Der YaMZ-238-Dieselmotor ist mit einem Turbolader ausgestattet, der die Energie der Abgase nutzt, um den Motor anzukurbeln
Durch die Erhöhung der in die Zylinder eintretenden Luftmasse trägt der Turbolader zu einer effizienteren Verbrennung der erhöhten Kraftstoffdosis bei und erhöht so die Motorleistung bei mäßiger thermischer Belastung.
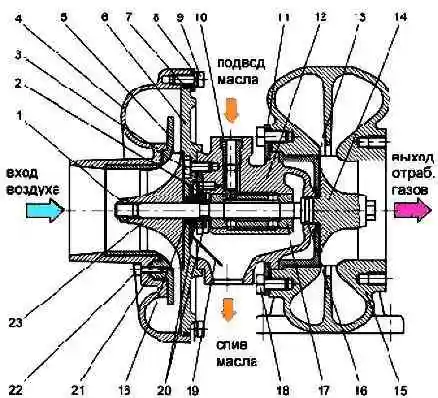
Turbolader: 1 - Kompressorradmutter; 2 - Axiallager; 3 - Bolzen; 4 - Kompressorgehäuse; 5 - einfügen; 6 - Abdeckung des Kompressorgehäuses; 7 - Dichtungsring; 8 - Kompressorplatte; 9 - Bolzen; 10 - Riegelstopper; 11 - Turbinenplatte; 12 - Lagergehäuse; 13 – Distanzstück des Turbinengehäuses; 14 - Turbinenrad mit Welle; 15 - Turbinengehäuse; 16 - Dichtungsringe; 17 - Buchse; 18 - Bolzen; 19 - Öltropfensieb; 20 - Anlaufscheiben; 21 - Dichtungsring; 22 - Schraube; 23 - Verdichterrad
Der Turbolader (Abb. 1) besteht aus einem einstufigen Radialverdichter und einer radialen Zentripetalturbine.
Das Turbinenrad 14 und das Kompressorrad 23 befinden sich an gegenüberliegenden Enden der Rotorwelle und sind in Bezug auf die Lagerhülse 17 freitragend.
Das Laufrad 23 des Radialkompressors ist ein halboffener Typ mit entgegen der Rotation gebogenen Schaufeln und ist aus einer Aluminiumlegierung gegossen.
Es wird auf die Welle gepresst und mit Mutter 1 gesichert, mit Dichtmittel montiert.
Das Turbinenlaufrad 14 ist ein halboffener Typ mit radialen Schaufeln und wird durch Gießen aus einer hitzebeständigen Legierung hergestellt. Die Verbindung mit der Welle erfolgt durch Reibschweißen.
Das Turbinengehäuse besteht aus hitzebeständigem Gusseisen. Die Gaszufuhr zum Turbinenrad erfolgt über zwei sich verengende Kanäle.
Am Ende des Turbinengehäuses befinden sich Stehbolzen zur Befestigung der Abgasleitung.
Kompressorgehäuse 4, Lagergehäuseeinsatz und Deckel 6 bestehen aus einer Aluminiumlegierung.
Der Lagergehäusedeckel 6 wird mit Schrauben 3 und Dichtmittel am Lagergehäuse befestigt.
Der Turbolader verwendet ein Gleitlager 17 in Form einer Hülse aus einer Aluminiumlegierung.
Es ist in der Bohrung des gusseisernen Lagergehäuses 12 installiert und wird durch einen Anschlagbolzen 10 vor axialen Bewegungen geschützt.
Die Schmierung der Turboladerbuchse erfolgt unter dem Druck des Motorschmiersystems.
Der sorgfältig ausgewuchtete Rotor ist in der Nabe 17 montiert.
Axialkräfte, die auf den Rotor wirken, werden vom Axiallager 2 aufgenommen. An jedem Ende der Rotorwelle sind geteilte Dichtringe 16 aus Spezialgusseisen verbaut.
Der Turbolader ist über das Turbinengehäuse an den Abgaskrümmern befestigt.
Der Auslass des Kompressorgehäuses ist über die Rohre und den Nachkühler mit den Ansaugkrümmern des Motors verbunden.
Wartung des Turboladers
Die Wartung des Turboladers sollte alle 3000 Betriebsstunden des Motors durchgeführt werden.
Überprüfen Sie bei der Wartung das Axial- und Radialspiel des Rotors mit einem Messgerät.
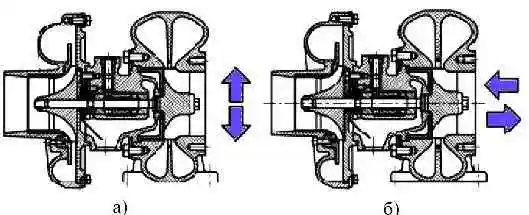
Das Spiel ist definiert als die Differenz zwischen den Anzeigewerten, wenn die Welle in zwei zueinander entgegengesetzte Richtungen abweicht (Abb. 2).
Zulässige Grenzspielwerte axial – 0,20 mm, radial – 0,80 mm. Wenn das Spiel größer als die Grenzwerte ist, muss der Turbolader ausgetauscht werden.
Entfernen Sie einmal im Jahr Ablagerungen vom Verdichterturbinengehäuse und den Laufrädern.
Kompressorteile sollten mit Benzin gereinigt werden, Turbinenteile – mit einem Kalzinator.
Überwachen Sie beim Einbau des Turboladers am Motor sorgfältig die Sauberkeit der mit dem Turbolader verbundenen Rohrleitungen und das Fehlen von Gegenständen und Fremdkörpern darin.
Nach dem Einbau des Turboladers füllen Sie das Lagergehäuse über den Öleinlass mit sauberem Öl.
Überwachen Sie sorgfältig die Abwesenheit von Lecks und Undichtigkeiten in Luft-, Gas- und Ölleitungen und deren Verbindungen.
Es ist zu beachten, dass der optimale Betrieb des Turboladers im Bereich einer höheren Motordrehzahl erfolgt.
Demontage und Montage des Turboladers
Um die Teile des Turboladers zu reinigen, führen Sie dessen teilweise Demontage durch:
- 1. Entfernen Sie den Turbolader vom Motor.
- 2. Bringen Sie Markierungen an den Turboladergehäusen an, um die relative Position der Gehäuse während der Montage beizubehalten.
- 3. Lösen Sie die Schrauben des Kompressorgehäuses und entfernen Sie das Gehäuse. Achten Sie dabei darauf, es nicht zu verkanten Achten Sie darauf, die Verdichterradschaufeln nicht zu beschädigen.
- 4. Lösen Sie die Schrauben, mit denen das Turbinengehäuse befestigt ist, und entfernen Sie das Gehäuse. Wenn sich die Schrauben nur schwer lösen lassen, schmieren Sie ihre Gewinde mit Dieselkraftstoff.
Eine weitere Demontage des Turboladers unter Betriebsbedingungen ist nicht zulässig.
Montieren Sie den Turbolader in umgekehrter Reihenfolge wie beim Zerlegen. Montieren Sie die Gehäuse sorgfältig und schützen Sie dabei die Schaufeln der Laufräder vor Beschädigungen.
Um die korrekte relative Position der Koffer sicherzustellen, verwenden Sie die vor der Demontage angebrachten Markierungen.
Wir schauen uns auch den Artikel an – Reparatur des Turboladers eines MAZ-Autos
Wartung des Luftfilters
Eine vorzeitige Wartung des Luftfilters beeinträchtigt die Luftreinigung und führt zum Eindringen von Staub in den Motor, was zu einem erhöhten Verschleiß der Zylinder-Kolben-Gruppe und einem vorzeitigen Motorausfall führt.
Der ordnungsgemäße Betrieb des Motors erfordert eine regelmäßige Wartung des Luftfilters sowie eine ständige Aufmerksamkeit auf den Zustand seiner Teile, insbesondere der Dichtungen, und auf die korrekte Installation des Luftfilters.
Die Wartung der ersten Stufe des Luftfilters sollte regelmäßig während der saisonalen Wartung durchgeführt werden.
Beim Arbeiten über einen längeren Zeitraum unter Bedingungen mit erhöhter Staubentwicklung und bei plötzlichen Änderungen der Umgebungsbedingungen sollten die Servicebedingungen auf der Grundlage der Erfahrungen unter diesen Bedingungen und des Zustands der ersten Stufe festgelegt werden.
Um die erste Stufe des Filters zu warten, lösen Sie die Muttern, mit denen der Trichter befestigt ist. Entfernen Sie den Trichter und den Trichterdeckel und entfernen Sie Staub davon.
Lösen Sie die Mutter, mit der die Filterelemente befestigt sind, und entfernen Sie sie.
Waschen Sie das Luftfiltergehäuse in Benzin, Dieselkraftstoff oder heißem Wasser und trocknen Sie es.
Achten Sie beim Zusammenbau des Luftfilters darauf:
- auf den Zustand der Dichtungen. Ersetzen Sie zerrissene Dichtungen. Die Qualität der Dichtung wird durch das Vorhandensein eines durchgehenden Aufdrucks auf der Dichtung kontrolliert.
- Bei Verwendung von zwei Filterelementen ist ein Abstandshalter dazwischen erforderlich.
- Der Pfeil auf dem Trichter sollte nach oben zeigen.
Das Filterelement sollte entsprechend der Anzeige der Luftfilter-Verstopfungsanzeige gewartet werden: bei Fehlen einer Anzeige – bei TO-2 und bei Bedingungen mit erhöhter Staubentwicklung – häufiger, basierend auf der Betriebserfahrung unter diesen Bedingungen.
Die geschätzte Lebensdauer des Filterelements beträgt 1500 Stunden.
Eine zu häufige Wartung des Filterelements verringert seine Lebensdauer, da die Gesamtzahl der Elementwartungen aufgrund einer möglichen Zerstörung der Filterpappe begrenzt ist (nicht mehr als 6 Mal).
Um das Element zu warten, entfernen Sie den Trichter, lösen Sie die Befestigungsmutter und entfernen Sie das Element aus dem Filtergehäuse.
Wenn sich rußfreier Staub auf dem Kartonelement befindet oder es sofort verwendet werden soll, blasen Sie das Element mit trockener Druckluft aus, bis der Staub vollständig entfernt ist.
Um zu verhindern, dass das Filterpapier platzt, sollte der Druckluftdruck 300 kPa (3 kgf/cm 2) nicht überschreiten.
Der Luftstrahl sollte in einem Winkel zur Oberfläche gerichtet sein und die Stärke des Strahls durch Ändern des Abstands des Schlauchs vom Element anpassen.
Wenn sich Staub, Ruß oder Öl auf dem Karton befinden und das Anblasen mit Druckluft wirkungslos ist, waschen Sie das Element in einer Lösung aus Reinigungsmittel OP-7 oder OP-10 (GOST 8433-81) in warmem (40-50 °C). °C) Wasser mit einer Konzentration von 20 -25 g Substanz pro 1 Liter Wasser.
Anstelle einer Lösung von OP-7 oder OP-10 können Sie eine Lösung mit der gleichen Konzentration von Haushaltswaschpulvern verwenden.
Um das Element zu waschen, tauchen Sie es eine halbe Stunde lang in die angegebene Lösung und drehen Sie es anschließend intensiv oder tauchen Sie es 10–15 Minuten lang in die Lösung.
Spülen Sie das Element nach dem Spülen in der Lösung mit klarem, warmem Wasser ab und trocknen Sie es gründlich ab.
Zum Trocknen ist die Verwendung einer offenen Flamme und Luft mit einer Temperatur über 70 °C verboten.
Überprüfen Sie nach jeder Wartung des Elements oder beim Einbau eines neuen Elements dessen Zustand visuell, indem Sie es von innen mit einer Lampe beleuchten.
Bei mechanischer Beschädigung, Bruch der Wellpappe, Ablösen von Abdeckungen und Karton vom Kleber, was zum Austreten von Staub führen kann, ersetzen Sie das Element.
Neues Filterelement 8421.1109080, 238Н-1109080 muss enthalten:
- 215-220 Wellen mit einer Wellenbreite von 55 mm;
- 235-245 Wellen mit einer Wellenbreite von 48-50 mm.
Prüfung der Dichtheit des Ansaugtrakts
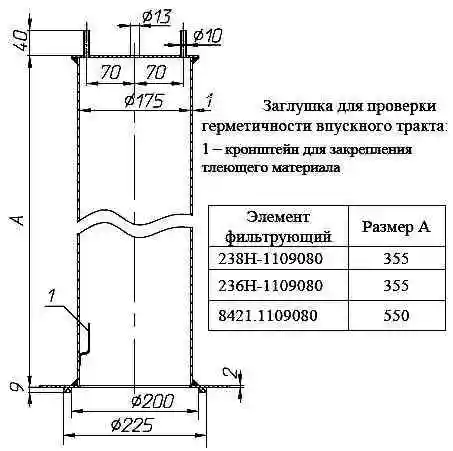
Die Dichtheit des Ansaugtraktes muss durch die Abdichtung und Befestigung der Zwischenleitungen gewährleistet sein.
Achten Sie genau auf den Zustand und die korrekte Installation der Dichtungen und Befestigungselemente des Systems: Hülse in, Dichtungen, Klemmen.
Bei Bedarf ersetzen.
Ohne Dichtheit gelangen unweigerlich Staub und Schmutz zusammen mit der Luft in die Motorzylinder, was zu einem vorzeitigen Verschleiß der Teile der Zylinder-Kolben-Gruppe führt.
Überprüfen Sie die Dichtheit des Ansaugtrakts, indem Sie unter Zugabe von Rauch einen Überdruck im Ansaugtrakt erzeugen.
Um die Dichtheit des Ansaugtrakts zu überprüfen, installieren Sie anstelle des Filterelements einen Stopfen (siehe Abb. 3), in dem sich schwelendes Material befindet (Kabel, Industriewatte usw.).
Die Größe des Stopfens hängt von der Größe des Luftfilterelements ab, an dessen Stelle der Stopfen installiert wird.
Schließen Sie eine Druckluftquelle an einen der Schläuche Ø10x1 des Steckers und einen Steuerschlauch mit Hahn oder Klemme an den anderen an.
Als Druckluftquelle können Sie eine Reifenfüllpumpe oder ein Industrienetz mit einem Luftdruck von 10–20 kPa (0,1–0,2 kgf/cm 2) verwenden; Höherer Druck würde die Rohrleitungen zerstören.
Öffnen Sie vorübergehend das Kontrollrohr, stellen Sie sicher, dass der Ansaugtrakt mit Rauch gefüllt ist, leiten Sie dann 2-3 Minuten lang Luft in den Ansaugtrakt und überprüfen Sie den Zustand des Ansaugtrakts durch äußere Inspektion.
An Stellen mit Lecks ist Rauchentwicklung zu beobachten.