Las dimensiones principales del bloque de cilindros se dan en la Figura 1
El bloque de cilindros está fabricado en hierro fundido especial de baja aleación
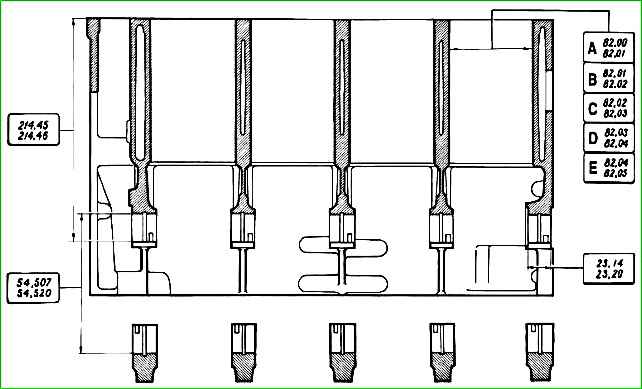
Los diámetros de los cilindros se dividen en cinco clases cada 0,01 mm, designadas con las letras A, B, C, D, E.
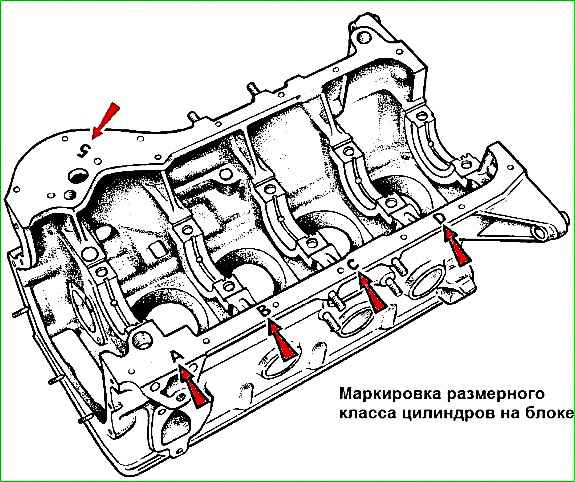
La clase de cilindro está estampada en el plano inferior del bloque de cilindros
Es posible perforar los cilindros para reparar pistones, aumentando su diámetro en 0,4 y 0,8 mm.
Las tapas de los cojinetes de bancada se procesan como un conjunto con el bloque de cilindros.
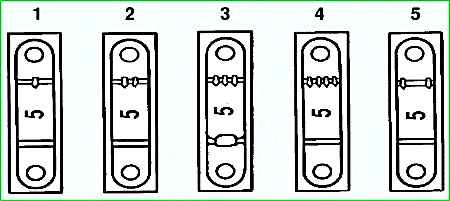
Por lo tanto, no son intercambiables y para distinguirlos tienen marcas en la superficie exterior (ver Fig. 2-18).
Comprobación del estado técnico y reparación del bloque de cilindros
Lavar bien el bloque de cilindros y limpiar los canales de aceite.
Después de soplar y secar con aire comprimido, inspeccione el bloque de cilindros. No se permiten grietas en los soportes u otros lugares del bloque de cilindros.
Si sospecha que ha entrado refrigerante en el cárter, utilice un soporte especial para comprobar el apriete del bloque de cilindros.
Para hacer esto, tapando los orificios en la camisa de enfriamiento del bloque de cilindros, bombee agua a temperatura ambiente a una presión de 0,3 MPa (3 kgf/cm 2).
No debería haber fugas de agua del bloque de cilindros en dos minutos.
Si entra aceite en el refrigerante, sin desmontar completamente el motor, compruebe si hay grietas en el bloque de cilindros en las áreas de los canales de aceite.
Para hacer esto, drene el refrigerante del sistema de enfriamiento, retire la culata, llene la camisa de enfriamiento del bloque de cilindros con agua y suministre aire comprimido al canal de aceite vertical del bloque de cilindros.
Si aparecen burbujas de aire en el agua que llena la camisa de enfriamiento, reemplace el bloque de cilindros.
Compruebe la planitud del bloque de cilindros y la culata utilizando una regla y una galga de espesores.
La regla se instala a lo largo de las diagonales del plano y en el medio en dirección longitudinal y transversal. La tolerancia de planitud no debe ser superior a 0,1 mm.
Reparación de cilindros
Compruebe que el desgaste del cilindro no supere el máximo permitido: 0,15 mm.
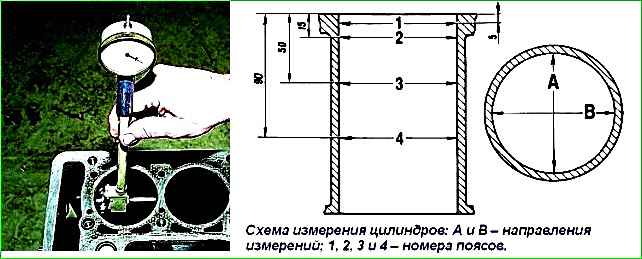
El diámetro del cilindro se mide con un calibre de diámetro interior (Fig. 2-32) en cuatro zonas, tanto en la dirección longitudinal como en la transversal del motor. Se utiliza un micrómetro para poner el calibre del diámetro a cero.
En la zona 1 de la correa, los cilindros prácticamente no se desgastan. Por lo tanto, por la diferencia en las medidas de la primera y otras correas, se puede juzgar la cantidad de desgaste del cilindro.
Si el valor de desgaste máximo es superior a 0,15 mm, taladre los cilindros al tamaño de reparación más cercano, dejando un margen de 0,03 mm para el diámetro a bruñir.
Luego, pula los cilindros, manteniendo un diámetro tal que al instalar el pistón de reparación seleccionado, el espacio calculado entre este y el cilindro sea de 0,025 a 0,045 mm.
Reemplazo de bujías
Reemplazo de tapones del canal de aceite:
- - taladrar en el centro del tapón 1, Figuras 5 y 6, un agujero con un diámetro de 4-5 mm;
- - quitar el tapón del bloque 2;
- - eliminar las rebabas, limpiar y desengrasar la superficie de asiento del tapón;
- - desengrasar la bujía nueva;
- - aplicar pegamento anaeróbico a la superficie de asiento del bloque de cilindros debajo del tapón (pegamento anaeróbico AN-112);
al instalar el enchufe 1/01586/01:
- - instalar el tapón 1, (Fig. 5), en el orificio del canal de aceite y asentarlo;
- - calafatee el ajuste del enchufe;
al instalar el enchufe 21083-1002046:
- - instale el tapón 1 (Fig. 6) en el orificio del canal de aceite y presiónelo con un mandril. La profundidad de prensado está asegurada tecnológicamente (mandril 67.7853-9631).
Reemplazo de tapones del sistema de enfriamiento:
- - taladre un agujero con un diámetro de 6-7 mm en el tapón a una distancia de 1/4 de su diámetro desde el borde, como se muestra en la Figura 7;
- - colocar el tapón en el lado diametralmente opuesto al orificio hasta que aparezca un espacio entre la pared interior del bloque de cilindros y el borde del tapón;
- - inserte el firmware o la varilla tecnológica en el orificio y retire el tapón del bloque de cilindros;
- - eliminar las rebabas, limpiar y desengrasar la superficie de asiento del tapón;
- - desengrasar la bujía nueva;
- - aplicar pegamento anaeróbico a la superficie de asiento del bloque de cilindros debajo del tapón (pegamento anaeróbico AN-112);
- - instale un tapón nuevo (mandril 67.7853-9590 para tapones 00001-0043299-01-0 con un diámetro de 40 mm, mandril 67.7853-9591 para tapones 00001-0043289-01-0 con un diámetro de 25 mm, martillo ).