Die Lenkung besteht aus einem Lenkrad 1, einer Säule 2, deren Welle über ein Kardangetriebe 3 mit dem Lenkmechanismus 7 verbunden ist, und einem Lenkgetriebe.
Das Lenkgetriebe ist ein System aus Stangen und Hebeln, das zusammen mit dem Lenkmechanismus das Auto dreht.
Durch den Lenkmechanismus bewegt sich die Längsstange 8 vorwärts oder rückwärts, wodurch ein Rad nach links oder rechts gedreht wird und das Lenkgestänge das Drehmoment auf das andere Rad überträgt.
Das Trapez umfasst den Balken 5 (Abb. 2.) der Vorderachse, die Hebel 3 und 6 der Achsschenkel und die Spurstange 4.
Wenn sich ein Rad über die Hebel 3 und 6 und die Stange 4 dreht, dreht sich auch das andere Rad.
In diesem Fall dreht sich aufgrund einer Änderung der Position des Querlenkers 4 relativ zur Vorderachse das Innenrad in Richtung Drehzentrum um einen Winkel, der größer ist als der Drehwinkel des Außenrads.
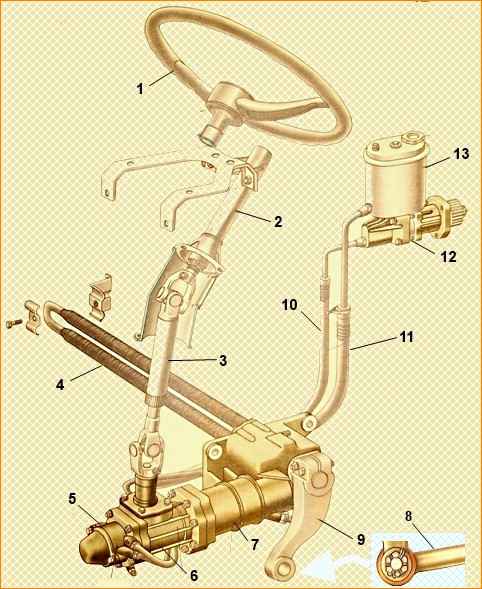
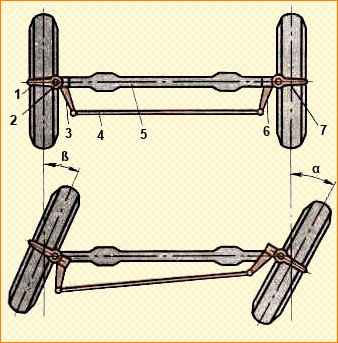
Der Lenkmechanismus von KamAZ-Fahrzeugen umfasst ein Winkelgetriebe, ein Schrauben-Mutter-Getriebe mit umlaufenden Kugeln und ein Zahnstangen-Zahnrad-Paar.
Das Lenkgetriebegehäuse ist gleichzeitig das Servolenkungsgehäuse, in das das Lenkgetriebe integriert ist.
Das Übersetzungsverhältnis des Winkelgetriebes beträgt 1:1, das Lenkgetriebe von Fahrzeugen mit der Achsfolge 6X4-20: 1, von Geländefahrzeugen 21,7:1.
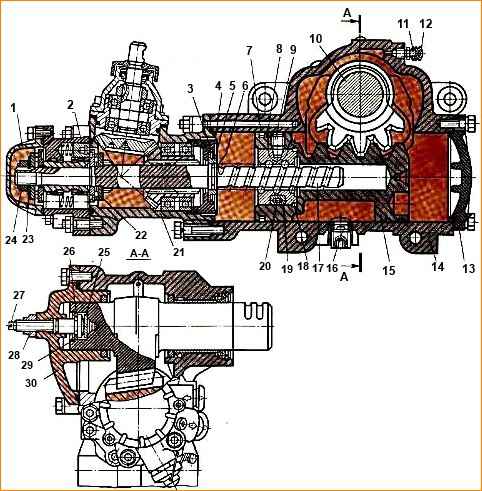
Der Lenkmechanismus besteht aus einem Gehäuse 14 (Abb. 3.), in dem sich eine Kolbenstange 15 bewegt, die in den Zahnsektor der Zweibeinwelle 10 eingreift.
Die Kugelmutter 18 wird mit Stellschrauben 9 in der Kolbenstange befestigt.
Die Schrauben werden durch Öffnen in der Nut der Kolbenstange verriegelt.
Kugelmutter 18 und Schraube 17 haben spiralförmige Nuten.
Auf der Außenfläche der Kugelmutter befindet sich eine schräge Nut, die durch zwei Löcher mit der spiralförmigen Nut verbunden ist.
In diese Nut sind zwei Nuten 19 eingearbeitet, die zusammen ein Rohr bilden, das wie eine Fortsetzung der spiralförmigen Nut ist.
Der Schraubenkanal, der durch die Nuten der Schraube und der Mutter sowie die Nuten gebildet wird, enthält 20 Kugeln.
Wenn sich die Schraube dreht, rollen die Kugeln von einer Seite der Mutter heraus, passieren die Rillen wie durch einen Bypass-Kanal und kehren zum Schraubenkanal zurück, jedoch auf der anderen Seite der Mutter.
Im geschlossenen Kanal zirkulieren insgesamt 31 Kugeln, davon 8 im Bypass-Kanal.
Die Dicke der Zähne des Zweibeinwellensektors und der Kolbenstange ist über die Länge variabel, sodass Sie den Eingriffsspalt durch axiale Bewegung der in die Seitenabdeckung 30 eingeschraubten Einstellschraube 27 ändern können.
Die freie axiale Bewegung der Zweibeinwelle nach dem Zusammenbau des Lenkmechanismus sollte 0,02–0,08 mm betragen, was durch eine Änderung der Dicke der Einstellscheibe 26 gewährleistet wird.
Auf dem im Hohlraum des Winkelgetriebegehäuses 21 befindlichen Teil der Lenkgetriebeschraube befinden sich Keilverzahnungen, mit denen die Schraube mit dem Winkelgetriebegetriebe verbunden ist.
Ausbau und Reparatur des Lenkmechanismus
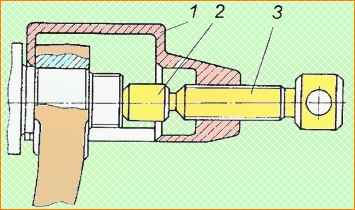
So entfernen Sie das Lenkgetriebe:
- - Bewegen Sie die Kabine in die erste Position (42°);
- - Nachdem Sie die Muttern gelöst und gelöst haben, entfernen Sie die Zweibein-Kupplungsschrauben 9 (siehe Abb. 1) oder schrauben Sie die Mutter des oberen Kopfes des Zweibeins ab, indem Sie die Antennen der Sicherungsscheibe biegen;
- - Entfernen Sie das Zweibein mit einem Abzieher, schrauben Sie die Schraube 3 (Abb. 4) in den Griff 1 des Abziehers und legen Sie die Spitze 2 gegen das Ende des Zweibeinschafts (das Herausschlagen des Zweibeins kann zum Bruch von Teilen führen);
- - Schrauben Sie den Magnetstopfen ab und lassen Sie das Öl aus dem Lenkgetriebegehäuse ab; für eine vollständigere Entwässerung drehen Sie das Lenkrad zwei- oder dreimal von einer Extremposition in die andere;
- - Trennen Sie die Hoch- und Niederdruckleitungen vom Lenkmechanismus und lassen Sie das restliche Öl in der Pumpe ab;
- - Lenkantriebswelle vom Lenkmechanismus trennen, dazu den Splint entfernen, die Keilmutter abschrauben und den Keil herausschlagen;
- - Lösen Sie die Schrauben, mit denen das Lenkgetriebegehäuse an der vorderen Federhalterung befestigt ist, und entfernen Sie das Lenkgetriebe;
- - Reinigen und spülen Sie die Außenfläche des Lenkmechanismus;
- - Lassen Sie das restliche Öl ab, indem Sie den Lenkmechanismus mit dem Ventil nach unten drehen und die Welle des Kegelradantriebs zwei- oder dreimal von einer Extremposition in die andere drehen.
- Beim Einbau des Lenkgetriebes in ein Fahrzeug:
- - Installieren Sie den Mechanismus an der vorderen Halterung der linken Vorderfeder und befestigen Sie ihn mit Schrauben mit einem Anzugsdrehmoment von 275–314 Nm (28–32 kgf);
- - Schließen Sie die Ablass- und Ablassleitungen an das Steuerventil der Servolenkung an;
- - Befestigen Sie die Lenkkardanwelle am Lenkmechanismus, nachdem Sie zuvor das Loch in der Kardangabel und den Keil flach auf der Antriebswelle ausgerichtet haben, schlagen Sie den Keil ein, ziehen Sie die Mutter fest und stecken Sie sie mit dem Anzugsdrehmoment des Keils fest Mutter von 13,7-16,7 Nm(1,4-1,7 kgcm);
- - Öl einfüllen und Servolenkung entlüften (siehe Abschnitt „Öl wechseln“);
- - Nachdem Sie zuvor den Schlitz des oberen Kopfes des Zweibeins mit einem Keil geöffnet haben, setzen Sie das Lenkzweibein auf die Lenkgetriebewelle, setzen Sie die Kupplungsbolzen ein, schrauben Sie die Muttern auf die Bolzen, ziehen Sie sie fest und stecken Sie sie mit einem Anzug fest Drehmoment von 177–196 Nm (18–20 kgcm). Die Schraubenmuttern sollten sich auf gegenüberliegenden Seiten des Zweibeinkopfes befinden;
- - Überprüfen Sie die Dichtheit der Anschlüsse und Schläuche des Lenkhydrauliksystems. Lassen Sie kein Öl aus den Anschlüssen austreten.
Zerlegen und überprüfen Sie den Lenkmechanismus in der folgenden Reihenfolge:
- Entfernen Sie nach dem Lösen der Befestigungsschrauben die Seitenabdeckung zusammen mit dem Zweibeinschaft. Reinigen Sie beim Entfernen des Zweibeinschafts zunächst dessen verzahntes Ende.
- Überprüfen Sie die axiale Bewegung der Einstellschraube im Zweibeinschaft. Wenn die Bewegung mehr als 0,15 mm beträgt, stellen Sie das Axialspiel durch Auswahl einer Unterlegscheibe ein. Die Einstellschraube muss eine axiale Bewegung relativ zum Zweibeinschaft von 0,02–0,08 mm haben und sich leichtgängig drehen lassen, ohne zu verklemmen. Der Sicherungsring muss vollständig in die Nut des Zweibeinschafts passen. Dies ist für eine zuverlässige Verbindung der Teile dieser Baugruppe erforderlich. Ersetzen Sie bei Bedarf den O-Ring der Einstellschraube mit einem Dorn. Nach dem Zusammenbau der Seitenabdeckung sollte sich die Zweibeinwelle frei von Hand drehen lassen und die Einstellschraube sollte bewegungslos bleiben (ohne Sicherungsmutter prüfen).
- Entfernen Sie nach dem Lösen der Befestigungsschrauben die vordere Abdeckung. Bedenken Sie bei allen weiteren Demontage- und Montagearbeiten, dass das Herausdrehen der Lenkgetriebeschraube aus der Kugelmutter um mehr als zwei Umdrehungen aus der Mittelstellung zu Schäden führen kann
- Schrauben Sie die Muttern ab, mit denen das Steuerventilgehäuse der Servolenkung befestigt ist, und schieben Sie das Gehäuse vorsichtig so weit nach vorne, dass es relativ zur Schraube gedreht werden kann, ohne die Stehbolzen des Kegelradgehäuses zu berühren.
- Überprüfen Sie, ob die Drucklagermutter fest sitzt und dass sich das Steuerventilgehäuse relativ zur Schraube reibungslos dreht.
Das zum Drehen des Steuerventilkörpers erforderliche Drehmoment muss 98,1–122,6 N cm (10–12,5 kgf·cm) betragen (während des Betriebs darf das Drehmoment auf 34,3 N·cm (3,5 kgf·cm) sinken. Wenn das Drehmoment nicht dem angegebenen Wert entspricht, passen Sie den Anzug der Drucklagermutter an. Wenn die Drehung des Ventilkörpers nicht gleichmäßig ist (der Drehwiderstand ist unterschiedlich), tauschen Sie die Lager aus. Um den Anzug anzupassen oder die Lager auszutauschen , ist es notwendig, den in die Schraubennut gedrückten Mutternbund zu drücken und die Mutter abzuschrauben, um das Antriebszahnrad des Winkelgetriebes am Drehen zu hindern.
Achtung: Achten Sie beim Abschrauben der Drucklagermutter darauf, dass sich die Antriebswelle des Winkelgetriebes nicht dreht. Die Nichtbeachtung dieser Regel führt zum Bruch der Ranke der Federscheibe 23 (siehe Abb. 3) und zur Beschädigung des Gewindes der Schraube 17. Achten Sie beim Ausbau des Steuerventilkörpers darauf, dass die Spule und die Reaktionskolben nicht herausfallen , da bei der Werksmontage jeder von ihnen individuell auf sein Loch abgestimmt wird. Axiallagerringe nicht vermischen, sondern komplett halten.
- Überprüfen Sie die Glätte mit der Hand Bewegungen der Reaktionskolben und der Spule im Gehäuse des Servolenkungssteuerventils. Wenn Sie ein Klemmen oder eine Änderung der Kraft bemerken, die zum Bewegen der genannten Teile erforderlich ist, entfernen Sie die blockierten Teile nacheinander. Beseitigen Sie die Ursache der Blockierung, waschen Sie sie und ersetzen Sie sie.
- Überprüfen Sie die Dichtheit des Rückschlagventils, indem Sie Öl in das Loch gießen. Ölaustritt ist nur in Form einzelner Tropfen zulässig.
- Nachdem Sie die Befestigungsschrauben und zwei Muttern gelöst haben, entfernen Sie das Kegelrad zusammen mit der Schraube und der Kolbenstange.
- Entfernen Sie mit einer Zange den Sicherungsring 3 (siehe Abb. 3) und entfernen Sie vorsichtig das Kegelrad von der Schraube.
- Überprüfen Sie die axiale Bewegung der Kugelmutter relativ zur Kolbenstange. Ziehen Sie bei Bedarf die beiden Gewindestifte fest bzw. ersetzen Sie sie und schrauben Sie sie heraus. 11. Überprüfen Sie den Sitz der Kugelmutter im mittleren Teil der Spiralnut der Schraube. Die Mutter sollte sich ohne zu verkanten auf der Schraube drehen und ihr axiales Spiel gegenüber der Schraube sollte 0,3 mm nicht überschreiten. Wenn die Drehung der Schraube in der Kugelmutter nicht reibungslos verläuft und das Axialspiel 0,3 mm nicht überschreitet, tauschen Sie den Kugelsatz aus.
Um einen Satz Kugeln auszutauschen, gehen Sie zunächst wie folgt vor:
- - Verwenden Sie einen Spezialschlüssel mit ausreichend großer Schulter, um die Stellschrauben der Kugelmutter zu lösen;
- - Entfernen Sie die Kugelmutter und die Schraube von der Kolbenstange und achten Sie darauf, dass die Nuten und Kugeln nicht herausfallen;
- - Entfernen Sie die Nuten, überprüfen Sie sie und ersetzen Sie sie, wenn die Federn beschädigt sind;
- - Drehen Sie dann die Schraube relativ zur Mutter in die eine oder andere Richtung, entfernen Sie die Kugeln und legen Sie sie in eine separate Box. Der Einbau von Kugeln mit einem Durchmesserunterschied von mehr als 0,002 mm ist nicht zulässig. Bei Nichtbeachtung dieser Anforderung kann es zur Zerstörung der Kugeln und zum Blockieren des Lenkmechanismus kommen. Nach dem Austausch der Kugeln sollte sich die Mutter unter dem Einfluss eines Drehmoments von 29,4–78,5 Nm (3–8 kgcm) im mittleren Teil des Schraubengewindes drehen, an den Rändern sollte die Mutter frei sitzen. Die Laufbahnen an Schraube und Mutter dürfen nicht beschädigt werden. Wenn die Laufbahnen beschädigt sind (Beulen, Grate usw.), ersetzen Sie die gesamte Schrauben-Kugel-Mutter-Kugel-Baugruppe.
- Inspizieren Sie die Arbeitsflächen des hydraulischen Verstärkers. Sollten sich einzelne Grate am Zylinderspiegel befinden, diese mit einem Schaber entfernen. Einzelne Längsspuren und Kratzer auf dem Zylinderspiegel (ohne Grate) stellen kein Mangelzeichen dar.
- Überprüfen Sie die Einstellung des Seitenspiels zwischen den Zähnen der Kegelräder. Der seitliche Abstand zwischen den Zahnpaaren sollte im Bereich von 0,02–0,07 mm liegen und das Drehmoment des Antriebszahnrads im Kegelrad sollte 49,1 Ncm (5 kgf.cm) nicht überschreiten.
Die Einstellung des seitlichen Spiels in den Zähnen der Getrieberäder erfolgt durch Bewegen der Antriebsradbaugruppe durch Auswahl eines Dichtungspakets unter dem Flansch des Antriebsradgehäuses. In diesem Fall müssen mindestens drei Dichtungen mit einer Dicke von 0,05 mm eingebaut werden.
Wenn die Kegelräder richtig ineinandergreifen, sollte das Kontaktmuster elliptisch sein und sich näher am inneren schmalen Teil des Zahns befinden. Es ist nicht akzeptabel, dass die Kontaktfläche die Zahnränder erreicht. Beschädigen Sie beim Zerlegen des Kegelrads nicht den kompletten Satz aus Kegelradgehäuse und Kegelradpaar.
Bauen Sie den Lenkmechanismus in einer sauberen Umgebung in umgekehrter Reihenfolge der Demontage gemäß den folgenden Anweisungen zusammen:
- Spülen und trocknen Sie alle Teile des zerlegten Mechanismus, blasen Sie die inneren Kanäle und Löcher nach dem Waschen mit trockener Druckluft aus. Wischen Sie Teile nicht mit einem Lappen ab, da sonst Fäden, Fusseln usw. zurückbleiben könnten.
- Vor dem Zusammenbau alle Kontaktflächen der Lenkmechanismusteile mit Turbinenöl Tn-22 GOST 9972-74 oder Ölsorte R schmieren.
- Überprüfen und ersetzen Sie alle Gummidichtungsteile. Die Fluorkunststoffringe der Kolben- und Schraubendichtungen dürfen nicht beschädigt werden. Um die Montage von Gummiringen zu erleichtern und ein Einklemmen bei der Montage zu vermeiden, darf PVK-Schmiermittel GOST 19537-74 verwendet werden.
- Wenn Sie die Manschetten der Zweibeinwelle und der Antriebswelle des Kegelradgetriebes austauschen, drücken Sie diese mithilfe von Dornen sanft und ohne Verzerrungen ein. Abschließend drücken Sie die angegebenen Manschetten im Paket zusammen mit der Außenmanschette und anderen in den genannten Dichtungsbaugruppen enthaltenen Teilen zusammen – bis zum Anschlag im Mechanismuskörper. Bei der Montage der Schaftmanschetten des Zweibeins müssen deren Arbeitskanten durch die Schaftverzahnung vor Beschädigungen geschützt werden.
- Das Anzugsdrehmoment von M8-Schrauben sollte 20,6–27,5 Nm (2,1–2,8 kgcm) betragen, M10-Schrauben und Muttern 34,3–41,2 Nm (3,5–4,2 kgcm). Der Druckdeckel der Abtriebsrad-Baugruppe des Getriebes muss mit einem Drehmoment von 43,2–60,8 Nm (4,4–6,2 kgcm) angezogen und durch Öffnen seiner Kante in der Nut am Kegelradgehäuse verriegelt werden.
Die Mutter, mit der die Lager des Kegelradantriebs befestigt sind, muss mit einem Drehmoment von 39,2-58 angezogen werden 9 Nm (4-6 kgcm) und wird durch Drücken des Mutternbundes in die Nut auf der Antriebsradwelle verriegelt. Nach der Montage sollten sich Abtriebs- und Antriebsrad des Winkelgetriebes frei drehen lassen und kein spürbares Axialspiel aufweisen. Ziehen Sie die magnetische Ablassschraube (mit konischem Gewinde und zylindrischem Magnet) mit einem Drehmoment von 33,4–39,2 Nm (3–4 kgcm) an.
- Bauen Sie das Kugelumlaufspindelpaar zusammen und installieren Sie den zusammengebauten Satz in der folgenden Reihenfolge in der Kolbenstange:
- - Platzieren Sie eine schwimmende Dichtungshülse von der Seite ihrer Schraubennut her auf der Schraube;
- - Bringen Sie die Mutter am unteren Ende der Schraube an und richten Sie dabei die Löcher der Mutter, in die die Nuten passen, mit der Schraubennut der Schraube aus;
- - Platzieren Sie dreiundzwanzig Kugeln durch das Loch in der Mutter gegenüber dem Kegelrad und drehen Sie die Schraube gegen den Uhrzeigersinn;
- - Legen Sie acht Kugeln in die zusammengefalteten Rillen und verhindern Sie, dass sie herausfallen, indem Sie die Auslässe der Rinne mit PVK-Fett GOST 19537-74 abdecken;
- - Setzen Sie die Nuten mit den Kugeln in die Mutter ein, drehen Sie ggf. die Schraube und befestigen Sie die Mutter, um ein Herausfallen der Nuten zu verhindern;
- - Überprüfen Sie das Drehmoment der Mutter am mittleren Teil der Schraube (sollte 29,4–78,5 Ncm (3–8 kgf.cm) betragen; wenn das Drehmoment nicht dem angegebenen Wert entspricht, ersetzen Sie die Satz Bälle, um ein Vermischen der Sätze zu vermeiden;
- - Drücken Sie die Mutter mit der Schraube in das Loch der Kolbenstange, schrauben Sie die Stellschrauben ein und öffnen Sie sie an zwei Stellen gegen die Nuten in der Kolbenstange. Das Anzugsdrehmoment der Stellschrauben sollte 49,1–58,9 Nm (5–6 kgcm) betragen. Wenn die Nut in der Kolbenstange mit dem Schraubenschlitz übereinstimmt, ersetzen Sie diesen. Ein Überstand der Schrauben über die zylindrische Oberfläche der Kolbenstange ist nicht akzeptabel. Dies führt zu Abrieb an der Arbeitsfläche des Servolenkungszylinders.
- Beim Zusammenbau eines Winkelgetriebes mit Schraube und schwimmender Dichthülse ist darauf zu achten, dass deren Sicherungsring sicher in der Nut des Druckdeckels des Winkelgetriebes sitzt. Der Sicherungsring muss vollständig in die besagte Nut passen.
- Montieren Sie die Kolbenstange mit einem Dorn ohne Verformung in das Kurbelgehäuse.
- Stellen Sie beim Zusammenbau des Servolenkungssteuerventils sicher, dass die Nut am Ende der Spule zum Kegelrad zeigt und die Fasen an den Reaktionskolben nach außen zeigen. Nach dem Zusammenbau sollten sich Spule, Rückschlagventil und Reaktionskolben reibungslos in den entsprechenden Löchern des Steuerventilgehäuses bewegen, ohne zu blockieren.
- Wenn Sie das Servolenkungssteuerventil mit einer Schraube zusammenbauen, installieren Sie die Drucklager so, dass ihre großen Ringe zur Spule zeigen. Die Federscheibe von Axiallagern muss mit der konkaven Oberfläche zum Lager hin eingebaut werden. Nachdem Sie das zum Drehen des Steuerventilkörpers erforderliche Drehmoment (98,1–122,6 Ncm (10–12,5 kgf.cm)) eingestellt haben, sichern Sie die Befestigungsmutter des Drucklagers, indem Sie den Mutternbund in die Nut der Lenkgetriebeschraube drücken.
- Stellen Sie beim Zusammenbau der Einstellschraube und des Zweibeinschafts sicher, dass die axiale Bewegung der Schraube relativ zum Zweibeinschaft 0,02–0,08 mm beträgt, indem Sie eine Einstellscheibe auswählen. Ersetzen Sie bei Bedarf den O-Ring der Einstellschraube mit einem Dorn.
- Stellen Sie die Verzahnung im Paar „Kolben – Zahnstange – Zahnradsektor der Zweibeinwelle“ gemäß den oben genannten Anweisungen ein. Ziehen Sie nach dem Einstellen des Eingriffs die Einstellschraube des Zweibeins fest, indem Sie die Sicherungsmutter mit einem Drehmoment von 58,9–63,8 Nm (6–6,5 kgcm) anziehen und dabei die Einstellschraube am Drehen hindern.
Nach der Montage muss der Lenkmechanismus folgende Anforderungen erfüllen:
- Der volle Drehwinkel der Zweibeinwelle muss mindestens 90° betragen.
- Nach dem Drehen der Lenkgetriebeschraube bis zum Anschlag des Kolbens und dem Aufbringen eines zusätzlichen Drehmoments von mindestens 19,6 Nm (2 kgcm) auf das Antriebsrad sollten die Zentrierfedern für dessen klare Rückkehr in die Ausgangsposition sorgen. Diese Bedingung muss sowohl beim Rechts- als auch beim Linksabbiegen beachtet werden.
- Das beim Drehen des Antriebsrads ausgeübte Drehmoment (bzw. die auf den Lenkradkranz über einen Radius von 250 mm ausgeübte Kraft) muss betragen:
- - nachdem das Antriebsrad mehr als zwei Umdrehungen in eine beliebige Richtung aus der Mittelstellung gedreht wurde – 147–294 N.cm (15–30 kgf.cm) [die Kraft auf den Lenkradkranz beträgt 5,9–11,8 N (0,6-1,2 kgf)];
- - beim Drehen des Antriebszahnrads mit einem Übergang durch die mittlere Position mit einem garantierten Spalt in der Verzahnung des Zahnstangenkolbens und der Zweibeinwelle - 196-441 N.cm (20-45 kgf.cm) [die Kraft am Lenkradkranz beträgt 7,8–17,7 N (0,8–1,8 kgf)];
- - beim Drehen des Antriebszahnrads mit Übergang durch die Mittelstellung nach Einstellung der Verzahnung des Zahnstangenkolbens und der Zweibeinwelle - 98,1-147,2 Nm (10-15 kgf.cm) [um 3,9-5,9 N (0,4-0,6 kgf) mehr als mit einem garantierten Spalt], jedoch nicht mehr als 540 N.cm. (55 kgf.cm) [21,6 N (2,2 kgf)].
- Testen Sie zusätzlich den Lenkmechanismus m auf einem Ständer, der mit einer Pumpe mit einem Durchfluss von mindestens 9 1/min ausgestattet ist und die Ölversorgung der Bohrung im Steuerventilgehäuse der Servolenkung gewährleistet. Führen Sie den Test mit Öl der Klasse P bei einer Temperatur von nicht weniger als plus 40 °C durch. Entfernen Sie vor dem Test die Luft aus dem System.
Stellen Sie das Sicherheitsventil der Tischpumpe auf einen Öffnungsdruck von 5390 kPa (55 kgf/cm 2) ein und prüfen Sie:
- - Die Drehung des Antriebsrads in jede Richtung bei einem Widerstandsmoment gegen die Drehung der Zweibeinwelle von 0 und 1275 Nm (130 kgcm) sollte gleichmäßig und ohne Blockierung erfolgen;
- - Der Druck am Einlass zum Steuerventil des hydraulischen Verstärkers sollte bei neutraler Spule nicht mehr als 294 kPa (3 kgf/cm 2) betragen.
- - Moment am Antriebsrad mit einem Widerstand an der Zweibeinwelle von 1275 Nm (130 kgf.cm) – nicht mehr als 1766 N.cm (180 kgf.cm);
- - Leckage am Ausgang des Servolenkungssteuerventils beim vollständigen Drehen des Antriebsrads nach rechts oder links (Messzeit nicht länger als 20 s, Messung beginnt 5 s nach dem vollständigen Drehen der Schraube) - nein mehr als 1200 cm 3/min;
- - Die Drehung des Zweibeinschafts von einer Extremposition in eine andere sollte durch eine Kraft mit einem Moment von nicht mehr als 118 Nm (12 kgcm) erfolgen. Stellen Sie das Sicherheitsventil der Tischpumpe auf einen Öffnungsdruck von 90 U/min ein und prüfen Sie:
- - Druck in der Druckleitung, wenn das Antriebsrad ganz nach rechts und links gedreht wird; er sollte 7355–7846 kPa (75–80 kgf/cm 2) betragen. Nachdem die Kraft von der Schraube entfernt wurde, ohne die Antriebswelle zu bremsen und anzuhalten, sollte der Druck schnell auf einen Wert von nicht mehr als 294 kPa (3 kgf/cm 2) abfallen;
- - Dichtheit des Lenkmechanismus in beiden Extrempositionen des Kolbens (5 Minuten in jeder Position) bei einem Druck von 8826 kPa (90 kgf/cm 2). Stellen Sie den Druck sicher, indem Sie ein Ventil in der Rücklaufleitung installieren;
- - Korrektheit der Schalteigenschaften. Das freie Spiel auf der Antriebswelle (der Drehwinkel der Welle, bis der Druck in der Druckleitung um 78,5 kPa (0,8 kgf/cm 2) ansteigt) sollte 3–5° in jede Richtung betragen . Die gesamte freie Spielbewegung (Summe der Winkel nach rechts und links) darf nicht mehr als 10° betragen.