Das Schmiersystem sorgt für die Ölversorgung der Reibflächen der Teile, wodurch die Reibung zwischen ihnen und deren Verschleiß verringert werden und außerdem die Motorleistungsverluste aufgrund der Überwindung von Reibungskräften reduziert werden
Während des Motorbetriebs zirkuliert das zwischen den Teilen eingebrachte Öl ständig; Gleichzeitig kühlt es die Teile, schützt sie vor Korrosion und entfernt Verschleißprodukte.
Eine dünne Ölschicht auf den Kolben, Kolbenringen und Zylindern verringert nicht nur deren Verschleiß, sondern verbessert auch die Motorkompression.
Das Schmiersystem des KamAZ-Fahrzeugs ist kombiniert. Dies bedeutet, dass das Öl den reibenden Teilen auf verschiedene Weise zugeführt wird: durch Druck, Spritzwasser und Schwerkraft.
Unter Druck stehendes Öl wird in die Lücken zwischen den am stärksten belasteten Reibteilen gepumpt:
- - an die Haupt- und Pleuellager der Kurbelwelle, Nockenwellenlager;
- - an den Kipphebelbuchsen und den oberen Spitzen der Schubstangen;
- - zu den Lagern der Hochdruck-Kraftstoffpumpe, des Bremspneumatikkompressors und der Turbolader.
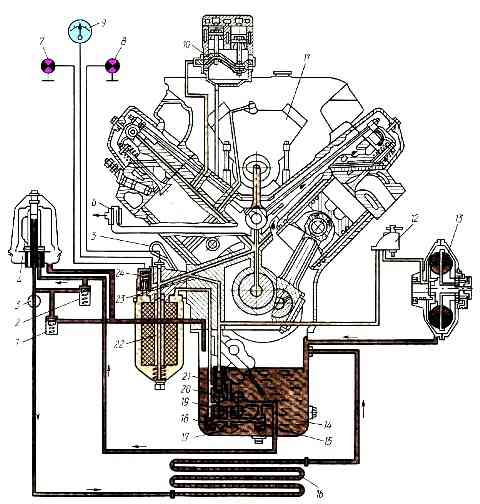
Schmiersystemdiagramm: 1 - Ablassventil des Ölkühlers; 2 - Bypassventil des Zentrifugalfilters; 3 – Ölkühlerventil; 4 - Zentrifugalölfilter (Zentrifuge); 5 - Ölstandsanzeige; 6 - Verschnaufpause; 7 - Kontrollleuchte für Verstopfung des Hauptölfilters; 8 - Warnleuchte für niedrigen Öldruck; 9 - Manometer; 10 - Kompressor; 11 - Hochdruck-Kraftstoffpumpe; 12 - Flüssigkeitskupplungsschalter; 13 - hydraulische Kupplung des Lüfterantriebs; 14 - Ölwanne; 15, 18 - Sicherheitsventile des Kühlers und Druckabschnitte der Ölpumpe; 16 - Ölkühler; 17 - Ölbehälter; 19, 20 - Kühler- und Druckabschnitte der Ölpumpe; 21 - Differentialventil des Schmiersystems; 22 - Vollstromölfilter; 23 - Hauptölleitung; 24 - Bypassventil eines Vollstromfilters mit Verstopfungsalarm
Das Schmiersystem besteht aus einer Ölpumpe, die auf der unteren Ebene des Kurbelgehäuses in der Wanne 14 (Abb. 1) installiert ist, einem Vollstromölfilter 22, einem Zentrifugalölfilter (Zentrifuge) 4, einer Ölleitung 23 mit Kanälen, Kühler 16, Öleinfüllstutzen, Ölstandsanzeige.
Der Ölbehälter ist die Ölwanne.
Durch den Hals wird Öl bis zur oberen Markierung der Füllstandsanzeige (Messstab) hineingegossen. Die untere Markierung zeigt die minimal zulässige Ölmenge an.
Der tiefe Teil der Wanne befindet sich bei KamAZ-Fahrzeugen mit der Achsfolge 6X4 im hinteren Teil des Motors, bei KamAZ-4310, -43105-Fahrzeugen im vorderen Teil des Motors. Dies ist auf die Anordnung der Fahrzeuge zurückzuführen.
Während des Motorbetriebs wird Öl aus der Ölwanne 14 von einer zweiteiligen Pumpe durch einen Siebölsammler 17 angesaugt.
Von hier aus wird ein kleinerer Teil des Öls durch die Kanäle des Kurbelgehäuses und der vorderen Abdeckung des Blocks ständig durch den Kühlerabschnitt in die Zentrifuge 4 gepumpt.
Von einer Zentrifuge gereinigtes Öl gelangt über Hahn 3 in den Kühler 16, wo es abgekühlt und dann in die Wanne abgelassen wird.
Wenn Ventil 3 geschlossen ist oder der Öldruck im Kühler auf 50-70 kPa steigt, fließt es von der Zentrifuge durch das geöffnete Ablassventil in die Wanne und umgeht den Kühler.
Der größte Teil des Öls gelangt in den Saughohlraum des Auslassabschnitts der Ölpumpe und wird über deren Zahnräder in den Hauptstromfilter 22 gefördert, wo es gereinigt wird, indem es durch zwei parallel geschaltete Filterelemente und dann hindurch gelangt Ein Kanal im Block geht in die Hauptlinie 23 ein.
Von dieser Leitung wird Öl über Kanäle in den Trennwänden und Wänden des Zylinderblocks den Hauptlagern der Kurbelwelle, den Nockenwellenlagern und den Kipphebelbuchsen des Gasverteilungsmechanismus zugeführt.
Von den Ringnuten an den Hauptlagerschalen gelangt das Öl durch die Kanäle in den Hauptzapfen und Wangen der Kurbelwelle in die Schmutzhohlräume der Pleuelzapfen, wo es einer zusätzlichen Zentrifugalreinigung unterzogen wird und dann zur Schmierung gelangt die Pleuellager.
Aus den Spalten herausgepresstes Öl wird von den rotierenden Teilen des Kurbeltriebs versprüht und es entsteht ein Ölnebel, der sich auf der Oberfläche der Zylinderlaufbuchsen, Kolben, Stößel und anderen Teilen absetzt und diese so schmiert.
Das vom Ölabstreifring von den Zylinderwänden entfernte Öl wird in den Kolben abgegeben und schmiert die Kolbenbolzenhalterungen in den Naben und das obere Kopflager der Pleuelstange.
Über Kanäle in den kurzen Armen der Kipphebel des Gasverteilungsmechanismus und in den Einstellschrauben wird Öl zu den oberen Spitzen der Stangen geleitet.
Die Stäbe hinunterfließen, Es schmiert ihre unteren Spitzen und Drücker und gelangt dann in die Pfanne.
Die Spitzen der Kipphebel und Ventilschäfte werden mit Öl geschmiert, das aus den Lücken der Kipphebelbuchsen fließt und von beweglichen Teilen versprüht wird. Anschließend wird es über geneigte Kanäle in den Hohlraum für die Stangen und dann in den Hohlraum für die Stangen abgegeben der Sumpf.
Ein Teil des Öls aus der Hauptleitung wird durch einen Kanal im Zylinderblock und Rohr in den Hohlraum der Hochdruck-Kraftstoffpumpe geleitet, schmiert deren Lager und Teile des Drehzahlreglers und gelangt dann durch das Abflussrohr Das Motorkurbelgehäuse.
Öl wird von der Hauptleitung sowohl zu den Turboladerlagern als auch zur Kurbelwelle der pneumatischen Bremskompressoren gepumpt.
Der Schalter 12 der Flüssigkeitskupplung des Lüfterantriebs wird außerdem ständig mit Öl unter Druck versorgt.
Bei geöffnetem Schalter gelangt das Öl in den Arbeitsraum der Flüssigkeitskupplung 13 und fließt von dort in die Ölwanne ab.
Der Öldruck im System wird durch Manometer 9 auf der Instrumententafel im Cockpit kontrolliert.
Darüber hinaus gibt es einen Notfall-Druckalarm.
Wenn der Druck unter 70 kPa sinkt, leuchtet die rote Lampe 8 am Manometer auf. In diesem Fall muss der Motor abgestellt und die Ursache der Störung ermittelt werden.
Die Lampe 7 dient dazu, zu signalisieren, dass die Filterelemente des Ölfilters 22 stark verstopft sind.
Das konstante Leuchten dieser Lampe zeigt an, dass sich das Bypassventil geöffnet hat und ungereinigtes Öl unter Umgehung der Filterelemente in die Hauptleitung gelangt.
Das kurzzeitige Aufleuchten der Warnleuchte 7 (bis der Motor warm ist) ist zulässig; wenn sie ständig leuchtet, müssen die Filterelemente ausgetauscht werden.
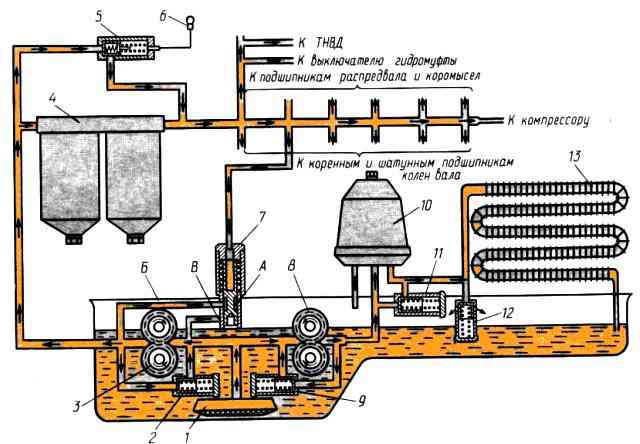
Ventile des Schmiersystems: 1 – Ölbehälter; 2, 9 - Sicherheitsventile der Auslass- und Kühlerabschnitte; 3, 8 - Auslass- und Kühlerabschnitte der Ölpumpe; 4 - Vollstromölfilter; 5 - Bypassventil mit Verstopfungsanzeige; 6 - Kontrollleuchte für Verstopfung des Hauptölfilters; 7 - Differentialventil des Schmiersystems; 10 - Zentrifugalölfilter; 11 - Zentrifugen-Bypassventil; 12 - Zentrifugenablassventil; 13 - Ölkühler
Schmiersystemventile. Unter einem bestimmten Druck wird den reibenden Teilen Öl zugeführt.
Ist dies nicht ausreichend, kommt es aufgrund einer Verringerung der Strömungsgeschwindigkeit in den Zwischenräumen zu einer Auswaschung von Verschleißprodukten aus diesen und zu einer Verschlechterung der Teilekühlung.
Übermäßiger Druck erhöht die Belastung der Baugruppen des Schmiersystems und den Energieverbrauch zum Antrieb der Ölpumpe.
Der Öldruck in der Leitung hängt von der Kurbelwellendrehzahl, der Öltemperatur, dem Verschleißgrad der Teile, dem Widerstand von Ölfiltern, Kühlern usw. ab.
Um sicherzustellen, dass der normale Betrieb nicht durch Änderungen dieser Faktoren gestört wird, ist das System mit automatisch arbeitenden Kolbenventilen ausgestattet.
Es gibt insgesamt sechs davon: drei für die Ölpumpe – Sicherheitspumpen und zwei (Abb. 2) für den Kühler- bzw. Auslassbereich und Ventil 7; für eine Zentrifuge – Ablassventil 12 und Bypassventil 11 und ein Bypassventil 5 für einen Vollstrom-Ölfilter.
Ventil 7 ist erforderlich, um den normalen Öldruck (400–550 kPa) in der Hauptleitung eines warmen Motors aufrechtzuerhalten.
Nach dem Funktionsprinzip ist das Differentialventil ein Kolben mit einer Ringnut "A".
Auf der einen Seite wird es durch die Kraft des Öldrucks aus der Hauptleitung und auf der anderen Seite durch eine Feder belastet.
In diesem Fall stört die direkt vom Druckabschnitt der Ölpumpe über Kanal "B" auf die Nut "A" übertragene Druckkraft das Gleichgewicht nicht, da sie auf die flächengleichen Endflächen der Nut wirkt .
Wenn der Druck in der Hauptleitung den zulässigen Grenzwert überschreitet, bewegt sich das Ventil unter Überwindung des Federwiderstands und die Nut "A" verbindet die Kanäle "B" und "C", wodurch das Öl austritt von der Pumpe fließt ungehindert durch Kanal "B" in den Sumpf.
Das Bypassventil 5 wird aktiviert, wenn die Filterelemente des Hauptstromfilters 4 verstopft sind.
Auf das Ventil 5 wirkt einerseits die Druckkraft des Rohöls, andererseits die Druckkraft des gereinigten Öls und die Kraft der Feder, angepasst an die Druckdifferenz (Differenz). vor und nach dem Filter, gleich 250–300 kPa.
Wenn der Filterwiderstand den Druckabfallwert überschreitet, öffnet sich das Ventil und ein Teil des Öls wird unter Umgehung des Filters in die Hauptleitung geleitet.
Somit wird bei Aktivierung des Bypassventils eine Notschädigung des Motors verhindert, gleichzeitig erhöht sich jedoch der Verschleiß der Teile durch die Zufuhr von unreinem Öl.
Damit der Fahrer dies weiß, befindet sich im Bypassventil eine Kontaktvorrichtung ein Gerät, das dafür sorgt, dass die Lampe 6 auf der Instrumententafel im Cockpit eingeschaltet wird und anzeigt, dass der Motor mit unreinem Öl läuft.
Sicherheitsventile 2 und 9 verhindern einen übermäßigen Druckanstieg durch die Ölpumpenabschnitte, deren Durchfluss mit einer Reserve für den Betrieb bei reduzierter Drehzahl, mit heißem Öl und einem gewissen Motorverschleiß berechnet wird .
Auf der Druckseite des Ventils wirkt die Öldruckkraft auf das Ventil, auf der gegenüberliegenden Seite wirkt die Federkraft.
Wenn die Druckkraft den Federwiderstand überschreitet (z. B. beim Pumpen von kaltem Öl beim Starten eines kalten Motors), öffnet sich das Ventil und gibt überschüssiges Öl in den Saughohlraum ab, wodurch die Belastung der Pumpenteile verringert wird.
Um den normalen Betrieb der Zentrifuge zu gewährleisten, ist ein ausreichend hoher Druck des in die Zentrifuge eintretenden Öls erforderlich. Daher wird das Bypassventil 11 auf einen Öffnungsdruck von 600–650 kPa eingestellt.
Um dünnwandige Ölkühlerrohre vor Zerstörung zu schützen, muss der Öldruck in seiner Leitung deutlich niedriger sein, sodass das Ablassventil 12 bei einem Druck von 50-70 kPa öffnet.