Zum Zusammenbau des Motors sowie zum Zerlegen wird der mit dem Kupplungsgehäuse zusammengebaute Motorzylinderblock auf einem Ständer befestigt (siehe Abb. 1)
Vor dem Zusammenbau werden alle Motorteile nach Größe ausgewählt, gründlich gewaschen, mit Druckluft ausgeblasen und mit sauberen Servietten abgewischt
Alle Gewindeverbindungen (Bolzen, Stopfen, Fittings usw.) müssen, wenn sie bei der Demontage entfernt oder ersetzt wurden, mit rotem Blei oder weißem Blei, verdünnt mit natürlichem Trockenöl, installiert werden.
Dauerhafte Verbindungen (Blockstopfen und Zylinderköpfe) werden mit Nitrolack montiert.
Folgendes darf an dem zu reparierenden Motor nicht eingebaut werden:
- - gebrauchte Splinte und Splinte;
- - Federscheiben, die ihre Elastizität verloren haben;
- - Bolzen und Stehbolzen mit verlängertem Gewinde;
- - Schrauben und Muttern mit abgenutzten Kanten;
- - Teile, die mehr als zwei Kerben oder Dellen am Gewinde oder gebrochene Gewinde aufweisen;
- - beschädigte Dichtungen.
Bauen Sie den Motor in umgekehrter Reihenfolge wie beim Zerlegen zusammen.
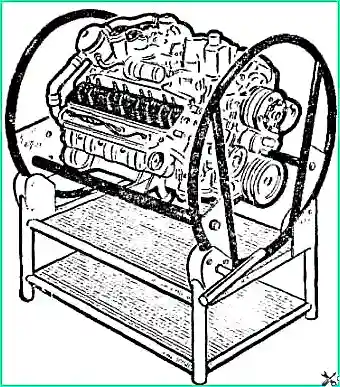
Die Vorbereitung der Teile für die Motormontage finden Sie im Artikel „Vorbereitung der Komponenten und Teile für die Montage des ZMZ-53-Motors“.
Im Folgenden finden Sie spezifische Empfehlungen und zusätzliche Anforderungen für die Motormontage.
Beim Austausch von Zylinderlaufbuchsen wird vor dem Einbau die Laufbuchse entsprechend der Buchse im Zylinderblock ausgewählt.
Ärmel werden mit einem genauen Metalllineal und einem Satz Fühlerlehren wie folgt ausgewählt:
- Die Laufbuchse, die ohne Dichtungen an ihrem Platz im Zylinderblock eingebaut wird, muss relativ zur Passfläche des Zylinderblocks versenkt sein.
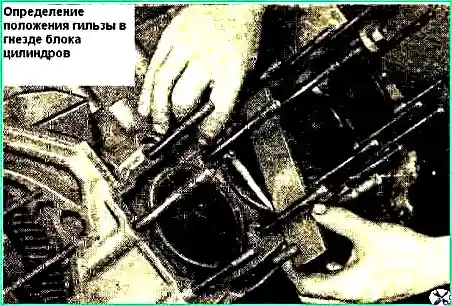
Das Lineal wird auf der Gegenfläche platziert und die Sonde in den Spalt zwischen dem Lineal und dem Ende des Liners eingeführt (Abb. 2).
Die Dicke der Dichtung wird so gewählt, dass nach dem Einbau der Laufbuchse mit der Dichtung eine Höhe über der Oberfläche des Zylinderblocks von 0,02 bis 0,09 mm gewährleistet ist.
Dichtungsdichtungen sind in verschiedenen Stärken erhältlich:
- 0,3; 0,2; 0,15 und 0,1 mm. Je nach Spalt wird die eine oder andere Dichtung auf die Zylinderlaufbuchse aufgelegt; manchmal wird der erforderliche Wert durch einen Satz Dichtungen unterschiedlicher Dicke erreicht.
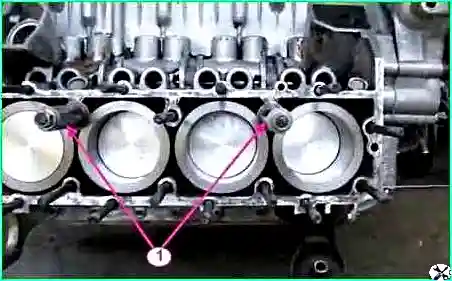
Nach dem Einbau in den Zylinderblock werden die Laufbuchsen mit Spannbuchsen gesichert (siehe Abb. 3).
Mit einer Öl-Graphit-Mischung imprägniertes Asbestkabel wird als hintere Öldichtung an Motoren verwendet.
Ein 140 mm langes Kabel wird in die Buchsen des Zylinderblocks und des Öldichtungshalters gelegt.
Mit dem Gerät wird das Kabel mit leichten Hammerschlägen in seine Buchsen gedrückt, wie in Abb. 4.
Ohne das Gerät zu entfernen, schneiden Sie die Enden des Kabels bündig mit der Ebene des Stopfbuchshalter-Anschlusses ab.
Der Schnitt muss glatt sein, ein Ausfransen der Enden und ungleichmäßige Schnitte sind nicht zulässig.
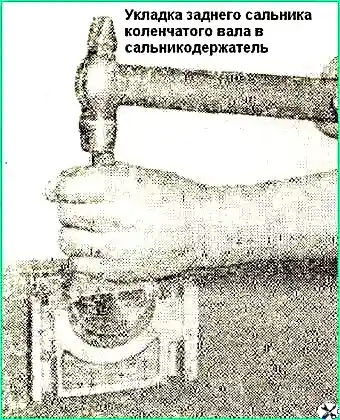
Beachten Sie beim Zusammenbau der Kurbelwelle mit Schwungrad und Kupplung die folgenden Anforderungen.
Die Schwungrad-Befestigungsmuttern werden angezogen und sorgen für ein Drehmoment von 7,6–8,3 kgm.
Beim Zusammenbau der Kupplung wird die Abtriebsscheibe mit einem Dämpfer an der Druckscheibe montiert und auf dem Kurbelwellenlager zentriert (die Antriebswelle des Getriebes kann als Dorn verwendet werden).
Die auf der Druckplatte und dem Schwungradgehäuse in der Nähe eines der Löcher für die Gehäusebefestigungsschrauben eingeprägten „O“-Markierungen müssen ausgerichtet sein.
Die Kurbelwelle, das Schwungrad und die Kupplungsbaugruppe müssen dynamisch ausgewuchtet sein. Zulässige Unwucht 70 g/m².
Entfernen Sie beim Auswuchten überschüssige Masse von der schweren Seite, indem Sie das Schwungradmetall in einem Abstand von 6 mm vom Zahnkranz mit einem Bohrer mit einem Durchmesser von 8 mm bis zu einer Tiefe von maximal 10 mm aufbohren.
Wenn die Unwucht der montierten Welle 180 Gcm überschreitet, wird die Welle zerlegt und jedes Teil einzeln ausgewuchtet.
Die Unwucht des Schwungrads sollte 35 Gcm nicht überschreiten;
Ungleichgewicht der Druckplattenbaugruppe mit dem Gehäuse – 36 Gcm;
Unwucht der angetriebenen Scheibe – 18 Gcm.
Informationen zum Zusammenbau der Kurbelwelle finden Sie im Artikel „Kurbelwelle mit Schwungrad und Kupplung zusammenbauen und in den Zylinderblock einbauen“
Hauptlagerdeckel werden so montiert, dass sich die Verriegelungsnasen der Laufbuchsen auf einer Seite befinden und die auf den Deckeln eingestanzten Zahlen oder Markierungen den Bettnummern entsprechen.
Beim Einbau der vorderen Abdeckung ist darauf zu achten, dass die Befestigungsranke der hinteren Drucklagerscheibe in die Nut der Abdeckung passt und keine Stufen zwischen dem Ende der Abdeckung und dem Ende des Zylinders entstehen blockieren.
Ziehen Sie die Muttern fest, mit denen die Hauptlagerdeckel befestigt sind (Drehmoment 11–12 kgm).
Nach dem Anziehen und Splinten der Muttern des Hauptlagerdeckels sollte sich die Kurbelwelle mit geringem Kraftaufwand leicht drehen lassen.
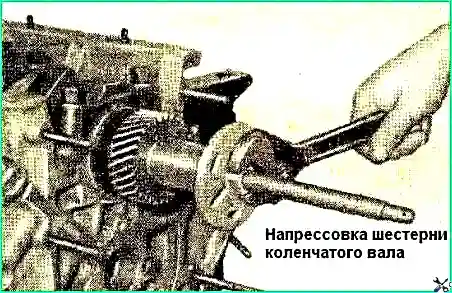
Nach dem Einpressen des Kurbelwellenzahnrads (Abb. 5) mit einem Abzieher und einer Druckbuchse das Axialspiel der Kurbelwelle prüfen, dazu die Kurbelwelle mit einer Fühlerlehre an das hintere Ende des Motors drücken Bestimmen Sie den Abstand zwischen dem Ende der hinteren Drucklagerscheibe und dem Ende der vorderen Hauptkurbelwellenzapfen (Abb. 6).
Der Spalt sollte zwischen 0,075 und 0,175 mm liegen.
Beim Zusammenbau von Teilen der Pleuel- und Kolbengruppe sind folgende Anforderungen zu beachten.
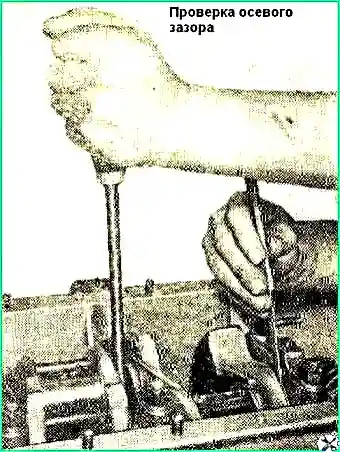
Kolbenbolzen sind für die Pleuel so ausgewählt, dass sich der leicht geschmierte Bolzen bei Raumtemperatur (+18° C) unter leichtem Daumendruck reibungslos in der Pleuelbohrung bewegt.
Vor dem Zusammenbau werden die Kolben in heißem Wasser auf +70°C erhitzt.
Das Eindrücken eines Stifts in einen kalten Kolben ist nicht erlaubt, da dies zu einer Beschädigung der Oberflächen der Kolbennabenlöcher sowie zu einer Verformung des Kolbens selbst führen kann.
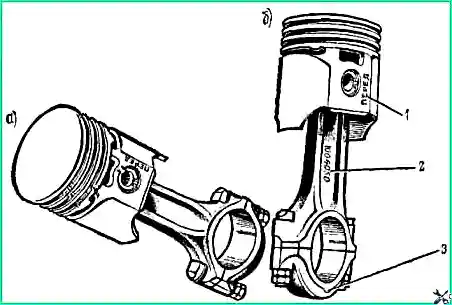
Pleuelstangen und Kolben sind beim Zusammenbau wie folgt ausgerichtet: Bei Kolben des ersten, zweiten, dritten und vierten Zylinders die Aufschrift auf dem Kolben „vorne“ und die auf der Pleuelstange eingestanzte Nummer Die Stangenstange muss in entgegengesetzte Richtungen gerichtet sein, und für die Kolben des fünften, sechsten, siebten und achten Zylinders - in eine Richtung (Abb. 7).
Die Kolbenbolzensicherungsringe werden so in die Nuten der Kolbennaben eingebaut, dass die Biegung der Ranke nach außen zeigt.
Kolbenringe werden entsprechend den Laufbuchsen ausgewählt, in denen sie eingesetzt werden.
Der an der Verbindungsstelle des in der Hülse platzierten Rings gemessene Spalt sollte bei Kompressions- und Ölabstreifringen im Bereich von 0,3 bis 0,5 mm liegen.
In der oberen Kolbennut ist ein verchromter Kompressionsring und in der zweiten Nut ein verzinnter Kompressionsring mit einer Aussparung an der Innenseite nach unten verbaut.
Vor dem Einbau in die Zylinderlaufbuchsen sollten die Stöße der Kolbenringe in einem Winkel von 120° zueinander positioniert werden und es sollten Schutzkappen aus Messing auf die Pleuelbolzen aufgesetzt werden, um eine versehentliche Beschädigung der Oberfläche zu vermeiden Pleuelzapfen.
Achten Sie beim Einbau von Kolben in Zylinderlaufbuchsen darauf, dass die Aufschrift „front“ auf dem Kolben zum vorderen Ende des Zylinderblocks zeigt.
Ziehen Sie die Muttern der Pleuelschrauben fest (Drehmoment 6,8–7,5 kgm) und sichern Sie sie.
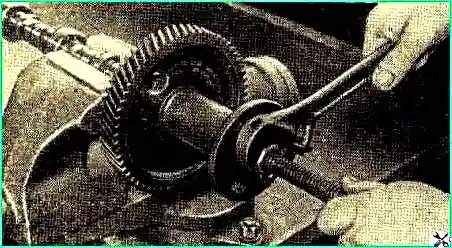
Nachdem Sie das Zahnrad auf die Nockenwelle gedrückt haben (Abb. 8), prüfen Sie mit einer Fühlerlehre das axiale Spiel zwischen dem Druckflansch und dem Ende des Nockenwellenzahnrads. Der Spalt sollte zwischen 0,08 und 0,2 mm liegen.
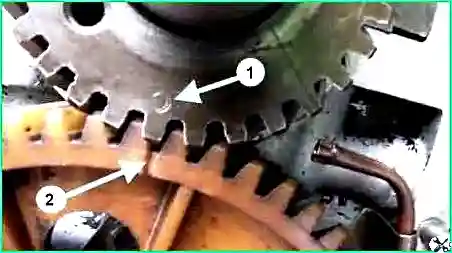
Wenn die Steuerräder eingerückt sind, muss der Zahn des Kurbelwellenrads mit der „O“-Markierung versehen sein in den Hohlraum der Nockenwellenverzahnung eintreten, der mit einer Markierung markiert ist.
Ersetzen Sie die Zahnräder als Satz, da sie im Werk auf der Grundlage des seitlichen Spiels und der Betriebsgeräusche ausgewählt werden.
Das seitliche Spiel im Eingriff sollte im Bereich von 0,03–0,08 mm liegen.
Um bei der Montage und Installation von Zahnrädern keinen Fehler zu machen, müssen Sie berücksichtigen, dass sich die Markierung auf dem Kurbelwellenzahnrad auf dem 12. Zahn befindet, gezählt vom Zahn gegenüber dem Schlitz für den Schlüssel gegen den Uhrzeigersinn (Abbildung 11)
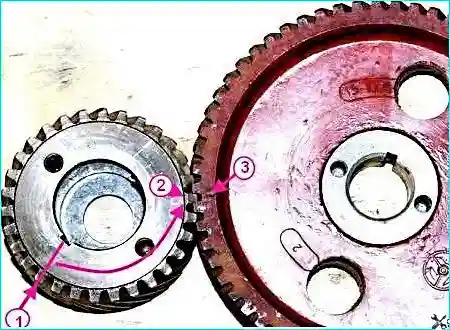
Zentrieren Sie bei der Montage am Zylinderblock die Steuerradabdeckung mit einem konischen Dorn am vorderen Ende der Kurbelwelle, um zu verhindern, dass der vordere Öldichtring der Kurbelwelle auf einer Seite läuft.
Setzen Sie eine konische Referenz auf das vordere Ende der Kurbelwelle und drücken Sie die Steuerradabdeckung mit einer Ratsche gegen den Zylinderblock. Ziehen Sie dann die Befestigungsmuttern der Abdeckung fest.
Die Dichtung des Ölansaugrohrs sollte in die Buchse im Zylinderblock eingesetzt und nicht auf das Rohr aufgesetzt werden.
Vor der Montage am Motor wird die Ölpumpe mit Öl gefüllt.
Beim Zusammenbau der Zylinderköpfe werden die neuen Ventilschäfte mit einer Mischung bestehend aus sieben Teilen eines kolloidalen Graphitpräparats und drei Teilen Luftfahrtöl beschichtet.
Die Kipphebelachsen werden so zusammengebaut, dass die Löcher für die Befestigungsbolzen in der Achse und den Zahnstangen in die entgegengesetzte Richtung zu den Kipphebel-Einstellschrauben verschoben sind.
Die Befestigungsmuttern des Ansaugkrümmers werden mit mäßiger Kraft angezogen, da die Gummidichtungen das Anziehen nicht bis zum Anschlag begrenzen können und beim Anziehen der Muttern die Gummidichtungen zerquetscht werden können.
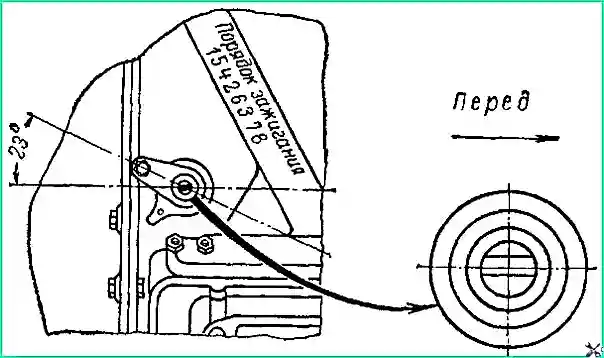
Der Leistungsschalter-Verteiler-Antrieb muss in dieser Reihenfolge installiert werden.
Stellen Sie den Kolben des 1. Zylinders beim Kompressionshub auf den oberen Totpunkt (OT).
Führen Sie den Unterbrecher-Verteilerantrieb so in das Loch im Zylinderblock ein, dass der Schlitz in der Antriebswelle entlang der Motorachse ausgerichtet und nach links verschoben ist, wobei mitgezählt wird, wie sich das Fahrzeug bewegt.
Befestigen Sie das Antriebsgehäuse mit einem Halter und einer Mutter so, dass die Halterung mit einem Gewindeloch zur Befestigung des Leistungsschalter-Verteilers nach hinten gerichtet und in einem Winkel von 23˚ nach links von der Längsachse des Motors gedreht ist, as in Abb. dargestellt. 10.
Bevor Sie den Verteilerschalter am Motor installieren, sollten Sie den Spalt der Unterbrecherkontakte prüfen und gegebenenfalls anpassen.
Der Abstand zwischen den Kontakten sollte zwischen 0,3 und 0,4 mm liegen.
Verwenden Sie die Oktanzahl-Korrekturmuttern, um das Gehäuse des Unterbrecher-Verteilers so zu drehen, dass der Pfeil auf die Nullskalenteilung zeigt.
Drehen Sie den Verteilerrotor so, dass er zum Anschluss des ersten Zylinders zeigt.
Der Anschluss des ersten Zylinders auf der Zündverteilerkappe ist mit der Zahl „1“ gekennzeichnet.
Platzieren Sie die Verteilerkappe mit den Kabeln und verbinden Sie diese in der Reihenfolge der Betätigung der Motorzylinder (1-5-4-2-6-3-7-8) mit den Zündkerzen. Der Zündbefehl wird am Ansaugkrümmer des Motors angezeigt.