Дизель ЯМЗ-238 обладнаний турбокомпресором, який використовує енергію вихлопних газів для наддуву двигуна
Збільшуючи масу повітря, що надходить у циліндри, турбокомпресор сприяє більш ефективному згоранню збільшеної дози палива, за рахунок чого підвищується потужність двигуна при помірній тепловій напруженості.
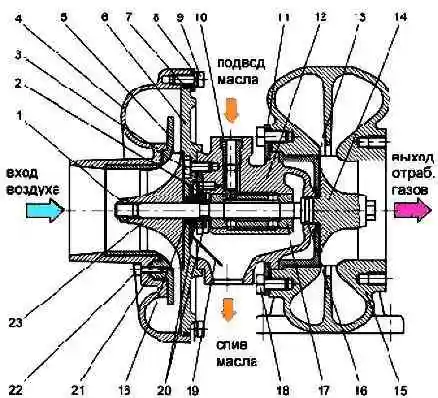
Турбокомпресор: 1 - гайка кріплення колеса компресора; 2 - упорний підшипник; 3 – болт; 4 – корпус компресора; 5 – вставка; 6 – кришка корпусу компресора; 7 - кільце ущільнювальне; 8 – пластина компресора; 9 – болт; 10 – болт-стопор; 11 – пластина турбіни; 12 – корпус підшипника; 13 – проставка корпусу турбіни; 14 – колесо турбіни з валом; 15 – корпус турбіни; 16 - кільця ущільнювальні; 17 – втулка; 18 – болт; 19 - екран маслоскид; 20 - упорні шайби; 21 - кільце ущільнювальне; 22 - гвинт; 23 - колесо компресора
Турбокомпресор (рис. 1) складається з одноступінчастого відцентрового компресора та радіальної доцентрової турбіни.
Колесо турбіни 14 та колесо компресора 23 розташовані на протилежних кінцях валу ротора консольно по відношенню до втулки підшипника 17.
Робоче колесо 23 відцентрового компресора — напіввідкритого типу, із загнутими проти обертання лопатками, відлито з алюмінієвого сплаву.
Вона напресована на вал і закріплена гайкою 1, встановленою з герметиком.
Робоче колесо турбіни 14 — напіввідкритого типу, з радіальними лопатками, виготовлене методом лиття із жароміцного сплаву. Воно пов'язане з валом методом зварювання тертям.
Корпус турбіни виготовлений із жароміцного чавуну. Газ підводиться до колеса турбіни двома каналами, що звужуються.
На торці корпусу турбіни є шпильки для кріплення випускного трубопроводу.
Корпус компресора 4, вставка та кришка корпусу підшипника 6 виготовлена з алюмінієвого сплаву.
Кришка корпусу підшипника 6 кріпиться до корпусу підшипника болтами 3 із застосуванням герметика.
У турбокомпресорі застосований підшипник ковзання 17 у вигляді втулки, виготовленої з алюмінієвого сплаву.
Вона встановлена у розточуванні чавунного корпусу підшипника 12 і утримується від осьових переміщень болтом-стопором 10.
Змащування втулки турбокомпресора здійснюється під тиском із системи змащення двигуна.
Ретельно відбалансований ротор встановлений у втулці 17.
Осьові зусилля, що діють на ротор, сприймаються завзятим підшипником 2. На кожному кінці валу ротора встановлені розрізні кільця ущільнювача 16, виготовлені зі спеціального чавуну.
Турбокомпресор кріпиться до випускних колекторів корпусом турбіни.
Вихідний патрубок корпусу компресора з'єднаний через патрубки та охолоджувач наддувного повітря з впускними колекторами двигуна.
Технічне обслуговування турбокомпресора
Технічне обслуговування турбокомпресора проводити через кожні 3000 годин роботи двигуна.
При технічному обслуговуванні перевірити осьовий та радіальний люфти ротора за допомогою індикатора.
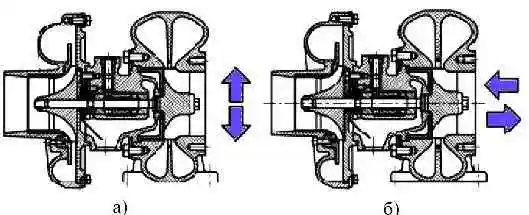
Люфт визначається як різниця показань індикатора при відхиленні валу у двох взаємно протилежних напрямках (рис. 2).
Припустимі граничні величини люфтів осьовий - 0,20 мм, радіальний - 0,80 мм. Якщо люфти більші від граничних значень, турбокомпресор треба замінити.
Один раз на рік видаляти відкладення з корпусу турбіни компресора та з робочих коліс.
Очищення деталей компресора проводити за допомогою бензину, деталей турбіни - за допомогою декарбонізатора.
Під час встановлення турбокомпресора на двигун ретельно простежити за чистотою трубопроводів, що приєднуються до турбокомпресора та відсутність у них предметів та сміття.
Після встановлення турбокомпресора заповнити корпус підшипників чистою олією через отвір підведення олії.
Ретельно стежити за відсутністю підсмоктування та підтікань у повітряних, газових, масляних трубопроводах та їх з'єднаннях.
Слід мати на увазі, що оптимальний режим роботи турбокомпресора здійснюється в діапазоні вищої частоти обертання колінчастого валу двигуна.
Розбирання та складання турбокомпресора
Для очищення деталей турбокомпресора здійснити його часткове розбирання, для цього:
- 1. Зняти турбокомпресор із двигуна.
- 2. Нанести мітки на корпуси турбокомпресора з таким розрахунком, щоб зберегти взаємне розташування корпусів при збиранні.
- 3. Відвернути болти корпусу компресора і зняти корпус, не допускаючи його перекосу, таким чином щоб не пошкодити лопатки колеса компресора.
- 4. Відвернути болти кріплення корпусу турбіни та зняти корпус. При утрудненому відвертанні болтів змастити їх різьблення дизельним паливом.
Наступне розбирання турбокомпресора в умовах експлуатації не допускається.
Складання турбокомпресора проводити в порядку, зворотному розбиранні. Корпуси встановлювати обережно, оберігаючи від пошкодження лопатки робочих коліс.
Для забезпечення правильного взаємного розташування корпусів, використовувати мітки, нанесені перед розбиранням.
Так само дивимося статтю - Ремонт турбокомпресора автомобіля МАЗ
Обслуговування повітряного фільтра
Несвоєчасне обслуговування повітряного фільтра погіршує очищення повітря і призводить до проникнення пилу в двигун, що спричиняє підвищений знос циліндропоршневої групи та передчасний вихід двигуна з ладу.
Для нормальної роботи двигуна потрібне регулярне обслуговування повітряного фільтра, а також постійна увага до стану його деталей, особливо ущільнювальних прокладок, та до правильної установки повітряного фільтра.
Обслуговування першого ступеня повітряного фільтра проводити періодично під час сезонного обслуговування.
При тривалій роботі в умовах підвищеної запиленості та при різких змінах умов довкілля терміни обслуговування визначати, виходячи з досвіду роботи в даних умовах та стану першого ступеня.
Для обслуговування першого ступеня фільтра відвернути гайки кріплення бункера. Зняти бункер, заглушку бункера та видалити з нього пил.
Відвернути гайку кріплення фільтруючих елементів та вийняти їх.
Корпус повітряного фільтра промити в бензині, дизельному паливі або гарячій воді, просушити.
При збиранні повітряного фільтра звернути увагу:
- на стан ущільнювальних прокладок. Прокладки, що мають надриви, замінити. Якість ущільнення контролювати наявність суцільного відбитка на прокладці.
- при використанні двох фільтруючих елементів встановлення проставки між ними є обов'язковим.
- стрілка на бункері повинна бути спрямована вгору.
Фільтруючий елемент слід обслуговувати за показанням індикатора засміченості повітряного фільтра: у разі відсутності індикатора — при ТО-2, а в умовах підвищеної запиленості частіше, виходячи з досвіду експлуатації в цих умовах.
Орієнтовний термін служби фільтруючого елемента становить 1500 годин.
Занадто часто обслуговування фільтруючого елемента скорочує термін його служби, оскільки загальна кількість обслуговування елемента обмежена (не більше 6 разів) через можливе руйнування, фільтруючого картону.
Для обслуговування елемента зняти бункер, відвернути гайку кріплення та вийняти елемент із корпусу фільтра.
При наявності на картоні елемента пилу без сажі або при негайному його використанні обдути елемент сухим стиснутим повітрям до повного видалення пилу.
Щоб уникнути прориву фільтруючого картону, тиск стисненого повітря повинен бути не більше 300 кПа (3 кгс/см 2).
Струм повітря слід направляти під кутом до поверхні та регулювати силу струменя зміною відстані шланга від елемента.
При наявності на картоні пилу, сажі, олії, якщо обдув стисненим повітрям неефективний, промити елемент у розчині миючої речовини ОП-7 або ОП-10 (ГОСТ 8433-81) у теплій (40-50°С) воді концентрації 20 -25 г речовини на 1 літр води.
Замість розчину ОП-7 або ОП-10 можна використовувати розчин тієї ж концентрації пральних порошків побутового призначення.
Для промивання елемента завантажити його на півгодини у вказаний розчин з подальшим інтенсивним обертанням або зануренням у розчині протягом 10-15 хвилин.
Після промивання в розчині прополоскати елемент у чистій теплій воді та ретельно просушити.
Для просушування забороняється застосовувати відкрите полум'я та повітря з температурою понад 70°С.
Після кожного обслуговування елемента або під час встановлення нового перевірити його стан візуально, підсвічуючи зсередини лампою.
За наявності механічних пошкоджень, розриву гофр картону, відшаровування кришок та картону від клею, що може призвести до пропуску пилу, елемент замінити.
Новий фільтруючий елемент 8421.1109080, 238Н-1109080 повинен містити:
- 215-220 гофр при ширині гофри 55 мм;
- 235-245 гофр при ширині гофри 48-50 мм.
Перевірка герметичності впускного тракту
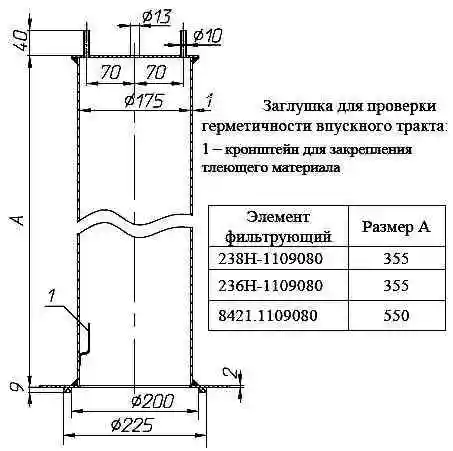
Герметичність впускного тракту повинна забезпечуватися ущільнювальними та кріпильними деталями проміжних трубопроводів.
Звертати увагу на стан і правильність установки ущільнювальних і кріпильних деталей системи: рукавов, прокладок, хомутів.
За потреби замінити.
За відсутності герметичності в циліндри двигуна разом з повітрям неминуче потраплятиме пил і бруд, що призведе до передчасного зносу деталей циліндропоршневої групи.
Контроль герметичності впускного тракту проводити шляхом створення в тракті надлишкового тиску з додаванням диму.
Для перевірки герметичності впускного тракту замість фільтруючого елемента встановити заглушку (див. рис. 3) із закріпленим усередині неї тліючим матеріалом (паклів, технічною ватою та ін.).
Розміри заглушки залежать від розмірів фільтруючого елемента повітряного фільтра, на місце якого встановлюється заглушка.
До однієї з трубок Ø10х1 заглушки приєднати джерело стисненого повітря, до іншої – контрольну трубку з краном або затискачем.
В якості джерела стисненого повітря можна користуватися насосом для накачування шин або промисловою мережею з тиском повітря 10–20 кПа (0,1–0,2 кгс/см 2); вищий тиск призведе до руйнування трубопроводів.
Відкривши на якийсь час контрольну трубку, переконатися в заповненні впускного тракту димом, після чого протягом 2–3 хвилин подавати в тракт повітря, перевіряючи зовнішнім оглядом стан впускного тракту.
У місцях негерметичності спостерігатиметься вихід диму.