Reinigen Sie die Kolbenköpfe und Nuten für Kolbenringe von Kohlenstoffablagerungen
Kolben in den Zylindern des Blocks müssen Gruppe für Gruppe gemäß der Tabelle eingebaut werden
Kolben nach dem Außendurchmesser des Mantels und Zylinder nach dem Innendurchmesser werden in drei Größengruppen eingeteilt und mit den Buchstaben A, B, C gekennzeichnet.
Ein Buchstabe, der die Größengruppe des Zylinderdurchmessers angibt, ist auf der Außenfläche des Zylinderblocks rechts gegenüber jedem Zylinder aufgemalt.
Größengruppen von Zylinderdurchmessern werden bei der Herstellung des Zylinderblocks bestimmt.
Bei der Reparatur eines gebrauchten Motors mit verschlissenen Zylindern ist es notwendig, die Zylinderdurchmesser erneut zu messen und ihre Gruppe zu bestimmen.
Zylinderdurchmesser sollten bei einer Temperatur von plus 20 ± 3 °C gemessen werden.
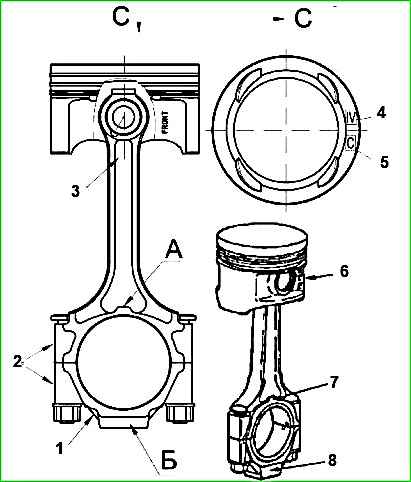
Kolben sind auf der Unterseite mit Buchstaben gekennzeichnet (Abbildung 1).
Der größte Durchmesser des Kolbenschafts liegt in einer Ebene senkrecht zur Kolbenbolzenachse im Abstand von 47,5 mm vom Kolbenboden.
Messen Sie die Kolbenschaftdurchmesser bei einer Kolbentemperatur von plus 20 ± 3 °C.
Bolzen nach Außendurchmesser, Pleuelstangen und Kolben nach Bolzenlochdurchmesser werden in vier Größengruppen sortiert, die mit Farbe oder römischen Ziffern gekennzeichnet sind (Tabelle 1).
Die Größengruppe der Pleuelbohrung für den Bolzen ist mit Farbe auf der Pleuelstange im Bereich des Kolbenbodens markiert.
Die Kolbenlochgruppe ist durch auf der Unterseite eingestanzte römische Ziffern gekennzeichnet (Abbildung 1) und der Stift durch am Ende eingestanzte römische Ziffern.
Die Pleuelstange muss mit einem Bolzen der gleichen Größengruppe zusammengebaut werden.
Wenn die Nichtparallelität der Achsen der Kolben- und Kurbelkopfbohrungen den maximal zulässigen Wert überschreitet, ist die Pleuelstange verformt und muss ersetzt werden.
Wenn das Loch in der Pleuelbuchse für den Bolzen über das akzeptable Maß hinaus abgenutzt ist, muss die Buchse ausgetauscht, eine Nut in die Buchse für den Ölkanal gemacht und das Loch in der Buchse für den Bolzen bearbeitet werden.
Bevor Sie eine neue Buchse einbauen, messen Sie den Durchmesser des Befestigungslochs für die Pleuelstange. Wenn das Loch mehr als akzeptabel abgenutzt ist, sollte die Pleuelstange aussortiert werden.
Messen Sie Kolben, Bolzen und Pleuel bei einer Temperatur von 20 ± 3 °C.
Pleuelstangen werden nach Gewicht in drei Gruppen sortiert und mit Farbe auf der Pleuelstangenabdeckung markiert (Abbildung 1). Markierungsfarbe:
- - weiß - entspricht der Masse der Pleuelstange 900-905 g;
- - grün - 895-900 g;
- - gelb – 890-895
Größengruppen von Kolben und Zylindern des Blocks
Gruppe A:
- - Kolbendurchmesser (Schürze) – 95,488 – 95,500 mm;
- - Zylinderdurchmesser - 95,536 - 95,548 mm
Gruppe B:
- - Kolbendurchmesser (Schürze) – 95.500 – 95.512 mm;
- - Zylinderdurchmesser - 95,548 - 95,560 mm
Gruppe C:
- - Kolbendurchmesser (Schürze) – 95,512 – 95,524 mm;
- - Zylinderdurchmesser - 95,560 - 95,572 mm
Erhöhung der Gruppen-KI-Reparatur um 0,25:
- - Kolbendurchmesser (Schürze) – 95,738 – 95,750 mm;
- - Zylinderdurchmesser - 95,786 - 95,798 mm
Gruppen-BI-Reparaturerhöhung um 0,25:
- - Kolbendurchmesser (Schürze) – 95,750 – 95,762 mm;
- - Zylinderdurchmesser - 95,798 - 95,810 mm
Erhöhung der CI-Gruppenreparatur um 0,25:
- - Kolbendurchmesser (Schürze) – 95,762 – 95,774 mm;
- - Zylinderdurchmesser - 95,810 - 95,822 mm
Reparaturerhöhung für Gruppe AII 0,5:
- - Kolbendurchmesser (Schürze) – 95,988 – 96,000 mm;
- - Zylinderdurchmesser - 96,036 - 96,048 mm
Reparaturerhöhung der Gruppe BII um 0,5:
- - Kolbendurchmesser (Schürze) – 96.000 – 96.012 mm;
- - Zylinderdurchmesser - 96,048 - 96,060 mm
Gruppen-CII-Reparaturerhöhung um 0,5:
- - Kolbendurchmesser (Schürze) – 96,012 – 96,024 mm;
- - Zylinderdurchmesser - 96,060 - 96,072 mm
Größengruppen von Bolzen, Kolben und Pleueln
Fingerdurchmesser – 21,9935–21,9960 mm:
- - Löcher in der Kolbennabe – 21,9975—22,0000 mm;
- - Löcher in der Pleuelbuchse – 22,0045—22,0070 mm;
- - Pleuelmarkierung – weiß;
- - Kolben- und Bolzenmarkierung – „I“
Fingerdurchmesser – 21,9910–21,9935 mm:
- - Löcher in der Kolbennabe – 21,9950—21,9975 mm;
- - Löcher in der Pleuelbuchse – 22,0020–22,0045 mm;
- - Pleuelmarkierung – grün;
- - Kolben- und Bolzenmarkierung – „II“
Fingerdurchmesser – 21,9885–21,9910 mm:
- - von Loch in der Kolbennabe – 21,9925—21,9950 mm;
- - Löcher in der Pleuelbuchse – 21,9995—22,0020 mm;
- - Pleuelmarkierung – gelb;
- - Kolben- und Bolzenmarkierung – „III“
Fingerdurchmesser – 21,9860–21,9885 mm:
- - Löcher in der Kolbennabe – 21,9900—21,9925 mm;
- - Löcher in der Pleuelbuchse – 21,9970—21,9995 mm;
- - Pleuelmarkierung – rot;
- - Kolben- und Bolzenmarkierung – „IV“
Für den Einbau am Motor sollten Pleuel der gleichen Gewichtsgruppe verwendet werden.
Kolben sind nicht nach Gewicht sortiert.
Überprüfen Sie den Massenunterschied der ausgewählten Sätze aus Kolben, Bolzen, Pleuel und Ringen, der 10 g nicht überschreiten sollte.
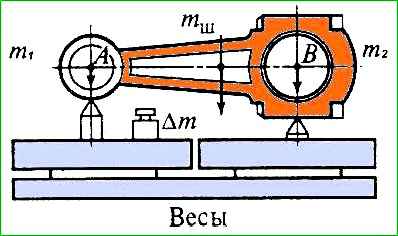
Bei einem größeren Unterschied in den Massen der Sätze sollte zur Eliminierung erhöhter Motorvibrationen die Masse der Sätze ausgeglichen werden; dazu ist das Metall von den Pleueln schwererer Sätze vom Gewicht zu entfernen Kolbennaben oder Kurbelköpfe, abhängig von der Masse der Köpfe, auf eine Größe, die nicht kleiner ist als die in Abbildung 2 gezeigte.
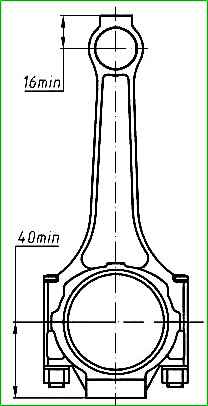
Beim Materialabtrag sollte die Masse der Pleuelköpfe folgende Grenzen nicht überschreiten: Kolben (m 1) - 211-217 g, Kurbel (m 2). ) - 679-688 g.
Kolbenbolzen mit Motoröl schmieren und in die Löcher des Kolbens und der Pleuelstange einsetzen.
Pleuelstangen und Kolben müssen beim Zusammenbau mit einem Kolbenbolzen wie folgt ausgerichtet sein: Die Aufschrift „FRONT“ an der Außenseite der Bolzennabe und der Vorsprung „A“ am Kurbelkopf der Pleuelstange müssen ausgerichtet sein in die gleiche Richtung gerichtet.
Die Pleuelabdeckung muss so auf der Pleuelstange montiert werden, dass die Leiste „B“ auf der Pleuelabdeckung und die Leiste „A“ auf dem Kurbelkopf bzw. die auf der Seitenfläche der Abdeckung und Kurbel eingeprägten Zylindernummern vorhanden sind Der Kopf bzw. die Nuten für die Liner befinden sich auf einer Seite (Abbildung 1).
Ringe, die für den Einbau in Zylinder mit Nenndurchmesser vorgesehen sind, sind auf dem oberen Kompressionsring mit gelber Farbe gekennzeichnet.
Zum Einbau in Zylinder der ersten Reparaturgröße - blau, der zweiten Reparaturgröße - grün.
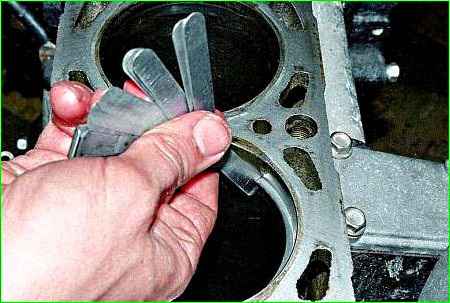
Der thermische Abstand, gemessen an den im Zylinder platzierten Verbindungen (Abbildung 4), sollte für neue Ringe betragen:
- - 0,25–0,45 mm am oberen Kompressionsring;
- - 0,45–0,65 am unteren Kompressionsring;
- - 0,30–0,55 mm für einen kastenförmigen Ölabstreifring.
Bei abgenutzten Ringen beträgt die maximal zulässige Größe im Schloss nicht mehr als 1,5 mm.
Platzieren Sie Ringe zur Messung des thermischen Spalts im Schloss im oberen, unverschlissenen Teil des Zylinders (von der Oberkante des Zylinders bis zur Stelle des ersten Kompressionsrings, wenn sich der Kolben im oberen Totpunkt befindet) oder in einem Dorn des Gleicher Durchmesser.
Reinigen Sie die Oberfläche des Zylinders vorab von Kohlenstoffablagerungen.
Der Einbau von Kolbenringen mit einem kleineren thermischen Spalt an der Verbindungsstelle führt zu einer Konvergenz der Ringverbindung während des Motorbetriebs und zum Zylindernadir.
Der Einbau verschlissener Ringe mit großem Spalt führt zu einer Verringerung des Kompressionshubdrucks und einem erhöhten Ölverlust.
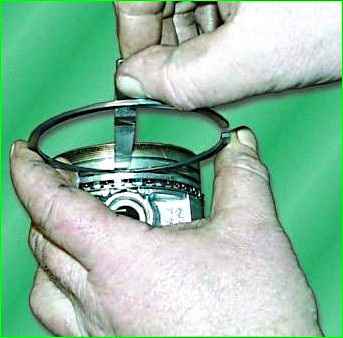
Überprüfen Sie den seitlichen Abstand zwischen den Ringen und der Kolbennutwand mit einer Fühlerlehre (Abbildung 5). Überprüfen Sie den Umfang des Kolbens an mehreren Stellen.
Das Seitenspiel sollte bei neuen Ringen und Kolben 0,045–0,090 mm betragen. Bei verschlissenen Ringen und Kolben ist ein maximales Spiel von nicht mehr als 0,15 mm zulässig.
Ein größerer Spalt führt aufgrund der „Pumpwirkung“ der Ringe zu einem erhöhten Ölverlust.
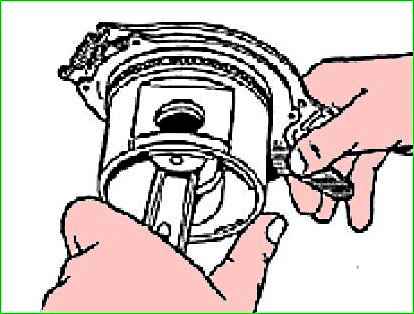
Setzen Sie die Kolbenringe mit dem Werkzeug auf den Kolben (Abbildung 6).
Montieren Sie den unteren Kompressionsring mit der Aufschrift „TOP“ (oben) am Ende Richtung Kolbenboden. Die Ringe in den Nuten müssen frei beweglich sein.
Setzen Sie die Kolben wie folgt in die Zylinder ein:
- - Richten Sie die Pleuel-Kolben-Gruppe so aus, dass die Aufschrift „FRONT“ auf der Kolbennabe zur Vorderseite des Zylinderblocks zeigt.
- - Wischen Sie die Pleuellager und deren Abdeckungen mit einer Serviette ab, wischen Sie die Buchsen ab und setzen Sie sie ein.
- - Drehen Sie die Kurbelwelle so, dass die Kurbeln des ersten und vierten Zylinders die Position einnehmen, die dem UT entspricht;
- - Schmieren Sie die Lager, den Kolben, den Pleuelzapfen und den ersten Zylinder mit sauberem Motoröl;
- - Bewegen Sie die Ringverschlüsse in einem Winkel von ca. 120° zueinander, wobei das Gelenk des Federexpanders gegenüber dem Verschluss des Ölabstreifringkastens platziert werden sollte, bevor Sie den Ring am Kolben anbringen.
Es wird empfohlen, die Ringschlösser nicht in einer Ebene senkrecht zur Fingerachse zu platzieren;
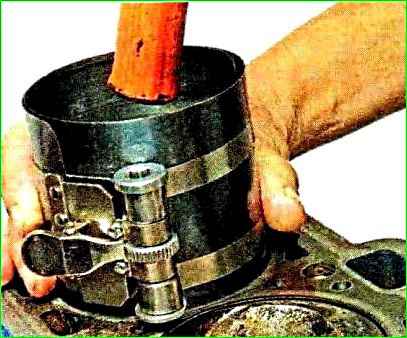
- Bringen Sie Sicherheitsspitzen an den Pleuelschrauben an, drücken Sie die Ringe mit einem speziellen Dorn mit konischer Innenfläche zusammen und setzen Sie den Kolben in den Zylinder ein (Abbildung 7).
Vor dem Einbau des Kolbens sollten Sie noch einmal sicherstellen, dass die auf dem Pleuel und seinem Deckel eingestanzten Nummern mit der Seriennummer des Zylinders übereinstimmen, und die korrekte Position des Kolbens und des Pleuels im Zylinder überprüfen.
Ziehen Sie die Pleuelstange am Kurbelkopf zum Pleuelzapfen, entfernen Sie die Messingspitzen von den Bolzen und setzen Sie die Pleuelstangenabdeckung auf.
Die Pleuelkappe sollte so montiert werden, dass sich die auf der Kappe und der Pleuelstange eingestanzten Nummern oder die Rillen für die Laufbuchsen auf einer Seite befinden.
Ziehen Sie die Muttern mit einem Drehmomentschlüssel mit einem Drehmoment von 68–75 Nm (6,8–7,5 kgcm) an.
In der gleichen Reihenfolge den Kolben des vierten Zylinders einsetzen.
Drehen Sie die Kurbelwelle um 180˚ und setzen Sie die Kolben des zweiten und dritten Zylinders ein.
Drehen Sie die Kurbelwelle mehrmals, sie sollte sich leicht und mit geringem Kraftaufwand drehen lassen.