Ausbau der Einspritzpumpe
So entfernen Sie die Hochdruck-Kraftstoffpumpe:
- - die manuellen Steuerkabel des Motorstopphebels und des Drehzahlreglerhebels, die Steuerstange der Kraftstoffzufuhr, die Kraftstoffleitungen zur Pumpe, den Auslass, die Ablassleitungen und die Leitung vom Kraftstofffeinfilter, das Öl Zuleitung zur Pumpe, Ölablassleitung; li>
- - Lösen Sie die beiden Schrauben der angetriebenen Kupplungshälfte (um die Schrauben zu lösen, bewegen Sie sie in eine geeignete Position, indem Sie die Kurbelwelle mit einem Brecheisen durch die Löcher am Schwungrad durch die Kupplungsgehäuseklappe drehen);
- - Kraftstoffleitungen zu den Zündkerzen, Hochdruckleitungen (entfernen) und Luftzufuhrleitung zum Ventil des Zusatzbremssystems abklemmen;
- - Lösen Sie die vier Schrauben, mit denen die Kraftstoffpumpe befestigt ist.
- - Entfernen Sie die Pumpe.
So installieren Sie die Hochdruck-Kraftstoffpumpe:
- - Drehen Sie die Kurbelwelle in die Position, die dem Beginn der Kraftstoffeinspritzung im ersten Zylinder entspricht (die Sperre ist mit dem Schwungrad verbunden). in diesem Fall muss die Passfedernut der Antriebskupplung wie folgt angeordnet sein:
- - unten, für Motormod. 740.11-240 und Mod. 740.14-300;
- - in horizontaler Position auf der linken Seite, von der Schwungradseite aus für Motormodifikationen betrachtet. 740.13-260;
Installieren Sie die Pumpe am Motor und richten Sie sie aus:
- - Markierungen am Pumpenkörper und an der Einspritzvorlaufkupplung, für Motoren Mod. 740.11-240 und Mod. 740.14-300;
- - Einbaumarkierung am Flansch der angetriebenen Kupplungshälfte mit Anzeige am Gehäuse der Einspritzpumpe für Motormod. 740.13-260;
- - ziehen Sie die Befestigungsschrauben der Pumpe wie in der Abbildung gezeigt fest;
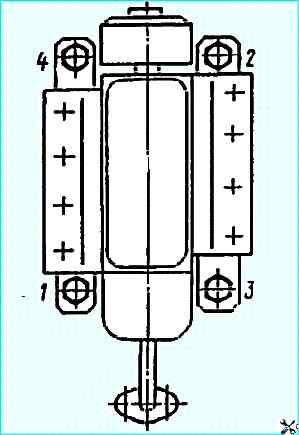
- - ohne die relative Position der Markierungen zu verändern, ziehen Sie die obere Schraube der angetriebenen Kupplungshälfte des Antriebs fest, schieben Sie die Sperre in die kleine Nut, drehen Sie die Kurbelwelle eine Umdrehung und ziehen Sie die zweite Schraube der angetriebenen Kupplungshälfte fest;
- - Installieren Sie die Lukenabdeckung des Kupplungsgehäuses.
- - Verbinden Sie die Hochdruckleitungen, die Ölversorgungsleitung mit der Hochdruck-Kraftstoffpumpe und die Ölablassleitung, die Luftversorgungsleitung mit dem Ventil des Hilfsbremssystems, die Niederdruckleitungen und die Steuerstange der Kraftstoffversorgung , die Handsteuerzüge des Stopphebels und des Reglersteuerhebels.
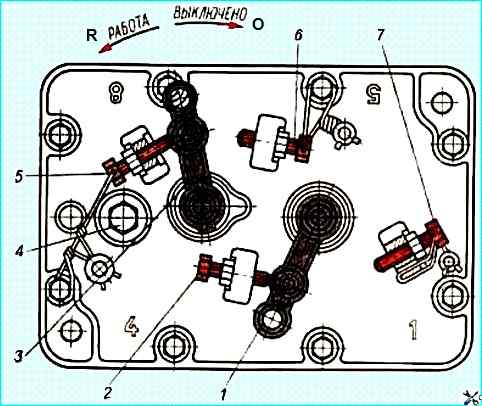
Nach dem Einbau der Hochdruck-Kraftstoffpumpe den Motor starten und mit der Schraube 2 (Abb. Deckel Einspritzpumpenregler) die minimale Leerlaufdrehzahl einstellen, diese sollte 600±50 min -1
Bei der Reparatur der Hochdruck-Kraftstoffpumpe:
- - Ersetzen Sie den Pumpenkörper, wenn er Risse und abgenutzte Hauptgewinde aufweist;
- - Zu den Defekten an der Kolbenbuchse zählen Absplitterungen und Metallabplatzungen an den Löchern, Riefen, Kratzer, Verschleiß der Arbeitsfläche, Vergrößerung des Durchmessers der Einlass- und Absperrfenster, Risse und Schwächungen an den Sitzstellen (Absplitterungen, Metallabplatzungen und Risse sind irreparable Mängel).
Messen Sie den Verschleiß der Lauffläche der Kolbenbuchse mit einer Genauigkeit von 0,001 mm, Ovalität, Konizität und Vergrößerung der Buchsenbohrung mit einem Mikrometer oder einem Anzeigegerät zur Messung von Innenflächen mit einem Teilungswert von bis zu 0,001 mm und konische Lehren;
- Zu den Kolbendefekten zählen Metallabsplitterungen und Kratzer auf der Arbeitsfläche, Verschleiß der Arbeitsfläche und Risse.
Erkennen Sie die Verformung der Kolbengeometrie mit einem Minimeter mit einer Genauigkeit von 0,001 mm, wenn Sie seinen Zeiger entsprechend der Originalprobe auf Null stellen, oder mit einem Messgerät in Form einer konischen Hülse;
- Prüfen Sie das Spaltmaß im Kolbenpaar auf einem Druckprüfstand mit fallender Last.
Spülen Sie die gepaarten Teile vor dem Test gründlich mit gefiltertem Dieselkraftstoff ab.
Installieren Sie das Kolbenpaar in der Ständerbuchse und den Kolben in der maximalen Vorschubposition.
Füllen Sie den Raum über dem Kolben mit gefiltertem Dieselkraftstoff.
Installieren Sie die Dichtungsplatte am Ende der Buchse, befestigen Sie sie mit der Schraube und lösen Sie anschließend die Ladeverriegelung. Unter seiner Wirkung wird der Kraftstoff allmählich durch den Spalt im Dampf herausgedrückt - chem je größer die Lücke, desto schneller.
Der Wert der Belastung des Kolbens muss dem Wert des Kraftstoffdrucks von 19,1–20,1 MPa (195–205 kgf/cm 2) entsprechen.
Das vollständige Anheben des Kolbens bis zum Abschaltmoment unter Lasteinwirkung, begleitet vom Herauspressen von Kraftstoff durch den Spalt zwischen der Hülse und dem Kolben, muss in mindestens 20 s erfolgen.
Installieren Sie das Kolbenpaar mit einer Kolbenanstiegszeit bis zum Abschalten von mehr als 40 Sekunden, befeuchtet mit gefiltertem Dieselkraftstoff, in vertikaler Position am Ende der Hülse, nachdem Sie zuvor ein Blatt sauberes Papier darunter gelegt haben.
Nach einer Wartezeit von fünf Minuten sollte die Hülse beim Anheben des Paars am Kolbenende durch die Einwirkung ihres Eigengewichts vom Kolben fallen;
- der Kolbenschieber ist mit einem Abstand von 0,025–0,075 mm in der Öffnung des Pumpenkörpers eingebaut.
Der maximal zulässige Spalt im Betrieb beträgt 0,2 mm. Messen Sie den Außendurchmesser des Kolbenstößels mit einem Mikrometer oder Messschieber.
- Bei der Montageeinheit Schubrolle – Rollenbuchse – Rollenachse liegt der Hauptdefekt im Verschleiß der Passflächen.
Der Gesamtspalt in der Paarung beträgt 0,022–0,087 mm, maximal zulässig sind 0,3 mm (mit Messkopf messen).
Wenn der Verschleiß den angegebenen Grenzwert überschreitet, muss der Drücker zerlegt und repariert werden. Führen Sie dabei gesonderte Messungen durch.
Das maximal zulässige Spaltmaß für den Oberflächenverschleiß beträgt in der Verbindung Rollenachse – Rollenbuchse 0,12 mm, in der Verbindung Rollenbuchse – Schubrolle 0,18 mm.
Messen Sie die Außenflächen der Teile mit einem Mikrometer und die Innenflächen mit einer Bohrungslehre und einem Zeiger.
- Auf der Oberfläche der Nockenwelle sind keine Metallabsplitterungen, Riefen, Gewindeabriße oder Korrosionsspuren zulässig.
Die maximal zulässige Höhe des Nockenprofils beträgt nicht weniger als 47,7 mm (die Höhe des Nockenprofils beträgt laut CD 47,95–48,05 mm).
Nehmen Sie die Messungen mit einer 47,7-Klammer vor. der Durchmesser der Zapfen für die Innenringe der Lager muss mindestens 30,0 mm betragen (gemäß CD 30.002-30.011 mm), die Spannung an der Dichtkante der Manschette mindestens 0,5 mm;
- Risse, Dellen und Korrosionsspuren sind auf der Oberfläche des Auslassventils nicht zulässig.
Ventilverschleiß äußert sich durch Undichtigkeit entlang des Dichtkegels und durch Feststecken des Ventils im Sitz.
Verwenden Sie eine 10-fache Lupe, um Defekte zu erkennen.
Bei Verlust der Dichtung Sitz und Ventil entlang des Konus mit Paste GOST 3647-71 aneinander schleifen; wenn das Ventil im Sitz feststeckt, die Teile mit Benzin oder Dieselkraftstoff waschen.
Wenn die Störung weiterhin besteht, ersetzen Sie das Paar.
- das maximal zulässige Spiel in der Verbindung des Stifts des Zahnstangenhebels - die Nut der Zahnstange beträgt 0,18 mm (gemäß CD 0,025-0,077 mm), das maximal zulässige Spiel in der Verbindung der Achse der Leine der Drehhülse - die Nut der Zahnstange der Kraftstoffpumpe beträgt 0,3 mm (gemäß CD 0,117 - 0,183 mm).
Verwenden Sie zum Messen von Nuten eine Bohrungslehre.
Bei der Reparatur des Drehzahlreglers:
- Ersetzen Sie die obere und hintere Abdeckung des Reglers, wenn diese Risse aufweisen.
Wenn der Netzölfilter in der hinteren Abdeckung des Reglers verstopft ist, blasen Sie ihn mit Druckluft aus. Wenn der Filter defekt ist, ersetzen Sie ihn.
Die Betriebsöldurchflussrate durch den Filter muss bei einem Druck von 98,1–294 kPa (1–3 kgf/cm 2) mindestens 1,6 l/h betragen;
- um die Eignung des mit Gewichten montierten Reglergewichtshalters für die weitere Verwendung zu bestimmen, prüfen und messen Sie ihn ohne Demontage, da beim Herausdrücken die Teile beschädigt werden können und die Paarung der Gewichte, die mit einem Unterschied in statischer Moment von nicht mehr als 196 kPa (2 kgf/ siehe 2).
Eine teilweise oder vollständige Demontage der Baugruppe sollte nur dann vorgenommen werden, wenn der Verschleiß das zulässige Maß überschreitet oder Teile beschädigt sind.
Der Abstand zwischen dem Reglerfederhebel und der in den Pumpenkörper eingepressten Hebelachse darf maximal 0,3 mm betragen
Bei der Reparatur der Niederdruckpumpe und der Vorstart-Kraftstoffpumpe:
- - Ersetzen Sie die Niederdruckpumpe und die Vorstart-Kraftstoffpumpe, wenn Risse im Gehäuse, Brüche, mechanische Beschädigungen oder Korrosion vorliegen, die zum Verlust der Beweglichkeit der Passteile führen.
- - Denken Sie beim Auseinanderbauen und Zusammenbauen einer Niederdruckpumpe daran, dass Kolben und Pumpenkörper ein exakt aufeinander abgestimmtes Paar sind und nicht auseinandergenommen werden können.
Die Pumpe wird nur dann zerlegt und repariert, wenn sie die geforderten Eigenschaften nicht aufweist;
- - Achten Sie besonders auf den Zustand der Stangen-Buchsen-Baugruppe der Niederdruckpumpe, da die in den Nockenwellenhohlraum fließende Kraftstoffmenge vom Verschleiß der Kupplung abhängt.
Der Spalt bei der angegebenen Paarung sollte 0,012 mm nicht überschreiten.
Überprüfen Sie die Spaltgröße, ohne die Buchse vom Pumpenkörper zu entfernen, indem Sie die Zeit bestimmen, die der Luftdruck benötigt, um von 490 kPa (5 kgf/cm 2) auf 392 kPa (4 kgf /cm 2). in einer 30 cm3 Batterie.
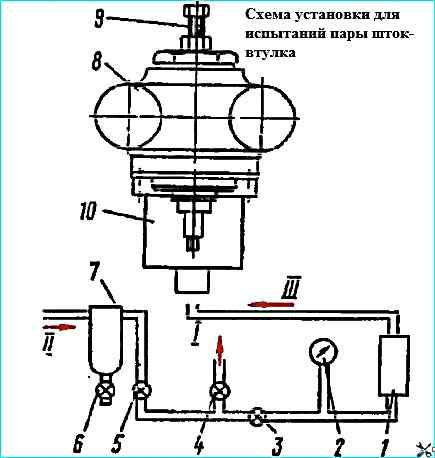
Das Aufbaudiagramm zur Messung der Dichte einer Präzisionsbaugruppe ist in der Abbildung dargestellt.
Installieren Sie den Pumpenkörper 8 in das Gerät, füllen Sie den Akkumulator mit Druckluft auf einen Druck von mindestens 539 kPa (5,5 kgf/cm 2), trennen Sie ihn hermetisch von der Druckluftleitung und Messen Sie die Zeit, in der der Batteriedruck von 490 kPa (5 kgf/cm 2) auf 392 kPa (4 kgf/cm 2) abfällt.
Vergleichen Sie die erhaltene Zeit mit ähnlichen Dichtewerten eines Referenzpräzisionspaars mit einem Passungsspalt von 0,012 mm.
Ersetzen oder reparieren Sie das Paar, wenn seine Dichte unter dem Referenzwert liegt.
Die Dichtheit des Paares lässt sich auch einfacher prüfen: Lassen Sie gefilterten Dieselkraftstoff durch den Spalt zwischen Pleuelstange und Buchse laufen.
Die durch den Spalt austretende Kraftstoffmenge sollte innerhalb von 20 Min. 1 cm 3 nicht überschreiten.
Wenn die Stangen-Buchsen-Einheit ausgetauscht wird, reinigen Sie die Gewindeoberfläche und die Stirnfläche im Niederdruckpumpenkörper von Klebstoffrückständen.
Installieren Sie die neue Stangenbuchse mit Epoxidkleber im Pumpenkörper.
Um die Festigkeit und Dichtheit der Verbindung sicherzustellen, entfetten Sie zunächst die gereinigten Kontaktflächen des Pumpenkörpers und der Buchse mit B-70-Benzin.
Nachdem Sie die Pleuelbuchse mit einem Drehmoment von 9,81 Nm (1 kgfm) festgezogen haben, prüfen Sie, ob sich die Pleuelstange darin leicht bewegen lässt. Bei Bedarf Anzugsdrehmoment reduzieren.
Überprüfen Sie während des Tests den Pumpendurchfluss.
Stellen Sie den Prüfaufbau gemäß dem Schema her: Kraftstofftank – Kraftstoff-Grobfilter – Vakuummeter – Kraftstoffpumpe – Druckmesser – Messbehälter.
Verbinden Sie die Elemente des Stromkreises mithilfe transparenter Rohre mit einem Innendurchmesser von mindestens 8 mm.
Installieren Sie Ventile, um am Pumpeneinlass ein Vakuum und am Auslass einen Gegendruck zu erzeugen.
Überprüfen Sie den Sommerdieselkraftstoff bei einer Temperatur von 25–30 °C und achten Sie bei Abwesenheit von Luft im System auf Sauberkeit des Kraftstoffstroms in transparenten Rohren.
Die Pumpe muss Kraftstoff aus einem 1 m unterhalb der Pumpe installierten Tank ansaugen.
Pumpendurchflussrate bei einer Nockenwellendrehzahl von 1100-1300 min -1, einem Vakuum am Einlassanschluss von 23 kPa (173 mm Hg) und einem Gegendruck:
- - 80–100 kPa (0,8–1,0 kgf/cm 2) sollten für Motormod. mindestens 3 l/min betragen. 740.11-240 und Mod. 740.13-260;
- - 125 kPa (1,25 kgf/cm 2) sollten für den Motor 740.14-300 mindestens 3,5 l/min betragen.
Bei komplett geschlossenem Auslassventil und einer Nockenwellendrehzahl von 1100-1300 min-1 muss die Pumpe einen Druck von mindestens erzeugen:
- - 400 kPa (4 kgf/cm 2) – für Motoren mod. 740.11-240 und 740.13-260;
- - 600 kPa (6 kgf/cm 2) – für Motor 740.14-300.
Bei vollständig geschlossenem Einlassventil und der angegebenen Nockenwellendrehzahl sollte das von der Pumpe erzeugte Mindestvakuum folgendes betragen:
- - 52 kPa (390 mmHg) – für Motoren mod. 740.11-240 und 740.13-260;
- - 70 kPa (525 mmHg) – für Motor 740.14-300;
- - Überprüfen Sie die Kraftstoffpumpe vor dem Start auf einem Ständer mit einem Diagramm: Kraftstofftank – Grobfilter – Kraftstoffpumpe. Die Pumpe muss den Kraftstoff aus einem Tank fördern, der 1 m unterhalb der Handpumpe installiert ist.
Überprüfen Sie die Pumpe auf Undichtigkeiten, indem Sie 5-6 Sekunden lang Luft mit einem Druck von 200-300 kPa (2-3 kgf/cm 2) unter den Kolben leiten und den Hohlraum vorher mit Dieselkraftstoff.
Verwenden Sie das Werkzeug, um die automatische Einspritzvorverstellungskupplung zu entfernen.
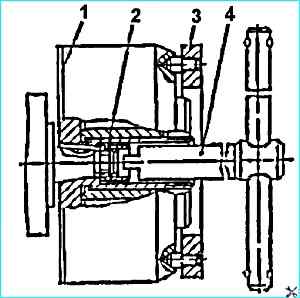
Zuerst muss die Mutter 2 (siehe Abb. Abschrauben der Befestigungsmutter der Einspritzvorverstellungskupplung) abgeschraubt werden, mit der die Kupplung befestigt ist.
Hierzu den Schraubendreher 4 in die Nut der Mutter einführen und, während die Kupplung 1 mit dem Schlüssel 3 gegen Verdrehen gesichert ist, die Mutter abschrauben.
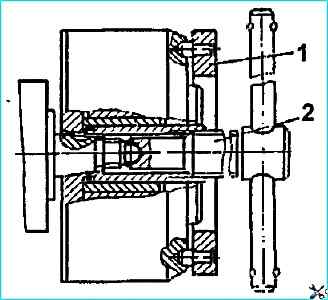
Dann geben Sie es ab Mit dem Abzieher 2 (Abb. Abziehen der Kupplung mit Vorrichtung) die Kupplung abziehen.
So demontieren Sie die Kupplung:
- Schrauben vom Gehäuse lösen und Öl ablassen:
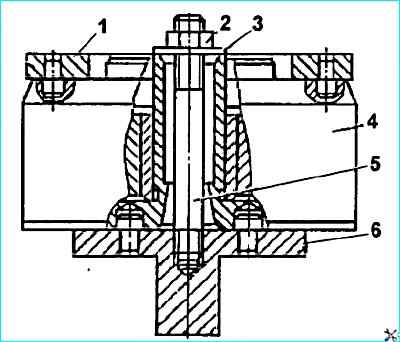
- - den Ständer 6 (Abb. Demontage der Kupplung) des Gerätes in einen Schraubstock einspannen und die Kupplung darauf montieren, den Bolzen 5 in den Ständer schrauben, die Unterlegscheibe 3 montieren und mit Mutter 2 festziehen;
- - mit Schlüssel 1 Gehäuse 5 abschrauben (siehe Abb. Automatische Einspritzvorverstellungskupplung);
- - die vordere Kupplungshälfte 1 mit Distanzstücken 12, Gewichten 11 und Federn 8 entfernen;
- - Bündchen 4 und 2 herausbügeln.
Da die Lasten nach dem statischen Moment ausgewählt werden, sollten sie für die spätere Installation paarweise verwendet werden.
So montieren Sie die Kupplung:
- - Drücken Sie die Manschette 4 in das Loch der vorderen Halbkupplung;
- - Montieren Sie die vordere Kupplungshälfte mit einem Dorn auf der Nabe der angetriebenen Kupplung;
- - Einstellbeläge 6 und Federn 8 in Schalen 7 einbauen, Schalen mit Federn
- - in die Führungslöcher der Lasten, in denen sie sich frei bewegen müssen, ohne zu verklemmen.
In jeder Position der Kupplungsteile sollte der Spalt zwischen Profiloberfläche und Distanzstück nicht mehr als 0,15 mm betragen.
Wenn die Lasten durch Drehen der vorderen Kupplungshälfte zum Stillstand gebracht werden, sollte einer der Spalte nicht mehr als 0,1 mm betragen, der andere sollte Null sein.
Passen Sie die Lücken durch Auswahl von Abstandshaltern an:
- - Hülse 2 bündig mit der inneren Stirnfläche in den Kupplungskörper einpressen;
- - einen Gummidichtring 14 in die Nut der angetriebenen Kupplungshälfte einbauen;
- - Schrauben Sie das Gehäuse auf die angetriebene Kupplungshälfte und ziehen Sie es mit einem Drehmoment von 314–343 Nm (32–35 kgfm) fest.
- - Die angetriebene Kupplungshälfte an drei Stellen abdichten.
Vor dem Einbau des Gehäuses ist darauf zu achten, dass zwischen Gehäuse und Federtellern gleichmäßige Abstände bestehen und die Gewichte bis zum Anschlag zusammengeführt werden. Der Spaltunterschied sollte nicht mehr als 0,2 mm betragen.
Füllen Sie die Kupplung nach der Montage mit dem für den Motor verwendeten Motoröl.
Verwenden Sie zum Zerlegen des Injektors das Gerät I801.20.000.
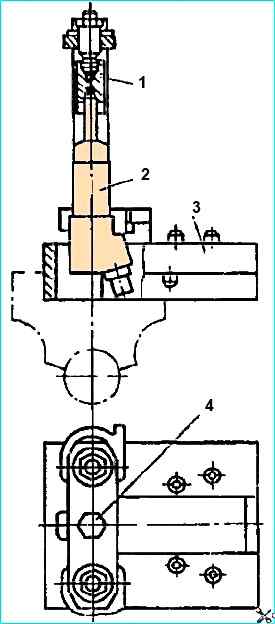
Rahmen 2 (Abb. Demontage der Düse) des Gerätes in einen Schraubstock einspannen, Düse mit der Sprühdüse nach oben in die Nut des Rahmens einbauen.
Beim Einschrauben der Schraube 4 die Düsendüse mit Anschlag 1 andrücken, anschließend mit einem Gabelschlüssel die Düsenmutter lösen.
Nach dem Lösen der Schraube 4 die Düse vom Gerät abnehmen und in Einzelteile zerlegen.
Denken Sie daran, dass das Gehäuse und die Nadel des Zerstäubers als Paar ausgewählt werden und nicht auseinandergenommen werden können. Der maximal zulässige Spalt zwischen Körper und Sprühnadel beträgt 0,006 mm.
Die Hubvergrößerung der Sprühnadel darf 0,4 mm nicht überschreiten; der Durchmesser der Sprühdüsenlöcher sollte 0,38 mm nicht überschreiten.
Eine schlechte Funktion der Einspritzdüsen wird durch einen Druckabfall zu Beginn der Kraftstoffeinspritzung verursacht, der durch den Verschleiß der mit der Feder verbundenen Teile und das Schrumpfen der Feder erklärt wird, daher erlauben Sie nicht die Höhe der Injektor-Abstandshalter muss kleiner als 8,89 mm sein (laut CD 8,9-9,0 mm).
Sollten auf dem Abstandshalter Kratzer oder Korrosionsspuren festgestellt werden (verwenden Sie hierzu eine Lupe mit 10-facher Vergrößerung), ersetzen Sie das Teil.
Zu den Defekten an den Einspritzdüsen zählen Federbrüche, Verstopfungen und Verschleiß der Düsenlöcher, Feststecken der Nadel und Verschleiß der Dichtungsteile (was zu Undichtigkeiten und schlechter Kraftstoffzerstäubung führt).
Reinigen Sie bei Bedarf die Düsenlöcher der Spritze vorsichtig mit einem Stahldraht mit 0,25 mm Durchmesser.
Entfernen Sie Kohlenstoffablagerungen von der Außenfläche der Sprühdüse mit einem in Motoröl getränkten Holzblock oder einer Messingbürste. Verwenden Sie keine scharfen, harten Gegenstände oder Schleifpapier.
Vor dem Zusammenbau den Körper und die Nadel des Zerstäubers mit Benzin waschen und mit gefiltertem Dieselkraftstoff schmieren, danach die Nadel, die um ein Drittel der Länge der Führungsfläche aus dem Körper herausragt, wenn der Zerstäuber in einem Winkel von 45 Grad geneigt wird ° sollte sich unter der Einwirkung der eigenen Masse sanft (ohne zu verklemmen) bis zum Anschlag absenken.
Beim Zusammenbau des Injektors ziehen Sie die Zerstäubermutter fest, indem Sie den Zerstäuber in das Gerät I801.20.000 drücken.
Teileabmessungen und zulässiger Verschleiß, mm
Automatische Kupplung Kraftstoffeinspritzung früh
Laut CD /Akzeptabel
- Durchmesser der Bohrung im Kupplungsgewicht 16.032-16.059 / 16.1
- Lastachsendurchmesser 15.982-16.000 / 15.86
- Abstand zwischen Achse und Ladung 0,032-0,077 / 0,24
- Raumlochdurchmesser 16.032-16.059 / 16.1
- Durchmesser des Bolzens der vorderen Kupplungshälfte 15,973-16,000 / 15.9
- Der Abstand zwischen dem Stift und dem Loch im Abstandshalter beträgt 0,032-0,086 / 0,2
Hochdruck-Kraftstoffpumpe mod. 337-40
Laut CD /Akzeptabel
- Der Durchmesser der Bohrung für den Kolbenschieber im Pumpenkörper beträgt 32.000-32.025 / 32.1
- Durchmesser des Kolbenschiebers 31,950-31,975 / 31,9
- Der Abstand zwischen dem Pumpenkörper und dem Kolbenschieber beträgt 0,025-0,075 / 0,2
- Innendurchmesser der Rollenbuchse 11.006-11.024 / 11.04
- Rollenachsendurchmesser 10.989-11.000 / 10.93
- Spalt zwischen Rollenachse und Buchse 0,006-0,035 / 0,11
- Bohrungsdurchmesser der Schubrolle 15.000-15.018/15.08
- Außendurchmesser der Rollenbuchse 14.956-14.984 / 14.9
- Spalt zwischen Walzenhülse und Walze 0,016-0,052 / 0,18
- Lagerinnendurchmesser 29,989-30,001
- Nockenwellenzapfendurchmesser 30.002-30.011 / 30
- Spalt zwischen Nockenwelle und Lager 0,000 - 0,001 / 0,003
- Innendurchmesser der Zahnstangenhebelbuchse 7,00-7,03 / 7,1
- Durchmesser der Zahnstangenhebelachse 6,945-6,985 / 6,9
- Spalt zwischen Achse und Buchse 0,015-0,085 / 0,2
- Zahnstangennutbreite 5,025-5,065 / 5,1
- Zahnstangenhebelstift Durchmesser 4,988-5,000 / 4,92
- Spalt zwischen Stift und Nutwänden 0,025-0,077 / 0,18
- Racknutbreite (Nut für die Schwenkbuchse der Leinenachse) 4,100-4,148 / 4,2
- Lenkhülsen-Lenkachsendurchmesser 3,965-3,983 / 3,9
- Spalt zwischen Achse und Nutwänden 0,117-0,183 / 0,3
Geschwindigkeitsregler
- Innendurchmesser der Gewichtshülse 7,035-7,065 / 7,1
- Der Durchmesser der Reglergewichtsachse beträgt 6,99-7,00
- Der Abstand zwischen der Lastachse und der Buchse beträgt 0,035–0,075
- Innendurchmesser der Lastrolle 7,023-7,050
- Rollenachsendurchmesser 6,99-7,00
- Spalt zwischen Achse und Rolle 0,023-0,060
- Innendurchmesser der Querlenkerbuchse 12.000-12.035 / 12.25
- Durchmesser der Steuerhebelwelle 11,93-11,98
- Spalt zwischen Welle und Hülse 0,020-0,105 / 0,4
- Durchmesser der Druckfersenbohrung 8,023-8,050 / 8,1
- Fersenachsendurchmesser 7,99-8,00 / 7,90
- Abstand zwischen Achse und Loch 0,023-0,060 / 0,2
- Durchmesser der Bohrung im Hebel der Regulierfeder 10.013-10.033 / 10.15
- Federhebelachsendurchmesser 9,915-9,965 / 9,85
- Abstand zwischen Achse und Hebelloch 0,048-0,118 / 0,3
- Gewichtshalter-Bohrungsdurchmesser 15.000-15.035 / 15.2
- Kugeldurchmesser der Kupplungshülse der Lasten 14,60-14,53 / 14,4
- Abstand zwischen Kugel und Loch 0,40-0,50 / 0,8
- Durchmesser der Bohrung des Hebels der Gewichtskupplung 10.035-10.085 / 10.1
- Außendurchmesser der Drehzahlhebelbuchse 10.010-10.025 / 9.9
- Der Abstand zwischen der Buchse und dem Loch im Hebel beträgt 0,010-0,075 / 0,2
- Innendurchmesser der Reglerhebelbuchse 7,00-7,023 / 7,1
- Hebelachsendurchmesser 6,940-6,965 / 6,9
- Spalt zwischen Buchse und Hebelachse 0,035-0,090 / 0,2
- Rechte Schienenrillenbreite 5.100-5.148 / 5.2
- Durchmesser des Gewichtskupplungshebelstifts 4,992-5,000 / 4,95
- Abstand zwischen Stift- und Nutwänden 0,100-0,156 / 0,25
- Innendurchmesser der Stößelstangenbuchse 6.000-6.025
- Stangendurchmesser 5,997-6,020
- Das Spiel zwischen Stange und Hülse beträgt 0,0027-0,0045 / 0,01
- Pumpenkörper-Lochdurchmesser 25.000-25.021 / 25.1
- Pumpenkolbendurchmesser 24,98-24,993 24,92
- Das Spiel zwischen Kolben und Gehäusebohrung beträgt 0,007-0,041 / 0,18
- Der Durchmesser der Bohrung für den Drücker im Reglerdeckel beträgt 19.000-19.023 / 19.09
- Stößelstangendurchmesser 18,915-18,975 / 18,89
- Spalt zwischen Drücker und Deckel 0,025-0,108 / 0,2
- Durchmesser der Drückerbohrung 7,000–7,016/7,05
- Rollenachsendurchmesser 6,973-6,987 / 6,9
- Spalt zwischen Achse und Stößel 0,013-0,043 / 0,15
- Innendurchmesser der Schubrolle 7,023-7,050 / 7,12
- Rollenachsendurchmesser 6,973-6,987 / 6,84
- Spalt zwischen Achse und Rolle 0,036-0,077 / 0,28
Anzugsdrehmomente von Gewindeverbindungen, Nm (kgcm)
- Injektornippel 78,5-98,1 (8-10)
- Mutter der Einspritzdüse. 58,8-78,5 (6 - 8)
- Mutter für Injektorhalterung 31,4-39,2 (3,2-4,0)
- Befestigungsmutter der Einspritzverstellungskupplung 98.1-117.7(10-12)
- Gehäuse der Einspritzverstellungskupplung. 314-343 (32-35)
- Öleinfüllschrauben am Einspritzkupplungsgehäuse 4,9-10,8 (0,5-1,1)
- Befestigungsmutter für Hochdruck-Kraftstoffleitung 24,5-44,1 (2,5-4,5)
- Schrauben zur Befestigung von Niederdruck-Kraftstoffleitungen an Einspritzdüsen 19,6-24,5 (2,0-2,5)
- Schrauben zur Befestigung von Niederdruck-Kraftstoffleitungen am Elektromagnetventil 16,7-22,6(1,7-2,3)
- Anschlussstück für Hochdruck-Kraftstoffpumpenabschnitt 98.1-117.7(10-12)
- Befestigungsmuttern für den Flansch der Hochdruck-Kraftstoffpumpe 24,5-43,2 (2,5-4,4)
- Befestigungsmuttern für Exzenterantrieb der Kraftstoffpumpe unten dessen Druck 44,1-54,0 (4,5-5,5) beträgt