenbaugruppe mit dem Ende der Druckhülse 11 gegen das Gehäuse 1 des Brecher-Verteiler-Antriebs gedrückt werden.
Die Achse der Bohrung muss durch die Achse und die Mitte der Stirnfläche der Rolle 7 verlaufen. Die zulässige Abweichung beträgt maximal 0,1 mm.
Stecken Sie die Sechskantwelle 7 des Ölpumpenantriebs in die Sechskantbohrung am Ende der Welle 2 des Antriebs und drücken Sie einen Stift mit 4 mm Durchmesser in die Bohrung.
Nieten Sie den Stift auf beiden Seiten.
Überprüfen Sie die Leichtgängigkeit der Rolle, den Abstand zwischen der Anlaufscheibe und dem Ende des Antriebszahnrads sowie den Versatz der Mitte der Zahnnut des Unterbrecher-Verteiler-Antriebszahnrads relativ zur Achse der Rollennut.
Demontage des Zentrifugalölfilters. Entfernen Sie das Gehäuse.
Entfernen Sie die Rotorschale vorsichtig an der Mutter und verhindern Sie, dass sich der Rotor dreht.
Bestimmen Sie durch Schwenken des Rotors auf der Achse das radiale Spiel in den Rotorbuchsen.
Eine spürbare Bewegung des Rotors deutet auf einen Verschleiß der Buchsen hin und der Rotor muss ausgetauscht werden.
Entfernen Sie den Rotor zusammen mit der Unterlegscheibe.
Beim Ausbau des Rotors muss darauf geachtet werden, dass der obere Ring des Axiallagers nicht zusammen mit dem Rotor angehoben wird, da dieser in das Filtergehäuse und von dort in den Steuerzahnraddeckel und in das Motorkurbelgehäuse fallen kann.
Nach dem Zerlegen des Filters alle Teile gründlich mit Kerosin waschen und mit Druckluft ausblasen.
Überprüfen Sie die Düsen und schrauben Sie sie bei Verstopfung zur Reinigung ab
Jede Düse sollte in ihrer eigenen Fassung installiert werden, da sie zusammen mit dem Rotor bearbeitet werden. Es wird daher nicht empfohlen, beide Düsen gleichzeitig vom Rotor abzuschrauben.
Zum Reinigen der Düse führen Sie einen Bohrer mit 5 mm Durchmesser in die Öffnung ein und entfernen durch Drehen mit der Hand sämtliche Ablagerungen.
Anschließend wird der Strahl noch einmal mit Kerosin gewaschen und mit Druckluft durch die Düsenöffnung geblasen.
Achten Sie beim Einbau der Düse darauf, dass eine der Kanten des Düsenkopfes mit der Markierung auf der Rotornabe übereinstimmt, da eine Verletzung der Position der Düsenlöcher dazu führt, dass Öl in die Rotorrotationszone geschleudert wird, was dessen Rotation erheblich verlangsamt.
Um die Dichtung der Rotorbechermutter zu ersetzen, entfernen Sie den Federsicherungsring von der Mutter und nehmen Sie die Mutter vom Rotorbecher ab.
Montieren Sie den Filter in umgekehrter Reihenfolge.
Achten Sie beim Zusammenbau darauf, dass die Dichtungen nicht aus ihrem Sitz gedrückt werden und sich der Filterrotor frei auf der Achse drehen kann.