Reinigen Sie alle Passflächen des Blocks von festsitzenden und gerissenen Dichtungen, die bei der Demontage entstanden sind
Befestigen Sie den Zylinderblock am Ständer, überprüfen Sie sorgfältig den Zylinderspiegel und entfernen Sie ggf. den ungetragenen Riemen über dem oberen Kompressionsring mit einem Schaber. Das Metall sollte bündig mit der verschlissenen Oberfläche des Zylinders entfernt werden.
Entfernen Sie die Ölkanalstopfen und blasen Sie alle Ölkanäle mit Druckluft aus. Schrauben Sie die Stopfen fest.
Bauen Sie die Kurbelwelle zusammen, indem Sie die Stopfen der Schmutzfänger der Pleuellagerzapfen abschrauben und Ablagerungen von ihnen entfernen, spülen und mit Luft ausblasen, die Stopfen einsetzen und sie mit einem Drehmoment von 37-51 Nm (3,8- 5,2 kgcm).
Für eine zuverlässige Verriegelung tragen Sie das anaerobe Dichtmittel Stopor-9 auf die Gewinde der Stopfen auf.
Überprüfen Sie den Zustand der Arbeitsflächen der Kurbelwelle. Kerben, Grate und andere äußere Mängel sind nicht zulässig.
Wischen Sie das Bett unter den Laufbuchsen im Block und in den Hauptlagerdeckeln mit einer Serviette ab.
Montieren Sie die oberen Hauptlagerschalen (mit Rillen und Löchern) im Blockbett und die unteren (ohne Rillen) im Abdeckbett, wischen Sie die Lager mit einem Tuch ab und schmieren Sie sie mit Motoröl.
Wischen Sie die Haupt- und Pleuellagerzapfen der Kurbelwelle mit einer Serviette ab, schmieren Sie sie mit sauberem Öl und bauen Sie die Kurbelwelle in den Zylinderblock ein.
Die Drucklager-Halbscheiben schmieren und einbauen:
- - oben – in den Rillen des dritten Hauptbetts mit einer Gleitschicht mit Rillen zur Wange der Kurbelwelle;
- - unten - zusammen mit der Abdeckung des dritten Hauptlagers. Die Vorsprünge der unteren Halbscheiben sollten in die Nuten der Abdeckung passen;
Montieren Sie die Abdeckungen der verbleibenden Stützen auf den entsprechenden Hauptlagerzapfen, schrauben Sie die Schrauben ein, mit denen die Hauptlagerabdeckungen befestigt sind, und ziehen Sie sie mit einem Drehmoment von 98–107,9 Nm (10–11 kgcm) fest.
Auf der Unterseite der 1., 2. und 4. Hauptkappe sind deren Seriennummern eingeprägt.
Auf der Unterseite der dritten Hauptträgerabdeckung befindet sich ein Gewindeloch zur Befestigung des Ölpumpenhalters und auf den Seitenflächen befinden sich Nuten und Nuten zur Montage von Halbscheiben.
Die Abdeckungen der Hauptstützen werden entsprechend ihrer Nummerierung montiert und so ausgerichtet, dass sich die Nuten für die Auskleidungsnase in der Abdeckung und im Block auf einer Seite befinden.
Drehen Sie die Kurbelwelle. Ihre Drehung sollte ohne großen Kraftaufwand möglich sein.
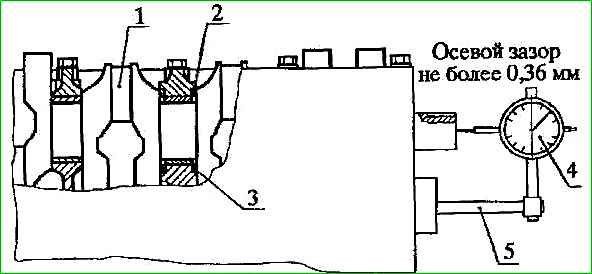
Überprüfen Sie das Axialspiel der Kurbelwelle (Abbildung 1), das nicht mehr als 0,36 mm betragen sollte. Bei ungetragenen Kurbelwellen- und Axiallager-Halbscheiben beträgt das Spiel 0,06–0,27 mm.
Wenn das Axialspiel den maximal zulässigen Wert überschreitet, ersetzen Sie die Anlaufscheiben durch neue und messen Sie das Axialspiel erneut. Wenn sich bei der Messung herausstellt, dass es mehr als 0,36 mm beträgt, ersetzen Sie die Kurbelwelle.
Nehmen Sie den Wellendichtringhalter mit dem Wellendichtring am hinteren Ende der Kurbelwelle und prüfen Sie die Eignung des Wellendichtrings für weitere Arbeiten.
Wenn die Öldichtung abgenutzte Arbeitskanten aufweist oder den Kurbelwellenflansch nur schwach abdeckt, ersetzen Sie sie durch eine neue.
Es wird empfohlen, den Wellendichtring mit einem Dorn in den Wellendichtringhalter zu drücken.
Die Öldichtung muss so eingebaut werden, dass sich die Manschette an der Außenseite des Motors befindet und die von der Feder abgedeckte Arbeitskante nach innen zeigt.
Tragen Sie vor dem Pressen Litol-24-Schmiermittel auf die Außenfläche der Öldichtung auf, um das Pressen zu erleichtern.
Füllen Sie ⅔ des Hohlraums zwischen der Arbeitskante und der Manschette der Gummimanschette mit CIATIM-221-Schmiermittel, installieren Sie den Öldichtungshalter und befestigen Sie ihn mit der Dichtung am Zylinderblock.
Montieren Sie das Schwungrad am hinteren Ende der Kurbelwelle und richten Sie dabei das Stiftloch im Schwungrad mit dem in den Kurbelwellenflansch gedrückten Positionierungsstift aus.
Setzen Sie die Unterlegscheibe der Schwungradschrauben ein, befestigen Sie die Schrauben und ziehen Sie sie mit einem Drehmoment von 70,6–78,4 Nm (7,2–8,0 kgf) fest.
Drücken Sie die Distanzhülse und das Lager in den Schwungradsitz. Drücken Sie das Lager hinein und üben Sie dabei Kraft auf den Außenring aus. Durch Einpressen in den Innenring wird das Lager beschädigt.
Als nächstes montieren wir die Pleuel- und Kolbengruppe – Artikel So montieren Sie die Pleuel- und Kolbengruppe des ZMZ-40524-Motors
Befestigen Sie den Halter an der Ölpumpe.
Montieren Sie die Ölpumpe mit der Dichtung auf der Passfläche des Zylinderblocks und befestigen Sie sie.
Schneiden Sie die überstehenden Enden der Kettenabdeckungsdichtungen und der Öldichtungshalterdichtungen ab, die über die Ebene des Blocks, der Kettenabdeckung und des Öldichtungshalters hinausragen.
Ölwanne mit Dichtung und Kupplungsgehäuseverstärker einbauen und sichern.
Die Zwischenwellenbuchsen und -lippen mit Motoröl schmieren Setzen Sie den Segmentschlüssel wieder in die Nut am Ende der Zwischenwelle ein und installieren Sie die Zwischenwelle im Zylinderblock.
Schrauben Sie zwei Schrauben in den vorderen Flansch der Zwischenwelle.
Montieren Sie das Zahnrad mit der Mutter am hinteren Ende der Welle, richten Sie die Keilnut des Zahnrads mit der Passfeder aus, drehen Sie die Zwischenwelle mit zwei Schrauben und ziehen Sie die Zahnradmutter bis zum Anschlag fest.
Zwischenwellenflansch montieren und sichern.
Schmieren Sie die Antriebswelle und die Zähne der Ölpumpe mit Motoröl und führen Sie die Rolle in das Loch im Block ein, bis die Antriebsräder der Ölpumpe und die Zwischenwelle ineinandergreifen.
Führen Sie die Sechskantwelle des Ölpumpenantriebs so in das Loch in der Antriebswellenbuchse ein, dass sie in das Sechskantloch der Ölpumpenwelle passt.
Montieren Sie die Antriebsabdeckung der Ölpumpe und befestigen Sie sie mit der Dichtung.
Überprüfen Sie, ob sich die Zwischenwelle leicht drehen lässt. Die Welle sollte sich frei drehen können, ohne zu blockieren.
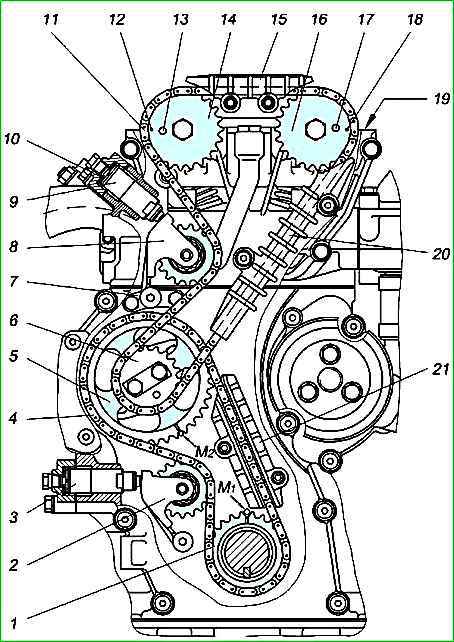
Einbau des Nockenwellenantriebs (Abbildung 2):
Drücken Sie den Segmentschlüssel in die Keilnut am vorderen Ende der Kurbelwelle.
Drücken Sie das Kettenrad mit einem Spezialwerkzeug auf die Motorkurbelwelle, wobei die Markierung nach vorne zeigt.
Setzen Sie den Gummi-O-Ring in die Nut am vorderen Ende der Kurbelwelle ein.
Drehen Sie die Kurbelwelle des Motors, bis die Markierung am Kurbelwellenrad mit der Markierung „M1“ am Zylinderblock übereinstimmt, was der Position des Kolbens des ersten Zylinders am oberen Totpunkt entspricht.
In diesem Fall sollte die Markierung auf dem Zylinderblock symmetrisch zur Achse des Hohlraums der Kettenradzähne liegen.
Montieren Sie die untere Kettenführung, ohne die Befestigungsschrauben vollständig festzuziehen, nachdem Sie zuvor das anaerobe Dichtmittel „Stopor - 6“ auf die Schraubengewinde aufgetragen haben.
Legen Sie die untere Kette auf das angetriebene Kettenrad (38 Zähne) der Zwischenwelle und auf das Kurbelwellenritzel des Motors.
Montieren Sie das Kettenrad mit der Kette auf der Zwischenwelle, wobei die Markierung auf dem angetriebenen Kettenrad der Zwischenwelle mit der Markierung „M2“ am Zylinderblock übereinstimmen muss und der Antriebszweig der Kette, der durch den Dämpfer verläuft, muss gespannt sein.
Montieren Sie das Antriebsritzel der Zwischenwelle mit einem Stift und befestigen Sie beide Ritzel mit Schrauben mit einem Drehmoment von 24,5–26,5 Nm (2,5–2,7 kgf) an der Zwischenwelle. Biegen Sie die beiden Ecken des Sicherungsblechs an den Kanten der Schraubenköpfe.
Montieren Sie den Spannhebel mit dem Kettenrad der unteren Nockenwellen-Antriebskette und befestigen Sie ihn mit der Hebelschraube, nachdem Sie zuvor anaerobes Dichtmittel Stopor-6 auf die Schraubengewinde aufgetragen haben.
Wenn Sie zu viel Dichtmittel auftragen, wird es aus dem Gewinde herausgedrückt und der Spannhebel wird auf der Achse blockiert.
Drücken Sie den Spannhebel, spannen Sie die Kette, prüfen Sie, ob die Kettenräder entsprechend den Markierungen richtig montiert sind, und ziehen Sie die Schrauben des unteren Dämpfers fest.
Nach dem Einbau der unteren Kette darf sich die Kurbelwelle nicht drehen, bis die Nockenwellenantriebskette und die hydraulischen Spanner eingebaut sind.
Montieren Sie die Schraubenhalterung für den Spannhebel und befestigen Sie sie mit Schrauben, nachdem Sie zuvor anaerobes Dichtmittel Stopor-6 auf die Schraubengewinde aufgetragen haben.
Montieren Sie den Spannhebel mit dem Kettenrad der oberen Nockenwellen-Antriebskette und befestigen Sie die Hebelschraube an der Halterung, nachdem Sie zuvor anaerobes Dichtmittel Stopor-6 auf die Schraubengewinde aufgetragen haben.
Legen Sie die Antriebskette der oberen Nockenwelle auf das Antriebsritzel der Zwischenwelle.
Tragen Sie das Silikon-Klebstoff-Dichtmittel Unisil H50-1 auf den Zylinderblock rund um die Installationshülse der Kettenabdeckung auf der rechten Seite des Blocks auf (im Inneren befindet sich ein Ölversorgungskanal zum unteren hydraulischen Spanner).
Nehmen Sie den Kettendeckel mit der Öldichtung und prüfen Sie die Eignung der Öldichtung für weitere Arbeiten.
Wenn die Öldichtung eine abgenutzte Arbeitskante aufweist oder die Nabe der Dämpferscheibe nur schwach abdeckt, ersetzen Sie sie durch eine neue.
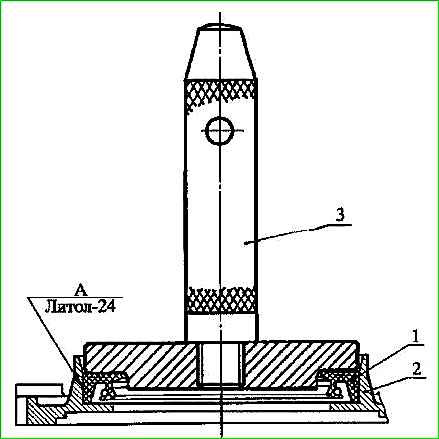
Es wird empfohlen, die Öldichtung mit einem Dorn in die Kettenabdeckung zu drücken (Abbildung 3).
Die Öldichtung muss mit der Manschette an der Außenseite des Motors und der von der Feder abgedeckten Arbeitskante nach innen eingebaut werden.
Tragen Sie vor dem Pressen Litol-24-Schmiermittel auf die Außenfläche der Öldichtung auf, um das Pressen zu erleichtern.
Füllen Sie den Hohlraum zwischen der Arbeitskante und der Manschette der Gummimanschette der Kettenabdeckung mit CIATIM-221-Schmiermittel.
Um zu verhindern, dass die Kette der zweiten Stufe vom Zwischenwellenritzel springt, installieren und befestigen Sie die Kettenabdeckung mit Dichtungen und der Generatorhalterung.
Installieren und befestigen Sie die Wasserpumpe mit der elektromagnetischen Kupplung und der Dichtung an der Kettenabdeckung, indem Sie die Schraube festziehen, mit der die Wasserpumpe an der Kettenabdeckung befestigt ist.
Schmieren Sie das Loch für den hydraulischen Spanner in der Kettenabdeckung mit sauberem Motoröl, das für den Motor verwendet wird, und installieren Sie den zusammengebauten hydraulischen Spanner, bis der Spannerhebel den Anschlag berührt, aber drücken Sie nicht, um zu verhindern, dass der hydraulische Spanner blockiert in Betrieb.
In den Deckel eine geräuschdämmende Unterlegscheibe einbauen, den hydraulischen Spanner mit einem Deckel mit Dichtung verschließen, die Schrauben einsetzen (die untere Schraube mit der Halterung zur Befestigung des Synchronisationssensorkabels) und die Deckelschrauben festziehen.
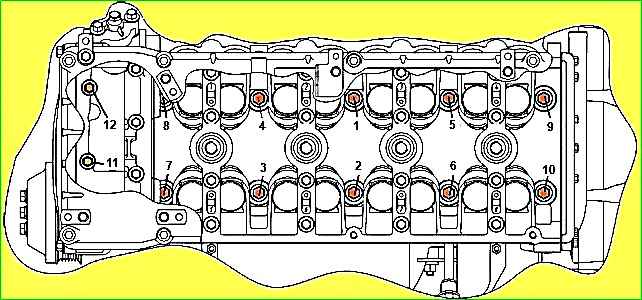
Verwenden Sie einen Dorn durch das Loch in der Abdeckung des hydraulischen Spanners, um auf den hydraulischen Spanner zu drücken. Bewegen Sie ihn bis zum Anschlag und lassen Sie ihn dann los. In diesem Fall löst sich der Sicherungsring am Kolben vom Gehäuse des hydraulischen Spanners und lässt den Kolben frei und der Körper bewegt sich unter der Wirkung der Feder.
Der Körper bewegt sich vollständig und die Kette wird über den Spannhebel gespannt.
Schrauben Sie den Stopfen in die Abdeckung des hydraulischen Spanners ein, nachdem Sie zuvor das anaerobe Dichtmittel Stopor-6 auf die Gewinde des Stopfens aufgetragen haben.
Schneiden Sie die Enden der Kettenabdeckungsdichtungen ab, die über die Ebene des Zylinderblocks und der Kettenabdeckung hinausragen.
Wenn an der Zylinderkopfdichtung an zwei Stellen, die an den Verbindungsstellen des Kettendeckels mit dem Zylinderblock liegen, keine Gummidichtungen vorhanden sind, sollte an diesen Stellen der Dichtung Silikon-Klebstoff-Dichtmittel „Unisil N50-1“ aufgetragen werden (Windows).
Montieren Sie die Zylinderkopfdichtung auf den Zylinderblockstiften und Kettenabdeckungsbolzen.
Installieren Sie einen Schlauch, der das Wasserpumpenrohr mit dem Thermostatgehäuse verbindet, am Wasserpumpenanschluss.
Montieren Sie den zusammengebauten Zylinderkopf auf dem Zylinderblock und befestigen Sie ihn.
Ziehen Sie die Zylinderkopf-Befestigungsschrauben in der in Abbildung 4 gezeigten Reihenfolge in zwei Schritten fest: Ziehen Sie die Schrauben zunächst mit einem Drehmoment von 40–50 Nm (4,0–5,0 kgf·m) fest, halten Sie diesen Zustand dann mindestens 1,2 Minuten lang und Ziehen Sie abschließend die Schrauben im 90˚-Winkel fest.
Vor dem Einbau die Schraubengewinde mit Motoröl schmieren. Ziehen Sie die Schrauben Nr. 11, 12 mit einem Drehmoment von 19,6-24,5 Nm (2,0...2,5 kgcm) an.
Um Wasserschläge beim Anziehen der Schrauben und das Auftreten von Rissen im Zylinderblock zu vermeiden, darf sich kein Öl in den Gewindebohrungen des Blocks befinden.
Schrauben Sie die Schrauben ab und entfernen Sie die Nockenwellenabdeckungen, wischen Sie das Bett unter den Nockenwellen im Kopf und in den Abdeckungen mit einer Serviette ab und schmieren Sie vor dem Anbringen der Abdeckungen die Gewinde der Schrauben mit sauberem Motoröl.
Schmieren Sie die Löcher im Kopf für die hydraulischen Drücker mit Motoröl und installieren Sie die hydraulischen Drücker im Zylinderkopf.
Wenn Sie einen Motor reparieren, ohne die Hydrostößel auszutauschen, sollten diese vor der Demontage entsprechend ihrer Position eingebaut werden.
Wenn der hydraulische Schieber ausfällt, muss er ersetzt werden, da er nicht repariert werden kann. Die hydraulischen Drücker müssen mit einem Saugnapf oder einem Magneten entfernt werden.
Montieren Sie die Nockenwellen am Zylinderkopf, nachdem Sie zuvor die Lager im Kopf mit Motoröl geschmiert haben.
Die Einlassnockenwelle wird mit dem Kettenradstift nach oben eingebaut und die Auslassnockenwelle wird mit dem Kettenradstift nach rechts zeigend eingebaut. Aufgrund der Winkelanordnung der Nocken sind diese Nockenwellenpositionen stabil.
Schmieren Sie die Wellenlagerzapfen mit sauberem Motoröl, das im Motor verwendet wird.
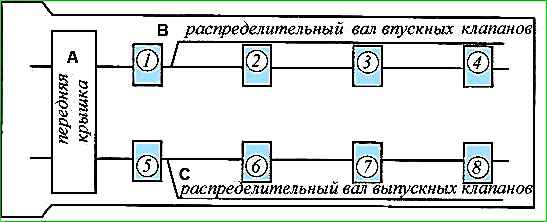
Nockenwellenabdeckungen müssen entsprechend ihrer Nummerierung eingebaut werden (Abb.Nr. 5), geführt durch runde Vorsprünge mit Nummern für die Einlasswelle – nach links, die Auslasswelle – nach rechts, von der Vorderseite des Motors aus gesehen.
Diese Ausrichtung hängt mit der asymmetrischen Lage der Ölkanalnut in den Abdeckungen zusammen.
Montieren Sie die vordere Nockenwellenabdeckung mit den darin montierten Druckflanschen auf den Montagehülsen und stellen Sie sicher, dass die Druckflansche durch die Längsbewegung der Nockenwellen in die Nuten eingebaut werden.
Schmieren Sie den Druckflansch vor dem Einbau mit sauberem Motoröl, das im Motor verwendet wird.
Montieren Sie die Abdeckungen Nr. 3 und Nr. 7 der Nockenwellen und ziehen Sie die Schrauben zur Befestigung der Abdeckungen vor, bis die Oberfläche der Abdeckungen die obere Ebene des Zylinderkopfs berührt.
Montieren Sie alle anderen Abdeckungen gemäß den Markierungen und ziehen Sie die Abdeckungsschrauben vorfest an.
Ziehen Sie abschließend die Schrauben der Nockenwellenabdeckung mit einem Drehmoment von 18,6–22,6 Nm (1,9–2,3 kgcm) fest.
Schmieren Sie alle Nockenwellennocken mit Motoröl und prüfen Sie die Drehung jeder Nockenwelle in den Halterungen, indem Sie die Nockenwelle mit einem Schraubenschlüssel und einem speziellen Vierkant auf der Nockenwelle drehen, bis die Ventilfedern eines der Zylinder vollständig zusammengedrückt sind.
Bei weiterer Drehung sollte sich die Nockenwelle unter der Wirkung der Ventilfedern selbstständig drehen, bis sie die nächsten Nocken mit Stößeln berührt.
Nachdem Sie die Leichtgängigkeit der Nockenwellen überprüft haben, drehen Sie sie so, dass die Ausrichtungsstifte für die Kettenräder ungefähr horizontal und in verschiedene Richtungen ausgerichtet sind (Abbildung 2).
Diese Nockenwellenpositionen sind stabil und werden durch die Winkelanordnung der Nocken gewährleistet.
Beginnen Sie mit der Einstellung der Winkelposition der Nockenwellen von der Auslasswelle aus; legen Sie dazu eine Antriebskette über das Kettenrad, montieren Sie das Kettenrad auf dem Flansch und dem Stift der Nockenwelle und richten Sie den Stift und das Loch darauf aus Drehen Sie die Nockenwelle um den Vierkant im Uhrzeigersinn.
Ziehen Sie die Antriebskette fest, indem Sie die Nockenwelle gegen den Uhrzeigersinn drehen, bis die Markierung auf dem Kettenrad mit der oberen Ebene des Zylinderkopfs übereinstimmt. Die Kurbelwelle darf sich nicht drehen.
Um die Einlassnockenwelle schräg einzubauen, legen Sie die Antriebskette über das Kettenrad, montieren Sie das Kettenrad am Flansch und am Nockenwellenstift, wobei der Kettenzweig zwischen den Kettenrädern leicht locker sein muss.
Ziehen Sie die Kette fest, indem Sie die Nockenwelle gegen den Uhrzeigersinn drehen, bis die Markierung auf dem Kettenrad mit der oberen Ebene des Zylinderkopfs übereinstimmt.
Setzen Sie die Befestigungsschrauben des Kettenrads ein und ziehen Sie sie mit einem Drehmoment von 54,9–60,8 Nm (5,6–6,2 kgcm) fest. Halten Sie dabei die Nockenwellen mit einem Schlüssel am Vierkant fest, damit sie sich nicht drehen.
Montieren Sie den hydraulischen Spanner für die obere Nockenwellen-Antriebskette auf die gleiche Weise wie den hydraulischen Spanner für die untere Kette.
Montieren Sie die mittleren und oberen Kettenführungen, ziehen Sie die Befestigungsschrauben fest, ohne sie vollständig festzuziehen, nachdem Sie zuvor anaerobes Dichtmittel Stopor-6 auf die Schraubengewinde aufgetragen haben.
Drehen Sie die Arbeitszweige der oberen Kette, indem Sie die Kurbelwelle des Motors in Drehrichtung drehen, und ziehen Sie schließlich die Schrauben fest, mit denen die Stabilisatoren der mittleren und oberen Kette befestigt sind.
Montieren Sie die Buchse am vorderen Ende der Kurbelwelle in der Nähe des Kettenrads. Richten Sie dabei die große Innenfase zum Dichtring und die Nut unter dem Ende der Passfeder zur Vorderseite des Motors aus.
Drücken Sie die Passfeder in die Keilnut am vorderen Ende der Kurbelwelle, sodass ihr halbkugelförmiges Ende vollständig in die Nut der Buchse passt.
Drücken Sie die Dämpferriemenscheibe mit einem Spezialwerkzeug bis zum Anschlag auf das vordere Ende der Kurbelwelle und richten Sie dabei die Keilnut der Dämpferriemenscheibe mit der Passfeder aus.
Ziehen Sie die Klemmschraube fest und ziehen Sie sie mit einem Drehmoment von 166,6–215,6 Nm (17–22 kgcm) an.
Überprüfen Sie nach Abschluss der Montage den Einbau der Nockenwellen, indem Sie die Motorkurbelwelle zwei Umdrehungen in Drehrichtung drehen, bis die Markierung am Kurbelwellendämpfer mit der Markierung am Kettendeckel übereinstimmt. In diesem Fall müssen die Markierungen auf den Nockenwellenrädern mit der oberen Ebene des Zylinderkopfes übereinstimmen.
Wenn Sie einen Motor reparieren, bei dem Nockenwellen, Zylinderköpfe und Kettenräder von der Zwischenwelle entfernt werden, installieren Sie den Nockenwellenantrieb während der Montage wie oben beschrieben.
Wenn die Zwischenwellenräder und die Kettenabdeckung bei Reparaturen nicht entfernt werden, muss vor der Demontage der Kolben des 1. Zylinders auf die OT-Position beim Kompressionshub eingestellt werden, wobei die Markierung auf der Kurbelwellen-Dämpferriemenscheibe übereinstimmen muss mit dem Vorsprung auf der Kettenabdeckung und den Markierungen auf den Nockenwellenrädern sollten horizontal angeordnet sein, in verschiedene Richtungen gerichtet sein und mit der oberen Ebene des Qi-Kopfes übereinstimmen lindrov.
Nach dem Ausbau der Nockenwellen und Zylinderköpfe kann die Kurbelwelle nur noch durch Zurückkehren in die Ausgangsposition oder durch Drehen der Kurbelwelle um 2 Umdrehungen gedreht werden.
Das Drehen der Kurbelwelle um eine Umdrehung führt zu einer falschen Ventilsteuerung, auch wenn die Markierungen auf der Riemenscheibe und der Kettenabdeckung übereinstimmen.
Wenn die Nockenwellen und Kettenräder falsch eingebaut sind, stimmen die Markierungen auf den Kettenrädern nicht mit der oberen Ebene des Zylinderkopfs überein. In diesem Fall ist es notwendig, die Kettenräder zu entfernen, die Kurbelwelle 1 Umdrehung in Drehrichtung zu drehen und den Einbau der Kettenräder wie oben beschrieben zu wiederholen.
Nachfolgende Arbeiten zum Zusammenbau des Motors
Montieren Sie die vordere Zylinderkopfabdeckung und befestigen Sie sie mit der Dichtung.
Setzen Sie das Thermostatgehäuse in den Thermostatschlauch ein und befestigen Sie das Thermostatgehäuse mit der Dichtung am Zylinderkopf, ziehen Sie die Schlauchklemmen fest.
Drücken Sie das Rohr der Ölstandanzeigestange hinein und installieren Sie die Anzeige. Um die Zuverlässigkeit der Installation und die Dichtheit zu erhöhen, tragen Sie zunächst das Dichtmittel Loctite-638 auf die Oberfläche des unteren Endes des Rohrs auf.
Montieren Sie den Abgaskrümmer mit Dichtung auf den Zylinderkopfbolzen. Bringen Sie alle bis auf die letzte Krümmer-Befestigungsmutter an und ziehen Sie sie fest.
Montieren Sie das Abgaskrümmersieb auf den Abgaskrümmerbolzen und befestigen Sie es mit Muttern.
Montieren Sie den Schlauch, der die Pumpe mit dem Wasseransaugrohr verbindet, am Wasserpumpenanschluss und befestigen Sie ihn mit einer Schelle.
Setzen Sie die Halterung auf das Wassereinlassrohr.
Führen Sie den Wasseransaugschlauch in den Schlauch am Wasserpumpenanschluss ein und platzieren Sie die Halterung am letzten Stift des Verteilers. Sichern Sie die Halterung, indem Sie die Mutter festziehen und die Schlauchklemme festziehen.
Montieren Sie die Ablassschraube des Zylinderblocks, nachdem Sie zuvor das Silikon-Klebstoff-Dichtmittel „Unisil N50-1“ oder das anaerobe Dichtmittel „Stopor-6“ auf das Gewinde der Schraube aufgetragen haben.
Ventildeckel mit Dichtung und Zündkerzenschachtdichtungen montieren und sichern. Montieren Sie den Steckerhalter des Zeitgebersensors am Ventildeckel.
Montieren und sichern Sie gleichzeitig die obere und untere Generatorhalterung sowie die vordere Motorhebehalterung.
Das Kühlmittelansaugrohr mit einer Dichtung einbauen. Tragen Sie zunächst das anaerobe Dichtmittel Stopor-6 auf die Gewinde der Rohrschrauben auf.
Montieren Sie das Ansaugrohr und befestigen Sie es mit der Dichtung am Zylinderkopf.
Montieren Sie den Empfänger mit der Dichtung auf den Bolzen des Einlassrohrs und befestigen Sie ihn mit Muttern.
Befestigen Sie den Empfänger mit zwei Eckhalterungen, die an den Zylinderkopfbolzen angebracht sind, am Zylinderkopf.
Ziehen Sie zuerst, ohne sie festzuziehen, die Schrauben fest, mit denen die Halterungen am Empfänger befestigt sind. Ziehen Sie dann die Muttern fest, mit denen die Halterungen am Kopf befestigt sind, und ziehen Sie die Schrauben fest, mit denen sie am Empfänger befestigt sind.
Entlüftungsschlauch mit Entlüftungsrohr montieren und mit Schellen befestigen. Den Schlauch des kleinen Lüftungszweigs auf die Anschlüsse von Lüftungsrohr und Empfänger aufstecken und mit Schellen befestigen.
Montieren und befestigen Sie die Abtriebs- und Druckplatten der Kupplung und zentrieren Sie die Abtriebsscheibe mit einem speziellen Dorn.
Die Getriebeeingangswelle kann als Dorn verwendet werden. Ziehen Sie die Schrauben der Druckplatte nacheinander in mehreren Schritten fest, um eine Verformung der Druckplatte zu vermeiden, und zwar mit einem Drehmoment von 19,6–24,5 Nm (2,0–2,5 kgcm).
Setzen Sie den Stift und die Stehbolzen der Kupplungsausrückgabel in das Kupplungsgehäuse ein.
Montieren Sie das Kupplungsgehäuse mit der Motorhebehalterung auf den Positionierungsstiften des Zylinderblocks und befestigen Sie es mit Schrauben am Zylinderblock.
Entfernen Sie den Motor vom Ständer.
Vorgehensweise zur Montage von Anbauteilen am Motor
- 1. Schmieren Sie die Gummi-O-Ringe der Einspritzdüsen mit sauberem Motoröl, installieren Sie die Kraftstoffleitung mit den Enden der Einspritzdüsen in den Löchern im Ansaugrohr und befestigen Sie die Kraftstoffleitung.
- 2. Installieren Sie den Notöldruckanzeigesensor im Zylinderkopf, nachdem Sie zuvor anaerobes Stopor-6-Dichtmittel auf den Gewindeteil des Sensors aufgetragen haben.
- 3. Installieren Sie den Generator und sichern Sie ihn. Ziehen Sie zuerst die Muttern der Schrauben fest, mit denen der Generator an der oberen und unteren Halterung befestigt ist, und dann die Schraube, mit der die Buchse der oberen Halterung befestigt ist.
- 4. Installieren Sie die automatische Spannvorrichtung so, dass der Stift der Vorrichtung in das Loch in der Nabe ihrer Befestigung passt, und ziehen Sie die Schraube ihrer Befestigung fest, nachdem Sie zuvor das anaerobe Dichtungsmittel Stopor-6 auf das Schraubengewinde aufgetragen haben.
Dann folgt:
- - Bewegen Sie die Spannrolle mit einem Schraubenschlüssel an der Rollenbefestigungsschraube in ihre äußerste Position;
- - Führen Sie den Befestigungsstift (Ø 4 mm und 55 mm lang) bis zum Anschlag in das Loch in der Spannvorrichtung ein;
- - Lassen Sie die Walze los, wobei sich der Walzenstift in der äußersten Position befindet;
- - Legen Sie den Riemen auf die Riemenscheiben;
- - Bewegen Sie die Walze leicht mit einem Schraubenschlüssel, lösen Sie den Stift und entfernen Sie den Stift mit einer Zange;
- - Bringen Sie die Rolle zum Band und lassen Sie die Rolle los. Der Riemen wird durch den Spanner gespannt.
- 5. Phasensensor einbauen in das Loch im Zylinderkopf einführen und mit einer Schraube befestigen, nachdem der O-Ring des Sensors mit sauberem Motoröl geschmiert wurde. Der Sensorflansch muss eng an der Oberfläche des Zylinderkopfs anliegen, bevor er mit einer Schraube befestigt wird.
- 6. Installieren Sie den Synchronisationssensor im Loch der Kettenabdeckung. Legen Sie das Sensorkabel in eine Halterung, die durch die untere Schraube der unteren hydraulischen Spannerabdeckung befestigt ist, und installieren Sie den Stecker in der Halterung an der Ventilabdeckung.
- 7. Installieren Sie den Klopfsensor und befestigen Sie ihn mit einer Mutter und einer Federscheibe mit einem Drehmoment von 20 ± 0,5 Nm (2,0 ± 0,05 kgcm).
- 8. Installieren Sie den Gashebel und befestigen Sie ihn mit der Dichtung am Empfänger.
- 9. Schrauben Sie die Zündkerzen ein
Treffen Sie beim Einbau der Zündkerzen Vorsichtsmaßnahmen, um das Gewinde der Zündkerzenbohrung im Zylinderkopf nicht zu beschädigen. Die Zündkerzen sollten durch leichtes Drehen des Schlüssels eingebaut und dann mit einem Drehmoment von 20,0–30,0 Nm (2,1–3,1 kgcm) festgezogen werden.
- 10. Installieren Sie die Zündspulen und befestigen Sie sie mit Muttern.
- 11. Den Anlasser einbauen und mit Schrauben befestigen.
- 12. Schrauben Sie die Kühlmitteltemperatursensoren des Steuersystems und die Kühlmittelüberhitzungsanzeige in das Thermostatgehäuse ein, nachdem Sie zuvor anaerobes Dichtmittel Stopor-6 auf den Gewindeteil der Sensoren aufgetragen haben.
- 13. Installieren Sie das Thermoventil mit der Dichtung, richten Sie den Anschluss nach oben aus und befestigen Sie das Thermoventil mit dem Ölfilteranschluss.
- 14. Den Ölfilter einbauen. Schmieren Sie vor dem Einbau des Filters die Gummifilterdichtung mit sauberem Motoröl. Schrauben Sie den Filter auf den Anschluss, bis die Dichtung die Auflagefläche berührt, und ziehen Sie ihn dann um eine ¾ Umdrehung fest.