Kolben werden aus einer Aluminiumlegierung mit hohem Siliziumgehalt gegossen und wärmebehandelt
Der Kolbenkopf ist zylindrisch mit flachem Boden.
Auf der zylindrischen Oberfläche des Kopfes sind drei Nuten eingearbeitet, in den oberen beiden sind Kompressionsringe und unten ein Ölabstreifer installiert.
Die Nut für den Ölabstreifring ist auf beiden Seiten geschlitzt, um eine Überhitzung der Reibflächen des Kolbenschafts durch die vom Kolbenboden kommende Hitze zu verhindern
Die gleichen Schlitze transportieren Öl in das Kurbelgehäuse des Motors, das vom Ölabstreifring entfernt wird
Unter der Nut für den Ölabstreifring befindet sich eine Fase und darauf befinden sich auf beiden Seiten zwei Löcher, die auch zum Ablassen des Öls dienen, das sich unter dem Ölabstreifring ansammelt.
Der Kolbenschaft ist im Querschnitt oval und im Längsschnitt tonnenförmig.
Die Hauptachse des Ovals liegt in einer Ebene senkrecht zur Kolbenbolzenachse.
Die Ovalität des Kolbens beträgt 0,39–0,43 mm.
Der größte Durchmesser des Kolbenschafts liegt 8 mm unterhalb der Kolbenbolzenachse.
Der Durchmesser der Schürze nimmt sowohl nach unten als auch in die entgegengesetzte Richtung gleichmäßig ab, die maximale Durchmesserverringerung an der Kante der Fase unter der unteren Nut beträgt 0,034–0,064 mm, an der Unterkante des tragenden Teils der Rock - 0,050-0,080 mm.
Die Achse des Lochs für den Kolbenbolzen ist von der Mittelebene um 1,5 mm nach rechts (entlang der Fahrzeugrichtung) verschoben, um das Geräusch zu reduzieren, das beim Verschieben des Kolbens von einer Wand der Laufbuchse zur anderen entsteht beim Ändern der Bewegungsrichtung des Kolbens (oben - unten).
Zwischen der unteren Nut und dem Loch für den Kolbenbolzen ist in den Kolbenkörper ein Stahl-Thermostateinsatz eingegossen, der dazu dient, die Verformung des Kolbens beim Erhitzen auf Betriebstemperatur zu reduzieren und die anfänglichen Einbauspalte bei der Montage zu verringern
Kolben werden in Hülsen derselben Größengruppe mit einem Spalt von 0,024–0,048 mm eingebaut
Um das erforderliche Spiel sicherzustellen, sind die Kolben und Laufbuchsen (nach Durchmesser) in fünf Gruppen unterteilt, die durch den entsprechenden Buchstaben gekennzeichnet sind, der auf dem Kolbenboden eingeprägt und auf der Außenfläche, dem unteren Teil der Laufbuchse, angebracht ist.
Um das Einlaufen zu verbessern, wird die Kolbenoberfläche (elektrolytisch) mit einer 0,001–0,002 mm dicken Zinnschicht beschichtet.
Damit Kolben ordnungsgemäß funktionieren, müssen sie in einer genau definierten Position in den Zylinder eingebaut werden.
Dazu befindet sich auf einer der Kolbennaben die Aufschrift „FRONT“, laut dieser Aufschrift muss der Kolben mit der angezeigten Seite zur Vorderseite des Motors zeigen
Größengruppen für den ZMZ-4063-Motor
Gruppe „A“ (Wert):
- - Kolbendurchmesser (Schürze) – 92.000–91.988 mm;
- - Zylinderdurchmesser - 92,036-93,024 mm
Gruppe „B“ (Nominalwert):
- - Kolbendurchmesser (Schürze) – 92,012–92,000 mm;
- - Zylinderdurchmesser - 92,048-92,036 mm
Gruppe „B“ (Nominalwert):
- - Kolbendurchmesser (Schürze) – 92,024–92,012 mm;
- - Zylinderdurchmesser - 92,060-92,048 mm
Gruppe „G“ (Nominalwert):
- - Kolbendurchmesser (Schürze) – 92,036–92,024 mm;
- - Zylinderdurchmesser - 92,072-92,060 mm
Gruppe „D“ (Wert):
- - Kolbendurchmesser (Schürze) – 92,048–92,036 mm;
- - Zylinderdurchmesser - 92,084-92,072 mm
Gruppe „A“ (Reparaturvergrößerung 0,5):
- - Kolbendurchmesser (Schürze) – 92.500–91.488 mm;
- - Zylinderdurchmesser - 92,536-92,524 mm
Gruppe „B“ (Reparaturvergrößerung 0,5):
- - Kolbendurchmesser (Schürze) – 92,512–92,500 mm;
- - Zylinderdurchmesser - 92,548-92,536 mm
Gruppe „B“ (Reparaturerhöhung 0,5):
- - Kolbendurchmesser (Schürze) – 92,524–92,512 mm;
- - Zylinderdurchmesser - 92,560-92,548 mm
Gruppe „G“ (Reparaturvergrößerung 0,5):
- - Kolbendurchmesser (Schürze) – 92,536–92,524 mm;
- - Zylinderdurchmesser - 92,572-92,560 mm
Gruppe „D“ (Reparaturvergrößerung 0,5):
- - Kolbendurchmesser (Schürze) – 92,548–92,536 mm;
- - Zylinderdurchmesser - 92,584-92,572 mm
Gruppe „A“ (Reparaturvergrößerung 1,0):
- - Kolbendurchmesser (Schürze) – 93.000–92.988 mm;
- - Zylinderdurchmesser - 93,036-93,024 mm
Gruppe „B“ (Reparaturvergrößerung 1,0):
- - Kolbendurchmesser (Schürze) – 93,012–93,000 mm;
- - Zylinderdurchmesser - 93,048-93,036 mm
Gruppe „B“ (Reparaturerhöhung 1,0):
- - Kolbendurchmesser (Schürze) – 93,024–93,012 mm;
- - Zylinderdurchmesser - 93,060-93,048 mm
Gruppe „G“ (Reparaturvergrößerung 1,0):
- - Kolbendurchmesser (Schürze) – 93,096–93,024 mm;
- - Zylinderdurchmesser - 93,072-93,060 mm
Gruppe „D“ (Reparaturvergrößerung 1,0):
- - Kolbendurchmesser (Schürze) – 93,048–93,036 mm;
- - Zylinderdurchmesser - 93,084-93,072 mm
Kolbenringe
Kompressionsringe sind aus Gusseisen gegossen, der obere besteht aus hochfestem Gusseisen, das hat o hohe Elastizität, die untere ist aus Grauguss
Der obere Kompressionsring arbeitet unter härtesten Bedingungen bei hohen Temperaturen und Drücken sowie mangelnder Schmierung.
Um die Verschleißfestigkeit zu erhöhen, ist die an den Zylinder angrenzende Außenfläche mit einer Chromschicht überzogen.
Die Chromschicht erhöht die Lebensdauer des Oberrings deutlich. Dies trägt auch dazu bei, die Lebensdauer des unteren Zylinderrings zu erhöhen.
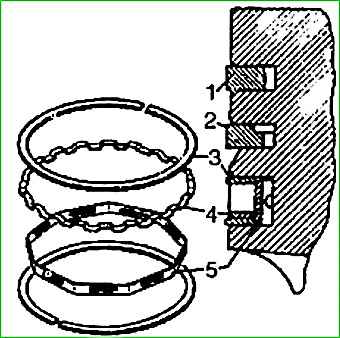
Die äußere zylindrische Oberfläche des unteren Kompressionsrings ist mit einer 0,006–0,012 mm dicken Zinnschicht beschichtet (oder die gesamte Oberfläche des Rings ist mit einer Phosphatbeschichtung versehen), was das Einlaufen verbessert.
Auf der inneren zylindrischen Oberfläche des unteren Kompressionsrings befindet sich eine Aussparung, dank der neue, in den Zylinder eingebaute Ringe leicht herausdrehen und nur mit der Kante mit dem Zylinder in Kontakt kommen
Dadurch wird das Einlaufen der Ringe in die Zylinderbohrung beschleunigt und verbessert.
Der Ring muss mit der Aussparung nach oben auf dem Kolben montiert werden; ein Verstoß gegen diese Bedingung führt zu einem starken Anstieg des Ölverbrauchs und der Motorrauchentwicklung
Der obere Ring hat keine Nut
Ölring – montiert, vier- oder dreiteilig.
Der Vier-Elemente-Ring besteht aus zwei ringförmigen Stahlscheiben 3 und zwei Stahlexpandern: axial 4 und radial 5
Der dreiteilige Ölabstreifring besteht aus zwei Ringscheiben aus Stahl und einem Doppelfunktions-Expander aus Stahl
Die Arbeitszylinderfläche (angrenzend an den Zylinder) der Ringscheiben ist mit einer 0,080–0,130 mm dicken Chromschicht überzogen.
Höhe der Kompressionsringe – 2 mm, Ölabstreifer-Baugruppe – 4,9 mm Ringverriegelung – gerade
Schwimmende Kolbenbolzen (sie sind weder am Kolben noch an der Pleuelstange befestigt) werden durch Kaltstauchen aus niedriglegiertem Stahl hergestellt.
Die Außenfläche des Fingers ist bis zu einer Tiefe von 1–1,5 mm mit Kohlenstoff gesättigt und durch Hochfrequenzerwärmung auf eine Härte von HRC 59–66 gehärtet.
Der Außendurchmesser des Stifts beträgt 25 mm
Um ein Klopfen der Finger zu verhindern, sind sie mit dem durch die Schmierungsbedingungen zulässigen Mindestspiel auf die Kolben abgestimmt
Da die lineare Ausdehnung des Kolbenmaterials etwa doppelt so groß ist wie die des Bolzens, passt der Bolzen bei Raumtemperatur mit Übermaß in die Löcher der Kolbennaben
Der Bolzen wird mit einem Spalt von 0,0045 bis 0,0095 mm zur Pleuelstange gewählt
Zur leichteren Auswahl sind Bolzen, Pleuel und Kolben in Größengruppen eingeteilt.
Größengruppen von Kolben, Pleueln und Fingern von Motoren der ZMZ-406-Familie
Fingerdurchmesser – 22,0000–21,9975 mm:
- - Löcher im oberen Kopf der Pleuelstange – 22,0070–22,0045 mm;
- - Löcher in der Kolbennabe – 22,0000–21,9975 mm;
- - Markierungen für Bolzen, Pleuel und Kolben – weiß;
- - Kolbenmarkierung „I“
Fingerdurchmesser – 21,9975–21,9950 mm:
- - Löcher im oberen Kopf der Pleuelstange – 22,0045–22,0020 mm;
- - Löcher in der Kolbennabe – 21,9975–21,9950 mm;
- - Markierung von Bolzen, Pleuel und Kolben – grün;
- - Kolbenmarkierung „II“
Fingerdurchmesser – 21,9950–21,9925 mm:
- - Löcher im oberen Kopf der Pleuelstange – 22,0020–21,9995 mm;
- - Löcher in der Kolbennabe – 21,9950–21,9925 mm;
- - Markierung des Bolzens, der Pleuelstange und des Kolbens – gelb;
- - Kolbenmarkierung „III“
Fingerdurchmesser – 21,9925–21,9900 mm:
- - Löcher im oberen Kopf der Pleuelstange – 21,9995–21,9970 mm;
- - Löcher in der Kolbennabe – 21,9925–21,9900 mm;
- - Markierung des Bolzens, der Pleuelstange und des Kolbens – rot;
- - Kolbenmarkierung „IV“
Größengruppen von Kolben, Pleueln und Fingern von Motoren der ZMZ-405-Familie
Fingerdurchmesser – 25,0000–24,9975 mm:
- - Löcher im oberen Kopf der Pleuelstange – 25,0070–25,0045 mm;
- - Löcher in der Kolbennabe – 25,0000–24,9975 mm;
- - Markierungen für Bolzen, Pleuel und Kolben – weiß;
- - Kolbenmarkierung „I“
Fingerdurchmesser – 24,9975–24,9950 mm:
- - Löcher im oberen Kopf der Pleuelstange – 25,0045–25,0020 mm;
- - Löcher in der Kolbennabe – 24,9975–24,9950 mm;
- - Markierung von Bolzen, Pleuel und Kolben – grün;
- - Kolbenmarkierung „II“
Fingerdurchmesser – 24,9950–24,9925 mm:
- - Löcher im oberen Kopf der Pleuelstange – 25,0020–24,9995 mm;
- - Löcher in der Kolbennabe – 24,9950–24,9925 mm;
- - Markierung des Bolzens, der Pleuelstange und des Kolbens – gelb;
- - Kolbenmarkierung „III“
Fingerdurchmesser – 24,9925–24,9900 mm:
- - Löcher im oberen Kopf Pleuel - 24,9995-24,9970 mm;
- - Löcher in der Kolbennabe – 24,9925–24,9900 mm;
- - Markierung des Bolzens, der Pleuelstange und des Kolbens – rot;
- - Kolbenmarkierung „IV“
Der Bolzen wird durch zwei Sicherungsringe aus rundem Federdraht mit einem Durchmesser von 2 mm im Kolben gehalten. Die Ringe haben eine seitlich gebogene Ranke.
Die Sicherungsringe werden mit einer Zange so montiert, dass die Ranke nach außen zeigt
Pleuelstangen bestehen aus geschmiedetem Stahl mit einem Stab mit I-Profil. In den Kolbenboden des Pleuels ist eine dünnwandige Buchse aus Zinnbronze eingepresst.
Der Kurbelkopf der Pleuelstange ist abnehmbar.
Der Kurbelkopfdeckel wird mit zwei Schrauben mit geschliffenem Sitz an der Pleuelstange befestigt.
Die Kopfschrauben und Pleuelschraubenmuttern bestehen aus legiertem Stahl und sind wärmebehandelt.
Die Muttern der Pleuelschrauben werden mit einem Drehmoment von 68–75 Nm (6,8–7,5 kgf-m) angezogen und mit Dichtmittel gesichert.
Die Pleueldeckel werden zusammen mit der Pleuelstange verarbeitet und können daher nicht von einer Pleuelstange zur anderen verschoben werden.
Um möglichen Fehlern vorzubeugen, sind die Seriennummern der Zylinder auf der Pleuelstange und auf der Abdeckung des Bolzenauges eingeprägt. Sie sollten sich auf einer Seite befinden.
Außerdem müssen die Aussparungen in Deckel und Verbindungsstange für die Rastvorsprünge der Laufbuchsen ebenfalls auf einer Seite liegen.
In der Pleuelstange in der Nähe des Kurbelkopfes befindet sich ein Loch mit einem Durchmesser von 1,5 mm, durch das der Zylinderspiegel geschmiert wird. Dieses Loch sollte auf die rechte Seite des Motors gerichtet sein, also in die Richtung entgegengesetzt zur Nockenwelle.
Bei korrekter Montage sollten die auf dem mittleren Flansch der Pleuelstange eingestanzte Zahl „24“ sowie der Vorsprung auf der Pleuelkappe zur Vorderseite des Motors zeigen.
Um das dynamische Gleichgewicht des Motors zu gewährleisten, darf die Gesamtmasse von Kolben, Kolbenbolzen, Ringen und Pleuel im Motor einen Unterschied zwischen den Zylindern von nicht mehr als 12 g aufweisen, was durch die Auswahl der Teile gewährleistet wird das entsprechende Gewicht.
Im Detail kann der Gewichtsunterschied betragen: Kolben – 4 g, Pleuel – 18 g, Kolbenbolzen – 2 g.
Um den oben genannten Unterschied in der Masse der Teile in einem Motor (12 g) sicherzustellen, werden die Pleuel in vier Gewichtsgruppen eingeteilt und müssen für einen Motor mit einem Unterschied von nicht mehr als 5 g ausgewählt werden.
Die Kurbelwelle ist aus hochfestem Gusseisen gegossen, hat fünf Lager, montiert mit Schwungrad und Kupplung, dynamisch ausgewuchtet, zulässige Unwucht - nicht mehr als 35 g cm).
Der Durchmesser der Hauptzapfen beträgt 64 mm, der Durchmesser der Pleuelzapfen beträgt 58 mm.
Die Pleuelzapfen sind hohl.
Die Hohlräume in den Pleuelzapfen sind mit Gewindestopfen verschlossen und dienen der zusätzlichen Reinigung des in die Pleuelzapfen eintretenden Öls.
Unter dem Einfluss der Zentrifugalkräfte, die beim Drehen der Kurbelwelle entstehen, lagern sich im Öl enthaltene Metallpartikel von Verschleißprodukten in den Hohlräumen der Pleuelzapfen ab.
Öl wird den Kurbelzapfenhohlräumen durch die Löcher in den Wellenwangen aus der Ringnut an den Hauptlagerbuchsen der Kurbelwelle zugeführt.
Öl gelangt von der Ölleitung durch Kanäle in den Blocktrennwänden zu den Hauptzapfen
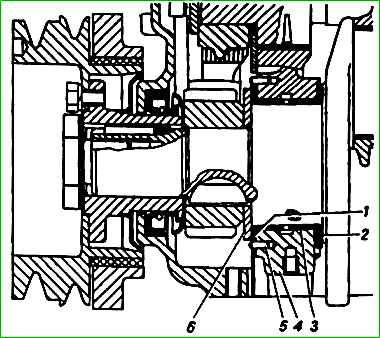
Die axiale Bewegung der Kurbelwelle wird durch zwei Druckscheiben 1 und 2 aus Stahl-Aluminium begrenzt, die sich auf beiden Seiten des vorderen Hauptlagers befinden.
Die vordere Unterlegscheibe 1 mit Gleitschicht ist der Stahlanlaufscheibe 6 auf der Kurbelwelle zugewandt, die hintere Unterlegscheibe 2 ist der Kurbelwellenwange zugewandt.
Die vordere Unterlegscheibe wird durch zwei Stifte 5, die in den Block und den Hauptlagerdeckel eingepresst sind, am Drehen gehindert.
Die hervorstehenden Enden der Stifte passen in die Nuten der Unterlegscheibe.
Die hintere Unterlegscheibe wird durch ihren Vorsprung, der in eine Nut am hinteren Ende des Hauptlagerdeckels passt, am Drehen gehindert.
Das Axialspiel beträgt 0,125–0,325 mm.
Am vorderen Ende der Kurbelwelle sind eine Anlaufscheibe aus Stahl, Nockenwellenantriebsräder, ein Ölabweiser und eine Kurbelwellenriemenscheibennabe auf Keilwellen montiert.
Alle diese Teile werden mit einer Schraube befestigt, die in das vordere Ende der Kurbelwelle eingeschraubt wird.
Die Keilnut in der Riemenscheibennabe ist mit einem Gummistopfen verschlossen.
Eine Kurbelwellenriemenscheibe ist mit sechs Schrauben an der Nabe befestigt, von der aus der Lüfter, das Wasserpumpenlaufrad und die Generatorriemenscheibe über zwei Riemen angetrieben werden.
Auf der Riemenscheibe ist eine spezielle Vorrichtung montiert – ein Dämpfer, der dazu dient, Torsionsschwingungen der Kurbelwelle zu dämpfen, wodurch Geräusche reduziert und die Betriebsbedingungen der Nockenwellenantriebsräder verbessert werden.
Der Dämpfer besteht aus einer Gusseisenscheibe, die durch ein Gummiband gepresst wird (Gummi-)Dichtung am zylindrischen Vorsprung der Kurbelwellenriemenscheibe
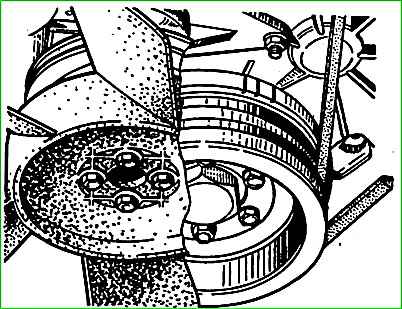
Es gibt eine Markierung auf der Kurbelwellenriemenscheibe und drei Markierungen auf der Dämpferscheibe (Abb. 3), die zur Bestimmung des oberen Totpunkts (OT) und zur Einstellung der Zündung dienen.
Die Markierung auf der Riemenscheibe und die dritte Markierung auf der Dämpferscheibe müssen einander gegenüberliegen. Eine gegenseitige Vermischung der Markierungen weist auf einen Ausfall des Dämpfers hin.
Wenn die Anzeigerippe am Steuerraddeckel mit der dritten Markierung in Drehrichtung auf der Dämpferscheibe ausgerichtet ist, befinden sich die Kolben des ersten und vierten Zylinders am oberen Totpunkt.
Die zweite Markierung entspricht der 5-Grad-Position. auf OT und dient zusammen mit der dritten Markierung zur Einstellung der Zündung bei stehendem Motor.
Die erste Markierung entspricht der Position 12 Grad vor OT und dient zusammen mit der zweiten und dritten Markierung zur Kontrolle des korrekten Einbaus der Zündung bei laufendem Motor.
Das vordere Ende der Kurbelwelle ist mit einer Gummidichtung und einem in den Nockenwellendeckel eingepressten Ölabweiser abgedichtet.
Der Ölabweiser verfügt über einen Flansch, der das an der Wand der Abdeckung herunterfließende Öl ableitet. Um die Bedienung der Manschette zu erleichtern, ist davor an der Kurbelwelle ein weiterer Ölabweiser angebracht.
Eine zuverlässige Funktion der Manschette nach dem Zusammenbau wird durch eine gute Ausrichtung der Steuerradabdeckung gewährleistet.
Das hintere Ende der Kurbelwelle ist mit einer Packung aus Asbestschnur abgedichtet, die mit einem Gleitmittel imprägniert und mit Graphit beschichtet ist.
Die Packung wird in den Nuten des Zylinderblocks und einem speziellen Halter platziert, der mit zwei Bolzen am Block befestigt wird
Auf dem Kurbelwellenzapfen unter der Packung befindet sich eine Mikroschraube, und vor der Packung befindet sich eine Kante, die dazu dient, Öl aus dem Dichtungsbereich zu schleudern.
Die Gelenke des Halters sind mit L-förmigen Gummidichtungen abgedichtet.
Am hinteren Ende der Kurbelwelle befindet sich eine gebohrte Buchse zum Einbau des Kugellagers der Getriebeeingangswelle
Das Schwungrad ist aus Grauguss gegossen. Es wird mit vier Erdungsschrauben am Flansch am hinteren Ende der Kurbelwelle befestigt
Das Anzugsdrehmoment der Schraubenmuttern beträgt 76–83 Nm (7,6–8,3 kgf·m). Die Muttern werden mit einem Biegeblech gesichert.
Ein Zahnkranz wird auf das Schwungrad gepresst, um den Motor mit einem Anlasser zu starten. Vor der Montage mit der Kurbelwelle wird das Schwungrad statisch ausgewuchtet.