Während des Betriebs sowie aufgrund von Fehlern bei der Herstellung von Steuertriebsteilen oder durch unsachgemäße Reparaturen des Steuertriebs ist eine erhebliche Abweichung der Ventilsteuerzeiten von den angegebenen Werten möglich
Die richtige Ventilsteuerung ist einer der wichtigsten Einflussfaktoren auf Leistung, Drehmoment und Wirtschaftlichkeit des Motors.
Wenn daher die Traktionseigenschaften des Motors nachlassen, der Kraftstoffverbrauch im Betrieb zunimmt und der Motor instabil wird, ist es notwendig, die Ventilsteuerung zu überprüfen und gegebenenfalls richtig einzustellen.
Zu diesem Zweck wird ein am ZMZ entwickelter Gerätesatz verwendet.
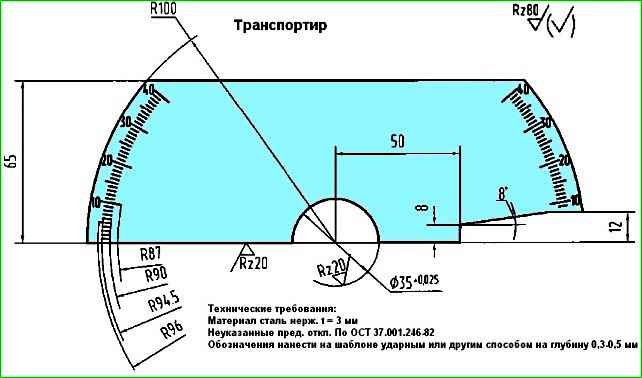
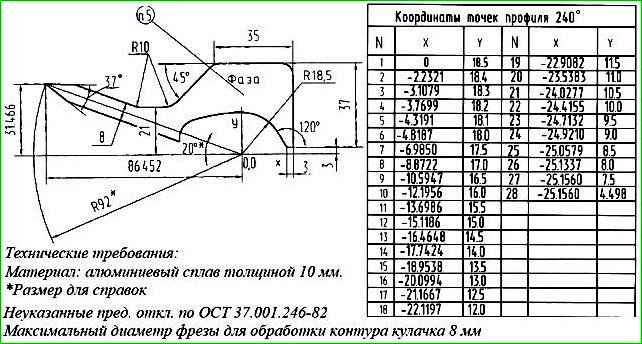
Das Kit enthält: Winkelmesser (Abbildung 1), Schablone (Abbildung 2) mit Nockenprofil und Pfeil
Außerdem eine Vorrichtung zum Bohren zusätzlicher Löcher für den Stift in den Nockenwellenrädern (Abbildung 3).
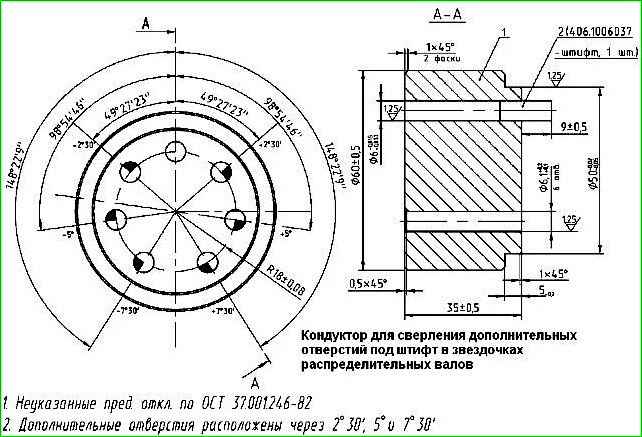
Die Überprüfung und Einstellung der Ventilsteuerung kann an einem in einem Auto eingebauten Motor durchgeführt werden. Um die Ventilsteuerung zu steuern, müssen Sie Folgendes tun:
- 1. Trennen Sie den Kurbelgehäuseentlüftungsschlauch vom Ventildeckelrohr, indem Sie die Befestigungsschelle lösen.
- 2. Trennen Sie die Kabelstecker von den Zündspulen.
- 3. Entfernen Sie die Spitzen von den Zündkerzen mit Dichtungen und Hochspannungskabeln.
- 4. Lösen Sie die Halterungen und entfernen Sie den Kabelbaum vom Ventildeckel.
- 5. Entfernen Sie den Ventildeckel mit Dichtung, Zündkerzenschachtdichtungen, Zündspulen und Hochspannungskabelbaugruppen, indem Sie acht Schrauben (Kopf „12“, Verlängerung und Schraubenschlüssel) lösen.
- Lassen Sie die Schrauben, Unterlegscheiben und Halterungen für den Kabelbaum in den Löchern in der Abdeckung. (Das Bild zeigt die Bühnen am Beispiel des ZMZ-4062)
- 6. Stellen Sie den Kolben des 1. Zylinders auf den oberen Totpunkt des Kompressionshubs, indem Sie die Kurbelwelle in Drehrichtung (im Uhrzeigersinn) drehen, bis die Markierung auf der Kurbelwellen-Dämpferriemenscheibe mit der Markierungsrippe (in Form einer Nabe) auf der Kettenabdeckung übereinstimmt .
Achtung! Das Drehen der Kurbelwelle gegen den Uhrzeigersinn ist nicht zulässig.
In diesem Fall müssen die Nockenwellennocken des 1. Zylinders und die Markierungen auf den Nockenwellenrädern gemäß der Abbildung lokalisiert werden
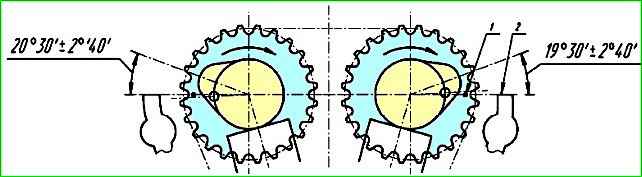
Wenn sich die Spitzen der Nocken und Markierungen nach innen befinden, muss die Kurbelwelle um eine weitere Umdrehung gedreht werden.
Die präzise Montage des Kolbens des 1. Zylinders am oberen Totpunkt kann mithilfe einer Messuhr erfolgen, die im Zündkerzenloch des 1. Zylinders installiert und befestigt wird.
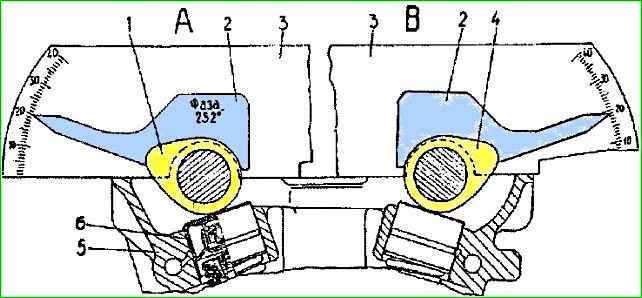
7. Installieren Sie den Winkelmesser 3 (Abbildung 6) hinter dem ersten Nocken der Einlassnockenwelle – Ansicht „A“, und platzieren Sie ihn zwischen dem Nocken und der Nockenwellenhalterungsabdeckung.
Drücken Sie den Winkelmesser 3 an die obere Ebene des Zylinderkopfs 5, befestigen Sie die Schablone 2 und drücken Sie sie fest an die Oberfläche des ersten Nockens.
Gleichzeitig Die Schablonenmarkierung sollte sich auf der Winkelmessermarkierung 20˚30′ ± 2˚40′ befinden.
Beim Messen muss der vordere Kettenzweig im Bereich des oberen Dämpfers (zwischen den Nockenwellenrädern) gespannt und in diesem Zustand gehalten werden, indem die Einlassnockenwelle mit einem 27er Schraubenschlüssel mithilfe des Vierkants entgegen dem Uhrzeigersinn gedreht wird Wellenkörper.
In diesem Fall ist das Drehen der Auslassnockenwelle nicht erlaubt.
Überprüfen Sie auf die gleiche Weise die Winkelposition des ersten Nockens der Auslassnockenwelle – Ansicht „B“.
Der Pfeil der Vorlage sollte auf die Winkelmessermarkierung 19°30′±2°40′ zeigen.
Beim Messen muss der Antriebsstrang der Kette im Bereich des mittleren Dämpfers (zwischen dem Nockenwellenrad und dem Antriebsrad der Zwischenwelle) gespannt und durch Drehen der Auslassnockenwelle gegen den Uhrzeigersinn in diesem Zustand gehalten werden Einen 27er Schraubenschlüssel am Vierkant am Wellenkörper anbringen.
In diesem Fall ist das Drehen der Zwischen- und Kurbelwelle nicht erlaubt.
Mit diesen Werten der Winkelstellung der ersten Nockenwellennocken wird die beste technische und wirtschaftliche Leistung des Motors erreicht.
Wenn die Abweichungen in der Winkelposition der Nockenwellen die zulässigen ±2°40′ überschreiten, ist eine Anpassung der Ventilsteuerzeiten erforderlich.
Dazu müssen Sie folgende Arbeiten an der Engine durchführen:
- 1. Entfernen Sie die vordere Zylinderkopfabdeckung, indem Sie die vier Schrauben (Schlüssel „12“) lösen.
- 2. Entfernen Sie den oberen hydraulischen Spanner (im Zylinderkopf), indem Sie die beiden Schrauben (Kopf „12“, Verlängerung und Knopf) lösen, mit denen die Abdeckung des hydraulischen Spanners befestigt ist, und entfernen Sie die Abdeckung mit der Schallschutzscheibe.
- 3. Entfernen Sie die obere und mittlere Kettenführung, indem Sie jeweils zwei Schrauben lösen (Schlüssel „6“ für Schrauben mit Innensechskant).
- 4. Entfernen Sie die Nockenwellenräder, indem Sie nacheinander ihre Befestigungsschrauben lösen (Schlüssel „12“), während Sie die Wellen mit einem Schlüssel „27“ am Vierkant am Nockenwellengehäuse festhalten.
Verhindern Sie, dass die von den Nockenwellenrädern entfernte Kette vom Zwischenwellenrad springt.
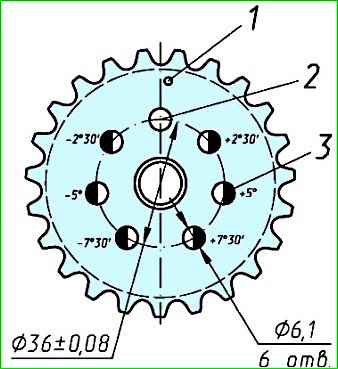
5. Bohren Sie mit der am Kettenrad installierten Bohrlehre in jedes Kettenrad sechs zusätzliche Löcher 3 (Abbildung 7) Ø 6,1 mm mit Winkelversätzen von 2°30', 5°00' und 7°30' von der Nennposition des Werkslochs 2, befindet sich entlang der Symmetrieachse einer der Hohlräume der Kettenradzähne.
Gleichzeitig sind drei zusätzliche Löcher, die von der Symmetrieachse der Zahnhöhle im Uhrzeigersinn versetzt sind, positiv, drei weitere, gegen den Uhrzeigersinn versetzt, sind negativ, wenn man das Kettenrad von der Seite der Markierung 1 aus betrachtet.
Wenn es beim Einstellen der Ventilsteuerzeiten erforderlich ist, die Nockenwelle(n) in ihrer Drehrichtung (im Uhrzeigersinn) zu drehen, müssen die Kettenräder in einem der zusätzlichen Löcher mit positivem Versatz montiert werden , befindet sich rechts vom Werksloch, wenn - gegen den Uhrzeigersinn, dann installieren Sie das/die Kettenrad(e) in einem der Löcher mit einem Minusversatz, das sich links vom Werksloch befindet.
Die Auswahl eines Lochs am Kettenrad mit dem erforderlichen Verschiebungswert erfolgt in Abhängigkeit von der Abweichung der Winkelposition der Nocke vom Nennwert.
Beim Einbau des Kettenrads in das zusätzliche Loch stimmt die werkseitige Ausrichtungsmarkierung 1 am Kettenrad nicht mit der oberen Ebene des Zylinderkopfs überein.
Beispiel
Betrachten Sie als Beispiel die Einstellung der Ventilsteuerung, wenn die Pfeilwerte der Vorlage 23°30′ für den Einlassventilnocken und 16°30′ für den Auslassventilnocken betragen und diese Winkelwerte die Nennwerte überschreiten für die Einlass- und Auslassnocken um 3°, was mehr als die zulässige Abweichung von ±2°40' ist.
Mit diesen Messwerten der Winkelposition der Nocken und unter Berücksichtigung der Tatsache, dass sich die Nockenwellen bei laufendem Motor im Uhrzeigersinn drehen, beobachtet man von der Seite der Kurbelwellenriemenscheibe aus den Beginn des Öffnens der Einlass- und Auslassventile treten mit einer gewissen Abweichung gegenüber den Werkswerten der Ventilsteuerung auf.
Um die Phasen einzustellen, ist es in diesem Fall notwendig, die Nockenwellen gegen den Uhrzeigersinn zu drehen und beim Einbau der Kettenräder ein zusätzliches Loch mit einem Minus-Winkelversatz mit einem Versatzwert von 2°30' zu verwenden (das erste Loch befindet sich). links vom Werksloch).
Setzen Sie die Arbeit in der folgenden Reihenfolge fort:
- 1. Mit einem 27-mm-Schlüssel drehen und die Auslassnockenwelle so einbauen, dass der Pfeil auf der Schablone steht lag gegenüber der Winkelmessermarkierung 19°30’.
- 2. Werfen Sie die Kette über das Kettenrad und richten Sie ihr erstes Zubehörloch, das sich links vom Werksloch befindet, so aus, dass es sich vor dem Nockenwellenstift und dem Antriebszweig der Kette (im Bereich der mittleren Führung) befindet ) ist gespannt.
Um das Kettenrad am Nockenwellenflansch und -stift anzubringen, drehen Sie die Nockenwelle mit dem Vierkantschlüssel leicht im Uhrzeigersinn.
Drehen Sie nach dem Einbau des Kettenrads die Nockenwelle gegen den Uhrzeigersinn, um den Antriebszweig der Kette zu spannen, während der Pfeil der auf der Nocke installierten Schablone 19°30’±2°40’ anzeigen sollte.
- 3. Installieren Sie die Einlassnockenwelle so, dass der Schablonenpfeil gegenüber der Winkelmessermarkierung 20°30’ liegt.
- 4. Montieren Sie das Kettenrad auf der Einlassnockenwelle auf die gleiche Weise wie das Auslassnockenwellenrad und verwenden Sie dabei das gleiche zusätzliche Loch.
In diesem Fall sollte bei gespanntem Vorderstrang der Kette (im Bereich des oberen Dämpfers) der Pfeil der auf der Nocke angebrachten Schablone 20˚30′±2˚40′ zeigen.
- 5. Ziehen Sie die Befestigungsschrauben des Kettenrads (Pos. „12“) vor.
- 6. Zerlegen und montieren Sie den hydraulischen Spanner („laden“), installieren Sie ihn im Loch im Zylinderkopf, schließen Sie den Deckel, ziehen Sie die Deckelschrauben fest und schrauben Sie den Stopfen vom Deckel ab.
- 7. Drücken Sie den hydraulischen Spanner mit einer Metallstange oder einem Schraubendreher durch das Loch in der Abdeckung des hydraulischen Spanners, bewegen Sie ihn ganz und lassen Sie ihn dann los. Der hydraulische Spanner „entlädt“ sich, wenn sich der Sicherungsring am Kolben vom hydraulischen Spanner löst Körper und ermöglicht die Bewegung des Kolbens und des Gehäuses unter der Wirkung der Feder.
Der Körper bewegt sich bis zum Deckel und die Kette wird über den Spannhebel gespannt.
- 8. Schrauben Sie den Stopfen in die Abdeckung des hydraulischen Spanners, nachdem Sie zuvor Stopper - 6 Dichtmittel auf das Gewinde des Stopfens aufgetragen haben.
- 9. Überprüfen Sie die korrekte Einstellung der Ventilsteuerung, indem Sie die Kurbelwelle zwei Umdrehungen in Drehrichtung drehen und die Markierungen auf der Dämpferscheibe und der Kettenabdeckung ausrichten.
Überprüfen Sie dies mit einem Winkelmesser und einer Nockenschablone, wie oben beschrieben. Der Pfeil der am Einlassnocken angebrachten Schablone sollte 20°30’±2°40’ zeigen, und am Auslassnocken 19°30’±2°40’.
Wenn diese Bedingung nicht erfüllt ist, muss die Installation der Ventilsteuerung wiederholt werden.
- 10. Schrauben Sie die Schrauben, mit denen die Nockenwellenräder befestigt sind, ein und ziehen Sie sie mit einem endgültigen Drehmoment von 56–62 Nm (5,6–6,2 kgf·m) fest.
- 11. Installieren Sie die oberen und mittleren Kettenführungen, indem Sie die Befestigungsschrauben eindrehen und mit einem Drehmoment von 20–25 Nm (2,0–2,5 kgf·m) anziehen (Schlüssel „6“ für Schrauben mit Innensechskant, Drehmomentschlüssel mit Kopf „6“).
Tragen Sie vorab Stopor-6-Dichtmittel auf die Schrauben auf, mit denen die Dämpfer befestigt sind.
- 12. Bauen Sie den Motor in umgekehrter Reihenfolge wie beim Zerlegen wieder zusammen
Nach dem Einstellen der Ventilsteuerzeiten sollte der Motor wie am Schnürchen laufen.