Der Zylinderblock und der Zylinderkopf erfordern keine Wartung, außer der Reinigung von Staub und Schmutz und dem Festziehen der Gewindeverbindungen
Im Laufe der Zeit wird die Zylinderkopfdichtung verbeult, so dass es möglich ist, dass sich die Kopfmuttern lösen, die Dichtung durchbrennt und Gase austreten können. Daher muss der Zylinderkopf während des Betriebs alle 20.000 km nachgezogen werden das Fahrzeug.
Die Muttern der Zylinderkopf-Befestigungsbolzen werden von der Mitte des Kopfes bis zu den Enden (vorne und hinten) angezogen.
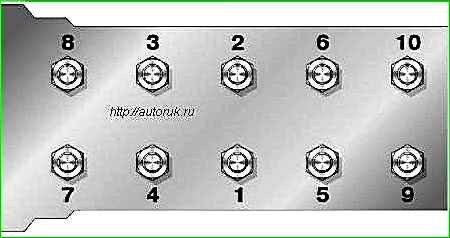
Das Anziehen und Überprüfen der Anzugsdrehmomente sollte bei kaltem Motor erfolgen.
Wenn dieser Vorgang an einem heißen Motor durchgeführt wird, ist das Anziehen der Muttern nach dem Abkühlen aufgrund des großen Unterschieds in den linearen Ausdehnungskoeffizienten des Materials von Kopf, Block und Stehbolzen unvollständig.
Für einen gleichmäßigen und festen Sitz des Kopfes am Block sollte das Anziehen in zwei Schritten erfolgen: zunächst mit geringer Kraft und schließlich mit einem festgelegten Drehmoment von 83–90 Nm (83–9,0 kgcm).
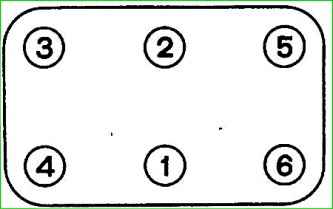
Es ist zu beachten, dass sich durch das Anziehen der Muttern die Abstände im Gasverteilungsmechanismus ändern. Deshalb ist es nach jedem solchen Vorgang notwendig, die Größe der Lücken zwischen den Kipphebeln und den Ventilschäften zu überprüfen.
Gegebenenfalls müssen die thermischen Abstände angepasst werden. Um einen festen und gleichmäßigen Sitz der Ventildeckeldichtung am Zylinderkopf zu gewährleisten, sollten die Befestigungsschrauben des Ventildeckels in der in der Abbildung gezeigten Reihenfolge angezogen werden.
Während des Betriebs eines Motors, insbesondere eines verschlissenen Motors, dessen Ringe viel Öl austreten, bildet sich eine Rußschicht an den Wänden des Brennraums und den Kolbenköpfen.
Ruß beeinträchtigt die Wärmeübertragung durch die Wände in das Kühlmittel, was zu lokalen Überhitzungen, Detonationen und Glühzündungserscheinungen führt, die Motorleistung sinkt und der Kraftstoffverbrauch steigt.
Wenn solche Anzeichen auftreten, entfernen Sie den Kopf und reinigen Sie die Brennkammer und den Kolbenboden von Kohlenstoffablagerungen.
Vor der Reinigung sollten die Kohlenstoffablagerungen mit Kerosin befeuchtet werden. Dies verhindert das Versprühen von Kohlenstoffablagerungen und verhindert, dass giftiger Staub in die Atemwege gelangt.
Ruß entsteht auch im Langzeitbetrieb bei geringer Belastung eines funktionstüchtigen, ungetragenen Motors.
In diesem Fall brennt der Kohlenstoff bei längerer Bewegung mit hoher Geschwindigkeit aus.
Beim Ausbau des Zylinderkopfes empfiehlt es sich, die Ventile abzuschleifen.
Während des Betriebs ist es alle 20.000 km des Fahrzeugs erforderlich, den Spalt zwischen den Ventilen und Kipphebeln zu überprüfen und einzustellen. Dies sollte bei kaltem Motor (+20° C) und festgezogenen Zylinderkopf-Befestigungsmuttern und Kipphebel-Befestigungsmuttern erfolgen.
Der thermische Spalt zwischen den Kipphebeln und den Ventilen sollte zwischen 035 und 045 mm liegen.
Bei vergrößertem Spiel kommt es zum Klopfen des Ventils, und bei verringertem Spiel sitzt das Ventil möglicherweise nicht fest am Sitz und das Ventil kann durchbrennen. Daher sollten die oben genannten Spielwerte auch bei etwas Klopfen nicht verringert werden. Dies ist zwar unangenehm für das Ohr, stört jedoch nicht den normalen Betrieb des Motors.
Überprüfen und stellen Sie die thermischen Abstände in der folgenden Reihenfolge ein:
- - Stellen Sie den Kolben des 1. Zylinders auf den oberen Totpunkt des Kompressionshubs. Drehen Sie dazu die Kurbelwelle mit einem Spezialschlüssel und richten Sie die dritte Markierung am Dämpferteil der Kurbelwellenriemenscheibe mit der Anzeigerippe am Steuerraddeckel aus.
Während des Kompressionshubs sollten beide Kipphebel des 1. Zylinders frei auf ihren Achsen schwingen, d. h. beide Ventile sind geschlossen.
Überprüfen Sie den Spalt zwischen Kipphebel und Ventil mit einer Fühlerlehre.
Wenn der Spalt falsch ist, schrauben Sie die Mutter der Einstellschraube mit einem Schraubenschlüssel ab und drehen Sie die Einstellschraube mit einem Schraubendreher, um den Spalt entsprechend der Fühlerlehre einzustellen.
Halten Sie die Einstellschraube mit einem Schraubendreher fest, kontern Sie sie mit einer Mutter und prüfen Sie das korrekte Spiel;
- - Drehen Sie die Kurbelwelle eine halbe Umdrehung und stellen Sie das Spiel für den 2. Zylinder ein;
- - Drehen Sie die Kurbelwelle um eine weitere halbe Umdrehung und stellen Sie das Spiel für den 4. Zylinder ein;
- - Drehen Sie die Kurbelwelle um eine weitere halbe Umdrehung und stellen Sie das Spiel für den 3. Zylinder ein.
Beim Betrieb des Fahrzeugs sollten Sie täglich den Ölstand im Kurbelgehäuse und die Dichtheit des Schmiersystems prüfen.
Alle 10.000 km des Fahrzeugs sollte das Öl im Schmiersystem und im Filter gewechselt werden Ölfilterelement, spülen Sie das Schmiersystem rechtzeitig und beseitigen Sie eventuelle Undichtigkeiten in den Verbindungen der Teile.
Der Ölstand wird bei nicht laufendem Motor anhand der Markierungen am Anzeigestab überprüft.
Es wird empfohlen, den Ölstand in der Nähe der „P“-Markierung zu halten.
Eine Erhöhung des Füllstands über die Markierung „P“ ist unerwünscht, da die Kurbelköpfe der Pleuel in Öl eintauchen und dieses verspritzen, was zur Bildung von übermäßigem Ölnebel im Kurbelgehäuse führt.
Dies führt zu Spritzern der Zündkerzen, starker Kohlenstoffablagerung an den Kolbenköpfen und Wänden der Brennkammer, Verkokung der Ringe, Rauchen des Motors und erhöhtem Ölverbrauch.
Es ist gefährlich, den Ölstand unter die Min-Marke zu senken, da dadurch die Ölzufuhr zum System unterbrochen wird und die Lager schmelzen können.
Der Ölstand sollte einige Minuten nach dem Auffüllen oder Abstellen des Motors überprüft werden.
Nach dem Ölwechsel müssen Sie den Motor starten und einige Minuten laufen lassen.
Überprüfen Sie nach einiger Zeit den Ölstand wie oben angegeben.
Sie müssen das Öl zum Austauschen nur ablassen, wenn der Motor heiß ist. In diesem Fall hat das Öl eine geringere Viskosität und läuft gut ab.
Beim Ölwechsel sollten Sie auch die Ablagerungen aus dem Ölfilter ablassen, die Innenfläche des Gehäuses und der Stange reinigen und das Filterelement wechseln.
Das Filterelement muss vor dem Einbau in sauberes Motoröl eingeweicht werden. Um einen festen Sitz des Filterdeckels zu gewährleisten, wird empfohlen, ihn zusammen mit der Dichtung an der gleichen Position zu platzieren, an der er sich vor dem Entfernen befand.
Ziehen Sie die Abdeckungsschraube nicht zu fest an, da dies zu einer Verformung der Abdeckung führen kann.
Die Dichtheit der Abdeckung wird nach dem Starten des Motors überprüft.
Um zu verhindern, dass ungefiltertes Öl in den Motor gelangt, müssen die Gummidichtringe des Filterelements elastisch sein und dürfen sich nicht verformen.
Wenn Sie den Motorbetrieb auf eine andere Ölmarke umstellen, muss das Schmiersystem mit frischem Öl der Marke gespült werden, die zum Schmieren des Motors verwendet wird.
Dazu müssen Sie das Altöl aus dem Kurbelgehäuse eines warmen Motors ablassen, Spülöl 2-4 mm über der Min-Markierung an der Ölstandsanzeige einfüllen, den Motor starten und 15 Minuten laufen lassen.
Im Leerlaufbetrieb bei niedriger Drehzahl den Motor abstellen, das Öl aus dem Kurbelgehäuse ablassen, das Filterelement austauschen und frisches Öl einfüllen.
Füllen Sie während des Betriebs nur Öl der Marke nach, die auch in den Motor eingefüllt wird.
Um das Kurbelgehäuseentlüftungssystem zu warten, müssen Sie:
- - Luftfilter und Kurbelgehäuseentlüftungsschläuche entfernen;
- - Entfernen Sie die Kipphebelabdeckung und den Vergaser;
- - Mit Kerosin spülen und Luft durch die Kipphebelabdeckung und die Schläuche blasen;
- - Reinigen Sie das kalibrierte Loch 50 im Gehäuse der Mischkammern mit Kupferdraht mit einem Durchmesser von 1,5 mm;
- - Stellen Sie bei der Montage sicher, dass alle Verbindungen dicht sind.
Während des Betriebs sollte der Betrieb nicht mit geöffnetem Öleinfüllstutzen erfolgen: Dies führt zum Eintritt ungereinigter Luft in den Motor und führt zu erhöhtem Verschleiß von Motorteilen.
Um die korrekte Montage und den normalen Betrieb des Kurbelgehäuseentlüftungssystems zu überprüfen, muss der Schlauch, der die Kurbelgehäusegase zum Vergaser liefert, bei laufendem Motor mit minimaler Leerlaufdrehzahl abgeklemmt werden.
Wenn die Motordrehzahl plötzlich abfällt oder der Motor abgewürgt wird, funktioniert das System normal.
Kühlsystempflege – besteht aus der täglichen Überprüfung des Kühlmittelstands im Ausgleichsbehälter.
Der Flüssigkeitsstand sollte bei kaltem Motor nicht unter der MIN-Marke liegen.
Die MIN-Markierung befindet sich an der Wand des Ausgleichsbehälters.
Füllen Sie bei Bedarf Kühlmittel in den Ausgleichsbehälter. Überprüfen Sie bei häufigem Nachfüllen die Dichtheit des Kühlsystems.
Bei der Wartung des Kühlsystems sollten Sie bedenken, dass die Kühlmittel Tosol-A 40M, Lena und Thermosol giftig und brennbar sind, da sie Ethylenglykol enthalten.
In Analogie zu Letzterem haben Flüssigkeiten eine giftige und narkotische Wirkung und die Fähigkeit, über die Haut in den Körper einzudringen.
Wenn Kühlmittel durch den Mund in den Körper gelangt, verursacht es eine chronische Vergiftung mit Schädigung lebenswichtiger menschlicher Organe (betrifft Blutgefäße, Nieren, Nervensystem).
Daher müssen bei der Verwendung von Kühlmittel folgende Vorsichtsmaßnahmen beachtet werden:
- - Saugen Sie bei der Transfusion keine Flüssigkeit in den Mund;
- - während der Arbeit mit Kühlmittel nicht rauchen oder essen;
- - Tragen Sie in Fällen, in denen während des Betriebs Kühlmittelspritzer möglich sind, eine Schutzbrille;
- - Freiliegende Hautbereiche, die mit Kühlmittel in Berührung gekommen sind, müssen mit Wasser und Seife gewaschen werden.
Alle 10.000 km ist eine Einstellung erforderlich b Spannen Sie die Antriebsriemen der Nebenaggregate und prüfen Sie außerdem den festen Sitz aller Anschlüsse des Kühlsystems.
Wenn Tropfen oder leichte Feuchtigkeit festgestellt werden, ziehen Sie die Verbindungsklemmen fest.
Bei erheblichen Flüssigkeitslecks kann in Ausnahmefällen Wasser zur Wiederherstellung des Füllstands verwendet werden.
Dadurch wird jedoch zwangsläufig die Dichte der Mischung verringert und ihr Gefrierpunkt erhöht. Daher sollten Sie das Gemisch schnellstmöglich durch neues Kühlmittel ersetzen.
Beim Nachfüllen von Wasser in das Kühlsystem sollte der Füllstand im Ausgleichsbehälter 7-10 cm über der MIN-Marke liegen.
Bevor Sie mit dem Winterbetrieb beginnen, sollten Sie die Dichte der Flüssigkeit im Kühlsystem überprüfen, die bei 20° C im Bereich von 1078–1085 g/cm 3 liegen sollte.
Alle drei Jahre ist es notwendig, das Kühlsystem zu spülen und neues Kühlmittel einzufüllen. Außerdem wird empfohlen, die Funktion des Thermostats und des Ventilblocks des Ausgleichsbehälterstopfens zu überprüfen.
Ersetzen Sie das Kühlmittel in der folgenden Reihenfolge:
- - Stellen Sie das Auto auf eine horizontale Plattform;
- - Stellen Sie sicher, dass der Heizungshahn geöffnet ist. Schalten Sie dazu die Zündung ein, drehen Sie den Knopf 4 des Lufttemperaturreglers und schalten Sie die Zündung aus.
- - Entfernen Sie den Deckel des Ausgleichsbehälters;
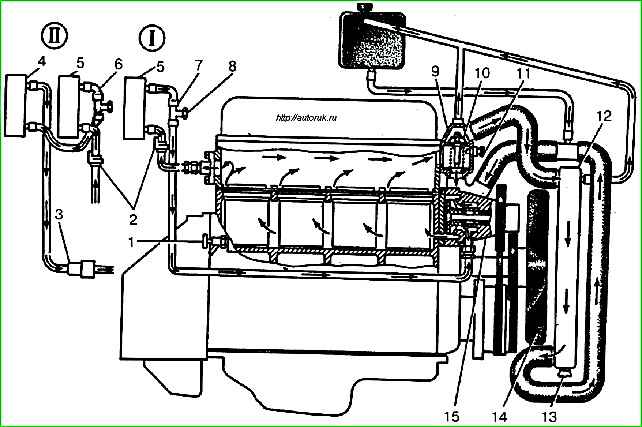
- - Lassen Sie das Kühlmittel aus Motor und Kühler durch Hahn 1 und Stopfen 13 ab;
- - Trennen Sie den Ablaufschlauch des Heizungssystems vom Anschluss am Motor (auf der rechten Seite) und den Zulaufschlauch vom unteren Heizkörperrohr;
- - Entfernen Sie bei GAZ-2705 „Combi“-Autos und -Bussen die Schutzabdeckung der Heizungsschläuche am Boden im Fahrerhaus und trennen Sie die Schläuche vom Kühler 4 der Zusatzheizung, nachdem Sie zuvor einen Flüssigkeitsbehälter darunter installiert haben unteres Kühlerrohr;
- - Nachdem Sie die Flüssigkeit aus dem Heizsystem abgelassen haben, installieren Sie die entfernten Schläuche an ihrer Stelle.
Spülen Sie das Kühlsystem, wozu:
- - Ventil 1 und Kühlerstopfen 13 festziehen;
- - Füllen Sie das Motorkühlsystem durch den Einfüllstutzen des Ausgleichsbehälters bis zum normalen Füllstand mit sauberem Wasser und ziehen Sie den Tankdeckel fest;
- - Starten Sie den Motor, erwärmen Sie ihn bei mittlerer Geschwindigkeit auf 80-90° C und lassen Sie ihn 3-5 Minuten lang laufen;
- - Stellen Sie den Motor ab und lassen Sie das Wasser wie oben beschrieben ab.
Das Kühlsystem füllen, wofür:
- - Ziehen Sie den Hahn am Motorblock und am Kühlerdeckel fest. T-Stecker 8 (siehe) sollte um 2-3 Umdrehungen herausgedreht werden;
- - Flüssigkeit langsam in den Ausgleichsbehälter gießen. Wenn die Flüssigkeit den Tank nicht verlässt, drücken Sie ein bis zwei Mal kräftig auf den Kühlerauslassschlauch, um angesammelte Luft zu entfernen.
- - Wenn Flüssigkeit unter dem T-Stecker austritt, ziehen Sie den Stecker fest.
Nach dem Auftanken müssen Sie den Motor starten und im Leerlauf warmlaufen lassen, bis das Hauptthermostatventil öffnet.
In diesem Fall müssen Sie bei GAZ-2705 „Combi“-Fahrzeugen und Bussen die Elektropumpe einschalten.
Lassen Sie den Motor 3–5 Minuten lang laufen. (Zyklen) bei unterschiedlichen Kurbelwellendrehzahlen: 3000 min -1 - 0,5 min; 1500 Min. -1 - 0,5 Min.; Mindestleerlaufdrehzahl - 0,5 Min.
Überprüfen Sie das Kühlsystem auf Undichtigkeiten.
Nachdem der Motor abgekühlt ist, überprüfen Sie den Flüssigkeitsstand im Ausgleichsbehälter und füllen Sie ihn bei Bedarf auf den Normalwert auf.
Die Überprüfung der Funktion des Thermostats besteht aus der Überprüfung der Temperatur, bei der das Hauptventil zu öffnen beginnt, des Wertes und der Zeit seiner vollständigen Öffnung.
Dazu wird der Thermostat aus dem Motor ausgebaut und in einen Tank mit Kühlmittel mit einem Volumen von mindestens 3 Litern gelegt und auf einer Halterung montiert, so dass das gesamte thermische Leistungselement von Strömen gemischter Flüssigkeit umspült wird.
Die Intensität der Flüssigkeitserwärmung nach 55 °C sollte nicht höher als 1 °C pro Minute sein.
Die Temperatur, bei der der Ventilhub 0,1 mm beträgt, wird als Temperatur angesehen, bei der das Hauptventil zu öffnen beginnt. Diese Temperatur sollte 80° C betragen.
Bei einer Temperatur, die 15° C über der Temperatur liegt Wenn das Hauptventil zu öffnen beginnt, muss der volle Öffnungswert des Ventils mindestens 8,5 mm betragen.
Die Zeit bis zum vollständigen Öffnen des Hauptventils wird ab dem Zeitpunkt bestimmt, an dem das Heizelement in eine Flüssigkeit mit einer Temperatur von etwa 100 °C eingetaucht wird. Diese Zeit sollte nicht mehr als 80 s betragen.
Während des Betriebs sind folgende Abweichungen der Thermostatparameter gegenüber den Nennwerten zulässig:
- Die Temperatur, bei der das Hauptventil zu öffnen beginnt, beträgt 3° C;
- Verlust des Ventilhubs – um 20 %.
Die einfachste Überprüfung der Funktionstüchtigkeit des Thermostats kann durch Berührung direkt am Fahrzeug erfolgen.
Nach dem Starten eines kalten Motors mit funktionierendem Thermostat sollte sich der Schlauch, der das Thermostatrohr mit dem rechten (in Richtung des Fahrzeugs) Kühlerbehälter verbindet, erwärmen, wenn die Kühlmitteltemperatur 80–90 °C erreicht.
In diesem Fall sollte der Pfeil der Kühlmitteltemperaturanzeige auf den grünen Bereich der Instrumentenskala eingestellt werden.
Es ist notwendig, die richtige Spannung der Antriebsriemen der Nebenaggregate aufrechtzuerhalten.
Die Durchbiegung des Antriebsriemens des Lüfters sollte innerhalb von 7–9 mm liegen, die Durchbiegung des Antriebsriemens der Kühlmittelpumpe und des Generators sollte innerhalb von 8–10 mm liegen, bei einer Belastung von jeweils 40 N (4 kgf).
Überprüfen Sie mit einem Dynamometer 7870-8679 wie folgt:
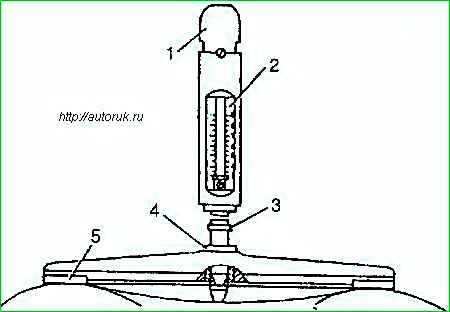
- - Installieren Sie den Dynamometer mit Riemen 5 an den Riemenscheiben des Lüfters und der Spannrolle, der Kühlmittelpumpe und dem Generator;
- - Drücken Sie mit der Hand auf den Griff 1, bis der Kragen 3 die Stange mit der Buchse 4 berührt und ermitteln Sie die Riemenspannungskraft auf der Skala 2;
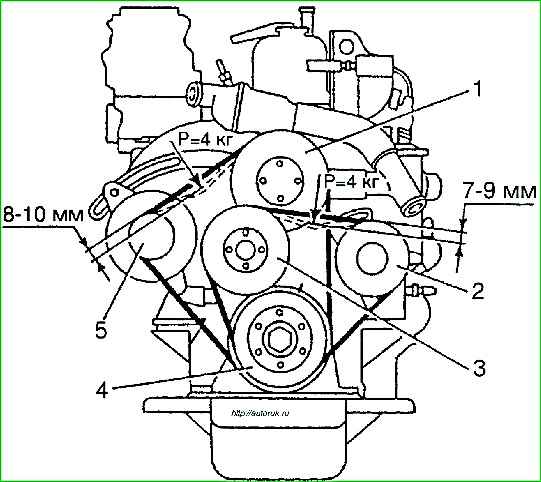
- - Passen Sie bei Bedarf die Spannung des Lüfterantriebsriemens an, indem Sie die Position der Spannrolle 2 ändern, den Generatorantriebsriemen und die Kühlmittelpumpe, indem Sie die Position des Generators ändern.
Bei schwacher Riemenspannung kommt es zu einem Durchrutschen, was zu einer unzureichenden Funktion des Lüfters, der Kühlmittelpumpe und des Generators sowie zu einer starken Erwärmung und Delaminierung der Riemen führt.
Eine zu hohe Riemenspannung führt zu einem schnellen Verschleiß des Lüfterlagers, der Kühlmittelpumpe, des Generators und der Spannrolle sowie zur Dehnung und Zerstörung der Riemen selbst.
Pflege des Stromversorgungssystems. Voraussetzung für den zuverlässigen Betrieb des Energiesystems ist die Sauberkeit seiner Geräte und Komponenten.
Es ist notwendig, nur sauberes Benzin in den Tank zu füllen und außerdem regelmäßig Sedimente und Wasser aus dem Tank abzulassen.
Sie sollten die Dichtheit der Verbindungen der Kraftstoffleitungen und anderer Systemkomponenten sorgfältig bei guter Beleuchtung und einer der Leerlaufdrehzahl entsprechenden Kurbelwellendrehzahl prüfen.
Auslaufender Kraftstoff stellt eine Brandgefahr dar. Undichtigkeiten in den Verbindungen werden durch das Anziehen von Muttern, Anschlüssen und Klemmen beseitigt.
Die Wartung des Drosselklappen- und Luftklappenantriebs besteht aus dem Austausch defekter Teile.
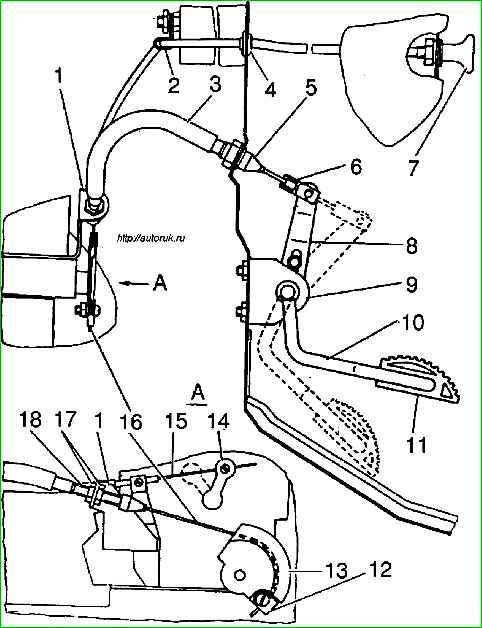
Der Einbau des Drosselklappenantriebs (siehe) muss wie folgt erfolgen:
- - Installieren Sie die Spitzen mit den Dichtungen 5 und 18 in der Frontplatte der Kabine und der Halterung 7 des Vergasers;
- - Führen Sie das Kabel von der Kabinenseite aus durch die Löcher der Spitzen 5 und 18;
- - Stecken Sie die Enden des Innenrohrs des Gehäuses 3 in die Fassungen der Spitzen 5 und 18 und stecken Sie die Enden des Außenrohrs auf die Enden der Spitzen;
- - Stecken Sie das Ende des Kabels mit der Spitze in die Buchse der Kupplung 6 und sichern Sie es mit einem Stift mit Splint am Pedalhebel mit dem Schlitz nach oben;
- - Halten Sie Pedal 11 bis zur Bodenmatte gedrückt und Sektor 13 in Position Drosselklappen vollständig öffnen, Kabel 16 mit Halterung 12 am Sektor 13 befestigen;
- - Passen Sie bei Bedarf die Seilspannung so genau wie möglich an, indem Sie die Spitze 18 in der Halterung 1 verschieben und die Muttern 17 verwenden (um ein vollständiges Öffnen und Schließen der Drosselventile sicherzustellen);
- - Nachdem Sie die Einstellung abgeschlossen haben, stellen Sie Sektor 13 auf die Position vollständig geschlossener Drosselklappen (Pedal in der oberen Position) und sichern Sie den Hebelbegrenzer 8 in der Kontaktposition mit der Halterung 9.
Lassen Sie bei der Installation eines flexiblen Stabs keine scharfen Biegungen des Kabels zu, da es bei einer Krümmung des Kabels dazu kommen kann, dass es in der Hülle stecken bleibt und es zu einem vorzeitigen Bruch des Kabels und einem Verschleiß der Kunststoffschläuche kommt .
Zur Pflege des Luftfilters gehört der regelmäßige Austausch des Filterelements.
Dazu müssen Sie die fünf Riegel lösen und die Filterabdeckung abnehmen.
Beim Zusammenbau des Filters ist auf die korrekte Lage der Dichtungen zwischen Filtergehäuse und Filterelement, des Filterdeckels sowie der Verbindung zwischen Gehäuse und Vergaser zu achten.
Bei der Reparatur eines Filters werden defekte Teile ersetzt.
Die Wartung des Kraftstofffiltersumpfs besteht aus dem regelmäßigen Ablassen des Sediments (alle 20.000 km) durch die Ablassschraube und dem saisonalen Waschen des Filtergehäuses und seines Filterelements einmal im Jahr.
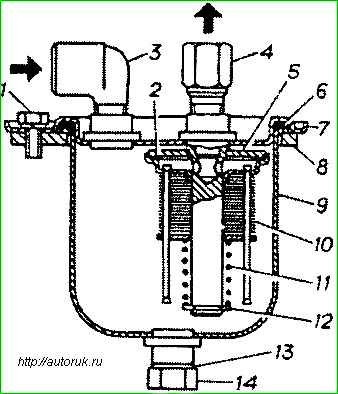
Um das Filterelement zu entfernen, müssen Sie die beiden Schrauben lösen, mit denen die Sumpftankhalterung 8 am Rahmen befestigt ist, die Schrauben 1 lösen, das Gehäuse mit der Halterung 8 entfernen, die Unterlegscheibe 12 und die Feder 11 entfernen.
Spülen Sie das Filterelement und das Filtergehäuse mit sauberem bleifreiem Benzin aus.
Beim Zusammenbau des Sedimentfilters ist auf den korrekten Einbau der Dichtungen 2 und 6 zu achten.
Die Wartung des Kraftstofffeinfilters besteht aus der regelmäßigen Reinigung des Sedimentationstanks von Schmutz und Ablagerungen alle 20.000 km, dem Waschen des Netzfilterelements oder dem Austausch des Papierfilterelements (für Motoren, die vor 2001 hergestellt wurden) und dem Austausch der Filterbaugruppe (für Motoren). veröffentlicht seit 2001).
Zur Wartung der Kraftstoffpumpe gehört das regelmäßige Entfernen von Schmutz vom Kopf und das Waschen des Siebs.
Es gibt zwei Möglichkeiten, den von der Pumpe erzeugten Druck zu überprüfen.
Erste Methode
Die Prüfung wird direkt am Fahrzeug durchgeführt, wobei der Motor bei minimaler stabiler Drehzahl läuft.
Die Kraftstoffpumpe wird vom Vergaser getrennt (der Motor wird durch die Schwerkraft angetrieben) und an ein Manometer mit einer Skala von bis zu 100 kPa (1 kgf/cm 2) angeschlossen.
Für eine funktionierende Pumpe sollte der Druck im Bereich von 23–32 kPa (023–032 kgf/cm 2) liegen.
Sie können den Pumpendruck überprüfen, allerdings weniger genau, ohne ihn vom Vergaser zu trennen, sondern indem Sie ein Manometer über ein T-Stück anschließen, das in den Kraftstoffauslass der Pumpe eingeschraubt wird.
Stellen Sie nach der Druckprüfung den Motor ab. Der Druckwert auf der Manometerskala muss mindestens 10 Sekunden lang angezeigt bleiben.
Ein schnellerer Druckabfall weist auf eine Fehlfunktion der Pumpe hin.
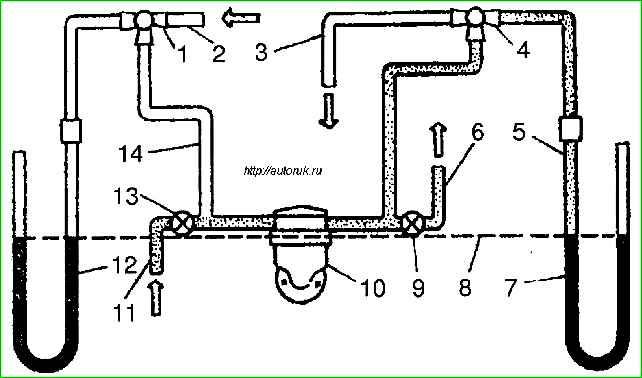
Zweite Methode
- Die Pumpe wird mit einem speziellen Gerät überprüft, das eine Saug- und Druckhöhe von 500 mm gewährleisten muss.
Bei der Überprüfung dieses Geräts muss die Kraftstoffpumpe folgende Anforderungen erfüllen: bei einer Nockenwellendrehzahl des Geräts von 120 min-1 muss die Pumpe Folgendes liefern:
- Null-Versorgungsdruck 23-32 kPa (023-032 kgf/cm 2); - - Das Mindestvakuum in der Saugleitung beträgt nicht weniger als 48,5 kPa (365 mm Hg). Der von der Pumpe erzeugte Druck und das Vakuum müssen bei ausgeschaltetem Antrieb mindestens 10 Sekunden lang aufrechterhalten werden;
- - Der Pumpendurchfluss muss bei einer Nockenwellendrehzahl des Geräts von 1800 min -1 mindestens 145 l/h betragen.
Vergaserpflege umfasst:
- - Inspektion und Entfernung von Staub und Schmutz sowie Überprüfung der Dichtheit aller Anschlüsse, Stecker und Stecker;
- - Überprüfen und Einstellen des Kraftstoffstands in der Schwimmerkammer;
- - Überprüfung der Einstellung des Leerlaufluftsystems;
- - Reinigen und Spülen der Kanäle und Dosierelemente des Vergasers.
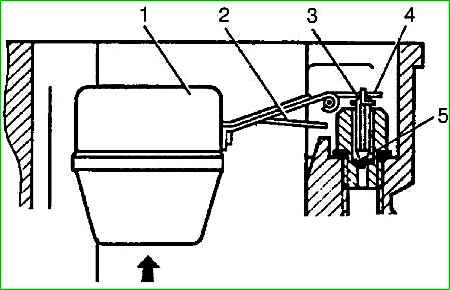
Der Kraftstoffstand in der Schwimmerkammer wird einmal im Jahr überprüft, wobei das Fahrzeug auf einer horizontalen Plattform steht, der Motor nicht läuft und die Vergaserabdeckung entfernt ist.
Der Kraftstoffstand muss innerhalb der Abmessung (A) liegen (20–23 mm von der Ebene des Schwimmerkammeranschlusses).
Der Füllstand wird durch Biegen der Zunge 4 des Hebels von Schwimmer 1 eingestellt. In diesem Fall sollte sich der Schwimmer in einer horizontalen Position befinden und der Hub von Ventil 3 sollte 20-2,3 mm betragen.
Der Ventilhub wird durch Biegen der Zunge 2 des Antriebshebels eingestellt.
Beim Einstellen des Schwimmermechanismus ist darauf zu achten, dass die Dichtscheibe 5 nicht beschädigt wird.
Wenn die Einstellung nicht das gewünschte Ergebnis liefert, müssen Sie den Schwimmermechanismus des Vergasers überprüfen.
Normalerweise sind die Ursachen für einen hohen oder niedrigen Kraftstoffstand in der Schwimmerkammer ein undichter Schwimmer, ein falsches Schwimmergewicht oder ein undichtes Kraftstoffventil.
Die Dichtheit des Schwimmers wird durch Eintauchen in heißes Wasser mit einer Temperatur von mindestens 80° C und einer Haltezeit von mindestens einer halben Minute überprüft.
Wenn die Dichtung des Schwimmers gebrochen ist, was durch die Freisetzung von Luftblasen angezeigt wird, muss der Schwimmer versiegelt werden, nachdem zuvor das Benzin entfernt wurde.
Nach dem Löten ist es notwendig, die Dichtheit und das Gewicht erneut zu überprüfen. Die Masse der Schwimmereinheit mit Hebel sollte nicht mehr als 12,5 g betragen.
Wenn das Kraftstoffventil undicht ist, ersetzen Sie die Dichtungsscheibe 5.
Nachdem Sie die Fehlfunktion des Schwimmermechanismus überprüft und behoben haben, müssen Sie den Kraftstoffstand in der Schwimmerkammer erneut überprüfen und ihn gegebenenfalls wie oben beschrieben anpassen.
Die Einstellung der Mindestdrehzahl der Motorkurbelwelle, des Gehalts an Kohlenmonoxid (CO) und Kohlenwasserstoffen (CH) in den Abgasen im Leerlauf erfolgt nach der Methode GOST 17.2.2.03-87 an speziellen Stellen in Kraftfahrzeuge oder an Autowerkstätten (STO).
Der Gehalt an CO und CH in den Abgasen sollte Folgendes nicht überschreiten:
- - 3,5 % CO und 1200 min -1 CH bei minimaler Leerlaufdrehzahl
- 20 % CO und 600 min -1 CH bei erhöhter Leerlaufdrehzahl< /li>
Die Prüfung sollte bei auf eine Kühlmitteltemperatur von 80-90° C aufgewärmtem Motor und vollständig geöffneter Vergaser-Luftklappe durchgeführt werden.
Das Prüfverfahren ist wie folgt:
- - Lassen Sie den Motor 15 Sekunden lang laufen. bei erhöhter Kurbelwellendrehzahl;
- - Reduzieren Sie die Kurbelwellendrehzahl auf die minimale Leerlaufdrehzahl;
- - nach 20 Sekunden. Überprüfen Sie bei der festgelegten Mindestkurbelwellendrehzahl den Gehalt an CO und CH in den Abgasen.
Abrupte Übergänge von einem Modus zum anderen sind nicht zulässig.
Vor der Einstellung müssen Sie sicherstellen, dass das Zündsystem in einwandfreiem Zustand ist, und dabei besonders auf den Zustand der Zündkerzen und die richtigen Abstände zwischen den Elektroden achten, auch beim ZMZ-4025, ZMZ-4026 und UMZ-Motoren den Zündzeitpunkt bei minimaler Leerlauffrequenz und das Spiel zwischen Kipphebeln und Ventilen des Gasverteilungsmechanismus prüfen und ggf. anpassen.
Die Einstellung erfolgt bei warmem Motor auf eine Kühlmitteltemperatur von 80-90° C.
Das Anpassungsverfahren ist wie folgt:
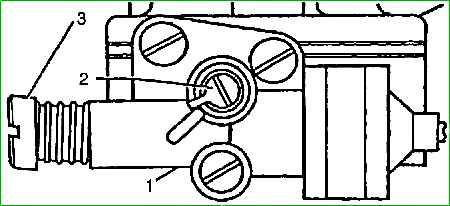
- - Entfernen Sie die Drosselkappe von Schraube 2 der Gemischzusammensetzung (Qualitätsschraube).
- - Schraube 2 und Schraube 3 zur betriebsmäßigen Einstellung der Leerlaufdrehzahl (Mengenschraube), ganz aufdrehen, aber nicht zu fest, dann Schraube 3 um 5-6 Umdrehungen herausdrehen und Schraube 2 um 2-3 Umdrehungen .
- - Starten Sie den Motor und stellen Sie mit Schraube 3 die Kurbelwellendrehzahl (60050) min -1
- ein
- - Inhalt anpassen Reduzieren Sie Kohlenmonoxid und Kohlenwasserstoffe in den Abgasen, indem Sie Schraube 2 einschrauben und mit Schraube 3 die vorgegebene Drehzahl einhalten, um einen stabilen Motorbetrieb zu erreichen.
Um einen optimalen Motorbetrieb zu gewährleisten, empfiehlt das Werk, den CO-Gehalt innerhalb von 0,5 Stunden auf 15 % und den CH-Gehalt auf nicht mehr als 800 min -1 einzustellen.
- - Erhöhen Sie die Kurbelwellendrehzahl auf (270050) min -1 und überprüfen Sie den Gehalt an Kohlenmonoxid und Kohlenwasserstoffen. Gemäß GOST 17.2.2.03-87 sollte sie 2 % bzw. 600 min -1 nicht überschreiten.
Eine Überschreitung der Standards weist auf eine Fehlfunktion des Vergasers hin.
- - Um die Richtigkeit der Einstellung zu überprüfen, drücken Sie das Gaspedal und lassen Sie es kräftig los.
Wenn der Motor ausgeht, erhöhen Sie durch leichtes Lösen der Schraube 3 die Kurbelwellendrehzahl, jedoch nicht mehr als (60050) min -1.
- - Setzen Sie nach Abschluss der Einstellung die Begrenzungskappe auf Schraube 2.
Seine Farbe muss von der vom Hersteller eingestellten Farbe der Kappe abweichen.
Während des Betriebs mit den Schrauben 2 und 3 dürfen Sie nur Anpassungen an den Werkseinstellungen vornehmen, um einen möglichst stabilen Motorbetrieb bei minimaler Leerlaufdrehzahl zu erreichen.
In diesem Fall ist das Eindrehen der Schraube 2 nur bis zu dem Winkel zulässig, der durch die Bewegung der Begrenzungskappenfahne von Anschlag zu Anschlag begrenzt ist (ca. 270°).
Versuche, die Begrenzungskappe in einen größeren Winkel zu drehen, führen zu ihrer Zerstörung.
Das Reinigen und Spülen des Vergasers sollte auf einer sauberen, speziell ausgestatteten Werkbank erfolgen. Um diese Arbeiten durchzuführen, muss der Vergaser vollständig zerlegt werden. Anschließend müssen die Außen- und Innenflächen des Deckels, des Vergasergehäuses, der Diffusoren und des Drosselklappengehäuses gründlich gespült, Teerablagerungen entfernt und die Kraftstoff-, Luft- und Emulsionsdüsen sowie die Düsen gespült werden Kanäle im Vergasergehäuse.
Verwenden Sie zum Spülen bleifreies Benzin.
Der Vergaser und seine Teile müssen nach dem Waschen mit Druckluft ausgeblasen werden.
Das Spülen des Vergasers mit Lösungsmitteln und das Abwischen von Teilen mit Wischspitzen ist nicht erlaubt.
Das Reinigen kalibrierter Löcher mit Metallgegenständen ist strengstens verboten.
Bei der Demontage und Montage dürfen Sie nur gebrauchsfähige Werkzeuge verwenden, um ein Abbrechen der Keilverzahnung und ein Zerquetschen der Muttern zu vermeiden.
Die Vergaserbefestigungen sollten gleichmäßig angezogen werden, um ein Verziehen der Flansche zu vermeiden.
Die Wartung des Umwälzsystems besteht darin, die Löcher im Ansaugrohr mit einem Draht von 4 mm Durchmesser zu reinigen und sie bei ausgebautem Umwälzventil nach 60.000 km des Fahrzeugs auszublasen.
Die Pflege der Abgasanlage umfasst das regelmäßige Anziehen aller Befestigungselemente, insbesondere der Verbindungen von Schalldämpfer, Resonator und Auspuffrohr.
Ausgefallene Schalldämpfer-, Resonator- und Befestigungsteile werden durch neue ersetzt.
Die Pflege der Motoraufhängung besteht darin, den Zustand regelmäßig (alle 20.000 km) zu überprüfen und die Montagehalterungen und Gummipolster festzuziehen.
Um die Haltbarkeit der Kissen zu erhöhen, muss sichergestellt werden, dass sie keinem Öl ausgesetzt sind. Defekte Kissen müssen ersetzt werden.