Alle Dichtungen und Dichtungen der Pumpe und ihres Antriebs müssen bei der Montage ausgetauscht werden.
Der Zusammenbau der Pumpe erfolgt in umgekehrter Reihenfolge wie die Demontage.
Nach der Reparatur muss die Pumpe auf einem speziellen Stand auf Leistung überprüft werden.
Der Zusammenbau der Pumpe muss unter völlig sauberen Bedingungen erfolgen.
Vor dem Zusammenbau müssen alle gebrauchten Dichtungsteile und Dichtungen ausgetauscht, die Teile gewaschen und mit trockener Druckluft ausgeblasen werden.
Während der Montage müssen alle Passflächen der Pumpenteile mit Öl geschmiert werden, das für den hydraulischen Verstärker verwendet wird.
Um die Pumpe zusammenzubauen, muss sie auf einem speziellen Gerät (Abb. 1) installiert werden, sodass sich die Aufschrift „Input“ auf der Monteurseite befindet.
Pumpenbuchsen werden paarweise der gleichen Größengruppe eingebaut.
In jeder Größengruppe sollte sich die Höhe der Buchsen um nicht mehr als 0,005 mm unterscheiden.
Antriebs- und Abtriebszahnräder müssen ebenfalls derselben Größengruppe angehören.
In jeder Größengruppe sollte sich die Länge der Zähne um nicht mehr als 0,01 mm unterscheiden.
Vor der Montage müssen auch Buchsen und Zahnräder nach Größengruppen zusammengebaut werden.
Die Pumpe wird in der folgenden Reihenfolge zusammengebaut
Setzen Sie zwei untere Buchsen der gleichen Größengruppe in die Gehäuseschächte ein, installieren Sie dann das angetriebene Zahnrad 4 (Abb. 2) und das Antriebszahnrad 3 und schmieren Sie es bis zur Hälfte des oberen Lagerzapfens mit Öl.
Das Antriebszahnrad ist im rechten Schacht installiert und das angetriebene Zahnrad ist im linken Schacht installiert.
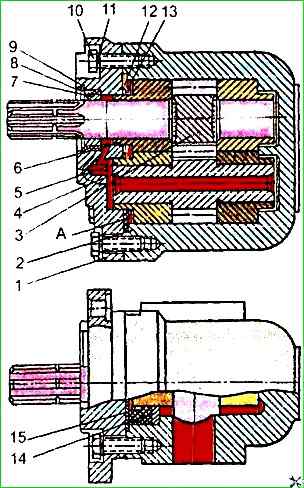
Führen Sie die oberen Buchsen in die Gehäuseschächte ein, bis sie die Stirnfläche der Zahnräder berühren. Normaler Kontakt wird durch Drehen der Buchsen im Uhrzeigersinn sichergestellt.
Installieren Sie die Auskleidung 14 in dem Sektor, der aus zwei gepaarten Buchsen besteht, bis sie das Ende der Aussparung auf der Seite des Lochs mit der Aufschrift „Input“ berührt.
Eine Spezialdichtung 15 mit dem zylindrischen Vorsprung nach oben in den Pumpengehäusebereich einbauen, bis sie die Oberfläche der Auskleidung 14 berührt.
Dann montieren Sie mit einem speziellen Dorn die Manschette 12 mit einer Aussparung oben für Ringe an den Buchsenhälsen.
Zuvor müssen die inneren zylindrischen Oberflächen der Manschette mit technischer Vaseline oder Litol-24-Gleitmittel geschmiert werden.
Ring 13 in die Manschettennut einsetzen.
Montieren Sie den Pumpendeckel 1 auf den Buchsenhälsen und schützen Sie dabei die Dichtfläche der Manschette vor Beschädigungen.
Die aus der Manschette herausragenden Dichtkanten müssen ins Innere des Pumpengehäuses gerichtet sein.
Schützen Sie das verzahnte Ende des Antriebszahnrads mit einer speziellen Kappe und führen Sie die Manschette 8 in den Pumpendeckel ein, nachdem Sie sie zuvor mit Öl geschmiert haben.
Nach dem Zusammenbau der Pumpe sollte die Abweichung zwischen den Ebenen des Deckels und der Buchsen 0,1 mm nicht überschreiten.
Danach muss die Pumpe in ein spezielles Gerät eingebaut werden, eine Führungshülse in das Loch im Deckel eingesetzt werden und ein Sicherungsring 9 in die Hülse eingesetzt werden.
Drücken Sie die Manschette bis zum Anschlag in die Abdeckung und ziehen Sie die Befestigungsschrauben der Abdeckung mit Federscheiben als Ganzes fest.
Der Zusammenbau des Pumpenantriebs und die Montage am Motor erfolgt in umgekehrter Reihenfolge wie die Demontage.
Überprüfung der Servolenkungspumpe nach der Montage
Die Qualität der Pumpenreparaturen kann an einem speziellen Stand überprüft werden, der mit Steuergeräten Mod. ausgestattet ist. KI-1774 oder KI-4200.
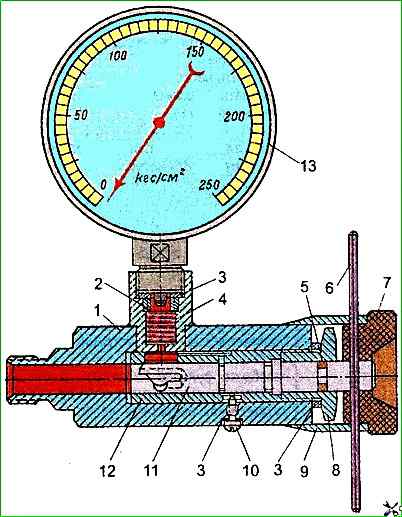
Die Überprüfung der Servolenkungspumpe auf einem Ständer vor dem Einbau in den Bus verhindert, dass die Pumpe nach der Reparatur aufgrund möglicher Fehlfunktionen wiederholt aus dem Bus entfernt werden muss.
Vor dem Test muss die Pumpe mit einer Drehzahl von 1200 min -1 im folgenden Modus betrieben werden:
- 2-3 Minuten – im Leerlauf;
- 3-4 Min. – bei einem Druck von 2 MPa;
- 3-4 Min. – bei einem Druck von 4 MPa;
- 3-4 Min. – bei einem Druck von 6 MPa;
- 3-4 Min. – bei einem Druck von 8 MPa;
- 2-3 Min. – bei einem Druck von 10 MPa.
Nach dem Einlaufen werden die Pumpen auf einem Stand getestet, wobei Fördermenge und volumetrischer Wirkungsgrad ermittelt werden. und Austreten von Arbeitsflüssigkeit durch den Abfluss der Pumpenwellendichtung.
Die Pumpenleistung muss bei einer Drehzahl von 1200 min -1 und einem Druck von 10 MPa mindestens 9,72 l/min betragen.
Volumeneffizienz Pumpe bei einer Temperatur von 50 °C, einem Druck von 10 MPa und einer Drehzahl von 1200 min -1 sollte nicht kleiner als 0,9 sein. Es ist zulässig, die Pumpe nach dem Einbau in den Bus mit dem Drosseldurchflussmesser KI-1097 zu überprüfen (siehe Abb. 3).