Bevor Sie mit der Einstellung beginnen, spülen Sie die Ölkammer der Pumpe und des Reglers mit sauberem Dieselkraftstoff und füllen Sie frisches Motoröl bis zur Höhe der Ablassöffnung ein. Verschließen Sie für die Dauer des Tests die Ablaufarmatur
Es wird empfohlen, Hochdruck-Kraftstoffpumpen an den Ständen von Motorpal, Friedman-Mayer und anderen Ständen ähnlicher Bauart anzupassen.
Der Ständer zum Einstellen von Hochdruck-Kraftstoffpumpen muss ausgestattet sein mit:
- – ein Mechanismus, der eine stufenlose Änderung der Drehzahl der Antriebswelle im Bereich von 0 bis 1500 min -1 ermöglicht
- – eine Vorrichtung zum Installieren und Befestigen der getesteten Pumpenbaugruppe mit einem Geschwindigkeitsregler, einer Kraftstoffeinspritz-Vorlaufkupplung und einer Kraftstoffansaugpumpe;
- - Kraftstofftank, grobe und feine Kraftstofffilter;
- – ein Kraftstoffsystem, das einen Kraftstoffdruck am Pumpenkopf von bis zu 2,3 MPa (23 kgf/cm 2) bereitstellt;
- – ein Gerät zum Messen und Probenehmen von Kraftstoffanteilen, die von jedem Abschnitt der Hochdruck-Kraftstoffpumpe geliefert werden;
- – ein Gerät zum Erhitzen von Kraftstoff und zum Halten seiner Temperatur im Bereich von (32 ± 2) ºС;
- – ein Zähler, der die Anzahl der Kolbenhübe aufsummiert und mit einer Vorrichtung zum Messen und Auswählen von Kraftstoffportionen gekoppelt ist;
- – Drehzahlmesser zum Einstellen des Geschwindigkeitsmodus;
- – ein Drehknopf zum Einstellen des Futterwechsels zwischen den Pumpenabschnitten;
- - Schwungrad auf der Pumpenantriebswelle mit einem Trägheitsmoment von 0,17 kg m 2 (1,7 kgf m.s 2);
- - die erforderliche Anzahl von Manometern, Vakuummetern und Rohrleitungen;
- - ein zusätzliches System zur Versorgung der Kraftstoffpumpe mit gefiltertem Öl mit einstellbarem Druck bis zu 0,4 MPa (4 kgf/cm 2) und ein Druckluftversorgungssystem mit einer Vorrichtung zur stufenlosen Druckregelung von 0 bis 0, 15 MPa (von 0 bis 1,5 kgf/cm 2) .
Ausrüstung und Geräte von Ständen müssen den Anforderungen von GOST 10578-95 entsprechen.
Zur Steuerung von Hochdruck-Kraftstoffpumpen ist neben Ständern folgende Ausrüstung erforderlich:
- - Waagen der mittleren Genauigkeitsklasse nach GOST 29329-92;
- – ein Gerät zur Kontrolle des Beginns der Wirkung des Reglers T 9597-111;
- – ein Gerät zur Steuerung des Hubumfangs des Schiebers T 9590-36.
Pumpentests sollten mit gefiltertem Dieselkraftstoff der Klasse L gemäß GOST 305-82 oder einer Prozessflüssigkeit, bestehend aus einer Mischung mit Industrieöl gemäß GOST 20799-88, Luftfahrtöl gemäß GOST 21743-76, durchgeführt werden oder Leuchtkerosin gemäß TU 38.401-58 -10-90, mit einer Viskosität von 5 bis 6 mm 2/s (cSt) bei einer Temperatur von (20 ± 5) ºС.
Es ist erlaubt, eine Mischung von Arbeitsflüssigkeiten zu verwenden, bestehend aus 40 % RZh-3 TU 38.101.964-83 und 60 % RZh-8 TU 38.101.883-33, mit einer Viskosität von 5 bis 6 mm 2 /s (cSt) bei einer Temperatur von (20 ± 5) ºС.
Die Temperatur des Kraftstoffs, gemessen am Auslassanschluss des Ständers mit der Kraftstoffleitung zur getesteten Pumpe, sollte bei der Kontrolle der Größe und Ungleichmäßigkeit der zyklischen Zufuhren (32 ± 2) ºС betragen.
Bevor Sie die Pumpe auf dem Ständer montieren, prüfen Sie das Axialspiel der Nockenwelle. Wenn der Spalt größer als 0,1 mm ist, passen Sie ihn mit Unterlegscheiben im Bereich von 0,01 bis 0,07 mm an.
Beim Anziehen der Lagerdeckelschrauben muss sich die Nockenwelle frei in den Lagern drehen lassen.
Die Überprüfung und Einstellung der Kraftstoffpumpe sollte mit einem Tischsatz von Einspritzdüsen des Modells 261-03С mit einer effektiven Durchflussfläche μf = 0,283 mm 2 durchgeführt werden.
Es ist erlaubt, die Kraftstoffpumpe mit einem funktionierenden Satz Einspritzdüsen zu überprüfen und einzustellen.
Jeder Injektor muss dem entsprechenden Abschnitt der Kraftstoffpumpe zugeordnet und anschließend in den mit diesem Abschnitt verbundenen Motorzylinder eingebaut werden.
Für das Bankset der Hochdruck-Kraftstoffleitungen sollten Rohre mit einer Länge von (415 ± 3) mm verwendet werden, der Unterschied im Durchsatz der Kraftstoffleitungen, aus denen das Bankset besteht, sollte 1 mm nicht überschreiten 3/Zyklus.
Bestimmen Sie den Durchsatz der Kraftstoffleitung an einem Hochdruckabschnitt, mit einer Düse und an einem Tischentschäumer.
Überprüfen Sie die eingestellte Kraftstoffpumpe auf Undichtigkeiten:
1. Ablasshohlraum, bei dem ein Rohr mit einem Innenvolumen von nicht mehr als 50 cm 3 (Innendurchmesser nicht mehr als 8 mm) hermetisch mit der Ölablassschraube verbunden ist.
Tauchen Sie das freie Ende des Rohrs maximal 50 mm tief in ein Gefäß mit Kraftstoff ein. Verschließen Sie das Gewindeloch der Abdeckung der Regler-Inspektionsklappe und die Ölzufuhrschraube fest.
Zum Einschraubablauf Liefern Sie Druckluft mit einem Druck von 0,05 bis 0,07 MPa (von 0,5 bis 0,7 kgf/cm 2) in den Hohlraum der Kraftstoffpumpe.
Die Kraftstoffpumpe gilt als tauglich, wenn 20 s lang keine Luftblasen im Behälter mit Kraftstoff beobachtet werden;
2. Kraftstoffpumpenanschlüsse. Dieser Test wird auf einem speziellen Prüfstand durchgeführt, der mit einem Satz Einspritzdüsen mit Hochdruck-Kraftstoffleitungen ausgestattet ist. Das Arbeitsmedium ist das gleiche wie beim Testen von Pumpen.
Stellen Sie die Düsenfedern auf den Einspritzstartdruck von 21,0 bis 21,8 MPa (von 210 bis 218 kgf/cm 2) ein.
Die Außenflächen der Kraftstoffpumpe müssen trocken sein.
Testmodus – nominal, der Steuerhebel des Geschwindigkeitsreglers muss an der Schraube zur Begrenzung der Höchstgeschwindigkeit anliegen.
Der Kraftstoffdruck in der Kraftstoffpumpenleitung sollte zwischen 0,05 und 0,10 MPa (von 0,5 bis 1,0 kgf/cm 2) und die Kraftstofftemperatur zwischen 50 und 60 °C liegen.
Testdauer 45 Min.
Kraftstofflecks durch die Dichtungen und Anschlüsse der Kraftstoffpumpe sind nicht zulässig.
3. Dichtheit der Kraftstoffleitungen. Verschließen Sie dazu das Loch in der Schraube des Bypassventils und die Anschlüsse der Kraftstoffpumpe.
Schließen Sie die Kraftstoffleitung der Werkbank an die Kraftstoffversorgungsschraube an, entfernen Sie die Abdeckung der Kraftstoffpumpe und erhöhen Sie den Kraftstoffdruck in der Leitung sanft auf 2 MPa (20 kgf/cm 2).
Für 15 Sekunden ist das Austreten von Kraftstoff unter den Schrauben, Karosseriestopfen, Kolbenbuchsen, Anschlüssen und durch die Wände nicht zulässig.
Bei der Überprüfung der Kraftstoffpumpe wird Folgendes überwacht:
- – geometrischer Beginn der Kraftstoffeinspritzung durch Pumpenabschnitte;
- – die Menge und Ungleichmäßigkeit der Kraftstoffzufuhr über die Pumpenabschnitte.
Der geometrische Beginn des Kraftstoffpumpens durch Pumpenabschnitte wird durch den Moment bestimmt, in dem der Kraftstoffausfluss aus den Anschlüssen der Kraftstoffpumpe stoppt. Überprüfen und justieren Sie ihn an der Position der Schiene, die dem Nennvorrat entspricht, wobei die Schiene um ( 19 ± 1) mm vom Pumpenende entfernt.
Der Beginn des Kraftstoffpumpens durch den ersten Abschnitt der Pumpe muss dem Hub des Drückers (4,5 ± 0,05) mm von der untersten Position entsprechen, bis das Ende des Kolbens das Einlassfenster der Hülse überlappt.
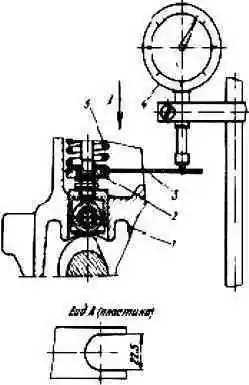
Messen Sie den Hub des Schiebers mit einem Indikator (Abb. 2).
In dem Moment, in dem der erste Abschnitt mit dem Pumpen von Kraftstoff beginnt, müssen die Markierungen auf der Anzeige für den Beginn der Kraftstoffeinspritzung und auf der Kupplung für die Kraftstoffeinspritzung übereinstimmen. Die Abweichung der Markierungen sollte 0,5° nicht überschreiten.
Pumpenabschnitte sollten in der folgenden Reihenfolge mit dem Pumpen beginnen (in Grad – Nockenwellenwinkel):
- Abschnitt Nr. 1 – 0° Abschnitt Nr. 4 – 180°
- Abschnitt Nr. 3 – 45° Abschnitt Nr. 5 – 225°
- Abschnitt Nr. 6 – 90° Abschnitt Nr. 7 – 270°
- Abschnitt Nr. 2 – 135° Abschnitt Nr. 8 – 315°
Die Abweichung der Drehwinkel der Nockenwelle, die dem Beginn der Kraftstoffeinspritzung durch die Pumpenabschnitte entsprechen, relativ zum geometrischen Beginn der Kraftstoffeinspritzung durch den ersten Abschnitt der Pumpe sollte ± 30 Minuten betragen, nicht mehr.
Der Beginn der Kraftstoffeinspritzung wird durch den Druckbolzen eingestellt.
Beim Herausdrehen der Schraube beginnt der Kraftstoff früher zu fließen, beim Einschrauben später. Kontern Sie nach der Einstellung die Einstellschraube mit einer Mutter.
Überprüfen und justieren Sie die Menge und Gleichmäßigkeit der Kraftstoffzufuhr; in der folgenden Reihenfolge:
- 1. Überprüfen Sie den Druck zu Beginn des Öffnens der Auslassventile. Er sollte 1 ± 0,15 MPa (10 ± 1,5 kgf/cm 2) betragen.
Der Druck zu Beginn des Öffnens der Auslassventile sollte überwacht werden, sobald der Kraftstoff beginnt, sich aus Kraftstoffleitungen mit einem Innendurchmesser von (2 ± 0,05) mm oder Armaturen zu bewegen, wobei der Kraftstoffdruck allmählich ansteigt Einlass zur Kraftstoffpumpe, die Rackposition, die der ausgeschalteten Kraftstoffzufuhr entspricht, und das verschlossene Loch der Bypassventilschraube.
- 2. Überprüfen Sie den Kraftstoffdruck in der Leitung am Einlass zur Kraftstoffpumpe. Der Druck sollte 0,075 ± 0,025 MPa (0,75 ± 0,25 kgf/cm 2) betragen, wenn der Steuerhebel an der Höchstgeschwindigkeitsbegrenzungsschraube anliegt und die Nenndrehzahl der Nockenwelle 1030 ± 10 min beträgt -1 für Kraftstoffpumpe 806.6-50 und 980±10 min -1 für Kraftstoffpumpe 807.6-50. Schrauben Sie bei Bedarf den Stopfen des Bypassventils ab und stellen Sie den Öffnungsdruck mit Unterlegscheiben ein.
- 3. Überprüfen Sie die Dichtheit der Auslassventile. In der Stellung der Schiene, die der abgeschalteten Zufuhr entspricht, dürfen die Ablassventile für 2 Minuten keinen Durchfluss durchlassen Kraftstoff unter Druck 0,11 ± 0,1 MPa (1,1 ± 1 kgf/cm 2).
Wenn es ein Leck gibt, tauschen Sie den Auslassventilsatz aus.
- 4. Überprüfen Sie die Verfügbarkeit der Bahnfahrt, um die Einspeisung abzuschalten. Die Zahnstangenhubreserve (Spielwert des Zahnstangenspiels – Spiel) muss mindestens 1 mm betragen, wenn der Steuerhebel des Reglers an der Mindestgeschwindigkeitsbegrenzungsschraube anliegt und bei einer Nockenwellendrehzahl von 450 bis 500 min -1.
Einstellbar mit einer Backstage-Schraube.
Das Herausragen der Jochschraube über das äußere Ende der Reglerabdeckung hinaus ist nicht zulässig.
5. Überprüfen Sie den Beginn des Abschaltens der Startkraftstoffzufuhr bei 230–250 min -1, wenn der Steuerhebel zu Beginn der Zahnstangenbewegung auf der Mindestgeschwindigkeitsbegrenzungsschraube ruht.
Wenn Sie die Geschwindigkeit erhöhen müssen, entfernen Sie den Federhaken vom Zahnstangenhebel und schrauben Sie ihn in die Feder. Um die Geschwindigkeit zu reduzieren, dreht man den Haken aus.
Danach setzen Sie den Haken auf den Schienenhebel.
6. Prüfen Sie den Wert der durchschnittlichen Startkraftstoffzufuhr, die bei einer Nockenwellendrehzahl von 80 ± 10 min -1 / mindestens 230 mm 3/Zyklus betragen muss.
Die Regulierung erfolgt über die Backstage-Schraube nur in Richtung einer Erhöhung der Kraftstoffzufuhr.
7. Überprüfen Sie die Rotationsfrequenz der Nockenwelle der Pumpe, die dem Beginn des Betriebs des Drehzahlreglers entspricht, und fixieren Sie sie am Drehzahlmesser in dem Moment, in dem sich die Schiene in Richtung des Abschaltens der Versorgung zu bewegen beginnt, bestimmt mit einem Anzeigegerät .
Der Beginn der Reglerwirkung sollte bei einer Nockenwellendrehzahl von 1065 bis 1085 min -1 für die Kraftstoffpumpe 806.6-50 und von 1025 bis 1045 min -1 erfolgen für die Kraftstoffpumpe 807.6-50.
Die Einstellung sollte mit der Höchstgeschwindigkeitsbegrenzungsschraube erfolgen.
8. Überprüfen Sie die Drehzahl, die der vollständigen Unterbrechung der Kraftstoffzufuhr entspricht, und fixieren Sie sie am Drehzahlmesser am Ende des Kraftstoffausflusses durch die Einspritzdüsen.
Die vollständige Abschaltung des Vorschubs sollte bei einer Drehzahl erfolgen, die 50–100 min -1 über der Drehzahl der Nockenwelle liegt, bei der der Regler zu arbeiten beginnt.
Passen Sie bei Bedarf an, indem Sie die Position der Schraube des zweiarmigen Hebels ändern.
Beim Einschrauben der Schraube des Zweiarmhebels verringert sich die Drehfrequenz der Nockenwelle, entsprechend der vollständigen Abschaltung der Kraftstoffzufuhr, beim Herausschrauben erhöht sie sich.
Gleichzeitig ändert sich auch der Abschaltbeginn, so dass eine nachträgliche Überprüfung und Anpassung erforderlich ist.
Am Ende der Einstellung die Schraube des Zweiarmhebels und die Schraube zur Begrenzung des Maximalmodus mit Muttern sicher kontern.
9. Überprüfen Sie die durchschnittliche zyklische Kraftstoffzufuhr, die Erhöhung der durchschnittlichen zyklischen Kraftstoffzufuhr und die Ungleichmäßigkeit der Kraftstoffzufuhr und stellen Sie diese bei Bedarf mit dem Werkbanksatz von Einspritzdüsen Modell 261-03C ein, wobei der Steuerhebel des Reglers an der Schraube für die Höchstgeschwindigkeitsbegrenzung anliegt nach Abschnitten, die lauten sollten:
q – durchschnittliche zyklische Kraftstoffzufuhr durch die Pumpe im Nennmodus.
Der Wert des durchschnittlichen zyklischen Vorschubs wird als Summe des Vorschubs aller Abschnitte dividiert durch die Anzahl der Abschnitte berechnet.
Die ungleichmäßige Kraftstoffversorgung nach Abschnitten wird nach folgender Formel berechnet:
- - qcmax – maximale zyklische Kraftstoffzufuhr nach Abschnitten, mm 3/Zyklus;
- - qcmin – minimale zyklische Kraftstoffzufuhr nach Abschnitten, mm 3/Zyklus.
10. Überprüfen Sie die Funktion des Boost-Korrektors. Dazu benötigen Sie:
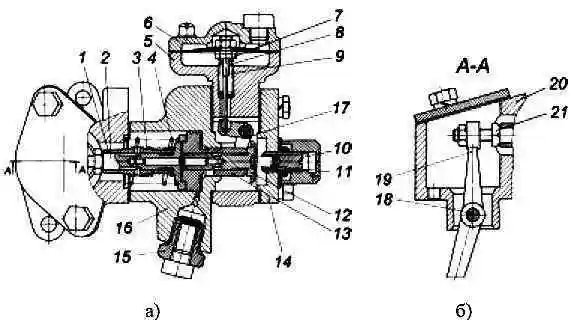
- - Waschen Sie den Netzfilter des Anschlusses 15 (Abb. 3) in sauberem Benzin und blasen Sie ihn gründlich mit Druckluft aus;
- - Reinigen Sie das Kalibrierungsloch im Korrektorkörper mit einem weichen Draht mit einem Durchmesser von 0,5 bis 0,7 mm;
- – Überprüfen Sie die Dichtheit des Korrektormembranhohlraums.
Um dies zu tun, zum Loch Luft unter einem Druck von 0,06 ± 0,01 MPa (0,6 ± 0,1 kgf/cm 2) in der Abdeckung des Membrangehäuses.
Wenn der Zuluftkanal vollständig blockiert ist, sollte der Druckabfall im Membranhohlraum innerhalb von 2 Minuten 0,01 MPa (0,1 kgf/cm 2) nicht überschreiten.
– Stellen Sie die Drehzahl auf 650 ± 10 min -1 ein und bringen Sie das Öl unter einen Druck von 0,275 ± 0,025 MPa (2,75 ± 0,025 kgf/cm). 2
Um den Boost-Korrektor in Betrieb zu nehmen, schalten Sie die Kraftstoffzufuhr einmal mit dem Kipphebel ab und bewegen Sie dann den Kipphebel in die Einspeisungsposition;
– Überprüfen Sie den Wert der zyklischen Zufuhren bei unterschiedlichen Luftdrücken im Membranhohlraum, der sein sollte:
Es ist notwendig, den Korrektor neu einzustellen, wenn die gemessenen Werte der zyklischen Einspeisungen von den angegebenen abweichen.
Die Einstellung des Wertes der zyklischen Kraftstoffzufuhr bei einem Luftdruck gleich Null erfolgt am eingebauten Ladedruckregler über die Einstellschraube 21 (Abb. 3).
Beim Eindrehen einer Schraube erhöht sich die Vorschubgeschwindigkeit, beim Herausschrauben verringert sie sich. Kontern Sie die Schraube nach der Einstellung mit einer Mutter.
Der Zyklus bei mittleren Luftdrücken wird durch das Korrekturfedergehäuse gesteuert.
Wenn das Federgehäuse eingeschraubt ist, verringert sich die Kraftstoffzufuhrmenge, wenn es herausgedreht wird, erhöht es sich. Kontern Sie das Federgehäuse nach der Einstellung mit einer Mutter.
Bevor Sie eine verschlissene Membran ersetzen (falls erforderlich), messen Sie den Überstand des Schafts vom unteren Ende der Mutter an der Membran mit der Schaftbaugruppe.
Danach ersetzen Sie die Membran und montieren sie mit einer Stange mit dem gleichen Überstand der Stange mit einer Genauigkeit von 0,1 mm, während das Ende der Spule 12 (Abb. 3) relativ zum Ende der Spule sinkt Kolben 13 sollte 0,2–0,9 mm betragen, sofern zwischen der Endfläche des Kolbens und dem Körper des Korrektors kein Spalt vorhanden ist.
Wenn Sie den Boost-Korrektor nach der Demontage (falls erforderlich) am Regler installieren, bewegen Sie die Pumpenschiene mit der Backstage-Halterung in die äußerste Aus-Position, installieren Sie den Boost-Korrektor im Korrektorgehäuse und lassen Sie dann die Halterung los.
Überprüfen Sie die Einstellung des Boost-Korrektors auf das Vorliegen einer Unterbrechung der Kraftstoffzufuhr durch den Regler.
11. Begrenzen Sie mit der Leistungseinstellschraube, wenn der Steuerhebel an der Schraube zur Begrenzung der Höchstgeschwindigkeit anliegt, die nominalen zyklischen Vorschübe auf die Werte, die sein sollten:
Verriegeln und versiegeln Sie die Leistungseinstellschraube sicher.
Überprüfen Sie die Bewegungsreserve der Zahnstange, wenn der Reglersteuerhebel an der Mindestgeschwindigkeitsbegrenzungsschraube anliegt und eine Nockenwellendrehzahl von 650 min-1 vorliegt.
Die Hubreserve der Schiene muss mindestens 0,5 mm betragen.
Stellen Sie sicher, dass der zyklische Vorschub durch die Kipphebelhalterung ausgeschaltet wird, wenn Sie sich um 40–45° aus der Ausgangsposition drehen.
Die Kraftstoffzufuhr von den Einspritzdüsen aller Abschnitte der Kraftstoffpumpe muss bei jeder Drehzahl der Nockenwelle vollständig unterbrochen sein.
Setzen Sie die Kappen auf die Kraftstoffpumpe und den Regler und verschließen Sie sie. Bringen Sie eine Dichtung an der Einstellschraube für die Höchstgeschwindigkeit an.