Motorkraftstoffversorgungsausrüstung – geteilter Typ
Es besteht aus einer Hochdruck-Kraftstoffpumpe mit einem All-Mode-Geschwindigkeitsregler und einem eingebauten Korrektor zur Einstellung der Kraftstoffzufuhr, einer Kraftstoff-Ansaugpumpe, Einspritzdüsen, groben und feinen Kraftstofffiltern sowie Nieder- und Hochdruck-Kraftstoffleitungen .
Aus dem Tank wird der Kraftstoff durch den Grobfilter von der Kraftstoffansaugpumpe angesaugt und dem Feinfilter und dann der Hochdruck-Kraftstoffpumpe zugeführt.
Entsprechend der Zündreihenfolge der Zylinder fördert die Kraftstoffpumpe Kraftstoff durch die Hochdruck-Kraftstoffleitungen zu den Einspritzdüsen, die ihn in den Motorzylindern zerstäuben.
Über das Bypassventil in der Kraftstoffpumpe und die Düse im Feinfilter wird überschüssiger Kraftstoff und damit die in das System eingedrungene Luft über die Kraftstoffleitung zum Kraftstofftank abgeleitet.
Der Kraftstoff, der in den Hohlraum der Düsenfeder gelangt ist, wird über das Abflussrohr zum Tank abgeleitet.
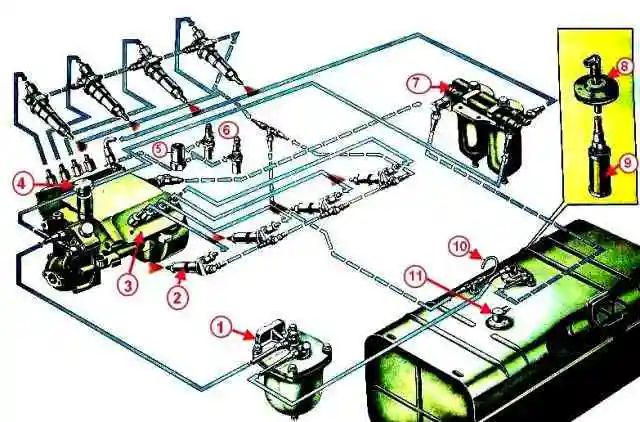
Schema des Stromversorgungssystems: 1 - grober Kraftstofffilter; 2 - Düse; 3 – Hochdruck-Kraftstoffpumpe, 4 – manuelle Kraftstoffansaugpumpe, 5 – Magnetventil; 6 - EFU-Kerze, 7 - Feinfilter; 8 - ein Aufnahmerohr eines Tanks; 9 - Tankfilter; 10 - Kraftstofftankentlüftung; 11 - Tankanzeigesensor
Hochdruck-Kraftstoffpumpe
Die Pumpe befindet sich im Zusammenbruch des Motors zwischen den Zylinderreihen und verfügt über einen Zahnradantrieb.
Die Hochdruck-Kraftstoffpumpe ist entsprechend der Anzahl der Motorzylinder achtteilig.
Die Motoren sind mit Hochdruck-Kraftstoffpumpen verschiedener Modelle ausgestattet, die sich in Design und Einstellung unterscheiden (siehe Artikel „Spezifikationen").
Hochdruck-Kraftstoffpumpe Modell 173
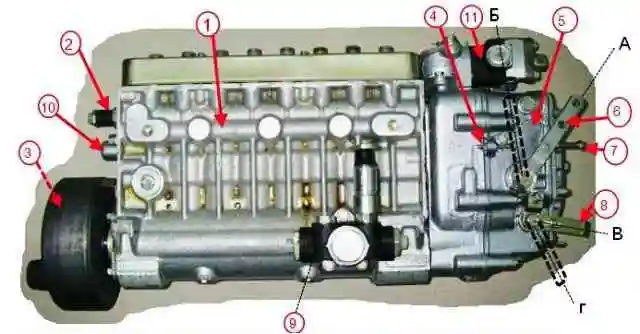
Einspritzpumpe Modell 173: 1 - Kraftstoffpumpengehäuse; 2 - Bypassventil; 3 - Dämpferkupplung; 4 - Schraube zur Begrenzung der Höchstgeschwindigkeit; 5 - Geschwindigkeitsregler; 6 - Reglersteuerhebel; 7 - ein Bolzen zur Begrenzung der Mindestumdrehungen; 8 - Anschlaghalterung; 9 - Kraftstoffansaugpumpe; 10 - Einstellschraube für den Startvorschub; 11 - Korrektur der Kraftstoffzufuhr; A – die Position des Hebels bei minimaler Leerlaufdrehzahl; B – Hebelposition bei maximaler Leerlaufdrehzahl; B – die Position der Halterung während des Betriebs; G – die Position der Halterung bei ausgeschaltetem Feed
Die Kraftstoffpumpenbaugruppe ist in Abb. dargestellt. 2.
Bei einer Hochdruck-Kraftstoffpumpe sind der Drehzahlregler 5, die Kraftstoffansaugpumpe 9 und die Dämpferkupplung 3 in einer Einheit vereint.
Aufbau und Funktionsweise der Hochdruck-Kraftstoffpumpe
Die Hochdruck-Kraftstoffpumpe besteht aus Abschnitten, separaten Pumpelementen, die in einem gemeinsamen Gehäuse untergebracht sind.
Die Anzahl der Abschnitte entspricht der Anzahl der Motorzylinder.
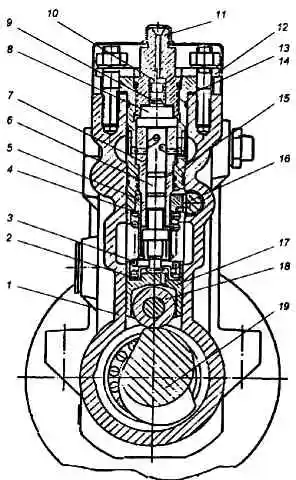
Abschnitt der Hochdruck-Kraftstoffpumpe Modell 173: 1 – Pumpengehäuse; 2 - untere Drückerplatte; 3 - Drückerfeder; 4 - obere Drückerplatte; 5 - Drehhülse; 6 - Kolben; 7 - Kolbenbuchse; 8 - Auslassventilsitz; 9 - Auslassventil; 10 - Ventilanschlag; 11 - passend; 12 - Druckflansch; 13.14 - Dichtungen; 15 - Abschnittskörper; 18 - Schiene; 17 - Drücker; 18 - Druckrolle; 19 - Nockenwelle
Die Anordnung des Hochdruckpumpenabschnitts ist in Abb. dargestellt. 3.
Im Gehäuse 1 der Pumpe sind Gehäuse aus Abschnitten 15 mit Kolbenpaaren, Auslassventilen und Anschlüssen 11 installiert, an die Hochdruck-Kraftstoffleitungen angeschlossen sind.
Auslassventil 9 und Ventilsitz 8, sowie Stößel 6 mit Hülse 7 sind Präzisionspaare, die nur im Satz ausgetauscht werden können.
Die Kolbenhülse wird durch einen in den Abschnittskörper gedrückten Stift in einer bestimmten Position arretiert.
Der Kolben 6 wird von der Nockenwelle 19 über den Rollenstößel 17 angetrieben. Die Feder 3 durch die untere Platte 2 drückt die Stößelrolle ständig gegen die Nocke
Die Drücker haben Abflachungen an den Seitenflächen und werden durch in das Pumpengehäuse eingepresste Klammern am Drehen gehindert.
Das Design des Kolbenpaares ermöglicht die Dosierung des Kraftstoffs durch Ändern der Start- und Endpunkte Futter,
Um die Menge und den Zeitpunkt des Beginns der Kraftstoffzufuhr zu ändern, wird der Kolben in der Hülse durch die Drehhülse 5 (Abb. 3) gedreht, die in die Schiene 16 eingreift.
Die Einstellung der Gleichmäßigkeit der Kraftstoffzufuhr im Maximalmodus durch jeden Abschnitt der Pumpe erfolgt durch Drehen des Abschnittsgehäuses bei gelösten Befestigungsmuttern der Abschnitte.
Die Änderung des geometrischen Einspritzbeginns in Abhängigkeit von der Fördermenge (Motorlast) erfolgt durch am Kolbenende angebrachte Steuerkanten.
Der Abschnitt funktioniert wie folgt
Wenn sich der Kolben 6 unter der Wirkung der Feder 3 nach unten bewegt, gelangt Kraftstoff unter leichtem Druck, der von der Kraftstoffansaugpumpe erzeugt wird, durch den Längskanal im Gehäuse in den Raum über dem Kolben.
Wenn sich der Kolben nach oben bewegt, gelangt Kraftstoff durch das Förderventil in die Hochdruck-Kraftstoffleitung und wird in den Kraftstoffversorgungskanal umgeleitet, bis die Endkante des Kolbens den Buchseneinlass verschließt.
Bei weiterer Aufwärtsbewegung des Kolbens steigt der Druck im Raum über dem Kolben stark an.
Wenn der Druck einen solchen Wert erreicht, dass er die von der Einspritzfeder erzeugte Kraft übersteigt, hebt sich die Einspritznadel und der Vorgang der Kraftstoffeinspritzung in den Motorzylinder beginnt.
Wenn sich der Kolben weiter nach oben bewegt, öffnen die Trennkanten des Kolbens Trennlöcher in der Buchse, was zu einem starken Abfall des Kraftstoffdrucks in der Auslassleitung führt und die Einspritznadel auf dem Verriegelungskegel des Kolbens landet Zerstäuber und Stoppen der Kraftstoffzufuhr zur Brennkammer.
Auf der Innenfläche der Hülse 7 des Kolbens befindet sich eine ringförmige Nut und in der Wand befindet sich ein Loch zum Ablassen von Kraftstoff, der durch den Spalt im Kolbenpaar ausgetreten ist.
Die Abdichtung zwischen Kolbenhülse und Sektionsgehäuse, Sektionsgehäuse und Pumpengehäuse erfolgt durch Gummiringe.
Aus dem Hohlraum um die Kolbenhülse gelangt der ausgelaufene Kraftstoff durch die Nut an der Kolbenhülse in den Niederdruckhohlraum des Pumpengehäuses und dann durch das Bypassventil und die Rohrleitung zum Kraftstofftank.
Die Nockenwelle befindet sich an der Unterseite des Kraftstoffpumpengehäuses.
Die Nockenwelle dreht sich in Kegelrollenlagern und einer Zwischenlagerung.
Die Nockenwelle wird mit einem Übermaß von 0,01–0,07 mm eingebaut, das durch die Einstellung und die zwischen dem Lagerdeckel und dem Pumpengehäuse installierten Dichtungen gewährleistet wird.
Die Abschnitte sind über eine Schiene mit dem Pumpendrehzahlregler verbunden.
Die Kraftstoffpumpenschiene bewegt sich in Führungsbuchsen, die in das Pumpengehäuse eingepresst sind. Am aus der Pumpe herausragenden Ende des Rails befindet sich ein Bolzen 10 (Abb. 2), mit dem es bei aufgesetztem Rail vor dem Starten des Motors an der Schutzkappe anliegt.
Wenn der Bolzen aus der Zahnstange entfernt wird, verringert sich der Startvorschub.
Die Schmierung der Kraftstoffpumpe erfolgt zentral über das Motorölsystem. Das Öl wird durch Boost dem Korrektor zugeführt, von wo es in den Hohlraum des Reglers gelangt und in den Hohlraum der Nockenwelle der Pumpe gelangt.
Geschwindigkeitsregler
Der Drehzahlregler 5 (Abb. 2) ist ein mechanischer All-Mode-Direktantrieb mit Overdrive-Getriebe für den Lastantrieb, der die vom Fahrer eingestellte Motordrehzahl aufrechterhält, indem er die zugeführte Kraftstoffmenge abhängig von der Drehzahl automatisch ändert Änderung der Motorlast.
Darüber hinaus begrenzt der Regler die maximale Motordrehzahl und hält den Motor im Leerlauf.
Der Regler verfügt über eine Vorrichtung zum jederzeitigen Abschalten der Kraftstoffzufuhr, unabhängig von der Motorbetriebsart. Durch die automatische Aufrechterhaltung des Drehzahlmodus bei wechselnden Lasten sorgt der Regler für einen sparsamen Betrieb des Motors.
Das Gerät des Geschwindigkeitsreglers ist in Abb. dargestellt. 4.
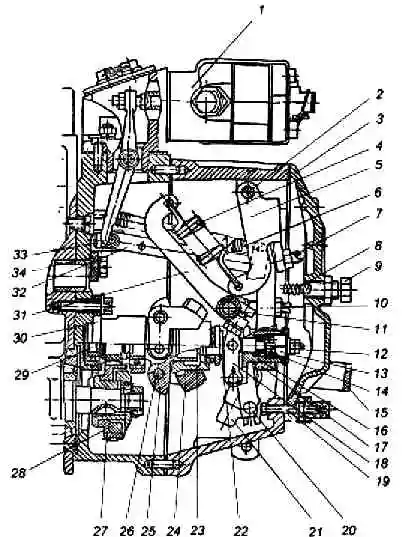
Drehzahlregler: 1 – Korrektur der Kraftstoffzufuhr; 2 - Achse des zweiarmigen Hebels; 3 - Abdeckung der Inspektionsluke; 4 - Reglerfeder; 5 - zweiarmiger Hebel; 6 - Zahnstangenhebelfeder; 7 - Schraube des zweiarmigen Hebels; 8 - Pufferfeder; 9 - Pufferfedergehäuse; 10 - Einstellschraube; 11 - Federhebelwelle; 12 - negativer Korrektor; 13 - Korrekturfedergehäuse; 4 - negative Korrekturfeder; 15 - Backstage-Halterung; 16 - negative Korrekturbuchse; 17- Reglerhebel; 18 - negativer Korrekturhebel; 19 - Leistungseinstellschraube; 20 - Schienenhebel; 21 - Flügel; 22 - Ferse; 23 - Frachtkupplung; 24 - Reglergewichte; 25 - Wareninhaber; 26 - Frachtachse; 27 - Antriebsrad; 28 - Cracker; 29 - Rollenhalterlasten; 30 - Glas; 31 - Federhebel; 32 - Zahnstangenstange; 33 - Schiene; 34 - Hervorhebung
Der Regler befindet sich am hinteren Ende der Hochdruck-Kraftstoffpumpe.
Auf einem Kegel zu Die Klauenwelle ist das Antriebszahnrad 27 mit einer Dämpfungsvorrichtung.
Die Drehung von der Pumpenwelle auf das Antriebsrad wird durch Gummicracker 28 übertragen.
Das Abtriebsrad ist einstückig mit der Welle 29 des Lasthalters gefertigt und auf zwei Lagern in der Schale 30 montiert.
Auf die Walze ist ein Gewichtshalter 25 aufgepresst (Abb. 4), auf dessen Achsen 26 sich Gewichte 24 befinden.
Die Gewichte liegen mit ihren Rollen am Ende der Kupplung 23 an, die über das Drucklager und den Absatz 22 die Kraft der Gewichte auf den Reglerhebel 17 überträgt, der zusammen mit dem zweiarmigen Hebel 5 aufgehängt ist die gemeinsame Achse 2.
Die Kupplung 23 mit dem Druckabsatz 22 in der Baugruppe ruht an einem Ende auf der Führungsfläche des Halters und ist am anderen Ende am Hebel 18 des Negativkorrektors aufgehängt, der an der Hülse 16 des Negativs befestigt ist Korrektor.
Der Absatz der Gewichtskupplung ist über die negative Korrekturbaugruppe mit dem Schienenhebel 20 und über die Stange 32 mit der Kraftstoffpumpenschiene verbunden.
Die Zahnstangenhebelfeder 6 ist oben am Zahnstangenhebel befestigt und hält die Pumpenzahnstange in der Position, die dem maximalen Durchfluss entspricht, was für eine erhöhte Kraftstoffzufuhr beim Starten des Motors sorgt.
Ein Finger wird in den unteren Teil des Zahnstangenhebels gedrückt, der in das Loch des Backstage-Schiebers 21 eindringt.
Die Welle 11 des Reglerhebels ist starr mit dem Steuerhebel 6 (Abb. 2) und dem Federhebel 31 (Abb. 4) verbunden.
Die Bewegung des Reglersteuerhebels wird durch zwei Bolzen 4 und 7 begrenzt (Abb. 2).
Am Federhebel 31 (mit kurzem Haken) (Abb. 4) und am Zweiarmhebel 5 (mit langem Haken) ist die Regulatorfeder 4 eingehängt, deren Kraft von den beiden übertragen wird. Armhebel durch die Schraube - 7 des Zweiarmhebels mit dem Reglerhebel verbinden.
In den Reglerhebel ist die Einstellschraube 10 eingeschraubt, die an der Welle des Federhebels anliegt und zur Einstellung der Nennkraftstoffzufuhr dient.
Im unteren Teil des Reglerhebels befindet sich eine Korrekturvorrichtung (12,13,14,16,18) mit negativem Korrektor, die dazu bestimmt ist, die äußere Drehzahlkennlinie der Einspritzpumpe und das Motordrehmoment zu formen.</ p>
Der Reglerhebel ist mit einem seitlichen Polster ausgestattet, das die Hülse 16 des Rückwärtskorrektors und die Schubferse 22 vor Drehung schützt.
Außerdem verhindert der in die seitliche Längsnut der Hülse eingreifende Schaft des Seitendeckelbolzens, dass dieser aus der Hebelbohrung fällt.
Der am Gehäuse des Reglers befestigte Anschlag 34 verhindert, dass sich der Federarm 31 gefährlich an rotierende Lasten annähert. Um die Kraftstoffzufuhr vollständig abzuschalten, wird ein Stoppmechanismus verwendet, der aus einer Hinterstufe 21, einer Halterung 15 und einer Rückholfeder besteht.
Im Betrieb wird der Lenker durch die Kraft der Rückstellfeder gegen die Einstellschraube 19 gedrückt.
Auf der Rückseite wird der Reglerdeckel durch einen Deckel 3 einer Inspektionsluke mit einer Puffervorrichtung verschlossen, die aus einem Körper 9 und einer Feder 8 besteht, die durch Glättung der Vibrationen des Reglerhebels 17 einen stabilen Betrieb gewährleistet der Motor im Leerlauf.
Das Funktionsprinzip des Drehzahlreglers basiert auf dem Zusammenspiel der Fliehkräfte der Gewichte und der Kräfte der Federn mit unterschiedlicher Vorspannung.
Wenn der Motor nicht läuft, befinden sich die Reglergewichte in der reduzierten Position und die Schiene 33 befindet sich unter der Wirkung der Feder 6 des Schienenhebels in der maximalen Vorschubposition (Position ganz links).
Wenn beim Starten des Motors die Kurbelwellendrehzahl 460-500 min -1 erreicht (der Steuerhebel liegt an der Schraube für die Mindestgeschwindigkeitsbegrenzung an), werden die Reglergewichte unter der Wirkung der Zentrifugalkraft belastet. Überwinden Sie den Widerstand der Zahnstangenhebelfeder und verschieben Sie den Zahnstangenhebel 32 durch die Lastkupplung 23, bis die Buchse 16 des negativen Korrektors im Reglerhebel stoppt.
Darüber hinaus bewegen die Gewichte unter Überwindung des Widerstands der Pufferfeder 8 das gesamte Hebelsystem und die Einspritzpumpenschiene nach rechts, bis der zyklische Vorschub des Einspritzpumpenabschnitts hergestellt ist, der dem Mindestgeschwindigkeitsmodus (Minimum) entspricht Leerlaufmodus).
Wenn Sie das Steuerpedal betätigen, drehen sich der Reglersteuerhebel und der damit fest verbundene Federhebel 31 um einen bestimmten Winkel, was zu einer Erhöhung der Spannung der Reglerfeder führt.
Unter dem Einfluss der Feder bewegt der Hebel 17 des Reglers das Hebelsystem, die Gewichtskupplung und die Schiene in Richtung einer Erhöhung des Vorschubs und die Motordrehzahl erhöht sich.
Dies geschieht so lange, bis die Zentrifugalkraft der Gewichte die Spannkraft der Feder 4 ausgleicht, d. h. zu einem stabilen Motorbetriebszustand.
Somit entspricht jede Position des Reglerhebels einer bestimmten Anzahl von Motorumdrehungen.
Wenn das Gesamtwiderstandsmoment gegen die Bewegung des Fahrzeugs abnimmt, erhöht sich die Motordrehzahl. In diesem Fall erhöht sich die Zentrifugalkraft der Lasten.
Die Gewichte divergieren und bewegen unter Überwindung der Kraft der Reglerfeder die Gewichtskupplung 23 und die Ferse 22.
In diesem Fall bewegen sich das Hebelsystem und die Schiene in Richtung abnehmenden Vorschubs (nach rechts), bis die Anzahl der Motorumdrehungen, die durch die Stellung des Steuerhebels gegeben ist, d. h. bis ein Gleichgewicht zwischen der Zentrifugalkraft der Gewichte und der Federkraft des Reglers herrscht.
Mit zunehmendem Gesamtwiderstandsmoment gegen die Bewegung des Fahrzeugs sinkt die Kurbelwellendrehzahl und damit auch die Zentrifugalkraft der Reglergewichte.
Mit der Kraft der Feder 4 des Reglers bewegen sich das Hebelsystem, die Ferse und die Gewichtskupplung nach links und bewegen die Schiene nach links, in Richtung der Erhöhung des Vorschubs.
Die Kraftstoffzufuhr wird abschnittsweise erhöht, bis die Motordrehzahl den durch die Position des Reglerhebels eingestellten Wert erreicht.
Der Motor wird durch Herunterdrehen des Verbindungsbügels 15 gestoppt. In diesem Fall drehen sich die Verbindung 21 und das untere Ende des Hebels 20 der Schiene nach links, die Pumpenschiene fährt in ihre äußerste Position und die Kraftstoffzufuhr stoppt.
Der negative Korrektor (12, 13, 14, 16, 18) sorgt für eine allmähliche Verringerung der zyklischen Kraftstoffzufuhr, wenn die Pumpennockenwellendrehzahl auf 500 min -1 reduziert wird, und sorgt so für einen rauchfreien Motor Betrieb.
Bei einer Kurbelwellendrehzahl, die der Nenndrehzahl entspricht, übersteigt die Zentrifugalkraft der Gewichte die Vorspannkraft der Korrekturfeder 14 und die Ferse liegt über den Korrekturhebel 12 und die Hülse 16 am Hauptreglerhebel an.
Wenn die Drehzahl der Nockenwelle der Hochdruck-Kraftstoffpumpe verringert wird, reicht die Kraft der Korrekturfeder aus, um die Kraft der Lasten zu überwinden.
Gleichzeitig bewegt sich der Korrektor 12 aus der Hülse 16 und verschiebt durch Bewegung der Gewichtskupplung und des Hebelsystems die Einspritzpumpenschiene in Richtung Reduzierung der zyklischen Kraftstoffzufuhr.
Die Rotationsfrequenz der Nockenwelle, die dem Moment entspricht, in dem der Korrektor zu arbeiten beginnt, d. h. Der Zeitpunkt des Beginns des Ausfahrens des Korrektors aus der Hülse wird durch die Vorspannung der Feder 14 reguliert.
Je niedriger die Geschwindigkeit, desto größer ist der Vorsprung des Korrektors aus der Hülse und desto größer ist der Wert der Einschränkung der zyklischen Kraftstoffzufuhr.
Bei 500 min-1 ist der Wert der zyklischen Kraftstoffzufuhrbegrenzung am größten, sein Wert wird durch den Maximalwert des Korrektorvorsprungs bestimmt.
Der Geschwindigkeitsregler ist mit einem Kraftstoffverstärkungskorrektor 1 ausgestattet, um die Wärmedichte und den Rauch in Dieselabgasen bei niedrigen Geschwindigkeiten und Übergangsbedingungen zu reduzieren.
Darüber hinaus schützt der Korrektor den Motor in Notsituationen, die bei einem Ausfall des Turboladersystems auftreten.
Das Funktionsprinzip des Ladedruckkorrektors besteht darin, dass er bei sinkendem Ladeluftdruck auf die Kraftstoffpumpenschiene einwirkt und so die Kraftstoffzufuhr verringert.
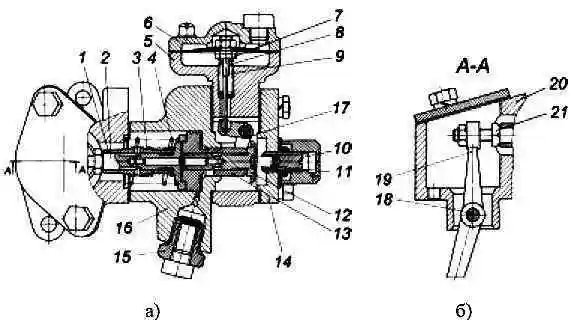
Korrektor für Boost-Kraftstoffzufuhr: a) - horizontaler Abschnitt; b) - vertikaler Abschnitt; 1 - Anschlaghülse; 2 - Betonung; 3 - Ärmelfeder; 4 - Kolbenfeder; 5 - Membrankörper; 6 - Membranabdeckung; 7 - Kontermutter der Membranstange; 8 - Frühling; 9 - Stab mit Membran; 10 - Korrekturfedergehäuse; 11 - Korrekturfeder; 12 - Spule; 13 - Kolben; 14 - Korrektorabdeckung; 15 - Ölversorgungsanschluss; 16 - Korrektorkörper; 17 - Hebel; 18 - Hebelachse; 19 - Hebel; 20 - Abstandshalter; 21 - Hebeleinstellschraube
Der Boost-Korrektor (Abb. 5) ist oben am Reglergehäuse montiert. Der Korrektorkörper 16, der Membrankörper 5 und die Korrektorabdeckung 14 sind mit Schrauben am Abstandshalter 20 befestigt.
Im Korrektorkörper befindet sich ein Paar aus Kolben 13 und Spule 12. Durch den Anschlag 2 wird der Kolben durch die Feder 4 an den Korrektorkörper gedrückt.
Auf dem Anschlag ist eine Anschlaghülse 1 montiert, die durch die Feder 3 ständig gegen den Stellbolzen 21 des Hebels 19 gedrückt wird.
Der Hebel ist auf Achse 18 in einem Distanzstück montiert.
An einem Ende des Hebels befindet sich eine Einstellschraube mit Mutter, und das andere Ende wirkt bei Betrieb des Korrektors direkt auf die Einspritzpumpenschiene.
Im Membrangehäuse befindet sich eine Membran aus Spezialgewebe, montiert mit einem Schaft 9, verschlossen mit einem Deckel 6.
Die Abdeckung verfügt über ein Loch für die Luftzufuhr vom Ansaugkrümmer des Motors.
Der auf der Achse montierte Hebel 17 dient zur Übertragung der Bewegung vom Schaft auf die Spule 12.
Die Korrekturfeder 11 liegt an der Spule an.
Um seine Vorkompression zu verändern, wird ein Federkörper 10 in den Deckel 14 des Korrektors eingeschraubt.
Eine Kontermutter und eine Kappe werden auf das Gehäuse aufgeschraubt.
Der Anschluss 15 zur Ölversorgung aus dem Motorschmiersystem ist in das Korrektorgehäuse eingeschraubt.
Die zusammenpassenden Teile des Boost-Korrektors werden mit Paronite-Dichtungen abgedichtet.
Wenn der Motor nicht läuft, herrscht kein Öldruck im Schmiersystem und keine Luft in den Ansaugkorrektoren.
Feder 4 drückt Kolben 13 mit Anschlag 2 an Korrektorkörper 16.
Richtige Feder ra 11 drückt die Spule 12 und den Schaft 9 mit der Membran bis zum Anschlag an die Membranabdeckung.
Wenn der Motor gestartet wird, beginnt Öl aus dem Motorschmiersystem durch die Schraube 15 in den Kolbenhohlraum des Korrektors zu fließen und mündet durch die offenen Ablassfenster des Kolbens in die axialen Kanäle von Spule, Kolben und Anschlag den Hohlraum des Reglers.
Wenn der Motor in den Leerlaufmodus wechselt, bewegt sich die Hochdruck-Kraftstoffpumpenschiene von der Ausgangsposition auf die Seite der Förderreduzierung.
Die Hülse 1 folgt der Schiene unter der Wirkung der Feder 3 und bewegt sich dabei, indem sie den Hebel 19 dreht.
Die Bewegung der Hülse relativ zum Anschlag führt zur Überlappung der Ablassfenster des Anschlags, wodurch der freie Abfluss stoppt und der Öldruck im Hohlraum unter dem Kolben ansteigt. und der Kolben beginnt sich nach links in seine Arbeitsposition zu bewegen.
Die Bewegung des Kolbens wird fortgesetzt, bis sich die Ablassfenster des Kolbens durch die Endarbeitskante der Spule öffnen.
Wenn der Motor unter Last läuft und die Kurbelwellendrehzahl steigt, erhöht sich der Luftdruck im Membranhohlraum.
Die Membran wird verformt, die Stange bewegt den Korrekturhebel 17, der wiederum die Korrekturspule nach rechts verschiebt.
Gleichzeitig vergrößert sich der Strömungsquerschnitt, durch den das Öl vom Hohlraum unter dem Kolben zum Axialkanal des Kolbens fließt, der Öldruck im Hohlraum unter dem Kolben nimmt ab und der Kolben, zusammen mit dem Anschlag, bewegt sich unter der Wirkung der Feder nach rechts und stellt seine Position relativ zur Spule wieder her.
Die Einspritzpumpenschiene folgt dem Kolben und dem Anschlag unter der Wirkung der Startfeder und bewegt sich.
Somit führt ein Anstieg des Luftdrucks im Membranhohlraum zu einer Erhöhung der zyklischen Kraftstoffzufuhr.
Die Bewegung der Schiene wird von der Drehung des Hebels 19 begleitet, während das Ausmaß der Bewegung der Schiene und die Änderung des zyklischen Vorschubs durch das Ausmaß der Bewegung des Kolbens und des Anschlags bestimmt werden.
Wenn die Kurbelwellendrehzahl abnimmt, sinkt der Druck des Turboladers, der Druck im Membranhohlraum nimmt ab, die Spule 12 bewegt sich unter der Wirkung der Feder 11 und der Arbeitskante der Endfläche der Spulenblöcke nach links die Ablassfenster des Kolbens.
Im Hohlraum unter dem Kolben erhöht sich der Öldruck, der Kolben bewegt sich nach links, bis sich die Ablassfenster öffnen, und durch Anschlag 2 und Hebel 19 verschiebt sich die Schiene in Richtung abnehmender Fördermenge.
Somit führt eine Änderung des Luftdrucks im Membranhohlraum zu einer Positionsänderung des Schiebers, der Kolben folgt automatisch der Position des Schiebers und sorgt für die entsprechende Bewegung des Einspritzpumpengestells.
Das Ausmaß der Zahnstangenbewegung und die Änderung des zyklischen Vorschubs werden durch den Druckabfall im Membranhohlraum und die Eigenschaften der Korrekturfeder bestimmt.
Bei einem Anstieg des Fülldrucks um etwa 0,06 MPa (0,6 kgf/cm 2) wird die Zufuhrbeschränkung durch den Korrektor aufgehoben.
Beim Stoppen des Motors schaltet der Korrektor automatisch den Startvorschub ein.
Eine Demontage des Boost-Korrektors zusammen mit dem Distanzstück 20 im Betrieb wird nicht empfohlen, da dann der Hebel 19 relativ zur Schiene falsch montiert werden kann, was zu einem Motorabstand führt.
Wenn eine Demontage erforderlich ist (z. B. während einer Reparatur), bewegen Sie bei der anschließenden Installation des Korrektors am Regler die Pumpenschiene mit der Anschlagwippenhalterung in die Auslaufposition und setzen Sie den Korrektor mit einem Abstandshalter ein in das Reglergehäuse.
Dann lassen Sie die Backstage-Klammer los. Danach ist es notwendig, die Einstellung des Ladedruckkorrektors sowie den Regler zum Abschalten der Kraftstoffzufuhr zu überprüfen.
Grundlegende Anpassungen durch das Design des Reglers
- Die minimale Leerlaufdrehzahl wird durch Bolzen 7 (Abb. 2) und Pufferfedergehäuse 9 (Abb. 4) reguliert;
- Die maximale Leerlaufgeschwindigkeit (Beginn des Zahnstangenauswurfs) wird durch Schraube 4 (Abb. 2) reguliert.
- Nennleistung (Vorschub) wird durch Schraube 10 eingestellt, eingestellt durch Schraube 19 (Abb. 4).
- Die Vorspannung der Feder (die Differenz zwischen den Umdrehungen am Ende und am Anfang des Auswurfs der Zahnstange) wird durch Schraube 7 eingestellt (Abb. 4).
- Die Kraftstoffzufuhr bei 500 min -1 wird durch die Umkehrkorrekturmutter 12 (Abb. 4) reguliert:
- Die Vorspannung der Rückwärtskorrektorfeder (die Geschwindigkeit, mit der der Korrektor zu arbeiten beginnt) wird durch den Korrektorkörper 13 (Abb. 4) reguliert.
Zu den Einstellmöglichkeiten gehört die Tatsache, dass sich der Federhebel beim Einstellen der Startgeschwindigkeit des Reglers möglichst nahe am Anschlag im Reglergehäuse befinden sollte, um eine reduzierte Kraft auf den Steuerhebel zu gewährleisten , was seine Drehung begrenzt.
Stellen Sie den Beginn der Regulatorwirkung mit der Schraube des zweiarmigen Hebels ein
Dämpferkupplung
Die Hochdruck-Kraftstoffpumpe ist mit einer Dämpferkupplung ausgestattet, die mit einem Presssitz durch die Ringmutter auf der konischen Fläche des vorderen Endes der Nockenwelle montiert und mit einer Passfeder gegen Verdrehen gesichert wird.
Die Dämpferkupplung dient zum Schutz von Mechanismen Zerstörung.
Die Dämpferkupplung ist eine nicht trennbare Konstruktion mit einem frei rotierenden Schwungrad in einer speziellen hochviskosen Flüssigkeit.
Beulen am Kupplungsgehäuse machen es unbrauchbar.