Der Ausbau und die Demontage des Motorzylinderkopfes wird in den entsprechenden Artikeln besprochen.
Nach der Demontage des Zylinderkopfes müssen Sie alle Teile des Kopfes waschen und von Kohlenstoffablagerungen befreien.
Teile für die Inspektion vorbereiten.
Überprüfen Sie die Sitzfläche des Kopfes und die Höhe des Zylinderkopfes.
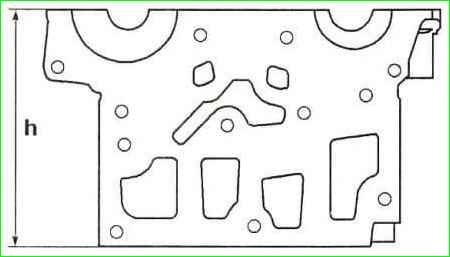
Die Höhe h des Blockkopfes sollte 137 mm betragen (Abbildung 1).
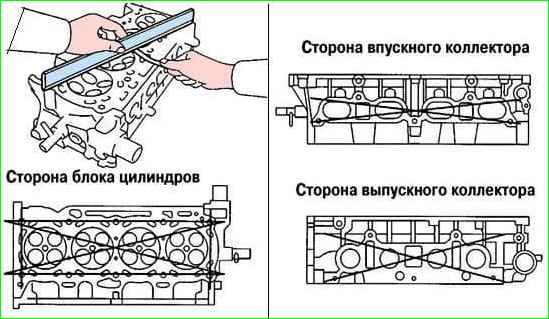
Überprüfen Sie mit einem Lineal und einer Fühlerlehre die Ebenheit der Sitzflächen des Zylinderkopfs (Abbildung 2).
Eine maximale Nichtebenheit von 0,05 mm ist zulässig. Flächenschleifen ist nicht erlaubt.
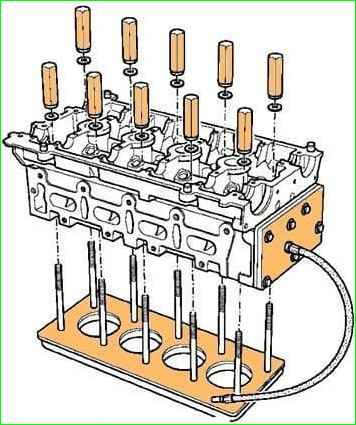
Überprüfen Sie den Zylinderkopf (keine Risse oder Durchrostung) mit dem entsprechenden Gerät (Abbildung 3).
Überprüfen Sie die Länge der Kopfbefestigungsschrauben. Die Länge der Schrauben ohne Kopf sollte nicht mehr als 117,7 mm betragen.
Wenn wir neue Schrauben einbauen, müssen diese vor dem Einbau nicht geschmiert werden; gebrauchte Schrauben müssen mit Motoröl geschmiert werden.
Ein nachträgliches Nachziehen der Zylinderkopfschrauben ist nicht erforderlich und nicht zulässig, da sonst die Wahrscheinlichkeit, dass die Schrauben beim Herausdrehen brechen, stark ansteigt.
Entfernen Sie vor dem Festziehen der Schrauben jeglichen Schmutz oder Ölreste in den Gewindelöchern des Zylinderblocks.
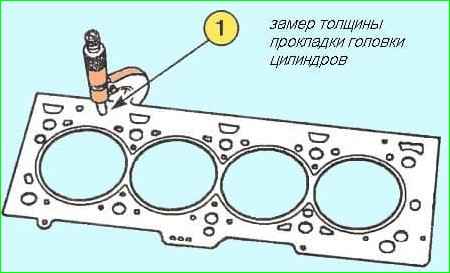
Messen Sie die Dicke der Dichtung (Abbildung 4). Die Dicke wird an der durch den Pfeil in Abbildung 4 angegebenen Stelle gemessen.
Die Dicke der neuen Dichtung sollte 0,96 ± 0,06 mm betragen; Die Dicke der komprimierten Dichtung sollte 0,90 ± 0,02 mm betragen.
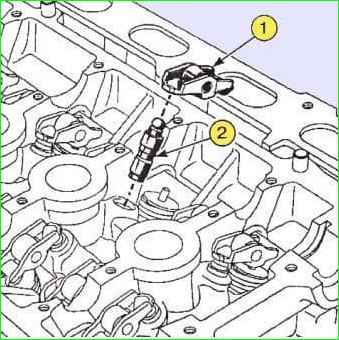
Überprüfen Sie die hydraulischen Stößel und Kipphebel.
Wir vermessen die Ventile gemäß Abbildung 6.
Ventilgrößen müssen mit den Angaben in der Tabelle übereinstimmen.
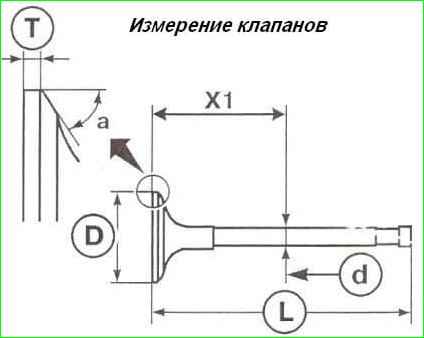
Abmessungen des Hauptventils
Name Größe mm.
Stangendurchmesser D1:
- Einlassventile 5.470-5.485*
- Auslassventile 5.456-5.471*
Kopfdurchmesser D2:
- Einlassventile 32,70 ± 0,12
- Auslassventile 27,96 ± 0,12
Ventillänge L:
- Einlassventile 109.32
- Auslassventile 107.64
Arbeitsfasenwinkel A:
- Einlassventile 45˚ 45′
- Auslassventile 45˚
Mindestdicke des zylindrischen Flansches des Ventiltellers T:
- Einlassventile 1,15
- Auslassventile 1,27
Ventilhub:
- Einlassventile 9.221
- Auslassventile 8.075
* Durchmesser D1 des Ventilschafts wird im Abstand X1 gemessen
- Einlassventile X1 = 75,14 ± 0,35 mm;
- Auslassventile X1 = 77,5 ± 0,35 mm;
Ventilführungen
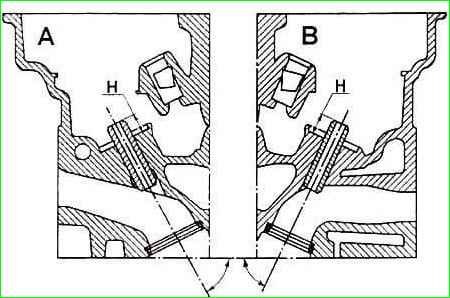
Die Neigung der Einlassventilführung beträgt 63˚30′ (Abbildung 7).
Die Neigung der Auslassventilführung beträgt 66°.
Die Höhe des hervorstehenden Teils der Ventilführung H beträgt 11 ± 0,15 mm für Einlass- und Auslassventile.
Ventildichtungen
Die Ventilschaftdichtungen werden mit dem Werkzeug Mot1335 entfernt.
Der Einbau der Ventilschaftdichtungen erfolgt gemäß blinkt Mot1511.
Die Wellendichtringe dürfen vor dem Einbau nicht geschmiert werden.
Ventilschaftdichtungen gemäß den Anweisungen in Abbildung 8 einbauen.
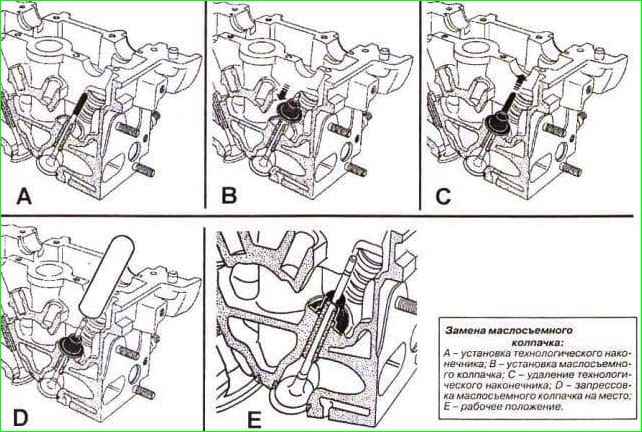
- - Setzen Sie das Ventil in den Zylinderkopf ein.
- - Setzen Sie die Spitze des Werkzeugs Mot1511 auf den Ventilschaft (der Innendurchmesser der Spitze muss dem Durchmesser des Schafts entsprechen) (siehe Abb. 8).
- - Drücken Sie das Ventil gegen den Sitz.
- - Bringen Sie die ungefettete Öldichtung an der Spitze an.
- - Schieben Sie die Öldichtung vor, indem Sie sie durch die Spitze schieben.
- - Entfernen Sie die Spitze.
- - Bringen Sie den Dorn an der Ventilschaftdichtung an. Der Innendurchmesser des Dorns muss mit dem Durchmesser des Ventilschafts übereinstimmen.
Außerdem sollte der untere Teil des Dorns teilweise an der Öldichtung anliegen, und zwar entlang der Fläche, die als Stütze für die Ventilfederscheibe dient.
- - Drücken Sie vorsichtig auf die Öldichtung, indem Sie mit Ihrer Handfläche auf die Oberseite des Dorns klopfen, bis die Öldichtung den Zylinderkopf berührt (siehe E, Abb. 8).
- - Wiederholen Sie die obigen Schritte für alle Ventile.
Ventilfedern prüfen
Federdefekte sind in Abbildung 9 dargestellt.
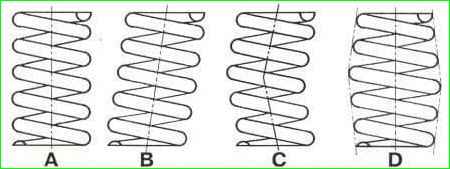
Bei den Verformungen B und C ist der Betrieb der Feder zulässig, wenn die Abweichung von der Vertikalen nicht mehr als 1,2 mm beträgt; wenn sie ihre Form verliert (D), muss die Feder ersetzt werden.
Auch wenn die Form der Feder erhalten bleibt, ist es notwendig, ihre mechanischen Eigenschaften (Höhe unter einer bestimmten Belastung) zu überprüfen.
Erst nach einer solchen Prüfung wird die Eignung der Feder für den weiteren Betrieb festgestellt (siehe Tabelle).
Ventilfederparameter
Parameter - mm
Freie Höhe 41,30
Federhöhe im betriebsbereiten Zustand 23,20
Innendurchmesser 18,80 ± 0,20
Außendurchmesser 27 ± 0,2
Drahtquerschnitt – Oval
Höhe / unter Last
- 34,50/180-200
- 24,50/563-617
Wenn Sie eine neue Feder haben, können Sie deren Eigenschaften mit den Eigenschaften der alten Federn vergleichen.
Montieren Sie die neue und die alte Feder nacheinander durch die Unterlegscheiben auf der langen Schraube.
Ziehen Sie die Schraubenmutter fest, sodass sich die Höhe der neuen Feder um 10 mm verringert.
Messen Sie die Höhe der alten Feder.
Wenn die Höhe der alten Feder von 9 auf 11 mm (±10 %) abgenommen hat, funktioniert sie immer noch. Wenn mehr, ersetzen Sie die alte Feder.
Ventilspiel in der Führungshülse prüfen
Die Überprüfung des Spalts zwischen Ventilschaft und Ventilführung kann auf zwei Arten erfolgen.
Erste Methode
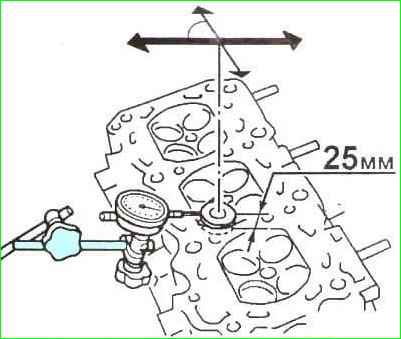
Heben Sie den Ventilkopf um 25 mm an und messen Sie dann mit einem Indikator die Bewegung des Ventils in Richtung der Pfeile (siehe Abb. 10) in einem Winkel von 90˚ zur Nockenwellenachse.
Die Hälfte des resultierenden Wertes ergibt den Wert des Spalts zwischen der Stange und der Ventilführung.
Zweite Methode
Messen Sie den Durchmesser des Ventilschafts und den Innendurchmesser der Führungshülse (siehe Abb. 11).
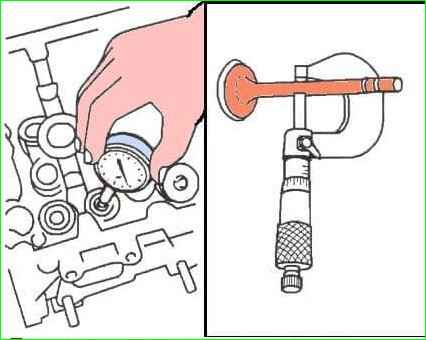
Nennspiel, mm:
- - Einlassventile 0,015–0,048;
- - Auslassventile 0,029–0,062.
Nockenwellen prüfen
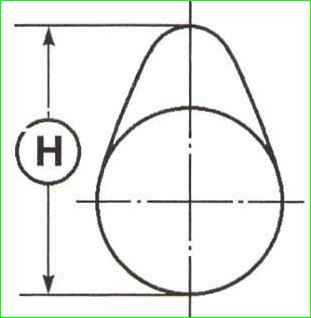
Die Höhe der Nockenwellen H (siehe Abb. 12) muss mit den Angaben in der Tabelle übereinstimmen.
Nockenwellenabmessungen
Parameter mm
Axialspiel der Nockenwellen:
- Einlass- und Auslassventile 0,080–0,178
- Diametraler Abstand zur Unterstützung ah 0,040-0,082
- Anzahl der Stützen 6
Durchmesser des Nockenwellenzapfens (siehe Abbildung 14):
- - Hälse Nr. 1; 24.979-25.000
- - Hälse Nr. 2, 3, 4, 5; 24.979-25.000
- - Hals Nr. 6 27.979-28.061
Backenhöhe H (Abb. 12):
- - Einlassventile 40,661 ± 0,030
- - Auslassventile 40,038 ± 0,030
Ansonsten Nockenwelle austauschen oder Reparaturen durchführen.
Die Hauptabmessungen der Nockenwellen sind in der Tabelle aufgeführt.
- - Überprüfen Sie dazu das Spiel der Nockenwellenzapfen in den Zylinderkopfstützen;
- - Bringen Sie die Zylinderkopfabdeckung wieder an und ziehen Sie die Befestigungsschrauben mit dem Standard-Anzugsdrehmoment fest.
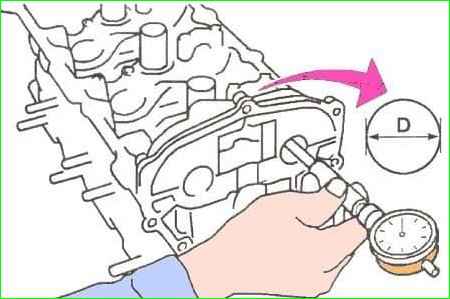
- Messen Sie mit einem Bohrmessgerät die Durchmesser aller Löcher in den Nockenwellenhalterungen (siehe Abb. 13) und notieren Sie die Messergebnisse.
Hinweis. Die Messungen sollten in der vertikalen Ebene des maximalen Verschleißes erfolgen.
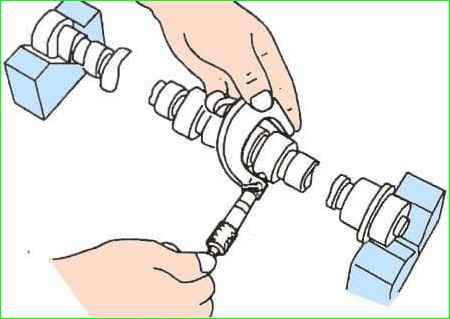
- Messen Sie mit einem Mikrometer die Durchmesser der Nockenwellenzapfen (siehe Abb. 14).
Die Messungen müssen an jedem Hals in zwei senkrechten Ebenen durchgeführt werden. Nehmen Sie den kleinsten Wert am Hals als Basiswert.
- Vergleichen Sie die Messergebnisse mit den maximal zulässigen Werten.
Berechnen Sie dann die Lücken für alle Zeitschriften und vergleichen Sie die erhaltenen Werte mit den maximal zulässigen Werten.
Den Ergebnissen zufolge:
- Ersetzen Sie die Nockenwelle, den Zylinderkopf oder beides.
Hinweis. Bei Verschleiß der Nockenwelle und des Zylinderkopfes sind restaurative Reparaturen (Spritzen mit anschließender Bearbeitung) möglich.
Oft sind solche Reparaturen viel günstiger als der Kauf neuer Teile.
- Wenn frühere Kontrollen nicht ergeben haben, dass Teile ausgetauscht werden müssen, überprüfen Sie das Axialspiel der Nockenwellen wie unten beschrieben und ersetzen Sie gegebenenfalls verschlissene Teile.
Wenn die Teile neu sind, überprüfen Sie sie trotzdem. Das ist nicht schwierig, aber wichtig für das Vertrauen in die Ergebnisse der Reparatur.
- - Installieren Sie die Nockenwellen und achten Sie auf deren korrekte Position.
- - Installieren Sie die Zylinderkopfabdeckung.
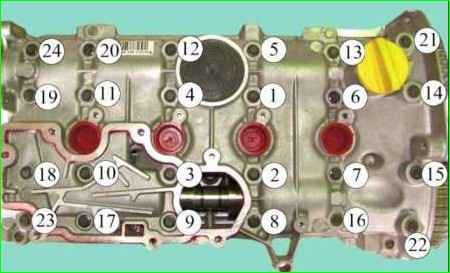
- - In der in Abb. gezeigten Reihenfolge festziehen. 15, erforderliches Drehmoment:
- - Zylinderkopf-Befestigungsschrauben 13, 20, 22, 23, Nm 8;
- - Zylinderkopfdeckel-Befestigungsschrauben von 1 bis 12, von 14 bis 19 und von 21 bis 24, Nm 12.
- - Lösen Sie die Kopfdeckelschrauben 13, 20, 22, 23.
- - Ziehen Sie die Zylinderkopfdeckelschrauben 13, 20, 22, 23 in der angegebenen Reihenfolge mit einem Drehmoment von 12 Nm an.
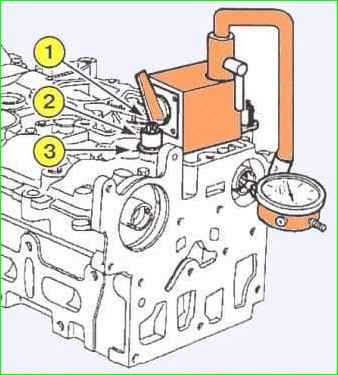
Befestigen Sie den Magnetständer des Axialspielprüfers Mot588 mit der Befestigungsstange (3) des Mot588-Werkzeugs am Zylinderkopf und ziehen Sie ihn mit den Ölabscheider-Befestigungsschrauben (1) und Distanzstücken (2) mit den folgenden Abmessungen fest ( siehe Abb. .16):
- - Außendurchmesser, mm - 18;
- - Bolzenlochdurchmesser, mm - 9;
- - Höhe, mm - 15.
- - Überprüfen Sie das Axialspiel der Nockenwelle, das im Bereich von 0,080–0,178 mm liegen sollte.
- - Entfernen Sie die Zylinderkopfhaube und die Nockenwellen.