Зняття ТНВД
Для зняття паливного насоса високого тиску:
- - від'єднайте тросики ручного керування важелем зупинки двигуна та важелем керування регулятором, тягу керування подачею палива, трубопроводи підведення палива до насоса, відвідний, дренажний трубопроводи та трубопровід від фільтра тонкого очищення палива, трубку підведення олії до насоса, масловідвідну
- - викрутіть два болти веденої напівмуфти (для вивертання болтів переведіть їх у зручне положення, провернувши колінчастий вал ломиком за отвори на маховику через люк картера зчеплення);
- - від'єднайте трубопроводи, що підводять паливо до штифтових свічок, трубопроводи високого тиску (зніміть їх), трубку підведення повітря до клапана допоміжної гальмівної системи;
- - викрутіть чотири болти кріплення паливного насоса;
- - зніміть насос.
Для встановлення паливного насоса високого тиску:
- - переверніть колінчастий вал до положення, що відповідає початку впорскування палива в першому циліндрі (фіксатор знаходиться в зачепленні з маховиком); при цьому шпонковий паз ведучої напівмуфти приводу повинен бути:
- - внизу для двигунів мод. 740.11-240 та мод. 740.14-300;
- - у горизонтальному положенні ліворуч, якщо дивитися з боку маховика для двигуна мод. 740.13-260;
Встановіть насос на двигун, сумісивши:
- - мітки на корпусі насоса та муфті випередження впорскування палива, для двигунів мод. 740.11-240 та мод. 740.14-300;
- - настановну мітку на фланці веденої напівмуфти з покажчиком на корпусі ТНВД для двигуна мод. 740.13-260;
- - затягніть болти кріплення насоса, як показано на малюнку;
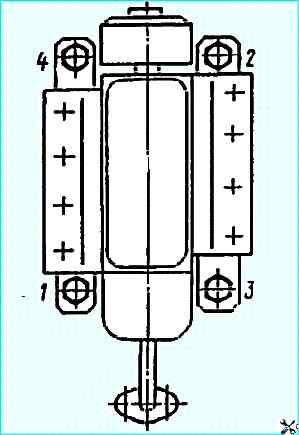
- - не порушуючи взаємного розташування міток, затягніть верхній болт веденої напівмуфти приводу, переставте фіксатор у дрібний паз, переверніть колінчастий вал на один оберт і затягніть другий болт веденої напівмуфти;
- - встановіть кришку люка картера зчеплення;
- - під'єднайте трубопроводи високого тиску, трубку підведення масла до ТНВД і трубу, що відводить трубку, трубку підведення повітря до клапана допоміжної гальмівної системи, трубопроводи низького тиску, тягу управління подачею палива, тросики ручного управління важелем зупинки і важелем управління регулятором.
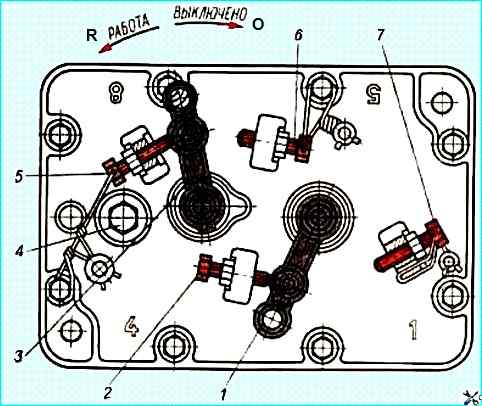
Після встановлення паливного насоса високого тиску пустіть двигун і болтом 2 (мал. Кришка регулятора ТНВД) відрегулюйте мінімальну частоту обертання холостого ходу, яка має бути 600±50 хв -1.
Під час ремонту паливного насоса високого тиску:
- - корпус насоса, що має тріщини та зриви основних різьблень, замініть;
- - до дефектів втулки плунжера віднесіть сколювання та фарбування металу у отворів, задираки, подряпини, знос робочої поверхні, збільшення діаметра впускного та відсічного вікон, тріщини та ослаблення в місцях посадки (скелювання, фарбування металу та тріщини є несправними).
Зношування робочої поверхні втулки плунжера виміряйте з точністю до 0,001 мм, овальність, конусність і збільшення отвору втулки мікрометричним або індикаторним приладом для вимірювання внутрішніх поверхонь з ціною поділу до 0,001 мм і конусними калібрами;
- до дефектів плунжера віднесіть фарбування металу та подряпини на робочій поверхні, знос робочої поверхні та тріщини.
Спотворення геометрії плунжера виявите мініметром з точністю до 0,001 мм при установці його стрілки на нуль за вихідним зразком або калібром у вигляді конусної втулки;
- величину зазору в плунжерній парі перевірте на опресувальному стенді з вантажем, що падає.
Перед випробуванням деталі пари ретельно промийте у профільтрованому дизельному паливі.
Плунжерну пару встановіть у гніздо стенду, плунжер - у положення максимальної подачі.
Надплунжерний простір заповніть профільтрованим дизельним паливом.
Встановіть на торець втулки ущільнювальну пластину, затиснувши її гвинтом, потім відпустіть клямку вантажу. Під дією його через зазор у парі поступово почне видавлюватися паливом більше зазор, тим швидше.
Величина навантаження на плунжер має відповідати величині тиску палива 19,1-20,1 МПа (195-205 кгс/см 2).
Повне підняття плунжера до моменту відсічення під дією навантаження, що супроводжується вичавлюванням палива через зазор між втулкою та плунжером, має відбуватися не менше ніж за 20 с.
Встановіть плунжерну пару з часом підняття плунжера до відсічки більше 40 с, змочену профільтрованим дизельним паливом, у вертикальне положення на торець втулки, попередньо підклавши аркуш чистого паперу.
Після п'ятихвилинної витримки при піднятті пари за хвостовик плунжера втулка повинна опускатися з плунжера під дією власної маси;
- штовхач плунжера встановлений в отвір корпусу насоса із зазором 0,025-0,075 мм.
Припустимий зазор при експлуатації 0,2 мм. Виміряйте зовнішній діаметр штовхача плунжера мікрометром або скобою;
- в складальній одиниці ролик штовхача - втулка ролика - вісь ролика основним дефектом є знос поверхонь, що сполучаються.
Сумарний зазор у парі 0,022-0,087 мм, гранично допустимий 0,3 мм (заміряйте індикаторною головкою).
Якщо знос перевищує вказану межу, штовхач розберіть і відремонтуйте, при цьому виміряйте окремо.
Горально допустимий зазор при зношуванні поверхонь у з'єднанні вісь ролика - втулка ролика 0.12 мм, у з'єднанні втулка ролика - ролик штовхача 0.18 мм.
Зовнішні поверхні деталей заміряйте мікрометром, внутрішні - нутроміром з індикатором.
- на поверхні кулачкового валу не допускаються фарбування металу, задираки, зриви різьблення, сліди корозії.
Горально допустима висота профілю кулачка не менше 47.7 мм (висота профілю кулачка за КД 47.95-48.05 мм).
Виміри здійсніть скобою 47.7; діаметр шийок під внутрішні кільця підшипників повинен бути не менше 30.0 мм (по КД 30,002-30,011 мм), натяг по кромці ущільнюючої манжети - не менше 0.5 мм;
- на поверхні нагнітального клапана не допускаються тріщини, вм'ятини, сліди корозії.
Зношування клапана проявляється у втраті герметичності по ущільнювальному конусу, у заїданні клапана в сідлі.
Для виявлення дефектів використовуйте лупу десятикратного збільшення.
При втраті герметичності разом притріть сідло і клапан по конусу пастою ГОСТ 3647-71, при заїданні клапана в сідлі деталі промийте бензином або дизельним паливом.
Якщо заїдання не усувається, пару замініть;
- гранично допустимий зазор у сполученні палець важеля рейок - паз рейки 0,18 мм (КД 0,025-0,077 мм), гранично допустимий зазор у сполученні вісь повідця поворотної втулки - паз рейки паливного насоса 0,3 мм (по КД 0. - 0,183 мм).
Для вимірювання пазів використовуйте нутромір.
При ремонті регулятора частоти обертання:
- замініть верхню та задню кришки регулятора, якщо є тріщини на них.
При засміченні сітчастого масляного фільтра в задній кришці регулятора продуйте його стиснутим повітрям. Якщо фільтр має дефекти, замініть його.
Експлуатаційна витрата масла через фільтр має бути не менше 1,6 л/год при тиску 98,1-294 кПа (1-3 кгс/см 2);
- для визначення придатності до подальшої експлуатації державку вантажів регулятора в зборі з вантажами огляньте і виміряйте без розбирання, оскільки при випресуванні деталі можуть бути пошкоджені і порушиться спареність вантажів, які підібрані з різницею статичного моменту не більше 196 кПа (2 кгс/ див 2).
Часткове або повне розбирання складальної одиниці робіть тільки при зносі, що перевищує допустимий, або руйнуванні деталей.
Зазор між важелем пружини регулятора та віссю важеля, запресованої в корпусі насоса, не повинен перевищувати 0,3 мм
При ремонті насоса низького тиску та насоса передпускового прокачування палива:
- - насос низького тиску та насос передпускової прокачування палива замініть за наявності тріщин на корпусі, зламів, механічних пошкоджень, корозії, що веде до втрати рухливості деталей, що сполучаються;
- - при розбиранні та збиранні насоса низького тиску пам'ятайте, що поршень і корпус насоса є точно підібраною парою і розкомплектуванню не підлягає.
Розбирання та ремонт насос піддається тільки в тому випадку, якщо він не забезпечує необхідних характеристик;
- - особливу увагу зверніть на стан складальної одиниці шток - втулка насоса низького тиску, так як від величини зносу в поєднанні залежить кількість палива, що перетікається, в порожнину кулачкового валу.
Зазор у поєднанні не повинен перевищувати 0,012 мм.
Величину зазору перевірте, не виймаючи втулки з корпусу насоса, визначення часу падіння тиску повітря з 490 кПа (5 кгс/см 2) до 392 кПа (4 кгс/см 2) в акумуляторі об'ємом 30 см 3.
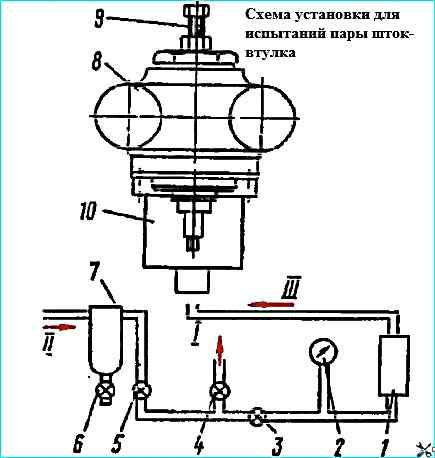
Схема установки для вимірювання щільності прецизійної складальної одиниці показана на малюнку.
Встановіть корпус 8 насоса в пристрій, заповніть акумулятор стисненим повітрям до тиску не менше 539 кПа (5,5 кгс/см 2), герметично відключіть його від магістралі стисненого повітря і заміряйте час протягом якого стане падіння в акумуляторі з 490 кПа (5 кгс/см 2) до 392 кПа (4 кгс/см 2).
Отриманий час порівняйте з аналогічними показаннями щільності еталонної прецизійної пари, що має зазор у парі 0.012 мм.
Пару замініть або відремонтуйте, якщо щільність у неї менша за еталонну.
Перевірку щільності пари можна зробити більш простим способом: через проміжок між штоком і втулкою пропустіть профільтроване дизельне паливо.
Об'єм палива, що просочився через зазор, не повинен перевищувати 1 см 3 протягом 20 хв.
Якщо складальна одиниця шток - втулка замінюється, поверхню різьблення та торець у корпусі насоса низького тиску очистіть від залишків клею.
Нову втулку штока встановіть у корпус насоса на клеї, складеному на основі епоксидної смоли.
Для забезпечення міцності та герметичності з'єднання очищені контактуючі поверхні корпусу насоса та втулки попередньо знежирте бензином Б-70.
Після затягування втулки штока з моментом 9,81 Нм (1 кгсм) перевірте легкість переміщення штока в ній. За потреби зменшіть момент затягування.
Під час випробування перевірте подачу насоса.
Установку для перевірки виготовте за схемою: паливний бак - фільтр грубого очищення палива - вакуумметр - паливопідкачувальний насос - манометр - мірний резервуар.
Елементи схеми з'єднайте прозорими трубопроводами з внутрішнім діаметром не менше 8 мм.
Для створення розрідження на вході в насос та протитиску на виході встановіть крани.
Перевірку проводьте на літньому дизельному паливі при температурі його 25-30° С, у відсутності повітря в системі переконайтеся в чистоті струменя палива в прозорих трубопроводах.
Насос повинен засмоктувати паливо з бака, встановленого на 1 м нижче насоса.
Подача насоса при частоті обертання кулачкового валу 1100-1300 хв -1, розрідженні біля вхідного штуцера 23 кПа (173 мм рт. ст.) та протитиску:
- - 80-100 кПа (0,8-1,0 кгс/см 2) має бути не менше 3 л/хв для двигунів мод. 740.11-240 та мод. 740.13-260;
- - 125 кПа (1,25 кгс/см 2) має бути не менше 3,5 л/хв для двигуна 740.14-300.
При повністю перекритому вихідному крані та частоті обертання кулачкового валу 1100—1300 хв-1 насос повинен створювати тиск не менше:
- - 400 кПа (4 кгс/см 2) - для двигунів мод. 740.11-240 та 740.13-260;
- - 600 кПа (6 кгс/см 2) - для двигуна 740.14-300.
При повністю перекритому вхідному крані та вказаній частоті обертання кулачкового валу мінімальне розрідження, створюване насосом, має бути:
- - 52 кПа (390 мм рт. ст.) – для двигунів мод. 740.11-240 та 740.13-260;
- - 70 кПа (525 мм рт. ст.) - для двигуна 740.14-300;
- - насос передпускового прокачування палива перевірте на стенді, що має схему: паливний бак - фільтр грубої очистки - паливний насос. Насос повинен подавати паливо з бака, встановленого нижче ручного насоса на 1 м.
Перевірте насос на герметичність, підводячи повітря під поршень при тиску 200-300 кПа (2-3 кгс/см 2) протягом 5-6 секунд з попереднім змочуванням порожнини дизельним паливом.
Для зняття автоматичної муфти випередження впорскування палива використовуйте пристрій.
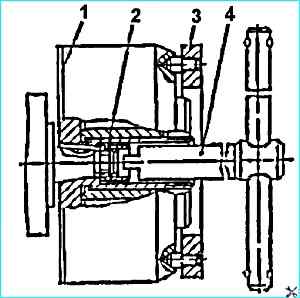
Спочатку відверніть гайку 2 (див. рис. Відвертання гайки кріплення муфти випередження впорскування палива) кріплення муфти.
Для цього вставте викрутку 4 у паз гайки та, утримуючи муфту 1 від обертання ключем 3, відверніть гайку.
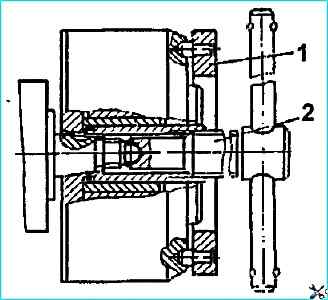
Потім, повертай вийміть у муфту знімач 2 (мал. Зняття муфти пристроєм), зніміть муфту.
Для розбирання муфти:
- викрутіть гвинти з корпусу та злийте масло:
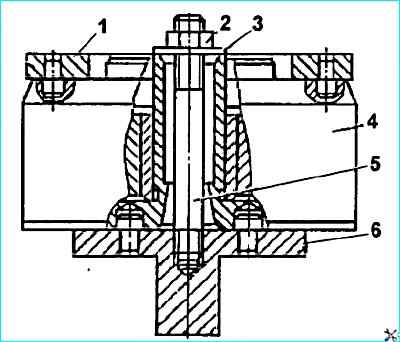
- - затисніть в настільні лещата підставку 6 (мал. Розбирання муфти) пристосування та встановіть на неї муфту, вверніть у підставку шпильку 5, встановіть шайбу 3 і затягніть гайкою 2;
- - ключем 1 відверніть корпус 5 (див. мал. Автоматична муфта випередження впорскування палива);
- - зніміть провідну напівмуфту 1 з проставками 12 , вантажі 11, пружини 8;
- - випресуйте манжети 4 та 2.
Враховуючи, що вантажі підібрані за статичним моментом, збережіть їхню спареність для подальшої установки.
Для складання муфти:
- - запресуйте манжету 4 в отвір провідної напівмуфти;
- - встановіть провідну напівмуфту оправкою на маточину веденою;
- - встановіть у склянки 7 регулювальні прокладки 6 та пружини 8, склянки із пружинами
- - в напрямні отвори вантажів, у яких вони повинні переміщатися вільно без заїдань.
У довільному положенні деталей муфти зазор між профільною поверхнею та проставкою повинен бути не більше 0,15 мм.
При зведених до упору поворотом провідної напівмуфти вантажах, один із зазорів повинен бути не більше 0,1 мм, інший - дорівнює нулю.
Відрегулюйте зазори підбором простовок:
- - запресуйте в корпус муфти врівень з внутрішньою торцевою поверхнею манжету 2;
- - встановіть у виточку веденої напівмуфти гумове кільце ущільнювача 14;
- - наверніть на ведену напівмуфту корпус і затягніть моментом 314-343 Нм (32-35 кгсм);
- - зачеканити в трьох місцях провідну напівмуфту.
Перед встановленням корпусу забезпечте рівні зазори між корпусом та склянками пружин при зведених до упору вантажах. Різниця проміжків повинна бути не більше 0,2 мм.
Після складання залийте в муфту моторне масло, що застосовується для двигуна.
Для розбирання форсунки використовуйте пристрій І801.20.000.
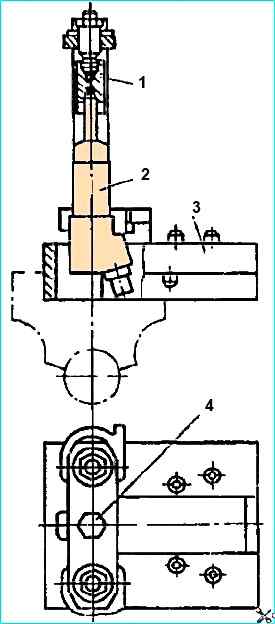
Затисніть станину 2 (мал. Розбирання форсунки) пристрою в лещатах, встановіть форсунку в паз станини розпилювачем вгору.
Повертаючи болт 4, відіжміть розпилювач форсунки упором 1, після чого ріжковим ключем відверніть гайку розпилювача.
Вивернувши болт 4. Вийміть форсунку з пристрою та розберіть на частини.
Пам'ятайте, що корпус та голка розпилювача підібрані парою і не підлягають розкомплектуванню. Гранично допустимий зазор між корпусом та голкою розпилювача 0,006 мм.
Збільшення ходу голки розпилювача не допускайте більше 0,4 мм, діаметр соплових отворів розпилювача не повинен перевищувати 0,38 мм.
Незадовільна робота форсунок викликається зменшенням тиску початку впорскування палива, що пояснюється зносом пов'язаних з пружиною деталей і усадкою пружини, тому висоту проставки форсунки не допускайте менше 8,89 мм (КД 8,9-9,0 мм).
При виявленні на проставці рисок та слідів корозії (використовуйте лупу з десятикратним збільшенням) деталь замініть.
До дефектів форсунки відносяться поломка пружини, засмічення та знос соплових отворів, заїдання голки та знос її ущільнювальної частини (викликає підтікання та погане розпилювання палива).
При необхідності обережно прочистіть соплові отвори розпилювача сталевим дротом діаметром 0,25 мм.
Нагар із зовнішньої поверхні розпилювача видаліть дерев'яним бруском, просоченим моторним маслом або латунною щіткою. Не застосовуйте гострі тверді предмети або наждачний папір.
Перед складанням корпус розпилювача та голку промийте бензином і змастіть профільтрованим дизельним паливом, після чого голка, висунута з корпусу на одну третину довжини напрямної поверхні, при нахилі розпилювача під кутом 45° повинна плавно (без заїдань) опуститися до упору під дією власної маси.
При збиранні форсунки гайку розпилювача затягуйте, віджавши розпилювач у пристосуванні І801.20.000.
Розміри деталей та допустиме зношування, мм
Муфта автоматична випередження впорскування палива
За КД /Припустимий
- Діаметр отвору у вантажі муфти 16,032-16,059 / 16,1
- Діаметр осі вантажу 15,982-16,000 / 15,86
- Зазор між віссю та вантажем 0,032-0,077 / 0,24
- Діаметр отвору проставки 16,032-16,059 / 16,1
- Діаметр пальця провідної напівмуфти 15,973-16,000 / 15,9
- Зазор між пальцем та отвором у проставці 0,032-0,086 / 0,2
Насос паливний високого тиску мод. 337-40
За КД /Припустимий
- Діаметр отвору під штовхач плунжера в корпусі насоса 32,000-32,025 / 32,1
- Діаметр штовхача плунжера 31,950-31,975 / 31,9
- Зазор між корпусом насоса та штовхачем плунжера 0,025-0,075 / 0,2
- Внутрішній діаметр втулки ролика 11,006-11,024 / 11,04
- Діаметр осі ролика 10,989-11,000 / 10,93
- Зазор між віссю ролика та втулкою 0,006-0,035 / 0,11
- Діаметр отвору ролика штовхача 15,000-15,018 / 15,08
- Зовнішній діаметр втулки ролика 14,956-14,984 / 14,9
- Зазор між втулкою ролика та роликом 0,016-0,052 / 0,18
- Внутрішній діаметр підшипника 29,989-30,001
- Діаметр шийки кулачкового валу 30,002-30,011 / 30
- Зазор між кулачковим валом та підшипником 0,000 - 0,001 / 0,003
- Внутрішній діаметр втулки важеля рейок 7,00-7,03 / 7.1
- Діаметр осі важеля рейок 6,945-6,985 / 6,9
- Зазор між віссю та втулкою 0,015-0,085 / 0,2
- Ширина паза рейки 5,025-5,065 / 5,1
- Діаметр пальця важеля рейок 4,988-5,000 / 4,92
- Зазор між пальцем та стінками паза 0,025-0,077 / 0,18
- Ширина паза рейки (паз для осі повідця поворотної втулки) 4,100-4,148 / 4,2
- Діаметр осі повідця поворотної втулки 3,965-3,983 / 3,9
- Зазор між віссю та стінками паза 0,117-0,183 / 0,3
Регулятор частоти обертання
- Внутрішній діаметр втулки вантажу 7,035-7,065 / 7,1
- Діаметр осі вантажу регулятора 6,99-7,00
- Зазор між віссю вантажу та втулкою 0,035-0,075
- Внутрішній діаметр ролика вантажу 7,023-7,050
- Діаметр осі ролика 6,99-7,00
- Зазор між віссю та роликом 0,023-0,060
- Внутрішній діаметр втулки важеля керування 12,000-12,035 / 12,25
- Діаметр валу важеля керування 11,93-11,98
- Зазор між валом та втулкою 0,020-0,105 / 0,4
- Діаметр отвору завзятої п'яти 8,023-8,050 / 8,1
- Діаметр осі п'яти 7,99-8,00 / 7,90
- Зазор між віссю та отвором 0,023-0,060 / 0,2
- Діаметр отвору в важелі пружини регулятора 10,013-10,033 / 10,15
- Діаметр осі важеля пружини 9,915-9,965 / 9,85
- Зазор між віссю та отвором важеля 0,048-0,118 / 0,3
- Діаметр отвору державки вантажів 15,000-15,035 / 15.2
- Діаметр сфери втулки муфти вантажів 14,60-14,53 / 14,4
- Зазор між сферою та отвором 0,40-0,50 / 0,8
- Діаметр отвору важеля муфти вантажів 10,035-10,085 / 10,1
- Зовнішній діаметр втулки важеля регулятора 10,010-10,025 / 9,9
- Зазор між втулкою та отвором у важелі 0,010-0,075 / 0,2
- Внутрішній діаметр втулки важеля регулятора 7,00-7,023 / 7,1
- Діаметр осі важелів 6,940-6,965 / 6,9
- Зазор між втулкою та віссю важелів 0,035-0,090 / 0,2
- Ширина паза правої рейки 5,100-5,148 / 5,2
- Діаметр штифта важеля муфти вантажів 4,992-5,000 / 4,95
- Зазор між штифтом та стінками паза 0,100-0,156 / 0,25
- Внутрішній діаметр втулки штока штовхача 6,000-6,025
- Діаметр штока 5,997-6,020
- Зазор між штоком та втулкою 0,0027-0,0045 / 0,01
- Діаметр отвору корпусу насоса 25,000-25,021 / 25,1
- Діаметр поршня насоса 24,98-24,993 24,92
- Зазор між поршнем та отвором корпусу 0,007-0,041 / 0,18
- Діаметр отвору під штовхач у кришці регулятора 19,000-19,023 / 19,09
- Діаметр штовхача 18,915-18,975 / 18,89
- Зазор між штовхачем та кришкою 0,025-0,108 / 0,2
- Діаметр отвору штовхача 7,000-7,016 / 7,05
- Діаметр осі ролика 6,973-6,987 / 6,9
- Зазор між віссю та штовхачем 0,013-0,043 / 0,15
- Внутрішній діаметр ролика штовхача 7,023-7,050 / 7,12
- Діаметр осі ролика 6,973-6,987 / 6,84
- Зазор між віссю та роликом 0,036-0,077 / 0,28
Моменти затягування різьбових з'єднань, Нм (кгсм)
- Штуцер форсунки 78,5-98,1 (8-10)
- Гайка розпилювача форсунки. 58,8-78,5 (6 - 8)
- Гайка скоб кріплення форсунки 31,4-39,2 (3,2-4,0)
- Гайка кріплення муфти випередження впорскування палива 98,1-117,7(10-12)
- Корпус муфти випередження впорскування. 314-343 (32-35)
- Гвинти маслозаливних отворів на корпусі муфти випередження впорскування 4,9-10,8 (0,5-1,1)
- Гайка кріплення паливопроводів високого тиску 24,5-44,1 (2,5-4,5)
- Болти кріплення паливопроводів низького тиску до форсунок 19,6-24,5 (2,0-2,5)
- Болти кріплення паливопроводів низького тиску до електромагнітного клапана 16,7-22,6(1,7-2,3)
- Штуцер секції паливного насоса високого тиску 98,1-117,7(10-12)
- Гайки кріплення фланця секції паливного насоса високого тиску 24,5-43,2 (2,5-4,4)
- Гайки кріплення ексцентрика приводу паливопідкачувального насоса низкого тиску 44,1-54,0 (4,5-5,5)