Nach der Demontage stellen wir den Motor zur Demontage auf einen Ständer
Entfernen Sie den Generator, den Zylinderkopf, das Schwungrad und den Ölfilter
Mit einem 17er Schraubenschlüssel lösen wir zwei Schrauben 1 der unteren Befestigung und mit einem 13er Schraubenschlüssel die Schraube 2 der oberen Befestigung der Halterung der vorderen rechten Stütze des Aggregats.
Entfernen Sie die Halterung
Mit einem 13er-Kopf lösen wir die drei Schrauben, mit denen die Generatorhalterung befestigt ist.
Entfernen Sie die Generatorhalterung.
Entfernen Sie die Ölwanne des Motors (siehe "Ersetzen der Ölwannendichtung").
Entfernen Sie den Ölbehälter und die Ölpumpe (siehe "Ausbau und Demontage der Ölpumpe").
Nachdem Sie die beiden Schrauben, mit denen das Zufuhrrohr der Kühlmittelpumpe am Zylinderblock befestigt ist, mit einem 10er-Schlüssel gelöst haben, entfernen Sie das Rohr und seine Dichtung.
Mit einem Kopf von 10 lösen wir die sechs Schrauben der Kurbelwelle
Entfernen Sie den hinteren Öldichtungshalter
Die Verbindung zwischen dem Öldichtungshalter und dem Zylinderblock ist mit einer Dichtung abgedichtet
Mit einem Kopf von 14 lösen wir die beiden Muttern der Schrauben, mit denen die Pleuelabdeckung befestigt ist (die Pleuelstange muss sich am UT befinden)
Durch Klopfen auf die Seiten der Pleuelkappe mit einem Hammer aus Kunststoff (oder weichem Metall)
Entfernen Sie die Pleuelstangenabdeckung
Entfernen Sie die Pleuellagerschale von der Abdeckung
Indem wir den Holzgriff des Hammers gegen die Enden der Stangen der Pleuelschrauben legen, verschieben wir den unteren Kopf der Pleuelstange vom Kurbelwellenhals
Entfernen Sie den Kolben mit der Pleuelstange vom Zylinder.
Entfernen Sie die Pleuellagerschale vom unteren Pleuelkopf.
In ähnlicher Weise entfernen wir Kolben mit Pleuel von anderen Zylindern.
Wenn die Teile der Pleuel- und Kolbengruppe nicht beschädigt und leicht abgenutzt sind, können sie wiederverwendet werden.
Deshalb müssen Sie bei der Demontage die Teile markieren, damit sie bei der späteren Montage an ihrem Platz eingebaut werden können.
Öffnen Sie mit den Fingern vorsichtig (ohne großen Kraftaufwand) die Verriegelung des oberen Kompressionsrings
Entfernen Sie den Ring aus der Kolbennut. Entfernen Sie auf die gleiche Weise den unteren Kompressionsring.
Öffnen Sie das Schloss und entfernen Sie den Ölabstreifring
Entfernen Sie den Ölabstreifring-Expander.
Um den Kolben von der Pleuelstange zu entfernen, hebeln Sie den Sicherungsring des Kolbenbolzens mit einem Schraubendreher ab und entfernen Sie ihn aus der Ringnut der Kolbennabe.
Auf die gleiche Weise nehmen wir den anderen Kolbenbolzen-Sicherungsring heraus.
Drücken Sie den Kolbenbolzen mit einem Dorn heraus und entfernen Sie den Kolben vom oberen Kopf der Pleuelstange.
Wir entfernen auch die restlichen Kolben.
Mit einem 17er-Kopf lösen wir die beiden Schrauben, mit denen der Kurbelwellen-Hauptlagerdeckel befestigt ist
Entfernen Sie den Hauptlagerdeckel.
Entfernen Sie die untere Kurbelwellen-Hauptlagerschale von der Abdeckung.
Entfernen Sie auf die gleiche Weise vier weitere Kurbelwellen-Hauptlagerdeckel.
Wir entfernen die Kurbelwelle vom Zylinderblock und entfernen dann die beiden Druckhalbringe der Kurbelwelle (durch Pfeile dargestellt) aus den Nuten des dritten Hauptlagerträgers (im Zylinderblock).
Entfernen Sie die oberen Kurbelwellen-Hauptlagerschalen von den Zylinderblockstützen.
Entfernen Sie mit einem scharfen Werkzeug das restliche Dichtmittel von der Passfläche des Zylinderblocks unter der Ölwanne
Entfernen Sie die Reste der Zylinderkopfdichtung. Wir reinigen die Passflächen des Zylinderblocks unter dem Kühlmittelpumpenrohr und dem hinteren Öldichtungshalter der Kurbelwelle.
Nach der Demontage des Motors waschen und reinigen wir die Teile der Zylinder-Kolben-Gruppe gründlich von Kohlenstoffablagerungen, um ihren technischen Zustand zu überprüfen.
Um den Verschleiß des Zylinders mit einem Bohrungsmessgerät zu bestimmen, messen wir den Zylinderdurchmesser in vier Zonen (im Abstand von 8, 15, 50 und 90 mm von der oberen Ebene des Zylinderblocks) und in zwei Richtungen (parallel und senkrecht Polachse der Kurbelwelle).
Im Bereich des ersten Riemens (bis 8 mm) verschleißt der Zylinder praktisch nicht.
Anhand der Differenz der Messungen in der ersten und anderen Zonen ist es daher möglich, den Verschleiß des Zylinders zu bestimmen.
Wenn der Verschleiß der Zylinder 0,15 mm überschreitet, ist es notwendig, die Zylinder auf eine Reparaturgröße (um 0,4 oder 0,8 mm erhöht) zu bohren und zu honen.
Um den Verschleiß des Kolbenschafts mit einem Mikrometer zu bestimmen, messen wir dessen Durchmesser in einer Ebene senkrecht zur Achse des Kolbenbolzens, in einem Abstand von 55 mm vom Kolbenboden.
Wir messen die Durchmesser aller Haupt- und Pleuelzapfen der Kurbelwelle mit einem Mikrometer in zwei diametral gegenüberliegenden Ebenen.
Wir schleifen die Kurbelwellenzapfen auf das nächstgelegene Reparaturmaß, wenn der Verschleiß oder die Ovalität größer als 0,03 mm ist und auch wenn Kratzer und Flecken auf den Zapfen vorhanden sind.
Nach dem Schleifen der Kurbelwellenzapfen müssen die Ölkanalstopfen entfernt werden.
Anschließend spülen wir die Kanäle gründlich aus und blasen sie mit Druckluft aus, um Schleifmittelrückstände zu entfernen.
Kurbelwellenzapfen schleifen, Stopfen aus- und einbauen.
Wir bauen den Motor in umgekehrter Reihenfolge zusammen.
Wir bauen neue Kurbelwellen-Hauptlagerschalen im Nenn- oder Reparaturmaß ein (nach dem Schleifen der Wellenzapfen).
Einsätze mit einer Nut auf der Arbeitsfläche werden in den Zylinderblockstützen und ohne Nuten in den Hauptlagerdeckeln eingebaut.
Schmieren Sie die Laufbuchsen mit Motoröl und platzieren Sie die Kurbelwelle in den Zylinderblockhalterungen.
Wir setzen mit Motoröl geschmierte Anlaufhalbringe in die Nuten des dritten Hauptlagerträgers ein.
Die Oberflächen der Halbringe mit einer Anti-Reibungs-Beschichtung (auf ihnen sind Nuten angebracht) müssen den Anlaufflächen der Kurbelwelle zugewandt sein.
Wir montieren die Hauptlagerdeckel gemäß den auf ihrer Außenfläche angebrachten Markierungen (die Deckel werden von der Zahnriemenantriebsseite aus gezählt).
Richten Sie die Abdeckungen beim Einbau so aus, dass sich ihre Markierungen näher an der Vorderseite des Zylinderblocks (Generatormontageseite) befinden.
In diesem Fall befinden sich die Verriegelungen der Ober- und Unterschale jedes Hauptlagers auf derselben Seite.
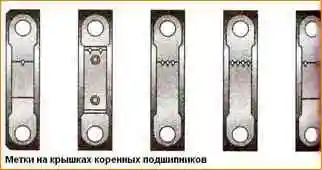
Wir ziehen die Schrauben der Hauptlagerdeckel mit einem Drehmoment von 68 - 84 Nm an.
Kolben für Zylinder werden entsprechend den Durchmesserklassen des Zylinders und der Kolbenmäntel ausgewählt.
Die Durchmesserklasse jedes Zylinders (in unserem Fall mit dem Buchstaben "C" gekennzeichnet) ist gegenüber dem Zylinder auf der unteren Ebene des Blocks (der Ebene der Ölwannenbefestigung) eingeprägt.
Die Kolbenmantelklasse ist auf dem Kolbenkopf gekennzeichnet. Am Motor sind Kolben der gleichen Massenklasse verbaut.
Markierung auf dem Kolbenboden:
- - d – Kolbenklasse entsprechend dem Durchmesser des Bolzenlochs;
- - C – Kolbenmanteldurchmesserklasse;
- - ↓ - Beim Einbau des Kolbens in den Zylinder sollte der Pfeil auf den Steuerantrieb gerichtet sein;
- - Г - Kolbenmassenklasse.
Die Kennzeichnung der Pleuelklassen nach Masse und Durchmesser der Bohrung für den Kolbenbolzen ist auf dem Pleueldeckel angebracht.
Markierung auf Pleueldeckel:
- - H – Pleuel-Gewichtsklasse;
- - 2 - Pleuelklasse entsprechend dem Durchmesser des Lochs für den Kolbenbolzen.
Vor dem Zusammenbau der Pleuel- und Kolbengruppe aus neuen Teilen ist es notwendig, die Finger an den Kolben und Pleuelstangen aufzunehmen.
Die Klasse des Kolbens und der Pleuelstange hinsichtlich des Durchmessers der Löcher für den Bolzen muss der Klasse des Durchmessers des Bolzens entsprechen.
Ein richtig ausgewählter, mit Motoröl geschmierter Kolbenbolzen sollte mit Daumendruck in das Loch im oberen Pleuelkopf eindringen und in vertikaler Position nicht herausfallen.
Beim Zusammenbau des Kolbens mit der Pleuelstange richten wir diese so aus, dass sich die auf der Pleuelstange eingestanzte Seriennummer beim Einbau in den Zylinder näher an der Rückwand des Zylinderblocks (an der sich der Ölfilter befindet) befindet ).
Vor dem Einbau der Kolbenringe auf den Kolben ist es notwendig, die thermischen Lücken in den Schlössern der Ringe zu überprüfen.
Führen Sie dazu den Kolbenring in den Zylinder ein, in den er bei der Montage eingebaut werden soll, und richten Sie den Ring am Kolbenboden aus.
Wir prüfen den Spalt in der Kolbenringsicherung mit einem Satz Flachfühler.
Der Spalt sollte 0,25–0,45 mm betragen. Maximal zulässiger Verschleißspalt 1 mm
Schmieren Sie die Nuten an den Kolben unter den Kolbenringen mit Motoröl. Wir montieren die Ringe an den Kolben.
Setzen Sie den unteren Kompressionsring mit der Nut ("Abstreifer") nach unten ein.
Wenn der Ring mit "TOP" oder "TOP" gekennzeichnet ist, wird der Ring mit der Markierung nach oben platziert.
Ordnen Sie die Ringe wie folgt an:
- - Wir richten die Verriegelung des oberen Kompressionsrings in einem Winkel von etwa 45˚ zur Achse des Kolbenbolzens aus;
- - Verriegelung des unteren Kompressionsrings – in einem Winkel von 180˚ zur Achse der Verriegelung des oberen Rings;
- - Ölabstreifringverriegelung - im Winkel von 90˚ zur Achse der oberen Kompressionsringverriegelung.
Beim Einbau des Ölabstreifrings platzieren wir das Spreizgelenk auf der Seite gegenüber der Ringverriegelung.
Bevor wir den Kolben in den Zylinder einbauen, setzen wir einen verstellbaren Dorn auf den Kolben und drücken durch Anziehen des Dorns die Kolbenringe zusammen.
Montieren Sie den Kolben mit der Pleuelstange im Zylinder.
In diesem Fall muss sich der Pleuelzapfen der Kurbelwelle dieses Zylinders in der UT-Position befinden.
Wir drücken den Hammerstiel gegen die Unterseite des Kolbens und drücken ihn in den Zylinder.
Nachdem wir den Dorn entfernt haben, schieben wir den Kolben mit dem Hammerstiel bis zum Anschlag in den Zylinder.
Gleichzeitig kontrollieren wir den Sitz der unteren Pleuelkopfbuchse am Kurbelwellenzapfen.
Beim Einbau der Pleuelstangenabdeckung müssen die Seriennummern auf der Pleuelstange und der Abdeckung übereinstimmen und sich auf derselben Seite der Pleuelstange befinden
Der weitere Zusammenbau des Motors erfolgt in umgekehrter Reihenfolge.