Der Zylinderblock ist aus Grauguss gegossen und hat die Form eines Monoblocks, wobei der Kurbelgehäuseteil unter die Achse der Kurbelwelle abgesenkt ist
Zwischen den Zylindern im oberen Teil befinden sich in den Guss eingearbeitete Kanäle für den Kühlmitteldurchgang
Am unteren Ende des Blocks befinden sich fünf Hauptlagergehäuse.
Die Hauptlagerdeckel bestehen aus hochfestem Gusseisen und werden zusammen mit dem Zylinderblock bearbeitet und sind daher nicht austauschbar.
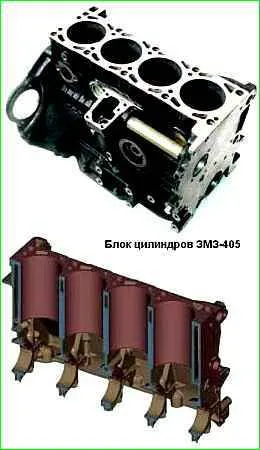
Auf der Unterseite der 1., 2. und 4. Abdeckung sind ihre Nummern zur korrekten Installation eingeprägt. Bei der Montage von Abdeckungen sollten sich die Rastnuten für die Laufbuchsen im Zylinderblock und in den Abdeckungen auf einer Seite befinden.
Blöcke mit Löchern in den Zylinderwänden, Rissen in der oberen Ebene des Blocks und an den Rippen, die die Hauptlager tragen, mit Löchern im Wassermantel und im Kurbelgehäuse unterliegen der Ablehnung.
Durch die natürliche Abnutzung nehmen die Zylinder im Block die Form eines unregelmäßigen Kegels in der Länge und eines Ovals im Umfang an.
Der Verschleiß erreicht seinen größten Wert im oberen Teil der Zylinder gegen den oberen Kompressionsring, wenn die Kolbenposition am oberen Totpunkt liegt, und am geringsten im unteren Teil, wenn die Kolbenposition am oberen Totpunkt liegt.
Zylinder und Kolben sind in fünf Größengruppen A, B, C, D, E unterteilt. Der Buchstabe, der die Zylindergruppe angibt, ist auf der linken Außenseite des Blocks gegenüber jedem Zylinder aufgemalt.
Alle Zylinder in einem Block sollten grundsätzlich auf das gleiche Reparaturmaß mit einer Toleranz von +0,036...+0,072 mm vom Nennwert bearbeitet werden, außer in Fällen, in denen ein flacher Ausbau erforderlich ist Kratzer auf dem Zylinderspiegel (im Vergrößerungsbereich Zylinderdurchmesser um 0,10 mm), hier können nur defekte Zylinder korrigiert werden.
Wenn nur eine begrenzte Anzahl von Kolben verfügbar ist, wird empfohlen, den Nenndurchmesser für jeden Zylinder auf der Grundlage der tatsächlichen Größe des Kolbenmanteldurchmessers zu berechnen, der für den Betrieb in diesem Zylinder vorgesehen ist, und die Zylinder innerhalb von 24 Stunden auf diese Größe zu bearbeiten Bearbeitungstoleranz unten angegeben.
Abweichungen von der geometrisch korrekten Form der Zylinder müssen im Toleranzbereich der Größengruppe für den Durchmesser des Zylinders liegen.
Die Dichtheit des Kühlmantels wird mit der Druckprüfmethode überprüft. Dazu müssen Sie alle Löcher im Block verschließen, bis auf eines, das mit Druckluft versorgt wird.
Der Block wird in ein Wasserbad abgesenkt und Druckluft mit einem Druck von 1,5 atm zugeführt. An beschädigten Stellen entstehen Luftblasen.
Die Reparatur von Zwischenwellenstützbuchsen besteht darin, sie je nach Verschleiß der Befestigungslöcher im Zylinderblock durch Standard- oder Reparaturbuchsen mit erhöhter Dicke zu ersetzen und dann das Innenloch der Buchsen auf eine Standard- oder Reparaturgröße aufzubohren , abhängig vom Verschleiß der Zwischenwellenlagerzapfen.
Stellen Sie Reparaturbuchsen aus einer reibungsarmen Legierung her.
Ersetzen Sie Standardbuchsen durch Reparaturbuchsen, auch wenn ihr Sitz gelockert oder verdreht ist.
Entfernen Sie vor dem Einbau der Zwischenwellenstützen das Rohr. Achten Sie beim Einbau von Reparaturbuchsen darauf, dass die Löcher in den Ölkanälen übereinstimmen.
Bohren Sie die Zwischenwellenhalterungen in einer Installation, um die Ausrichtung sicherzustellen. Drücken Sie den neuen Schlauch auf das anaerobe Dichtmittel.
Die Zwischenwellenzapfen werden auf Reparaturmaß geschliffen, falls der Verschleiß das maximal zulässige Maß überschreitet.
Wenn die Löcher für den Ölpumpenantrieb über das akzeptable Maß hinaus abgenutzt sind, bohren Sie die Löcher auf die Reparaturgröße für Reparaturbuchsen.
Stellen Sie Reparaturbuchsen aus Grauguss mit einem Außendurchmesser von 21 mm und einer Länge von unten – 17 mm, oben – 30 mm her.
Reparaturbuchsen einpressen, in die obere Buchse durch ein Loch mit konischem Gewinde ein Durchgangsloch für die Ölzufuhr Ø 3,5 mm bohren, das in die Ölleitung des Zylinderblocks führt, und die Löcher in den Buchsen auf Nennwert bearbeiten Größe.
Bearbeiten Sie die Befestigungslöcher des Zylinderblocks für die Buchsen und die Buchsenlöcher in einer Installation.
Schäden an Gewindelöchern in Form von Kerben oder Gewindebrüchen von weniger als zwei Gewindegängen werden behoben, indem die Gewinde mit einem Gewindebohrer normaler Größe bearbeitet werden.
Gewindelöcher mit verschlissenen oder gebrochenen Gewindegängen von mehr als zwei Gewindegängen werden repariert, indem Gewinde mit einer größeren Reparaturgröße geschnitten, Gewindeschrauben eingebaut und diese dann in normale Gewinde geschnitten werden Die letztere Reparaturmethode ist die effektivste und am wenigsten arbeitsintensivste.
Kontrollierte Parameter bei der Reparatur von Zylinderblock, Kolben, Pleuel und Zwischenwelle:
Zylinderdurchmesser:
- - Nenngröße Ø 95,5+0,072*+0,036 mm;
- - maximal zulässige Größe 95,65 mm;
- - erste Reparaturgröße +0,25 mm;
- - zweite Reparaturgröße +0,5 mm
Kolbendurchmesser:
- - Nenngröße Ø 95,5+0,024* -0,012 mm;
- - maximal zulässige Größe 95,4 mm;
- - erste Reparaturgröße +0,25 mm;
- - zweite Reparaturgröße +0,5 mm
Spalt zwischen Kolben und Zylinder (Auswahl):
- - Nenngröße 0,036–0,060 mm;
- - maximal zulässige Größe 0,25 mm;
Erhöhung für Reparaturgrößen von Zylindern, Kolben, Kolbenringen:
- - erste Reparaturgröße 0,25;
- - zweite Reparaturgröße 0,5
Rillenbreite für Kompressionsringe:
- - Obermaterial, Nenngröße – 1,55 ± 0,01 mm, maximal zulässig – 1,58 mm;
- - untere Nenngröße - 1,8 ± 0,01 mm, maximal zulässige Größe - 1,83 mm
Der Höhenspalt zwischen der Nut und dem Kompressionsring hat die Nenngröße – 0,045...0,090 mm, maximal zulässig – 0,15 mm;
Der Höhenspalt zwischen der Nut und dem Ölabstreifring beträgt Nennmaß – 0,045...0,090 mm, maximal zulässig – 0,15 mm;
Der Durchmesser der Zylinderblockhalterungen für die Hauptlagerschalen beträgt Nennmaß - 67+0,019 mm, maximal zulässig - 67,03 mm;
Radialer Schlag der mittleren Stützen des Zylinderblocks relativ zu den äußeren: Nenngröße - 0,02 mm; maximal zulässig - 0,05 mm;
Breite der dritten Stütze des Zylinderblocks: Nenngröße - 29-0,060-0,120 mm; maximal zulässige Größe - 22,1 mm;
Durchmesser der Innenbuchsen der Zwischenwellenträger:
- - Nenngröße der vorderen Buchse - 49+0,050 mm; maximal zulässige Größe - 49,1 mm; Reparaturgröße -0,2 mm;
- - Nenngröße der hinteren Buchse – 22+0,041+0,020 mm; maximal zulässige Größe - 22,1 mm, Reparaturgröße -0,2 mm;
Durchmesser der Zwischenwellenzapfen:
- - Nenngröße des vorderen Halses – 49–0,016–0,013 mm; maximal zulässige Größe - 48,95 mm, Reparaturgröße -0,2 mm;
- - Nenngröße des hinteren Halses – 22–0,013 mm; maximal zulässige Größe - 21,95 mm; Reparaturgröße -0,2 mm;
Durchmesser der Zylinderblocklöcher für Zwischenwellenbuchsen:
- - Nenngröße der vorderen Buchse - Ø 52,5+0,03 mm; maximal zulässige Größe - 52,56 mm, Reparaturgröße - +1,5 mm;
- - Nenngröße der hinteren Buchse – Ø 25+0,021 mm; maximal zulässige Größe - 25,06; Reparaturgröße - +1,5 mm;
Durchmesser der Bohrung für die Antriebswelle der Ölpumpe: Nenngröße Ø17+0,060+0,033; maximal zulässige Größe - 17,1 mm; Reparaturgröße Ø21+0,033 mm;
Durchmesser des Pleuelkurbelkopfes: Nennmaß 60+0,019 mm; maximal zulässige Größe 60,03 mm
Nichtparallelität der Achsen der Löcher der Kolben- und Kurbelköpfe der Pleuelstange in zwei zueinander senkrechten Ebenen: Nenngröße 0,04 mm auf einer Länge von 100 mm; maximal zulässig - 0,06 mm;
Durchmesser des Pleuellochs für die Buchse: Nenngröße Ø 23,25+0,045 mm; maximal zulässiger Ø23,30 mm;
Durchmesser des Pleuelbuchsenlochs für den Bolzen: Nenngröße 22+0,07*-0,003 mm; maximal zulässig 22,01 mm
*Toleranz 0,036 mm ist in 3 Gruppen unterteilt – alle 0,012 mm
* Die Toleranz von 0,010 mm ist in 4 Größengruppen unterteilt – jeweils 0,0025 mm