Ein einachsiger rahmenloser Kippsattelanhänger (Abb. 1) mit Heckentladung, offener Pritsche und zu öffnender Heckklappe mit einer Tragfähigkeit von 13,5 Tonnen ist für den Transport verschiedener Schüttbaustoffe auf Straßen der Kategorien I und II bestimmt
Das Hauptzugfahrzeug zum Abschleppen ist der Traktor MAZ-504G.
Achse, Naben, Räder und Reifen des Kippaufliegers sind die gleichen wie die des MAZ-5245-Aufliegers.
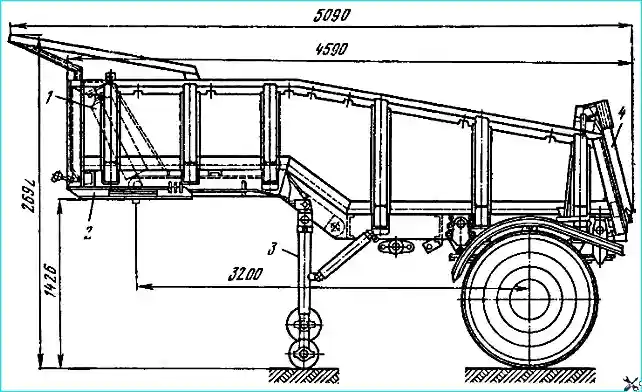
Zugrahmen mit Rollplatte
Die Kupplung des Sattelaufliegers mit der Zugmaschine erfolgt über einen Königszapfen, der in die Aufnahme der 3-Rollen-Platte eingepresst wird (Abb. 2).
Der Durchmesser des Kupplungsbolzens beträgt 50,8 mm.
Die Zugkraft wird über den Zugrahmen 2 übertragen, der über die Achsen 1 mit der Rollplatte 3 verbunden ist. Die Achsen werden durch an Halterungen befestigte Stifte an einer Bewegung gehindert.
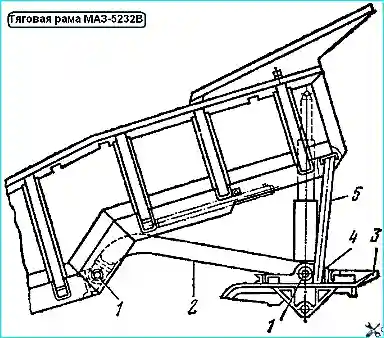
Bei der Rollplatte handelt es sich um eine Schweißkonstruktion, deren Basis ein 6 mm dickes Blech ist.
Zwischen den Längs- und Querträgern ist auf der Platte eine Königszapfenaufnahme mit eingepresstem Königszapfen verschweißt.
Die Zuverlässigkeit der Königszapfenbefestigung wird zusätzlich dadurch gewährleistet, dass der Schaft der unteren Zylinderhalterung in diese eingeschraubt wird (Schaftgewinde M42x x1,5), während die Ebene der Halterung gegen die Königszapfenaufnahme gedrückt wird.
Auf beiden Seiten der Platte sind entlang der Achsschenkelbolzenachse Gusshalterungen 4 zur Befestigung der Rollplatte an der Plattform angeschweißt.
Der Zugrahmen 2 ist aus zwei Längsträgern und drei Querträgern aus 14a-Profil verschweißt. Zur Verbindung mit der Rollplatte und der Plattform sind an den Enden der Längsträger geschmiedete Laschen eingeschweißt.
Innerhalb der Seitenteile und entlang der Enden der Regale sind Verstärkungsstreifen über die gesamte Länge der Seitenteile eingeschweißt, wodurch ein kastenförmiger Abschnitt entsteht.
Die erste Querstrebe dient zur Befestigung der Plattformhebebegrenzungskette und die zweite Querstrebe zur Befestigung der Kettenfreigabefeder.
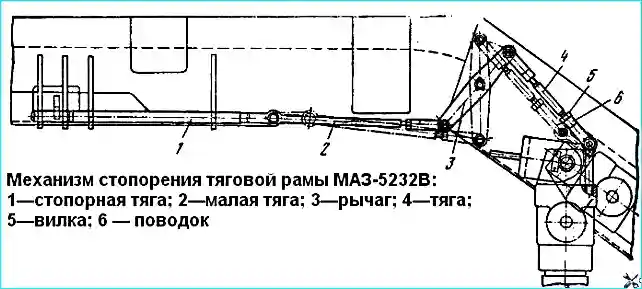
Die Wartung der Rollplatte und des Antriebsrahmens umfasst die regelmäßige Überprüfung und das Festziehen der Achsbefestigungsstifte sowie die Schmierung der Achsen gemäß Schmierplan.
Reparatur
Wenn der radiale Verschleiß des Achsschenkelbolzens mehr als 2 mm beträgt, muss dieser ausgetauscht werden. Der Königszapfen muss nach dem Abkoppeln des Hydraulikzylinders von der unteren Stütze entfernt werden. Dazu:
- - den Sattelauflieger auf Stützvorrichtungen montieren, die Zugmaschine abkoppeln, die Schläuche trennen, die Feststellbremse des Sattelaufliegers anziehen und Stützböcke unter dem Deichselrahmen montieren;
- - Die Verriegelungsstange 1 (siehe Abb. 3) lösen und von den Plattformhalterungen und dem Deichselrahmen abnehmen. Der Zugrahmen mit der Rollplatte wird auf die Böcke abgesenkt;
- - Den hydraulischen Heber von der unteren Halterung des Zylinders trennen und zur Seite bewegen, den Stopper von der unteren Halterung wegbiegen und vom Achsschenkelbolzen abschrauben, den Achsschenkelbolzen aus der Fassung schlagen.
Der Einbau des Königszapfens erfolgt in umgekehrter Reihenfolge.
Wenn die Achse 1 (siehe Abb. 2) der Deichselrahmenaufnahme verschlissen ist, muss diese ausgetauscht werden. Achse aus Stahl 40-45 Ø 50-0,17, Länge 132 mm.
Im Abstand von 15 mm vom Ende wird senkrecht zur Teileachse ein Loch mit Ø 19 mm gebohrt, um den Sicherungsstift einzusetzen.
In der Traktionsrahmenhalterung ist die Bohrung für die Achse Ø 50+0,50 mm, in den Laschen des Traktionsrahmens ist die Bohrung für die Achse Ø 50+0,25 mm eingearbeitet.
Der Austausch der Achsen an der Halterung 4 kann dadurch erfolgen, dass die unbelastete Plattform um 20–25° angehoben wird, der Anschlag 5 entfernt wird und dessen Ende mit dem Stift zwischen die Verstärkungsrippen des ersten Querträgers der Plattform eingesteckt wird und das gegenüberliegende Ende mit dem Führungsrohr in die Aufnahme der rechten Halterung der Rollplatte gesteckt wird. Anschließend senken Sie die Plattform bis zum Anschlag ab.
Verriegelungsmechanismus des Bremsrahmens
Vorrichtung. Um zu verhindern, dass sich der Zugrahmen mit der Abrollplatte beim Abkuppeln der Zugmaschine vom Sattelauflieger auf den Boden absenkt, wird eine Zugrahmenverriegelung eingesetzt (Abb. 3).
Bevor die Zugmaschine vom Auflieger abgekoppelt wird, muss die Stützvorrichtung abgesenkt werden, die sich in einem bestimmten Winkel zur Achse dreht.
Am Körper der Stützvorrichtung ist eine Leine befestigt, die über eine Stange 4 mit dem Hebel 3 des Verriegelungsmechanismus verbunden ist.
Schalthebel bewegt die Verriegelungsstange 1 mit Hilfe der Stange 2. Die Verriegelungsstange dringt in die Löcher der Ösen des Zugrahmens und der Basis der Plattform ein und verhindert so, dass der Zugrahmen mit der Rollplatte herunterfällt.
In Arbeitsstellung des Sattelanhängers müssen die Stützvorrichtungen angehoben sein.
Die Wartung des Verriegelungsmechanismus besteht in der rechtzeitigen Reinigung der Verbindung der Stangen und Gabeln von Schmutz. Außerdem muss darauf geachtet werden, dass die Stangen des Verriegelungsmechanismus nicht verbogen werden.
Wenn die Stangen verbogen sind, müssen sie gerade gebogen werden. Wenn die Verriegelungsstange nicht vollständig in die Halterungsösen eindringt, muss sie durch Drehen der Stangen in den Montagegabeln angepasst werden.
Mögliche Störungen am Zugrahmen und der Rollplatte und deren Beseitigung
Ursache der Störung - Methode zur Beseitigung
- Die ursprüngliche Position der Antriebsrahmen-Montageachsen ist beschädigt
Abgenutzte oder verlorene Achsbefestigungsstifte – Stifte ersetzen
- Spürbare Rucke beim Ändern der Bewegungsgeschwindigkeit
Königszapfenverschleiß mehr als 2 mm - Königszapfen ersetzen
Verschlissene Deichselrahmen-Befestigungsachsen - Achsen ersetzen
Verschleiß in den Halterungen oder Ösen des Deichselrahmens - Reparaturbuchsen in die Halterungen oder Ösen einpressen
Aussetzung
Die Achse ist mit Hilfe von Längs- und Halbellipsenfedern am Rahmen des Aufliegers aufgehängt.
Die Hauptfeder ist in zwei Gruppen unterteilt:
- - die erste Federgruppe mit einem Federweg von 65-8 mm, die zweite mit einem Federweg von 65+8 mm.
Zusätzliche Federn werden ebenfalls in zwei Gruppen unterteilt:
- -- die erste Federgruppe mit einem Federweg von 48+7 mm;
- - Sekunde mit einer Auslenkung von 48+1 mm.
Bremssystem
Das Bremssystem des Sattelaufliegers ähnelt dem Bremssystem des Sattelaufliegers MAZ-5245. Die Feststellbremse funktioniert ähnlich wie die gleiche Bremse am Anhänger MAZ-5206.
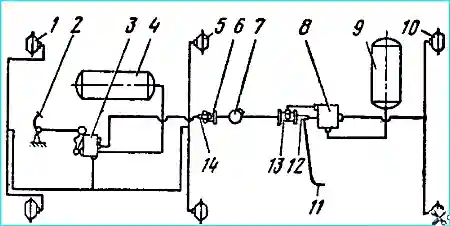
Eine Besonderheit bei einem rahmenlosen Kippsattelanhänger besteht darin, dass beim Entladen darauf geachtet werden muss, dass der Sattelanhänger an die Zugmaschine heranrollt bzw. die Zugmaschine an den Sattelanhänger heranrollt.
Unter Berücksichtigung dieses Umstands bietet das pneumatische Bremsantriebssystem des Lastzuges, bestehend aus der Zugmaschine MAZ-504G und dem Sattelauflieger MAZ-5232V, die Möglichkeit, je nach Entladebedingungen eine Zugmaschine oder einen Sattelauflieger zu bremsen (Abb. 4).
Je nach Entladebedingungen sollte die Bremsung wie folgt durchgeführt werden.
Beim Entladen in eine Deponie oder einen Bunker muss der Sattelanhänger gebremst werden. Dazu muss der Griff 14 des am Traktor installierten Trennventils 6 in eine Position senkrecht zur Längsachse des Krans gebracht werden.
In diesem Fall wird Luft aus der Anschlussleitung des Sattelaufliegers in die Atmosphäre abgelassen, wodurch das Luftverteilventil 8 aktiviert wird und der Sattelauflieger ohne Betätigung des Bremspedals 2 in der Sattelzugmaschine abgebremst wird.
Nach Abschluss des Entladens sollte der Griff 14 wieder in seine Ausgangsposition zurückgebracht werden.
Beim Entladen eines Sattelaufliegers auf einer Plattform empfiehlt es sich, die Zugmaschine abzubremsen, um die Ladung besser von der Plattform zu entfernen und so sicherzustellen, dass der Sattelauflieger aufrollt.
Hierzu muss der Griff 12 des am Sattelanhänger montierten Sattelhandbremsventils mittels der Stange 11 in eine Position senkrecht zur Ventillängsachse gebracht werden, wodurch das Luftverteilventil 8 betätigt wird und der Sattelanhänger freigegeben wird.
Das Abbremsen des Traktors erfolgt durch Betätigen des Bremspedals in der Traktorkabine.
Nach Abschluss des Entladens sollte der Griff 12 wieder in seine Ausgangsposition zurückgebracht werden.
In anderen Fällen ist das Entladen des Sattelanhängers bei ungebremster Zugmaschine und Sattelanhänger unter Beachtung der Sicherheitsvorschriften zulässig. Dabei ist es möglich, sowohl einen Sattelauflieger als auch eine Zugmaschine anzurollen.
Das Entladen eines Sattelanhängers bei gleichzeitigem Bremsen der Zugmaschine und des Sattelanhängers, sowohl mit der Betriebs- als auch mit der Feststellbremse, ist nicht zulässig, da dies aufgrund der Unmöglichkeit, die Zugmaschine und den Sattelanhänger zu rollen, zu einer starken Erhöhung der Belastung der Kipp- und anderer Mechanismen des Lastzugs führt, was zu deren Ausfall führen kann.
Elektrische Ausrüstung
Die elektrische Ausrüstung besteht aus siebenpolige Steckdose, zwei Rücklichter, die als Bremslicht fungieren, Seitenlichter, Blinker, eine Kennzeichenbeleuchtung und seitlich an der Plattform angebrachte Reflektoren.
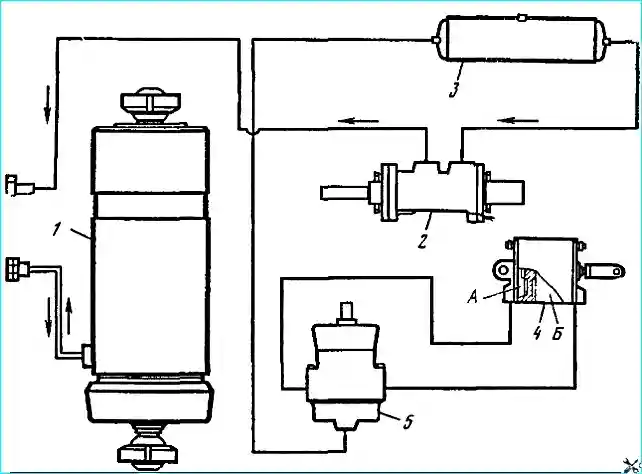
Die Ladefläche des Kippaufliegers ist tragfähig, aus Metall und verfügt über eine automatisch öffnende und schließende Ladeklappe.
Innenmaße der Plattform: Länge 4420 mm, Breite 2290 mm, Höhe vorne 660 mm, hinten 570 mm; Plattformvolumen 7 m³.
Die Plattform besteht aus dem eigentlichen Aufbau, einem Visier, einer Ladeklappe, einem Mechanismus mit Ladeklappenverriegelungsantrieb und Gummi-Metall-Stoßdämpfern.
Der Aufbau des Sattelaufliegers ist aus gestanzten Profilen geschweißt. Die Basis bilden Längsträger aus 20a-Profil.
Die Seitenteile sind aus 3 mm starkem Blech gefertigt und mit Omega-förmigen Streben verstärkt, die in die Bodenbefestigungsquerträger übergehen.
Der Boden ist zweistufig.
Die erste Ebene ist ein gestanztes Wellprofil mit einer Höhe von 30 mm und einer Dicke von 2 mm, das mit den Seitenelementen, Querträgern und dem unteren Teil der Seiten verschweißt ist.
Die zweite Ebene besteht aus einem 6 mm dicken Blech, das mit dem unteren Boden und den Seiten verschweißt ist.
An der Oberkante der Seitenwände ist eine gestanzte Verstärkung mit Löchern zur Montage von Seitenaufsätzen angeschweißt.
In die Vorderseite ist eine Nische für den Einbau einer hydraulischen Plattformhebebühne eingeschweißt.
Um den Traktor vor herabfallender Ladung zu schützen, ist an der Vorderseite der Karosserie ein Visier mit M10-Schrauben befestigt.
Vier Stoßdämpfer sind vorne unterhalb der Längsträger angebracht, um den Traktionsrahmen zu stützen.
Die Heckklappe öffnet sich um die oberen Achsen in den Bordwandhalterungen.
Die Seite wird je nach Hubwinkel der Plattform automatisch geöffnet und geschlossen.
Bei Bedarf können Sie den manuellen Verriegelungsmechanismus nutzen, der sich auf der linken Seite in der Nähe der Ladeklappe befindet.
Federhalterungen sind an den Plattformseitenteilen vernietet, Halterungen für Stützvorrichtungen und Halterungen für den Traktionsrahmen sind verschweißt.
Die Kotflügelhalterungen sind an den beiden hinteren Seitenstreben angeschweißt. Die Kotflügel werden mit M8X20 Schrauben an den Halterungen befestigt.
Die Wartung der Plattform besteht aus regelmäßigem Waschen und Ausbessern mit Farbe.
Bei Bedarf wird das Heckklappenschloss eingestellt. Die manuelle Verriegelung der Heckklappe muss nachjustiert werden, wenn in der Ebene des Heckklappenkontakts ein Spalt von mehr als 6 mm besteht.
Plattformreparaturen werden normalerweise durch Schweißen durchgeführt, wenn der Boden oder die Seiten durch Ladung beschädigt sind.
Beschädigte Stellen werden begradigt und ggf. mit zusätzlichem Einbau von Verstärkungsblechen verschweißt. Die Verstärkungsbleche sind mit durchgehenden Nähten verschweißt.
Plattform-Hebemechanismus
Der Kippauflieger arbeitet mit der Zugmaschine MAZ-504G zusammen, die mit einer speziellen Hydraulikausrüstung ausgestattet ist, die zum Anheben der Plattform des transportierten Kippaufliegers dient und vom Motor angetrieben wird (Abb. 5).
Der Plattformhebemechanismus sorgt dafür, dass die Plattform bis zu einem Winkel von 45° angehoben, abgesenkt und in jeder Zwischenposition angehalten wird, begrenzt automatisch den Hebewinkel und rüttelt die Plattform am Ende des Hubs, um die Last besser entladen zu können.
Zusätzlich ist ein automatisches Öffnen und Schließen der Plattformrückseite vorgesehen.
Der Hebemechanismus der Plattform wird pneumatisch von der Fahrerkabine aus über ein Luftverteilungsventil ferngesteuert.
Die pneumatische Fernbedienung des Plattformhebemechanismus und der Ladebordwandverriegelung erleichtert dem Fahrer die Arbeit und verkürzt die Entladezeit.
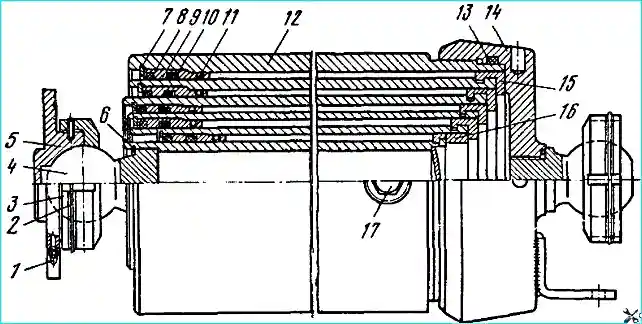
Der Hydraulikzylinder dient zum Anheben der Plattform. Es besteht aus einem festen Körperrohr 12 (Abb. 6) und fünf darin teleskopartig angeordneten einziehbaren Gliedern.
Die Abdichtung der Gleitverbindungen erfolgt durch Gummiringe 10 mit kreisförmigem Querschnitt, die im Kanal platziert sind in den Führungshülsen 9.
Die Führungshülsen selbst werden in den Rohren mit den gleichen Ringen 11 abgedichtet. Die Dichtringe der beweglichen Glieder werden durch schmutzabweisende Gummiringe 8 von außen vor Schmutz und Staub geschützt.
Die Führung der Gleitglieder und die Begrenzung ihres Bewegungsweges werden durch die mit Sicherungsringen gesicherten oberen Führungshülsen und die Führungshalbringe 15 erreicht, die in die im unteren Teil befindlichen beweglichen Glieder eingesetzt werden.
Von unten ist der Zylinderkörper durch einen Boden 14 verschlossen, der durch einen Gummiring 13 abgedichtet ist.
Die obere Abstützung des Zylinders (in der Plattform) erfolgt in Form eines Kugelgelenks.
Kugelzapfen 4 wird mittels Sicherungsring 6 im inneren Verlängerungsrohr und gleichzeitig mittels Mutter 3, die durch Sicherungsring 2 arretiert wird, am Kugelabsatz 5 der Plattform gesichert.
Eine ähnliche Scharnierverbindung verbindet das untere Ende des Zylinders mit der Rollplatte.
Die gelenkige Verbindung des Zylinders mit der Rollplatte und der Plattform befreit alle Zylinderverbindungen von den Auswirkungen der Querbelastungen, die beim Kippen der Plattform auftreten.
Die Ölzufuhr zum Zylinder erfolgt durch eine Öffnung im unteren Teil des festen Rohrs, die durch den Stopfen 17 verschlossen ist.
Die Kugelgelenke der oberen und unteren Zylinderhalterungen werden durch Öler 1 geschmiert.
Der Hubbegrenzungsmechanismus der Plattform (Abb. 7) dient dazu, den Hubwinkel der Plattform zu begrenzen und dafür zu sorgen, dass diese am Ende des Hubs rüttelt.
Das Ventil 12 zur Begrenzung des Plattformhubs wird in die Querträgeröffnung eingebaut und mit der Schraube 14 gesichert.
Durch die Stange 4, die mit dem Gelenkhebel 6 verbunden ist, bewegt sich die Spitze 7 beim Anheben der Plattform um einen Abstand von 3,0–3,5 mm zwischen der Mutter 11 und dem Ende der Abdeckung des Plattformhubbegrenzungsventils nach rechts (Abb. 8).
Wenn die Plattform auf den eingestellten Winkel angehoben wird, wirkt Hebel 6 (Abb. 7) auf Spitze 7, die Schaft 9 (siehe Abb. 8) des Ventils bewegt. Dabei stößt die Stange gegen Ventil 5 und reißt es aus der Fassung.
Unter Druck stehende Luft aus Hohlraum „A“ strömt in Hohlraum „B“ und gelangt dann in die pneumatische Kammer des am Traktor installierten Steuerventils.
In diesem Fall wird die Auslassleitung des Plattformhebemechanismus mit der Ablassleitung verbunden und die Plattform, die Öl aus dem Zylinder verdrängt, wird in einem bestimmten Winkel abgesenkt, bis das Ventil 5 unter der Wirkung der Feder 4 gegen den Sitz gedrückt wird und die Stange 9 durch die Kraft der Feder 6 in ihre ursprüngliche Position zurückkehrt.
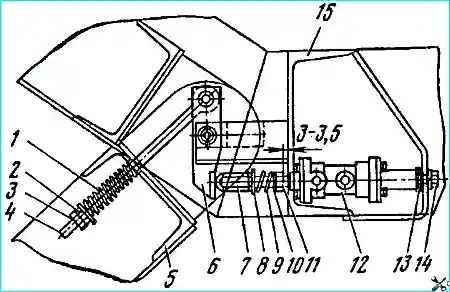
Luft aus der pneumatischen Kammer des Steuerventils wird durch Loch „B“ im Ventilschaft 9 in die Atmosphäre abgelassen, woraufhin die Plattform zu steigen beginnt und der Zyklus sich wiederholt.
Durch abwechselndes Öffnen und Schließen des Ventils wird sichergestellt, dass die Plattform am Ende des Hubvorgangs geschüttelt wird, was das Abladen der Last erheblich erleichtert.
Der hintere Seitenverriegelungsmechanismus (Abb. 9) dient dazu, die Seite beim Anheben der Plattform automatisch zu öffnen und in der Transportposition zu verriegeln.
Der Mechanismus wird durch einen pneumatischen Antrieb mit einem automatischen Ventil zur Steuerung des Seitenverriegelungsmechanismus angetrieben, das Luft in den pneumatischen Zylinder der Seitenverriegelung leitet.
Die seitlichen Zapfen 2 werden von zwei Griffen 1 gehalten, die sich auf beiden Seiten der Plattform befinden. Die Griffe 1 sind durch Stangen 15 mit Hebeln 11 verbunden, die starr auf einer gemeinsamen Welle 12 befestigt sind.
Jede der Stangen besteht aus zwei Teilen, die durch ein Gewinde so miteinander verbunden sind, dass die Gesamtlänge der Stange verändert werden kann.
Wenn sich die Welle 12 um einen bestimmten Winkel in die eine oder andere Richtung dreht, klemmen die Klemmen 1 die Zapfen 2 der Rückseite fest oder geben sie frei.
Zum Antrieb der Welle 12 wird ein doppeltwirkender, schwenkbarer Pneumatikzylinder 10 verwendet.
Die Deckel und der Zylinderkörper werden durch vier Bolzen zusammengehalten.
Kolben und Stange sind mit O-Ringen aus Gummi abgedichtet.
Der Zylinder ist mittels Stift 9 gelenkig an der Querstrebe 8 der Plattform befestigt und seine Stange ist mittels Gabel 6 über Stift 5 mit Hebel 4 verbunden, der in seinem Mittelteil starr mit Welle 12 verbunden ist.
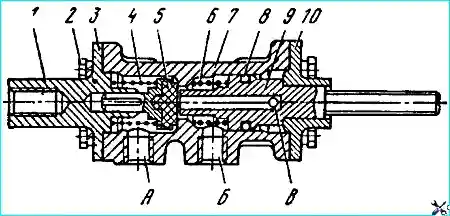
Die Luftzufuhr zum Pneumatikzylinder erfolgt durch Öffnungen in den Abdeckungen über Luftkanäle, die mit der automatischen Ventil zur Steuerung des seitlichen Verriegelungsmechanismus.
Wenn dem Hohlraum „A“ (Abb. 5) des Zylinders Luft zugeführt wird, bewegt sich der Kolben nach rechts und dreht die Welle 12 mithilfe des Hebels 4 (siehe Abb. 9). Die Stangen 15 bewegen sich ebenfalls, wodurch die Griffe 1 gegen den Uhrzeigersinn gedreht werden und die Seitenzapfen freigegeben werden.
Wenn Hohlraum „B“ (siehe Abb. 5) mit Luft versorgt wird (in diesem Fall wird Hohlraum „A“ über ein Ventil mit der Atmosphäre verbunden), erfolgt die Bewegung aller Glieder des Mechanismus in die entgegengesetzte Richtung und die Greifer drehen sich im Uhrzeigersinn und klemmen die Seitenzapfen fest.
Wenn sich der Sattelanhänger bewegt, steht der Hohlraum „B“ des Zylinders unter Luftdruck und somit wird der Kolben zwangsweise in der Position gehalten, die der geschlossenen Seite entspricht.
Auch bei fehlendem Luftdruck ist ein spontanes Öffnen der Seite ausgeschlossen, da sich die Stangen 15 (siehe Abb. 10) bei der der geschlossenen Seite entsprechenden Stellung der Mechanismusglieder oberhalb der Achse der Welle 12 befinden (den Totpunkt überschreiten), was eine Drehung dieser Welle im Uhrzeigersinn verhindert.
Um bei einer eventuellen Störung des pneumatischen Antriebs die Seitengriffe ansteuern zu können, ist an der Welle 12 auf der linken Seite des Sattelanhängers ein Griff 13 angebracht, mit dem der Fahrer die Seite öffnen oder schließen kann.
Bei geschlossener Seite liegt das Griffende am hinteren Widerlager der Seitenwand an, wodurch der Pneumatikzylinder von den Belastungen entlastet wird, die entstehen, wenn die Last auf die Rückseite drückt.
Die automatische Steuerung der Seitenverriegelung erfolgt über Ventil 5 (siehe Abb. 5).
Luft aus dem Luftzylinder des Sattelanhängers wird dem Ventil durch die Öffnung in der unteren Abdeckung 1 (Abb. 10) des Ventils zugeführt.
Wenn die Plattform angehoben wird, wirkt der Haken des Zugrahmens auf den Hebel 6 des Ventils, das an der Plattformquerstrebe montiert ist, welches sich um die Achse dreht und auf den Schieber drückt
Beim Abstieg drückt der Drücker das Gummiventil 12 von der Fassung weg.
Luft strömt aus dem unteren Hohlraum in den Raum zwischen dem Stößel und der Öffnung im Körper und wird durch die Öffnung 1 im Körper über eine Rohrleitung dem seitlich verriegelnden Pneumatikzylinder zugeführt.
Beim Absenken der Plattform wirkt der Haken des Zugrahmens auf den Hebel 6, der sich um die Achse dreht und auf den anderen Schieber drückt.
Der Vorgang ist ähnlich wie beschrieben, allerdings wird Luft in einen anderen Hohlraum des Zylinders geleitet.
Die aus dem Zylinder ausgestoßene Luft wird durch ein Loch im Drücker in die Atmosphäre abgegeben.
Der Plattform-Sicherheitsanschlag befindet sich auf der rechten Seite des Sattelanhängers.
Um den Anschlag zu montieren, müssen Sie die Plattform auf einen Winkel von 20 - 25˚ anheben, dann den Anschlag entfernen und das Ende mit dem Stift in die Plattformquerstrebe zwischen den Rippen einführen.
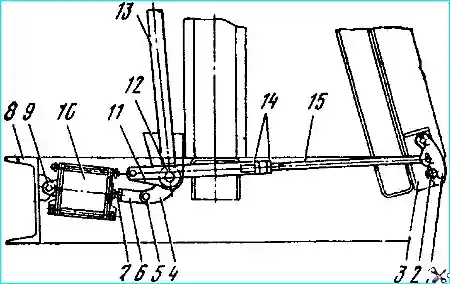
Das Führungsrohr muss in die Aufnahme der Rollplattenhalterung abgesenkt werden, danach muss die Plattform bis zum Anschlag abgesenkt werden.
Die Benutzung der Haltestelle ist bei beladenem Bahnsteig verboten.
Wartung. Während des Betriebs ist es notwendig, die Befestigung des Hydraulikzylinders am Rahmen und an der Plattform systematisch zu überprüfen, die Dichtheit seiner Dichtungen zu überwachen und die Kugelgelenke seiner oberen und unteren Stützen regelmäßig durch die Öler zu schmieren.
Es wird empfohlen, die Zylinderhalterung während TO-1 zu überprüfen. In diesem Fall ist es notwendig, die Zuverlässigkeit der Verriegelung der Muttern der oberen und unteren Zylinderhalterungen zu überprüfen.
Nach längerem Betrieb können an den Oberflächen der Hydraulikzylinder-Ausfahrglieder kleinere Ölleckagen auftreten, die durch das Abstreifen des Ölfilms durch die Dichtringe entstehen.
Sie sollten mit einem sauberen, trockenen Tuch entfernt werden. Starke Öllecks deuten auf verschlissene Dichtungsringe hin.
In diesem Fall müssen die Dichtringe ausgetauscht werden, da das Vorhandensein von Öl auf den Laufflächen der Zylinderglieder zu Verunreinigungen und in der Folge zu einem beschleunigten Verschleiß der Teile führt.
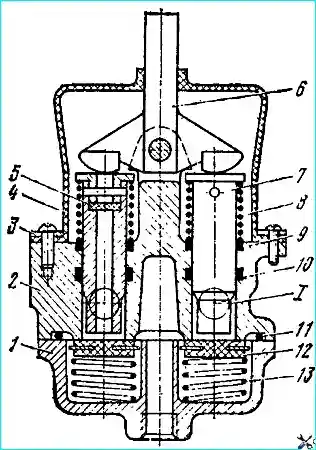
Unter normalen Betriebsbedingungen entspricht die Lebensdauer der Dichtungsringe 80-100.000 km der Kilometerleistung des Sattelanhängers, jedoch bei erheblicher Überlastung des Sattelanhängers und bei Verwendung Bei Verschmutzung mit Öl wird die Lebensdauer der Ringe stark reduziert.
Der häufige Austausch der Dichtringe der Hydraulikzylinder-Verlängerungsglieder unter normalen Betriebsbedingungen deutet auf Verschleiß hin und darauf, dass die oberen Führungshülsen ausgetauscht werden müssen.
Um einen Bruch der unteren Führungshalbringe der Zylinderverbindungen zu vermeiden, ist es notwendig, das Absenken einer unbeladenen oder sogar teilweise entladenen Plattform zu vermeiden, da die Führungshalbringe beim beschleunigten Absenken der Plattform starken Stoßbelastungen ausgesetzt sind.
Für den normalen Betrieb des Hydraulikzylinders ist es von großer Bedeutung, die maximale Hubwinkelbegrenzung der Plattform richtig einzustellen. Dies wird durch die Anpassung des Hubwinkelbegrenzungsmechanismus der Plattform erreicht.
Ein richtig eingestellter Mechanismus sollte es nicht zulassen, dass die Plattform mehr als 45° ansteigt.
Bei einem solchen Hubwinkel der Plattform ist der Zylinderhub etwas kleiner als der maximal mögliche und daher arbeitet der Zylinder nicht unter Spannung.
Die Wartung des Heckklappenverriegelungsmechanismus beschränkt sich auf die systematische Überwachung der Dichtheit der Verbindungen, Rohre und Schläuche, die den Zylinder mit Luft versorgen, der Dichtheit des Zylinders selbst und der regelmäßigen Überprüfung der Einstellung des Mechanismus.
Erhebliche Luftlecks durch Luftkanalverbindungen, Dichtungen der Abdeckungen pneumatischer Zylinder und deren Stangen werden normalerweise durch Gehör erkannt.
Kleinere Luftlecks können mit einer Seifenlösung aufgespürt werden. Die Dichtheit des Systems sollte während TO-1 überprüft werden.
Es wird empfohlen, den Mechanismus nur bei Bedarf einzustellen, wenn eine Funktionsstörung festgestellt wird.
Die Einstellung des Heckklappenverriegelungsmechanismus besteht aus der richtigen Auswahl der Länge der Stangen 15 (siehe Abb. 9) und der Länge der pneumatischen Zylinderstange 10.
Die Längenänderung der Stange 15 erfolgt durch Verschieben der Muttern 14 entlang des Stangengewindes. Die Längenänderung der Stange erfolgt durch Auf- bzw. Abschrauben der Gabel 6 auf die Zylinderstange.
Es wird empfohlen, den seitlichen Verriegelungsmechanismus in der folgenden Reihenfolge einzustellen:
- - Lassen Sie die Luft aus dem pneumatischen System des Traktors ab, lösen und entfernen Sie den Stift 5, der die Zylinderstange an Hebel 4 befestigt, und drücken Sie die Zylinderstange, bis der Kolben an der unteren Abdeckung anschlägt.
- - Drücken Sie das freie Ende des Griffs an den Widerlager, erhöhen Sie die Länge der linken Stange 15 durch Drehen der Muttern 14 auf einen Wert, der eine zuverlässige Klemmung des Seitenzapfens zwischen der Halterung 3 und dem Griff 1 gewährleistet.
Passen Sie auch die Länge des rechten Griffzugs an;
- Überprüfen Sie die Funktion des seitlichen Verriegelungsmechanismus manuell. Hierzu die Schlösser 2-3 mal mit dem Griff 13 öffnen und schließen.
Wenn die zum Bewegen der Stange durch den Totpunkt erforderliche Kraft zu groß ist, sollte die Länge der Stangen erhöht werden. Muttern 14 festziehen;
- - verlängern Sie die Zylinderstange um 5 mm, lösen Sie die Mutter 7 und bringen Sie durch Drehen der Gabel in die gewünschte Richtung die Gabellöcher in Ausrichtung mit dem Loch im Hebel 4, während Sie ihn fest an die Halterung am Ende des Griffs drücken;
- - Einsteck- und Splintfinger 5. Kontermutter 7;
- - Starten Sie den Motor, bringen Sie den Druck im pneumatischen System auf 4 kgf/cm² und heben und senken Sie die leere Plattform mehrere Male, wobei Sie die Funktion des seitlichen Verriegelungsmechanismus überprüfen.
Ein richtig eingestellter Verriegelungsmechanismus sollte eine zuverlässige Klemmung der Zapfen durch die Griffe gewährleisten, ein spontanes Öffnen der Seite verhindern und verhindern, dass die Griffe die Zapfen der Seite beim Öffnen und Schließen während des Hebens und Senkens der Plattform berühren.
Das Öffnen und Schließen der Heckklappe sollte bei einem Plattformhöhenwinkel von 10–15° erfolgen.
Ist dies bei einem größeren oder kleineren Plattformhubwinkel der Fall, ist es erforderlich, das automatische Ventil zur Steuerung der Seitenverriegelung in den Halterungsschlitzen so zu verschieben, dass bei einem Plattformhubwinkel von 10–15° der Ventilhebel 6 (siehe Abb. 7) mit dem Haken an der Querstrebe des Deichselrahmens in Kontakt kommen kann und so die Luftzufuhr zum Pneumatikzylinder der Seitenverriegelung freigegeben wird.
Einstellen des Hubbegrenzungsmechanismus der Plattform. Wenn der Plattformhubmechanismus richtig eingestellt ist, sollte das Plattformhubbegrenzungsventil bei einem Plattformhubwinkel von 45° funktionieren.
In diesem Fall sollte das letzte ausfahrbare Rohr des Zylinders um 250–300 mm ausfahren und die Plattform sollte automatisch rütteln.
Wenn bei vollständig angehobener Plattform das letzte Rohr mehr als 300 oder weniger als 250 mm herausragt; Die Einstellungen müssen in der folgenden Reihenfolge vorgenommen werden:
- - Heben Sie die Plattform mit einem Hebemechanismus an und installieren Sie einen Sicherheitsanschlag;
- - Stellen Sie sicher, dass der Abstand vom Ende des Ventildeckels bis zum Ende der Mutter 11 (siehe Abb. 7) 3–3,5 mm beträgt. Passen Sie den Wert dieses Maßes gegebenenfalls mit der Mutter 11 an und ziehen Sie die Kontermutter 10 fest.
- - Durch Veränderung der Arbeitslänge der Stange 4 mit den Muttern 2 und 3 eine Position erreichen, bei der das Ventil ausgelöst wird, wenn das letzte Zylinderrohr um 250–300 mm ausgefahren wird. Bei der Vergrößerung der Arbeitslänge der Stange 4 (beim Abschrauben und Muttern) vergrößert sich der Hubwinkel der Plattform, und wenn die Länge der Stange abnimmt, verringert er sich. Nach Abschluss der Einstellung die Kontermutter 3 festziehen.
Reparatur
Um den Hydraulikzylinder zu entfernen, müssen Sie:
- - Heben Sie die Plattform mit einem Hebemechanismus oder einer externen Hebevorrichtung an, verriegeln Sie sie sicher mit einem Sicherheitsanschlag und lassen Sie das Öl aus dem System ab;
- - Entfernen Sie den Sicherungsring der oberen Zylinderstützmutter, schrauben Sie die Mutter ab, trennen Sie den Auslassschlauch vom Zylinder, entfernen Sie den Sicherungsring der unteren Zylinderstützmutter und schrauben Sie die Mutter ab;
- - Den Zylinder vom Sattelauflieger entfernen.
Die Reihenfolge der Demontage des Hydraulikzylinders ist wie folgt:
- - Schrauben Sie die Unterseite des Zylinderkörpers ab, entfernen Sie den Dichtungsring von der Unterseite und schieben Sie jedes einziehbare Glied der Reihe nach aus dem Körper, vom Glied mit dem kleinsten Durchmesser bis zum Glied mit dem größten. Entfernen Sie die Führungshalbringe von jedem herausgezogenen Glied.
- - Entfernen Sie die Sicherungsringe zur Befestigung der oberen Führungshülsen vom Zylinderkörper sowie vom ersten, zweiten, dritten und vierten Gleitglied und dann die Führungshülsen selbst;
- - Entfernen Sie die äußeren und inneren Dichtringe sowie Abstreifer aus den Nuten der Führungshülsen.
Waschen und überprüfen Sie alle Zylinderteile sorgfältig. Ersetzen Sie verschlissene Teile. Die am stärksten verschleißenden Teile eines Hydraulikzylinders sind die Dichtringe der beweglichen Glieder und die Abstreifringe.
Wenn die Zylinderdichtringe vor der Demontage nicht fest genug waren, sollten die Ringe ausgetauscht werden.
Überprüfen Sie die Führungshalbringe sorgfältig.
Sollten Absplitterungen oder Risse vorhanden sein, die durch das Absenken einer beladenen Plattform entstanden sein könnten, müssen die Halbringe ausgetauscht werden.
Nach längerem Betrieb des Hydraulikzylinders (ca. nach 80.000 bis 100.000 Plattformaufzügen) kann ein Austausch der oberen Führungshülsen erforderlich sein. Dies äußert sich in der Regel in vergrößerten Spalten zwischen der Führung und dem entsprechenden Verbindungsstück, die einen beschleunigten Verschleiß der Dichtungsringe verursachen.
Die Montage des Hydraulikzylinders erfolgt in umgekehrter Reihenfolge der Demontage.
In diesem Fall ist es notwendig:
- - alle Teile des Hydraulikzylinders gründlich waschen, mit Druckluft ausblasen, die Dichtringe und die Innenfläche der Führungshülsen vor der Montage mit Fett schmieren;
- - Montieren Sie den Hydraulikzylinder vorsichtig und achten Sie darauf, die Dichtungsringe nicht zu beschädigen.
Nach der Montage muss der Zylinder auf Leichtgängigkeit und Dichtheit geprüft werden. Hierzu wird dem Zylinder Öl zugeführt, bis er vollständig expandiert ist, und anschließend der Druck auf 50 kgf/cm² erhöht.
Ein korrekt montierter Zylinder sollte sich unter der Einwirkung des eingepumpten Öls gleichmäßig und ohne Zwischenräume ausdehnen und bei Erreichen des vollen Hubs einem Öldruck von 150 kgf/cm² 5 Minuten lang ohne Undichtigkeiten standhalten.
Der Einbau des Zylinders in den Sattelauflieger erfolgt in umgekehrter Reihenfolge des Ausbaus.
Nach der Montage des Zylinders sichern Sie die Muttern der oberen und unteren Halterung sorgfältig mit einem Sicherungsring.
Mögliche Fehlfunktionen des Hydraulikzylinders und Methoden zu ihrer Beseitigung
Ursache der Störung - Methode zur Beseitigung
- Die Zylinderverbindungen werden nicht in der richtigen Reihenfolge ausgefahren, die Verbindungen werden ruckartig ausgefahren und die Plattform senkt sich nicht vollständig ab
Verklemmung der Zylinderverlängerungsglieder - Zylinder zerlegen, Ursachen der Verklemmung beseitigen
- Übermäßiger Ölaustritt durch die Gleitverbindungsdichtungen
Beschädigte oder verschlissene Dichtungen an Verbindungsstücken oder Führungshülsen – Dichtungen ersetzen
- Öl tritt durch das Gewinde des Zylinderbodens aus
Beschädigter Zylinderbodendichtring - Dichtring ersetzen