Ersatz des pneumatischen Kraftverstärkers durch hydraulischen Kupplungsantrieb
Wir tauschen die PGU bei auftretenden Störungen aus:
- - Blockieren des Kupplungsantriebs (bei einwandfrei funktionierendem Kupplungsgeberzylinder und Kupplungsmechanismus);
- - Erhöhung der Kraft auf das Kupplungspedal – kein Gewinn (bei entlüftetem Kupplungshydraulikantrieb und wartungsfähigem Hauptzylinder und Kupplungsmechanismus);
- - mechanische Beschädigung des pneumatischen Verstärkergehäuses, die den normalen Betrieb beeinträchtigt
Pneumatischen Kupplungskraftverstärker ausbauen
Wir bereiten das Auto vor und lassen die Luft aus dem Verbraucherkreislauf ab
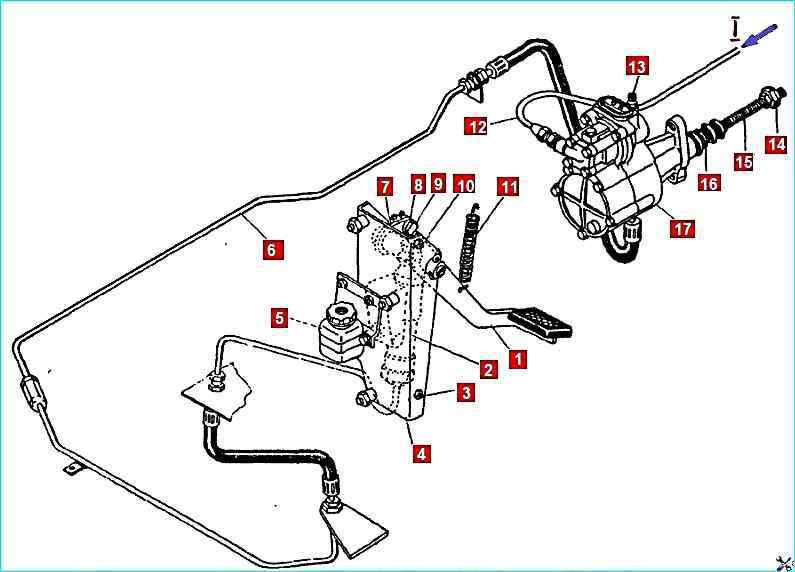
Antrieb des Kupplungsmechanismus: 1 - Pedal; 2 - Hauptzylinder; 3, 10 - Haltestellen; untere und obere; 4 - Klammer; 5 - Ausdehnungsgefäß; 6 - Hydraulikleitung; 7 - Hebel; 8 - Kolbenschieber; 9 - exzentrischer Finger; 11 - Entriegelungsfeder; 12 - Rohrleitung; 13 - Luftablassventil; 14 - sphärische Einstellmutter; 15 - pneumatischer Verstärkerkolbendrücker; 16 - Schutzhülle; 17 - PGÜ; I - Druckluft
Entfernen Sie die Ausrückfeder 11 des Ausrückgabelhebels der Kupplung
Die pneumatische Leitung 12 des pneumatischen Kupplungsverstärkers abklemmen
Hydraulikleitung 6 abtrennen und Flüssigkeit aus dem Kupplungshydraulikantrieb ablassen
Die beiden Befestigungsschrauben des pneumatischen Verstärkers lösen, den Drücker 15 vom Hebel lösen, herausnehmen und den pneumatischen Verstärker und die Federhalterung entfernen
Einbau eines pneumatischen Kupplungskraftverstärkers
Wir setzen den 15-Kolben-Schieber in den pneumatischen Verstärker ein und stecken das andere Ende in das Loch im Ausrückgabelwellenhebel
Wir richten die Löcher des pneumatischen Verstärkers mit den Löchern des Kupplungsgehäuses aus und befestigen sie mit zwei Schrauben. Anzugsdrehmoment der Schraube 53,9–58,9 Nm (5,5–6,0 kgfm)
Hydraulikleitung 6 anschließen
Anschluss der pneumatischen Rohrleitung
Installieren Sie die Ausrückfeder 11 des Ausrückgabelwellenhebels der Kupplung
Starten Sie den Motor und füllen Sie das pneumatische System mit Luft. Der Druck im System sollte mindestens 637 kPa (6,5 kgf/cm 2) betragen.
Füllen Sie Flüssigkeit durch die obere Öffnung mit zurückgeklappter Schutzabdeckung in den Vorratsbehälter des Hauptzylinders und entlüften Sie das hydraulische Antriebssystem.
Wir prüfen optisch die Dichtheit von Rohrleitungsverbindungen und beseitigen bei Bedarf das Leck
Leerweg des Ausrückhebels einstellen
Reparatur eines pneumatischen Kraftverstärkers mit hydraulischem Kupplungsantrieb
Demontage des pneumatischen Verstärkers
Wir montieren den pneumatischen Verstärker in einem Schraubstock und klemmen das hintere Gehäuse 55 mit den Backen fest
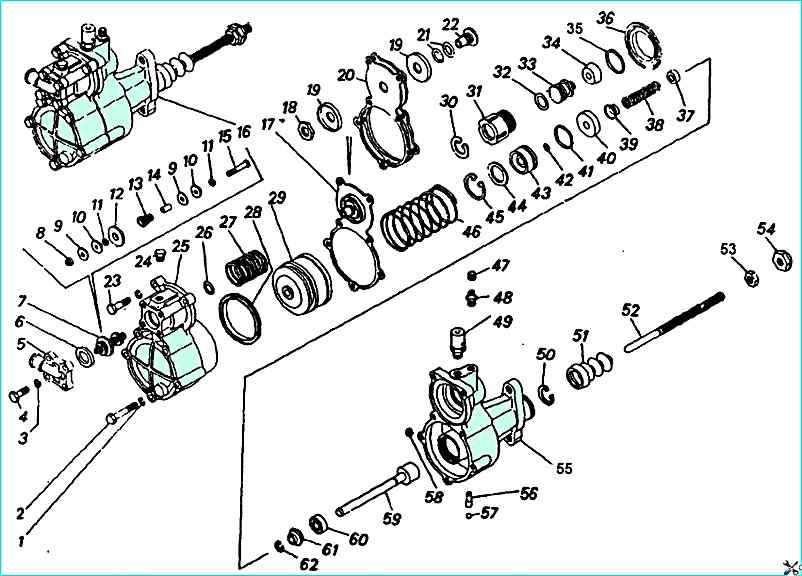
Pneumatisch-hydraulischer Verstärker des Kupplungssteuerantriebs: 1; 3 - Federscheiben; 2, 4, 23 - Bolzen; 8 - Abdeckung; 6 - Einstelldichtung; 7 - Ventilbaugruppe; 8 - Stangenmutter; 9, 11, 19, 44 - Unterlegscheiben; 10 - Kegel; 12, 22 - Sättel; 13, 27, 46 - Federn; 14 - Röhre; 15 Stange; 16 - montierte PGU; 17 - Membran; 18, 53 - Nüsse; 20 Blende; 21 - Sattelgabel; 24 Vorderer Gehäusestecker; 25 - Vorderes Gehäuse der PGU; 26; 32; 35; 41; 42 Dichtringe; 28, 34 - Manschetten; 29, 33, 59 - Kolben; 30 - Ring; 31 - Körper; 36 - Buchse; 37 - Druckbuchse; 38 - Distanzfeder; 39, 61 - Distanzhülse; 40; 60 - montierte Manschetten; 43 - Dichtungsgehäuse; 45; 62 - Druckringe; 47 - Kappe; 48 - Ventil; 49 - Entlüfter mit Ventilen in Baugruppe; 50 - Sicherungsring; 51 - Fall; 52 - Drücker; 54 - Nuss; 55 - hintere Karosserie; 56 - Düsenflugzeug; 57 - Ball; 58 - Sattel
Schrauben 4 mit Unterlegscheiben 3 lösen und Deckel 5 der Luftzufuhr abnehmen
Wir entfernen das Ventil 7 der Verstärkerbaugruppe vom Vordergehäuse des pneumatischen Verstärkers
Schrauben 2 und 23 mit Unterlegscheiben 1 lösen und das Vordergehäuse 25 zusammen mit dem pneumatischen Kolben 29 abnehmen
Entfernen Sie die 27 Membranfeder und die 46 pneumatische Kolbenfeder
Entfernen der Membran 17 der pneumatischen Verstärkerbaugruppe
Wir schrauben den Folgekolben 33 mit dem Gehäuse 31 vom hinteren Gehäuse 55 des Verstärkers ab
Wir entfernen den Druckring 45 und den Kolben 59 der Kupplungsausrückeinheit vom hinteren Gehäuse 55 des Verstärkers und dem Gehäuse 43 der Dichtung
Das Bypassventil 48 des hinteren Gehäuses zusammen mit der Kappe 47 abschrauben und entfernen
Schrauben Sie den Entlüfter 49 ab, der die Abdeckung der Auslassöffnung befestigt, entfernen Sie die Abdeckung und die Dichtung der Auslassöffnung des pneumatischen Verstärkers
Entfernen Sie das hintere Gehäuse des pneumatischen Verstärkers aus dem Schraubstock
Wir nehmen den Sicherungsring 50 des hinteren Verstärkergehäuses heraus
Mutter 8 des Ventilschafts 15 abschrauben
Unterlegscheibe 9 vom Ventilschaft 15 entfernen groß, Kegel 10, kleine Scheibe 11, Ventilsitz 12, Feder 13, Rohr 14, große Scheibe 9, Kegel 10 und kleine Scheibe 11 des Ventils
An einer Stelle entriegeln und die Mutter 18 der Reduziermembran abschrauben
Vom Sitz 22 die Unterlegscheibe 19, die Membran 20 und die Einsätze 21 entfernen
Dichtring 35 vom Körper 31 des Folgekolbens entfernen
Wir entfernen den Druckring 30 und den Folgekolben 33 aus dem Gehäuse 31
Den Dichtring 32 und die Manschette 34 vom Kolben 33 entfernen
Unterlegscheibe 44 vom Kupplungsausrückkolben 59, Kolbendichtungsgehäuse 43 komplett mit Dichtringen 41 und 42, Kolbendichtungsmanschette 40, Feder 38, Distanzhülse 39, Anlaufring 62, Hülse 61 und Manschette 60 entfernen
Wir entfernen aus dem Vordergehäuse 25 den pneumatischen Kolben 29 in Baugruppe und den Dichtring 26
Entfernen Sie die Manschette 28 vom pneumatischen Kolben 29
Wir waschen die pneumatischen Verstärkerteile, blasen sie mit Druckluft aus und überprüfen den technischen Zustand
Überprüfung der pneumatischen Verstärkerteile
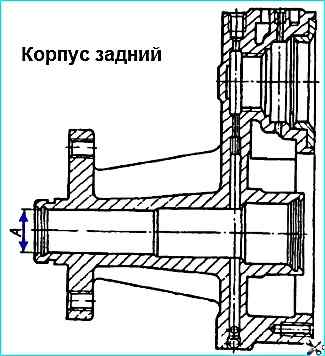
Auf der Arbeitsfläche „A“ des Gehäuses dürfen keine Spuren von Korrosion, Graten oder Kerben am hinteren Gehäuse vorhanden sein; der Durchmesser „A“ beträgt mehr als 28,06 mm.
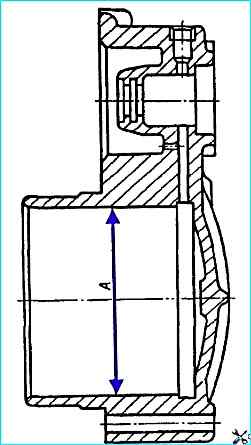
Folgendes ist auf der Vorderseite des Körpers nicht zulässig:
- - Grate, Dellen, Kerben der Arbeitsfläche „A“ des Körpers;
- - Durchmesser „A“ beträgt mehr als 90,2 mm.
Folgendes ist an Manschetten und Dichtringen nicht erlaubt:
- - Verschleiß und Aufquellen von Manschetten und Dichtringen;
- - Brüche und Risse an Arbeitskanten
Die Auslassdichtung darf keine Alterungserscheinungen (Risse, Brüche, Elastizitätsverlust) aufweisen
Die Membran darf keine Risse, Brüche oder Elastizitätsverluste aufweisen
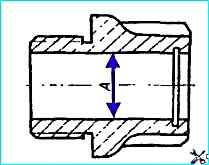
Folgendes ist am Folgekolbenkörper nicht zulässig:
- - Kerben, Grate, Dellen auf der Arbeitsfläche „A“;
Durchmesser „A“ ist größer als 28,06 mm
Zusammenbau des pneumatischen Verstärkers
Wir montieren die Manschette 28 auf dem pneumatischen Kolben 29 (Abb. 2)
Fett 158 in die Kolbennut 29 auftragen
Den Dichtring 26 und den pneumatischen Kolben 29 montieren wir im Zusammenbau in das Vordergehäuse 25
Wir montieren den Dichtring 42 in das Gehäuse 43
Hinweis: Von hier an müssen die Dichtungsringe und Manschetten vor dem Einbau mit NG-213-Flüssigkeit geschmiert werden.
Wir setzen die Dichtringe 41 und 42 auf das Gehäuse 43
Wir montieren auf dem Kolben 59 des Ausrückers die Manschette 60, die Buchse 61 als Distanzstück, den Druckring 62, die Druckbuchse 37, die Feder 38 als Distanzstück, die Buchse 39 als Distanzstück, die Manschette 40, das Gehäuse 43 des die Kolbendichtung in Baugruppe mit den Dichtringen 41 und 42 und der Unterlegscheibe 44 Dichtungsgehäuse
Wir setzen den Folgekolben 33 bei der Montage in das Gehäuse 31 ein
Wir montieren den Druckring 30 in den Körper 31 des Folgekolbens
Wir legen den Dichtring 35 auf das Gehäuse 31
Wir montieren auf dem Sitz 22 Membraneinsätze 21, eine Unterlegscheibe 19, zwei Membranen 20 und dann noch eine Unterlegscheibe 19
Mutter 18 der Membranbefestigung festziehen
Kontern Sie die 18 Membranbefestigungsmutter
Kontern Sie die Mutter 18, indem Sie den Rand der Mutter an einer Stelle in die Nut drücken
Wir setzen auf den Schaft 15 des Verstärkerventils die kleine Unterlegscheibe 11, den Kegel 10, die große Unterlegscheibe 9, das Rohr 14 des Ventilschafts, die kleine Unterlegscheibe 11, den Kegel 10, die große Unterlegscheibe 9 und Mutter festziehen 8
Wir montieren den Sicherungsring 50 in das hintere Gehäuse 55 des Verstärkers
Installieren Sie das hintere Gehäuse 55 in einem Schraubstock
Entlüfter einschrauben 49
Wir montieren und ziehen das Bypassventil 48 zusammen mit der Kappe 47 fest
Wir montieren den Kupplungsausrückkolben im hinteren Gehäuse des 55er Boosters
Wir montieren den Druckring 45 in das montierte hintere Gehäuse 55 des Verstärkers
Wir schrauben den Folgekolben 33 des Verstärkergetriebes mit dem Gehäuse 31 im Zusammenbau in das hintere Gehäuse 55
Einbau der Feder 46 des pneumatischen Kolbens
Wir installieren Feder 27 und Membran 17 der Verstärkergetriebebaugruppe im Frontgehäuse 25 und richten dabei die Membranlöcher mit den Löchern im vorderen Verstärkergehäuse aus.
Wir montieren das vordere Gehäuse des 25-Verstärkers auf das hintere Gehäuse des 55-Verstärkers, schrauben die Schrauben 2 und 23 der Befestigung mit Federscheiben 1 ein
Wir installieren Dichtungen 6 und Ventil 7 des Verstärkers bei der Montage in das Frontgehäuse 25 des Verstärkers
Hinweis: Beim Einbau des Ventils ist eine Gewichtsanpassung mittels 6 Unterlegscheiben erforderlich der ursprüngliche Spalt (2 +0,5 mm) zwischen Reduzierventil und Membransitz. Es muss mindestens eine Dichtung vorhanden sein.
Wir montieren die Luftzufuhrabdeckung 5 am Frontgehäuse 25 des Verstärkers, richten die Löcher aus und schrauben die Befestigungsschrauben 4 mit Federscheiben 3 ein
Entfernen der pneumatischen Verstärkerbaugruppe aus dem Schraubstock
Prüfen des pneumatischen Verstärkers auf Dichtheit und Funktion
Wir führen die Prüfung auf einem nach dem Diagramm hergestellten Ständer durch

Testdiagramm des pneumatisch-hydraulischen Kupplungskraftverstärkers: 1 - pneumatisch-hydraulischer Kraftverstärker; 2, 4, 6 - Druckmessgeräte; 3, 8, 9, 15 - Wasserhähne; 5 - Druckluftbehälter; 7 - Steuerzylinder mit Bremsflüssigkeit; 10 - Pumpe; 11 - Panzer; 12 - Rohrleitung; 13, 14 - Bypassventil
Vor der Prüfung muss das Hydrauliksystem mit Bremsflüssigkeit befüllt werden.
Füllen Sie die Bremsflüssigkeit ein und entlüften Sie die Bremsflüssigkeit mithilfe der Pumpe 10, des Behälters 11 und des am pneumatischen Verstärker installierten Bypassventils 14.
Bei laufender Pumpe 10 ist es notwendig, das Bypassventil 3-4 Sekunden lang um 0,5 Umdrehungen aufzuschrauben.
Gleichzeitig entweicht Luft aus dem Hydrauliksystem durch Rohrleitung 12 in Tank 11. Nachdem die gesamte Luft entwichen ist, schließen Sie das Bypassventil.
Gleichzeitig wird über Pumpe 10 und Hahn 9 der Steuerzylinder mit Arbeitsflüssigkeit gefüllt
Wir prüfen das Hydrauliksystem des Boosters mithilfe des Steuerzylinders 7 auf Dichtheit. In diesem Fall muss das Ventil 15 des pneumatischen Systems geschlossen sein (es darf keine Luft im pneumatischen System sein)
Bei der Dichtheitsprüfung der Hydraulikanlage muss der Anschlag „q1“ starr fixiert sein. In diesem Fall muss die Last „q“ einen Druck im Hydrauliksystem des Verstärkers von 5,8 MPa (60 kgf/cm 2) gemäß dem Druckmesser 6
erzeugen.
Bei der Prüfung darf keine Bremsflüssigkeit durch die Dichtungen in den Bremskraftverstärkerelementen austreten.
Der Kolben des Steuerzylinders 7 muss unter der Einwirkung der Last „q“ eine Minute lang stillstehen
Die Dichtheitsprüfung der pneumatischen Anlage erfolgt über einen Druckluftbehälter 5.
Während des Tests muss Tank 5 einem Luftdruck von 687 kPa (7 kgf/cm 2) ausgesetzt sein und Ventil 3 muss geschlossen sein.
Wenn Ventil 15 geöffnet ist, darf keine Luft durch den Verstärkerreduzierer entweichen.
In diesem Fall sollte der Luftdruck im Behälter 5, der durch Druckmesser 4 kontrolliert wird, während einer Minute der Abnahmeprüfung nicht abfallen.
Der Leistungstest wird im Zusammenspiel aller Elemente des pneumatischen Verstärkers durchgeführt.
Zur Überprüfung der Prüfungen am Anschlag (q1) muss ein Leistungsprüfstand installiert werden.
Die Last q muss drei Werte A 1, A 2, A 3 haben, wodurch der Druck im Hydrauliksystem des Verstärkers (P) 784, 1156, 1569 kPa (8, 12 und 16 kgf/cm 2) .
Der dem pneumatischen System während der Prüfung zugeführte Luftdruck darf nicht unter 589 kPa (6 kgf/cm 2) fallen.
Bei Belastung des Steuerzylinders 7 mit einer Last (q) gemäß den drei oben genannten Werten sollte die Kraft auf die Schubstange dem Diagramm entsprechen
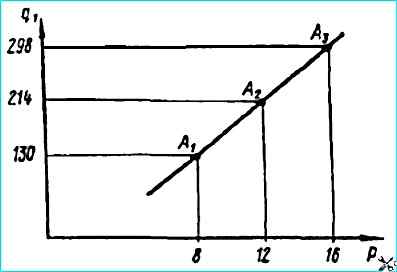
Wenn Sie jeden im Diagramm angegebenen Punkt 15 Sekunden lang festhalten, dürfen sich die Messwerte der Druckmesser 2 und 6 des Dynamometers nicht ändern.