- - очистити всі привалювальні поверхні блоку від прилиплих і порваних при розбиранні прокладок;
- - закріпити блок циліндрів на стенді, вивернути з переднього та заднього торців пробки масляного каналу та продути всі масляні канали стисненим повітрям
Завернути пробки на місце.
Якщо потрібна заміна картера зчеплення або він встановлюється на блок після ремонту, необхідно з блоку попередньо видалити два настановні штифти, потім картер закріпити на блоці болтами.
У блок на крайніх вкладках встановлюють колінчастий вал, до фланця якого кріпиться стійка індикатора.
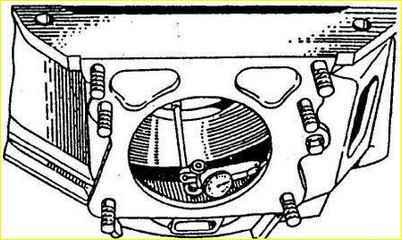
Обертаючи колінчастий вал, перевіряють биття отвору для центруючого бурта коробки передач, а також перпендикулярність заднього торця картера зчеплення щодо осі колінчастого валу, як показано на малюнку.
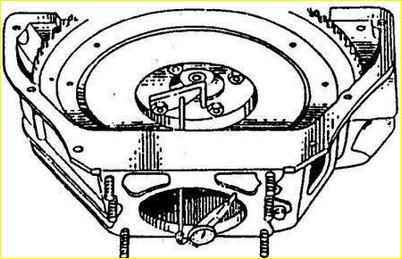
Биття отвору картера та торця не повинно перевищувати 0,3 мм, торця — 015 мм.
Якщо биття отвору перевищує вказану величину, слід послабити затяжку болтів і легкими ударами по фланцю картера домогтися правильної його установки.
Після затягування болтів отвору для настановних штифтів у картері та блоці розгортають до ремонтного розміру.
Чорнота в отворах не допускається. Після цього отвори запресовують штифти, діаметр яких на 0015-0051 мм більше розмірів отворів.
Биття торця картера усувається шабровкою.
Слід мати на увазі, що при вищеописаній перевірці необхідно користуватися незношеними колінчастим валом та вкладишами, які необхідно зняти після заміни картера;
- замінити дефектні гільзи циліндрів новими таким чином:
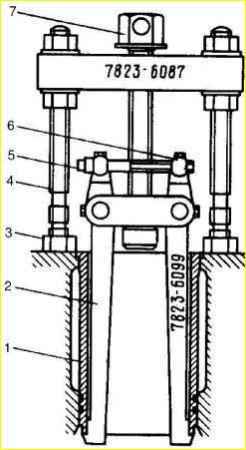
- а) за допомогою комбінованого зйомника випресувати стару гільзу.
Вставивши лапки з'ємника в циліндр двигуна, слід уперти шпильки 4 в блок і розсунути лапки розтискним болтом 5. далі, обертаючи гвинт 7, випресувати гільзу з циліндра;
- - б) ретельно очистити від накипу та корозії посадкові поверхні та поверхні ущільнення на гільзі та на блоці;
- - в) вставити відремонтовану гільзу з прокладкою з м'якої міді в циліндр, з якого вона була вийнята.
Гільза повинна входити в циліндр вільно, без зусиль і виступати над площиною блоку на 002-010 мм.
Зручніше перевірити величину потопання гільзи в циліндрі без прокладки. Потопання має бути в межах 020-025 мм;
- - г) закріпити гільзу утримувачем, щоб вона не випала;
- - відрізати від шнура два набивання заднього ущільнення колінчастого валу (довжиною 120 мм кожна), вкласти їх у блок та утримувач;
- - зробити підбір колінчастого валу, для цього вивернути всі пробки грязеуловлювачів шатунних шийок і видалити з них відкладення.
Промити та продути масляні канали та порожнини грязеуловлювачів стисненим повітрям, загорнути пробки моментом 38-42 Нм (38-4,2 кгсм);
- перевірити стан робочих поверхонь колінчастого валу.
Вибоїни, задираки та інші зовнішні дефекти не допускаються;
- - запресувати в задній кінець колінчастого валу кульковий підшипник 80203 АС9 із двома захисними шайбами. допускається використовувати підшипник 60203А з однією захисною шайбою, при цьому в порожнину для підшипника необхідно закласти 20 г мастила Літол-24
- - привернути до колінчастого валу маховик. Гайки затягнути моментом 76-83 Нм (7,6-8,3 кгсм).
Закінчити гайки, відігнувши один із вусів стопорної пластини на грань гайки;
- привернути до маховика натискний диск зчеплення в зборі з кожухом, попередньо відцентрувавши ведений диск за допомогою оправки (можна використовувати первинний вал коробки) по отвору в підшипнику в задньому торці колінчастого валу.
Мітки вибиті на кожусі натискного диска та на маховику біля одного з отворів для болтів кріплення кожуха повинні бути поєднані.
Затяжку болтів робити моментом 20-25 Нм (2,0-2,5 кгсм).
- колінчастий вал, маховик і зчеплення балансуються в зборі, і тому при замене На одній з цих деталей слід зробити динамічне балансування, висвердлюючи метал з маховика.
Балансування колінчастого валу, маховика та зчеплення в зборі не слід починати, якщо початковий дисбаланс перевищує 200 гсм.
У цьому випадку необхідно вузол розкомплектувати та перевірити балансування кожної деталі окремо
- надіти на першу корінну шийку колінчастого валу задню шайбу завзятого підшипника антифрикційним шаром до щоки колінчастого валу;
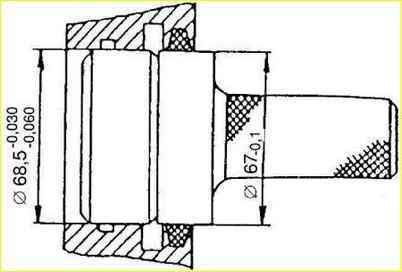
- - обжати набивання заднього ущільнення колінчастого валу в блоці та утримувачі оправкою
- - протерти чистою серветкою вкладки корінних підшипників та їх ліжка. Встановити вкладки в ліжку;
- - змастити чистою моторною олією вкладиші корінних підшипників і шийки колінчастого валу і укласти колінчастий вал у блок циліндрів;
- - надягти кришки корінних підшипників на шпильки блоку так, щоб фіксуючі виступи на верхньому і нижньому вкладках кожної кришки були з одного боку, а номери, вибиті на кришках, відповідали номерам ліжок.
Під час встановлення кришки переднього корінного підшипника вусик задньої шайби повинен увійти в паз кришки.
Торець кришки переднього підшипника має бути в одній площині з торцем блоку циліндрів;
- - посадити кришки корінних підшипників на свої місця легким постукуванням гумовим молотком, кришки повинні увійти в пази ліжок блоку циліндрів;
- - вдягнути на шпильки шайби, наживити гайки, нанести на різьбову частину гайок по 2-3 краплі (006 г) герметика «Унігерм-9» і рівномірно затягнути гайки.
Остаточну затяжку необхідно виконувати динамометричним ключем моментом 100-110 Нм (10-11 кг/см).
Якщо відсутня герметик, то стопоріння гайок можна виробляти стопорною пластиною 24-1005301-01;
- встановити в пази тримача набивання гумові прокладки та їх бічну поверхню, що виступає з паза, обмазати мильним розчином.
Встановити тримач на місце та затягнути гайки;
- повернути колінчастий вал, який повинен вільно обертатися при невеликому зусиллі.
Обертати колінчастий вал можна за маховик або за допомогою пристосування, що складається з первинного валу коробки з привареним до нього чотиригранником під ключ або ручку з квадратним отвором.
Пристрій може бути також використаний для центрування при постановці веденого диска зчеплення;
- - поставити передню шайбу завзятого підшипника антифрикційним шаром назовні, щоб штифти, запресовані в блок і кришку, входили в пази шайби;
- - надягти сталеву упорну шайбу колінчастого валу фаскою у внутрішньому отворі у бік передньої шайби завзятого підшипника;
- - напресувати до упору шестерню колінчастого валу та перевірити його осьовий зазор.
Перевірка проводиться таким чином: закласти викрутку (вороток, рукоятку молотка тощо) між першим кривошипом валу та передньою стінкою блоку і, користуючись нею як важелем, віджати вал до задньої частини двигуна.
За допомогою щупа визначити зазор між торцем задньої шайби завзятого підшипника та площиною бурта першої корінної шийки. Зазор має бути в межах 0,125-0,325 мм;
- зробити підбір шатунно-поршневої групи
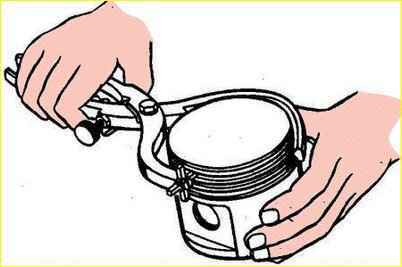
Очистити днища поршнів та канавки поршневих кілець від нагару.
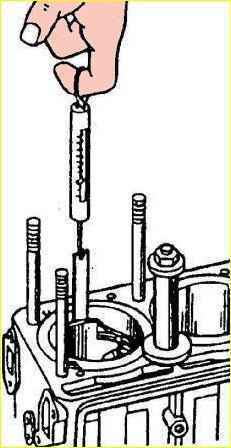
У разі заміни поршнів, гільз, поршневих пальців або шатунів підскладання пар, що сполучаються, слід проводити при температурі деталей (20±3)° С.
У розточені чи нові гільзи необхідно встановлювати поршні однакових із гільзою розмірних груп. допускається підбір із сусідніх груп, при цьому, як і при підборі поршнів у гільзи, що працювали, підбір проводиться за зусиллям протягування стрічки-щупа товщиною 0,05 мм і шириною 10 мм.
Стрічка-щуп розміщується в площині перпендикулярної осі поршневого пальця, по найбільшому діаметру поршня. Зусилля на динамометрі, з'єднаному зі стрічкою-щупом, має бути 35-55 Н (3,5-5,5 кгс);
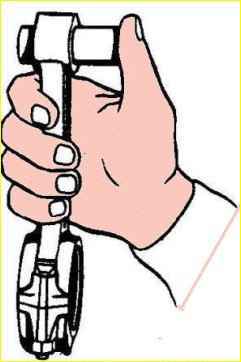
- підібрати поршневий палець до шатуна так, щоб він щільно входив в отвір шатуна під зусиллям великого пальця руки, переміщався вільно, без заїдань і не випадав під дією власної маси при розташуванні осі отвору шатуна під кутом 45 ° (орієнтовно).
Поршневий палець і шатун повинні бути однієї або суміжної розмірної групи.
При підборі поршневий палець повинен бути змащений моторним маслом. Розмірні групи поршня та поршневого пальця мають збігатися.
Поршень з поршневим пальцем, поршневими кільцями та шатуном у зборі повинні контролюватись за масою. Різниця в масі на один двигун не повинна перевищувати 12 г;
- запресувати поршневий палець у поршень і шатун за допомогою пристосування.
Поршень при цьому нагріти до температури 60-88 ° С, поршневий палець злегка змастити моторним маслом.
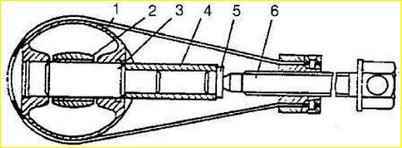
Поршень з'єднати напрямною оправкою 3 з шатуном, надягти поршневий палець на тонкий кінець оправки, як показано на надіти підп'ятник 5 на палець і гвинтом 6 надіслати палець на місце.
Запресування пальця в холодний поршень може призвести до псування поверхні отворів у бобишках поршня, а також до деформації самого поршня.
Під час встановлення поршня в циліндр (по мітці «ПЕРЕД» на поршні) отвір для змащення дзеркала циліндра з нижньої головки шатуна повинен бути звернений у бік, протилежний розподільчому валу;
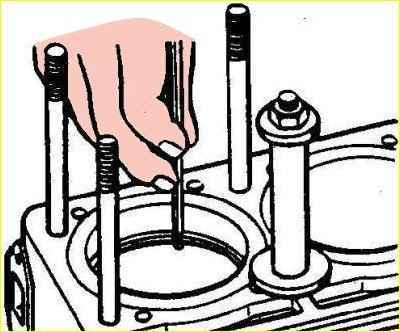
- підібрати по циліндру поршневі кільця, як показано на малюнку.
Зазор, заміряний у стиках кілець, повинен бути 03-0,7 мм у компресійних кілець і 0,3-1,0 мм у сталевих дисків олійного кільця.
У зношених циліндрах найменший зазор — 0,3 мм;
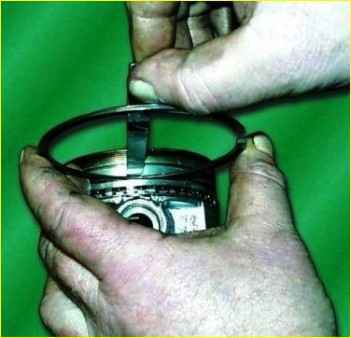
- щупом перевірити зазор між кільцями та стінкою поршневої канавки, як показано на малюнку.
Перевірку по колу поршня в кількох точках.
Величина зазору повинна бути для верхнього та нижнього компресійних кілець у межах 0,050—0,870 мм, для збірного маслознімного кільця — 0,135—0,335 мм;
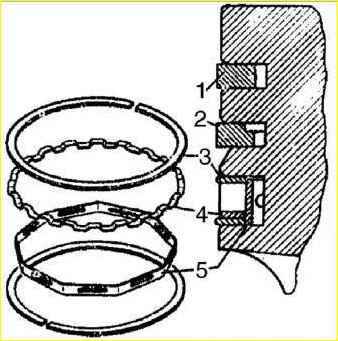
- одягнути на болти шатунів запобіжні латунні наконечники, стиснути кільця обтисканням або, користуючись конусним кільцем, вставити поршень у циліндр, як показано на малюнку.
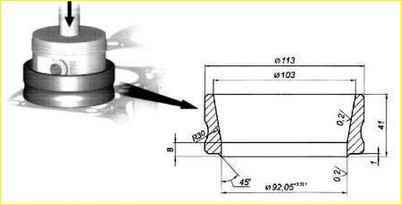
Перед встановленням поршня слід ще раз переконатися, що номери, вибиті на шатуні та його кришці, відповідають порядковому номеру циліндра, перевірити правильність положення поршня та шатуна в циліндрі;
- підтягнути шатун за нижню головку до шатунної шийки, зняти з болтів латунні наконечники, надіти кришку шатуна.
Кришку шатуна слід ставити так, щоб номери, вибиті на кришці та шатуні, були звернені в один бік.
Після наживлення гайок нанести на різьбову частину гайок по 2-3 краплі (0,06 г) герметика «Унігерм-9» та рівномірно затягнути гайки.
Остаточну затяжку гайок необхідно зробити динамометричним ключем моментом 68-75 Нм (6,8-7,5 кг/см).
У разі використання деталей, що працювали з гайок і болтів, необхідно видалити залишки раніше застосованого герметика, знежирити їх бензином і просушити;
- - в такому самому порядку вставити поршень четвертого циліндра;
- - повернути колінчастий вал на 180° і вставити поршні другого та третього циліндрів;
- - повернути кілька разів колінчастий вал, який повинен легко обертатися від невеликого зусилля;
- - зробити підбір розподільного валу в наступному порядку:
- - надіти на передній кінець розподільного валу розпірне кільце та упорний фланець;
- - напресувати за допомогою пристосування шестерню розподільного валу та закріпити її болтом із шайбою. Момент затяжки - 55-60 Нм (5,5-6,0 кг/см);
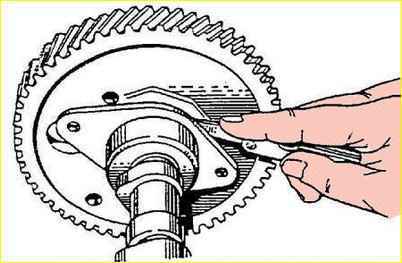
- - за допомогою щупа, що вставляється між упорним фланцем розподільчого валу і маточиною шестерні, встановити осьовий зазор
- - прочистити трубку мастила розподільних шестерень і привернути її за допомогою болта та хомутика до блоку; розподільчого валу. Зазор повинен бути не більше 0,1—0,2 мм;
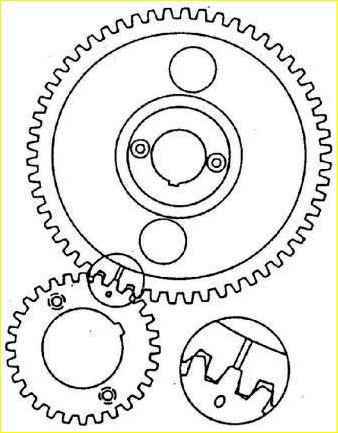
- вставити підібраний розподільний вал в отвір блоку, змастивши попередньо його опорні шийки моторним маслом.
При зачепленні шестерень зуб шестерні колінчастого валу з Міткою «0» має бути проти ризику у западини зубів шестерні розподільчого валу.
Бічний зазор у зачепленні має бути в межах 0,025—0,1 мм.
При більшому або меншому зазорі підібрати іншу пару шестерень;
- - через отвори в шестірні розподільного валу прикріпити двома болтами з пружинними шайбами завзятий фланець до блоку;
- - встановити на шию переднього кінця колінчастого валу масловідбивач опуклою стороною до шестерні;
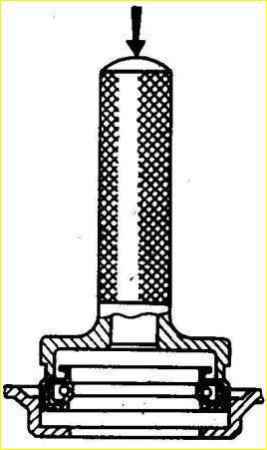
- перевірити придатність манжети, запресованої в кришку розподільних шестерень, для подальшої роботи.
Якщо манжета має зношені робочі кромки або слабо охоплює маточину шківа колінчастого валу, вставлену в манжету, замінити її новою.
Запресовування манжети в кришку рекомендується проводити за допомогою оправки, як показано на малюнку.
- одягнути на шпильки прокладки кришку розподільних шестерень;
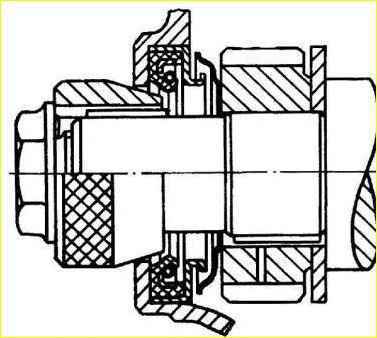
- сконцентрувати кришку по передньому кінці колінчастого валу за допомогою оправки та загорнути всі гайки та болти кріплення кришки.
Якщо немає центруючої оправки, то установку кришки можна проводити по маточці шківа колінчастого валу.
Ступицю треба напресувати на колінчастий вал так, щоб її кінець входив на глибину 5 мм в отвір кришки.
Після цього закріпити кришку гайками, витримуючи однаковий зазор по колу між маточкою та отвором кришки.
Вирівнювання зазору проводити легкими ударами дерев'яного або гумового молотка по кришці. Після цього остаточно закріпити кришку;
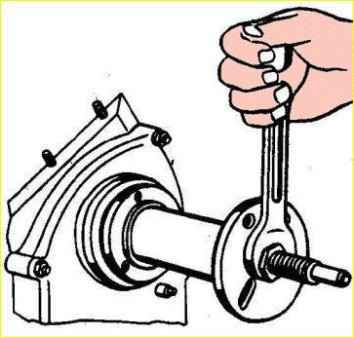
- - видалити центруючу оправку та напресувати маточину шківа зі шківом-демпфером колінчастого валу
- - вставити в шпонковий паз гумову пробку та запресувати шпонку;
- - завернути в носок колінчастого вала стяжний болт, попередньо вдягнувши на нього зубчасту шайбу.
Провертаючи за стяжний болт колінчастий вал, перевірити, чи не зачіпає шків-демпфер за кришку розподільних шестерень; - встановити масляний насос у зборі з маслоприймачем;
- - встановити привод масляного насоса та датчика розподільника запалювання в наступному порядку:
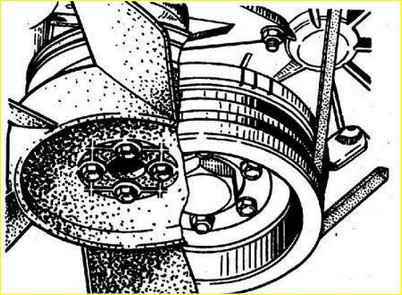
- повертаючи колінчастий вал, поєднати третю мітку на диску демпфера з ребром-покажчиком на кришці розподільних шестерень.
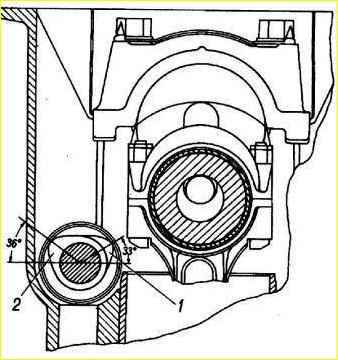
Кулачки розподільного валу, що приводять у дію клапани першого циліндра, повинні бути при цьому спрямовані вершинами в протилежну від штовхачів сторону (у бік масляного картера) і розташовані симетрично
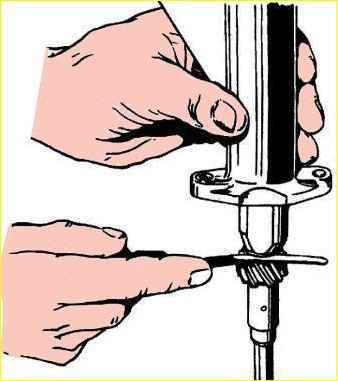
- - перевірити осьовий зазор між корпусом приводу та шестернею за допомогою щупа
- - надіти на шпильки кріплення приводу прокладку; Зазор повинен бути не більше 0,15—0,40 мм;
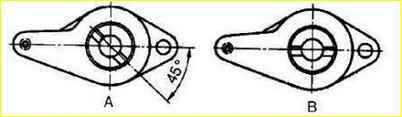
- повернути валик приводу в положення, показане на "А", і поставити привід у гніздо блоку.
При введенні приводу в гніздо необхідно злегка повертати валик масляного насоса, щоб кінець валика приводу увійшов у отвір вала насоса.
Привод повинен вставлятися без значних зусиль.
У правильно встановленому приводі проріз у втулці валика має бути спрямований паралельно осі двигуна і зміщений від двигуна, як показано на "В";
- закріпити привід;
- - перевірити наявність зазору в шестернях розподільчого валу та приводу;
- - змастити стики нижнього фланця блоку циліндрів з кришкою розподільчих шестерень та тримачем набивання клеєм-герметиком «Еластосил 1З7-8З» або пастою УН-25;
- - встановити на нижній фланець блоку циліндрів прокладку масляного картера;
- - встановити масляний картер на шпильки та закріпити його гайками з шайбами, рівномірно затягуючи гайки;
- - встановити та привернути болтами нижню частину картера зчеплення;
- - очистити камери згоряння та канали головки циліндрів від нагару та відкладень, протерти та продути стиснутим повітрям;
- - притерти клапани, використовуючи пасту притирочку, складену з однієї частини мікропорошку М-20 і двох частин масла І-20А.
Перед початком притирання слід перевірити, чи немає короблення тарілки клапана та прогорання клапана та сідла.
За наявності цих дефектів відновити герметичність клапана одним притиранням неможливо і слід спочатку прошліфувати сідло, а пошкоджений клапан замінити новим.
Якщо зазор між клапаном та втулкою перевищує 0,25 мм, то герметичність також не може бути відновлена. У цьому випадку клапан та втулку слід замінити новими.
Клапани (в запасні частини) випускаються стандартного розміру, а напрямні втулки — із внутрішнім діаметром, зменшеним на 0,38 мм (для розгортання їх під остаточний розмір після запресування в головку циліндрів).
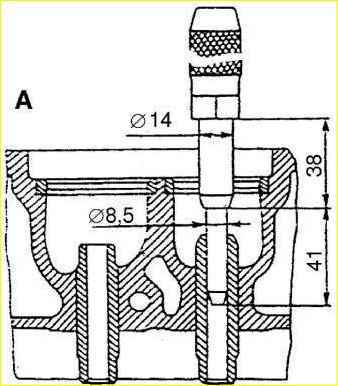
Випресування зношеної напрямної втулки здійснюється за допомогою оправки.
Сідла клапанів видаляються фрезеруванням твердосплавним зенкером.
Ремонтні сідла мають зовнішній діаметр на 0,25 мм більше, ніж стандартні, тому гнізда для сідел розточуються до наступних розмірів: для сідла впускного клапана — 49,25+0,025 мм, для випускного — 42,25+0,025 мм.
Сідла направляючі втулки перед складанням треба охолодити у двоокисі вуглецю (сухим льоду), а головку циліндрів нагріти до температури 160-175° С.
Сідла та втулки при складанні повинні вставлятися в гнізда голівки вільно або з легким зусиллям.
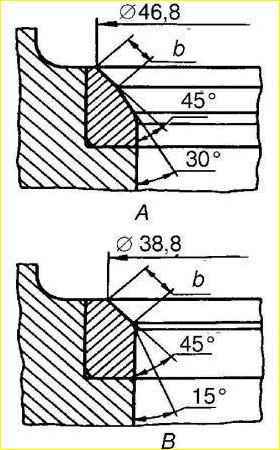
Запресування нових втулок впускного та випускного клапанів проводиться до виступу над головкою на 20 мм після запресування розгорнути отвори втулок до діаметра 9+0,022 мм, а фаски сідла прошліфувати, центруючи по отвору у втулці.
При шліфуванні слід забезпечити концентричність фаски на сідлі клапана з отвором у втулці в межах 0,05 мм. Фаски шліфують під кутом 45 °.
Зовнішній діаметр фаски у сідла для впускного клапана має бути 46,8 мм, а у випускного – 38,8 мм.
Ширина фаски має бути у сідла впускного клапана 1,8 - 2,3 мм., У випускного - 2,3-2,5 мм.
Ширина фаски забезпечується розшліфуванням отвору сідла впускного клапана під кутом 30°, як показано на "А", а випускного клапана - під кутом 15° клапана "В". Фаска має бути однаковою по всьому периметру.
Після шліфування сідел та притирання клапанів усі газові канали ретельно очистити та продути стиснутим повітрям, щоб не залишилося абразивного пилу;
- - стрижні клапанів обмазати тонким шаром колоїдного графіту, розведеного в маслі, що застосовується для двигуна, або змастити маслом
- - на направляючі втулки клапанів напресувати маслознімні ковпачки, вставити клапани у втулки згідно зробленим міткам і зібрати їх із пружинами. Переконатися, що сухарі увійшли до кільцевої канавки клапанів;
- натерти графітовим порошком з обох боків прокладку головки циліндрів і надіти її на шпильки.
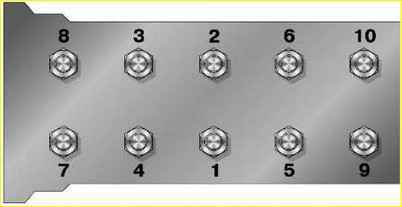
Встановити голівку та закріпити її гайками із шайбами. Затягнути гайки динамометричним ключем моментом 83-90 Нм (8,3-9,0 кг/см), дотримуючись порядку
- прочистити дротом і продути стисненим повітрям отвори в коромислах, осі коромисел і регулювальних гвинтах, четвертій основній стійці осі коромисел і масляні канали в головці циліндрів.
Перевірити надійність посадки втулок коромисел.
У разі слабкої посадки під час роботи втулка може зміститися та перекрити отвір для змащування штанги штовхача клапана. Такі втулки необхідно замінити;
- підскладання осі коромисел.
Перед постановкою кожного коромисла змастити його втулку моторним маслом;
- - вставити штовхачі у гнізда згідно з мітками на них. Товкачі та отвори в блоці попередньо змастити моторним маслом;
- - вставити штанги в зборі з наконечниками в отвори в головці циліндрів;
- - встановити підзбирану вісь коромисел на шпильки та закріпити гайками із шайбами. Регулювальні болти своєю сферичною частиною повинні лягати на сферу верхнього наконечника штанги;
- - встановити зазори між торцями стрижнів клапанів та носиками коромисел. Зазор між коромислами та першим та восьмим клапанами — 0,35-0,40 мм, зазор між рештою коромислами та клапанами — 0,40-0,45 мм.
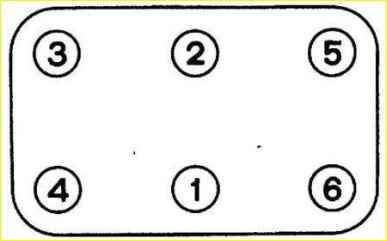
- - поставити прокладку та кришку коромисел і закріпити їх болтами з шайбами, дотримуючись правильності затягування, згідно з малюнком.
- - змастити та надіти на передню кришку коробки передач муфту вимкнення зчеплення.
- - встановити та закріпити коробку передач;
- - встановити вилку вимкнення зчеплення;
- - встановити деталі та агрегати двигуна, названі у статті «Розбір двигуна ЗМЗ-402 ГАЗ-2705»