Realizamos reparaciones de culata durante reparaciones generales del motor y al sustituir la junta de culata
Es muy importante reparar el cabezal después de que el motor se haya sobrecalentado.
Durante el sobrecalentamiento, pueden producirse defectos que pueden no ser visibles visualmente
Por lo tanto, es necesario realizar con cuidado todas las operaciones para reparar la culata.
De esto depende en gran medida el funcionamiento del motor. Y esto le evitará trabajos y costes innecesarios.
Vemos cómo quitar la culata en el artículo - Junta de culata ZMZ 405 GAZ-2705
Desmontaje de la culata
Desatornillar las tuercas 1 y quitar la rejilla 5 del sensor de fase, el soporte 2 de elevación del motor y el colector de escape 6.
Retire las juntas del colector de escape.
Desatornille el perno 3 y retire el sensor de 4ª fase.
Desatornille el sensor de presión de aceite de emergencia 7 y el indicador de presión de aceite 8.
Afloje la abrazadera 1 y retire la manguera del tubo regulador de aire inactivo.
Desatornille las tuercas 2 y retire el receptor 3 del tubo de entrada.
Retire la junta del receptor.
Desatornille las tuercas 1 y retire el tubo de admisión 2 junto con los inyectores y la línea de combustible (no se muestra en la foto).
Retire la junta del tubo de admisión.
Desatornille los tornillos 1 y retire la tapa trasera 2 de la cabeza del bloque.
Retirar la junta de la tapa
Extraiga los elevadores de válvulas hidráulicas 1. Es más cómodo retirar los empujadores hidráulicos mediante un imán o ventosa
Los empujadores hidráulicos no se pueden intercambiar, por lo que antes de desmontarlos se deben marcar para poder instalarlos en su lugar durante el montaje.
Los elevadores hidráulicos deben almacenarse en la misma posición que están en las válvulas, para que no se escape aceite de ellos.
Si el diseño del extractor no proporciona un tope de válvula, coloque un tope adecuado debajo.
Comprima los resortes con un desecante.
Para que la placa de resorte sea más fácil de retirar de las galletas, puedes aplicar un ligero golpe con un martillo en el bípode persistente del desecante.
Utiliza unas pinzas para quitar dos galletas y suelta suavemente los resortes.
Retire la placa superior y los dos resortes de válvula.
Utilice un extractor para quitar el tapón de aceite...
Utiliza un destornillador y retira la arandela de soporte 1 de los resortes de las válvulas.
Dar la vuelta Retire el bloque de cilindros y retire la válvula, marcando su lugar de instalación para que durante el posterior montaje la válvula vuelva a su lugar original. Del mismo modo retiramos y marcamos el resto de válvulas.
Presionamos las guías de válvulas desgastadas con un mandril
Utilice una llave hexagonal de “8” para desenroscar los tapones del canal de aceite
Inspección, resolución de problemas y reparación de la culata
Después de desmontar la culata, lave todas las piezas con gasolina, límpielas y séquelas. Limpiar las cámaras de combustión y las válvulas de los depósitos de carbón.
Inspeccione el cabezal del bloque.
Si hay grietas en los puentes entre los asientos de las válvulas, marcas de quemaduras y grietas en las paredes de la cámara de combustión, reemplace la culata.
Compruebe utilizando una regla de metal y galgas de espesores para ver si la planitud de la superficie de la cabeza adyacente al bloque está rota.
Para hacer esto, coloque la regla con su borde en la superficie de la cabeza del bloque, en el medio, a lo largo y luego a lo ancho, y use una galga de espesores para medir el espacio entre la superficie de la cabeza y la regla. Si el espacio supera los 0,1 mm, reemplace el cabezal.
Compruebe las holguras en los cojinetes del árbol de levas.
Compruebe los espacios entre los elevadores de válvulas hidráulicas y los canales para los elevadores hidráulicos en la culata.
La holgura se calcula como la diferencia entre el diámetro del canal y el diámetro del empujador hidráulico.
El diámetro nominal del canal para el empujador hidráulico es de 35,0 +0,025 mm, el máximo permitido es de 35,1 mm.
El diámetro nominal del empujador hidráulico es 35,0 -0,025 y 35,0 -0,041 mm, el diámetro máximo permitido es 34,95 mm. La separación máxima permitida es de 0,15 mm.
Si el espacio excede el valor especificado, reemplace el empujador hidráulico. Si esto no da un resultado positivo, reemplace el cabezal del bloque.
Inspeccione las válvulas.
Si se detectan grietas, deformación de la cabeza de la válvula, quemado o deformación del vástago en la cara de trabajo de la válvula, se debe reemplazar la válvula.
Las pequeñas marcas y rayones en la cara de trabajo de la válvula se pueden eliminar lapeando.
La válvula se muele en el asiento de la siguiente manera:
- - inserte la válvula en el cabezal del bloque;
- - colocar un dispositivo rectificador de válvulas en el vástago de la válvula;
- - aplique una fina capa de pasta para pulir, que es una mezcla de polvo abrasivo fino con aceite de motor, en el chaflán de trabajo de la válvula;
- - girar la válvula utilizando el dispositivo en ambas direcciones, presionándola periódicamente contra el asiento.
Un signo externo de un lapeado satisfactorio es el color gris mate uniforme del bisel de trabajo del asiento y la válvula.
Después del pulido, limpie el asiento y la válvula con un paño limpio y enjuáguelos bien para eliminar cualquier resto de pasta de pulido.
Para comprobar el apriete de la válvula, instálela en el cabezal del bloque junto con los resortes y chavetas.
Después de esto, coloque la cabeza del bloque de lado y vierta queroseno en el canal cerrado por la válvula. Si dentro de los 3 min. El queroseno no se filtrará a la cámara de combustión; la válvula se considera sellada.
Compruebe el estado de los resortes de las válvulas. Los resortes que estén doblados, agrietados o rotos deben reemplazarse.
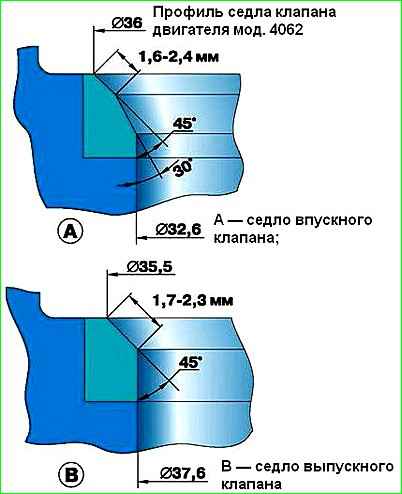
Compruebe el estado de los asientos de las válvulas. Los chaflanes de trabajo de los asientos no deben presentar signos de desgaste, agujeros, corrosión, etc.
Los daños menores (pequeñas marcas, rayones, etc.) se pueden eliminar rectificando las válvulas.
Los defectos más importantes se pueden eliminar mediante esmerilado. Al rectificar, mantenga las dimensiones del asiento indicadas en la figura
Después del pulido, verifique el descentramiento del chaflán del asiento en relación con el orificio en la guía de la válvula; el descentramiento máximo permitido es de 0,05 mm.
Después de rectificar, rectificar las válvulas.
A continuación, limpie a fondo y sople la culata con aire comprimido para que no queden partículas abrasivas en los canales cerrados por las válvulas y en las cámaras de combustión.
Cabe señalar que después de pulir el asiento, la válvula se asienta más profundamente en el asiento.
Por lo tanto, después del pulido, es necesario medir la distancia entre el extremo del vástago de la válvula presionado contra el asiento y el eje del árbol de levas.
Si esta distancia es inferior a 35,5 mm, sustituir la culata, ya que en este caso se altera el funcionamiento normal de los taqués.
Compruebe los espacios entre los casquillos guía y las válvulas.
El espacio se calcula como la diferencia entre el diámetro del orificio en el casquillo y diámetro del vástago de la válvula. La separación máxima permitida es de 0,2 mm.
Si el espacio excede el valor especificado, reemplace la válvula y el manguito guía.
El casquillo viejo se extrae mediante un mandril desde el lateral de la cámara de combustión.
Instale casquillos nuevos con anillos de retención colocados hasta que el anillo de retención se detenga en el plano de la cabeza del bloque en el lado del orificio para los empujadores hidráulicos.
Antes de la instalación, los casquillos deben enfriarse a –40...45 °C y el cabezal del bloque debe calentarse a una temperatura de +160-175 °C.
El casquillo debe introducirse en el cabezal del bloque libremente o con poca fuerza.
Las guías de válvula se suministran como repuestos en tres tamaños de reparación.
El primer tamaño de reparación con el diámetro exterior del casquillo aumentó en 0,02 mm.
El segundo es el diámetro exterior del manguito 14,2 +0,053 y 14,2 +0,040 mm, el tercero tiene un diámetro aumentado en 0,02 mm con respecto al segundo tamaño.
Al instalar casquillos del primer tamaño de reparación, no taladre el orificio para el casquillo en la cabeza del bloque.
Al instalar casquillos del segundo y tercer tamaño de reparación, debe perforar el orificio con un diámetro de 14,2 -0,023 y 14,2 -0,050 mm.
Después de instalar los nuevos casquillos, expanda el orificio para las válvulas en ellos hasta las dimensiones indicadas en la tabla. 2.1. Luego muela los asientos de las válvulas como se indica arriba.
Para comprobar si hay grietas en la cabeza del bloque, debe conectar una manguera de aire comprimido a uno de los orificios de la camisa de refrigeración.
Tape todos los agujeros del cabezal con tapones de madera. Sumerja el cabezal en un baño de agua y aplique aire comprimido a una presión de 1,5 atm. En los lugares donde haya grietas saldrán burbujas de aire.
Una vez limpiado el plano de contacto del cabezal, comprobamos con una regla la calidad del ajuste del cabezal al bloque.
Si la deformación supera los 0,05 mm, se debe restaurar la planitud mediante tratamiento mecánico, sin embargo, si la falta de planitud supera los 0,1 mm, la cabeza no se repara.
Utilice queroseno o combustible diésel para enjuagar el cabezal y limpiar los depósitos de los canales de aceite.
Luego limpiamos las superficies con un trapo limpio y soplamos los canales con aire comprimido. Reemplace los tapones del canal de aceite
Presionamos casquillos de válvula nuevos a través de un espaciador de aluminio, precalentamos el cabezal a 160-180 °C y enfriamos los casquillos en “hielo seco” (CO 2).
Instale las válvulas en el orden inverso al de extracción, reemplazando los sellos de aceite viejos por otros nuevos
Lapeado de válvulas
Aplique pasta de lapeado al chaflán de la válvula e instálela en el casquillo del cabezal correspondiente.
Coloque un dispositivo de lapeado en el vástago de la válvula y, presionando la válvula contra el asiento, gírela en ambas direcciones aproximadamente 90°
Continuamos rectificando hasta que el chaflán de sellado de la válvula en todo su ancho y largo quede mate y limpio.
El chaflán del asiento de la válvula también debería tener este aspecto. Limpia cualquier resto de pasta de la válvula y del asiento con un trapo.
Monte la culata en orden inverso.